What is Electrolytic Aluminum?
Electrolytic aluminum is aluminum obtained by electrolysis. Modern electrolytic aluminum industrial production adopts the cryolite-alumina molten salt electrolysis method. Molten cryolite is the solvent, alumina is used as the solute, the carbon body is used as the anode, and the aluminum liquid is used as the cathode. Electrochemical reactions, namely electrolysis, are carried out on the two poles in the tank.
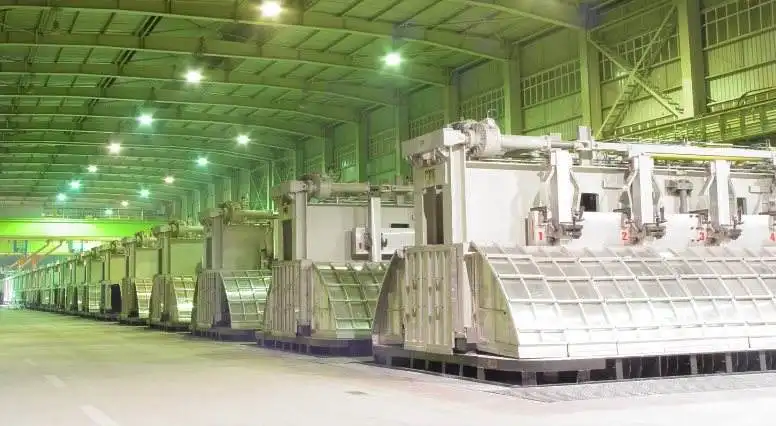
Factors Affecting Electrolytic Aluminum Coloring
The anodization method of aluminum is to use aluminum as the anode, place it in an electrolyte such as sulfuric acid, and apply an anode voltage for electrolysis to form a dense Al2O3 film on the surface of the aluminum. A two-layer structure is composed of layers. Anodized films can be divided into two categories: porous types – films that are formed in an acid electrolytic bath of sulfuric acid, oxalic acid, etc., and form very fine pores perpendicular to the surface. The barrier type – is a non-porous and extremely thin film formed in a neutral salt electrolytic bath such as ammonium borate, which is commonly used in electrolytic capacitors.
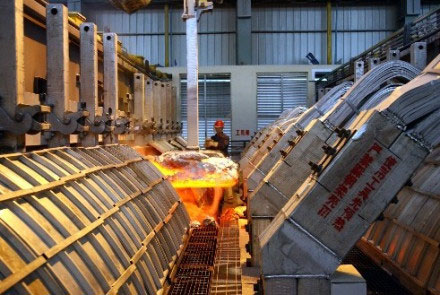
At present, the application of single anodized aluminum alloy building profiles in practice has been significantly reduced, and electrolytic colored oxide films, organic colored oxide films, porcelain oxide films, hard oxide films, imitation stainless steel oxide films, etc. It is widely used. Generally speaking, the factors that affect the oxidation coloring of aluminum alloys are as follows:
1. The Influence of Impurities in the Electrolytic Solution
The quality of the coloring of aluminum alloy products such as Electronic Aluminum Foil depends largely on the quality of the oxide film. Therefore, in the sulfuric acid anodic oxidation solution, the influence of impurities on the oxide film cannot be ignored. The impurities are mainly metal ions such as copper, iron, and aluminum and organic impurities, which should be removed in time to maintain the normal use range of the solution.
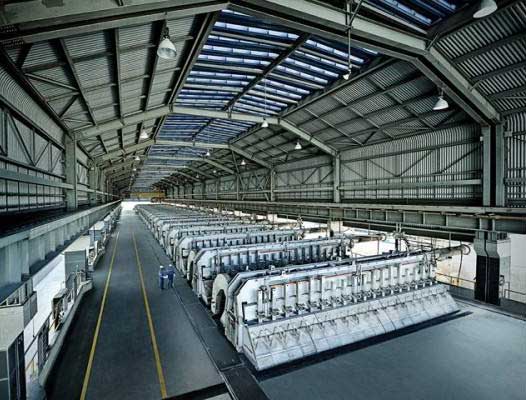
(1) Copper ions will be replaced and deposited on the surface of aluminum parts, causing loose pores in the oxide film and reducing transparency, corrosion resistance, and electrical insulation properties. Therefore, the content of copper ions is not allowed to exceed 0.02g/L.
(2) The chloride ion comes from the tap water or the cooling water after the cooling pipe is broken. The chloride ion content should be lower than 0.2g/L, otherwise, the oxide film generated is rough and loose, and the surface of the aluminum part will be eroded (breakdown) in severe cases.
(3) The aluminum ion in the aluminum ion electrolyte increases gradually. When the content is greater than 25 g/L, the conductivity of the electrolyte decreases, and the surface of the workpiece shows white spots or blocky white spots, which reduces the adsorption capacity of the film layer and makes dyeing difficult.
(4) Organic impurities will hinder the formation of the oxide film. After the film absorbs oil stains, the coloring will be uneven and mottled.
