The aerospace industry demands materials that can withstand extreme conditions, from the vacuum of space to the intense heat of atmospheric reentry. Heavy-duty aluminum foil has emerged as an indispensable material, offering a unique blend of properties that meet these stringent requirements. This paper delves into the various applications of heavy-duty aluminum foil in aerospace, showcasing its significance in ensuring the safety and efficiency of space exploration and air travel.