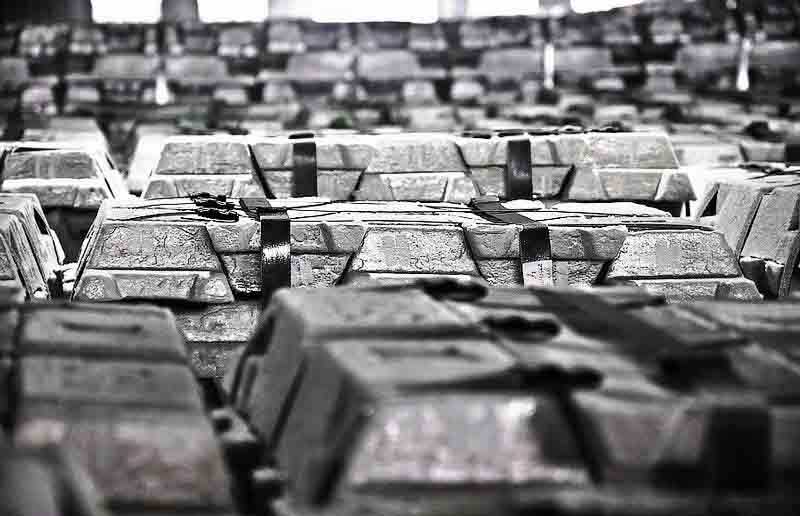
2. Quality of Oxide Film Colorin
(1) If the pretreatment and degreasing process is not carried out completely, it will cause obvious white spots on the film layer, which will bring difficulties to coloring.
(2) When the Sn salt concentration in the electrolytic solution is too low, the coloring speed is slow. When the concentration is higher than 25g/L, the coloring speed is fast, but it is not easy to grasp, and the color difference is often large.
(3) The coloring temperature has a great influence on the coloring. When the temperature is lower than 15°C, the coloring speed is slow. If the temperature is too high, the coloring film will be foggy, and the Sn salt will be easily hydrolyzed and reversed, resulting in the turbidity of the bath.
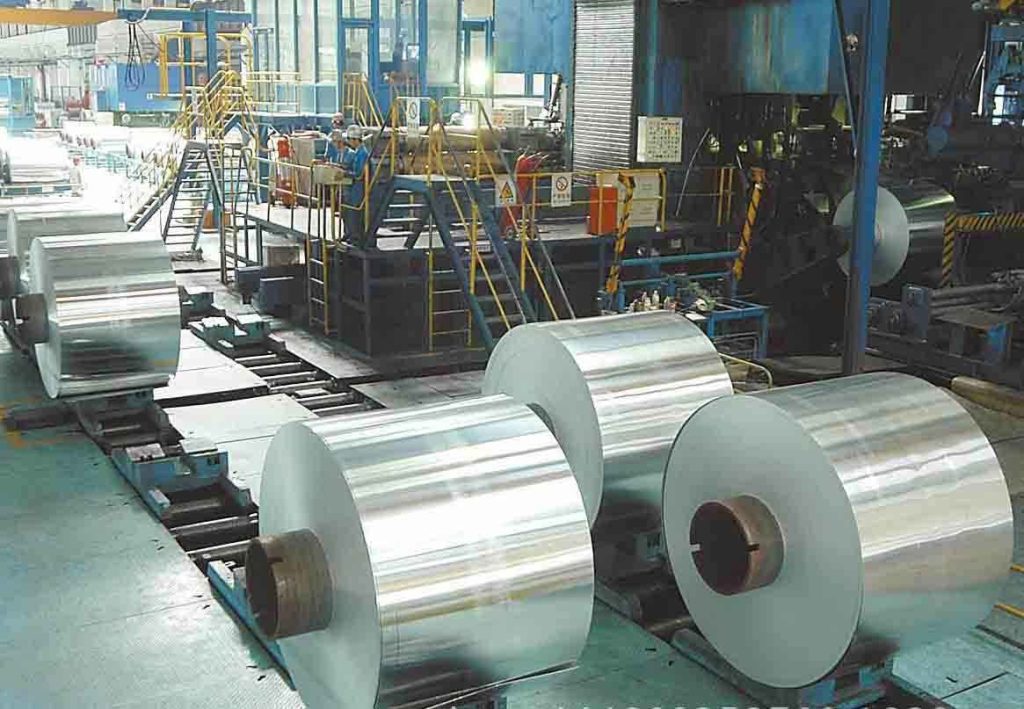
(4) Time: The length of coloring time will also affect the coloring quality and color resistance, such as short coloring time, light color is easy to fade, long time, the color is too dark, the surface is easy to flower.
(5) When the coloring voltage is low, the coloring speed is slow, the color change is slow, and uneven color tone is easy to occur. When the coloring voltage is high, the coloring speed is fast, and the coloring film is easy to peel off.
(6) No matter whether in anodic oxidation film formation or electrolytic coloring, surfactant-based additives and stabilizers should be added to stabilize the film formation speed and film thickness, inhibit the dissolution of the oxide film and improve the uniformity of coloring.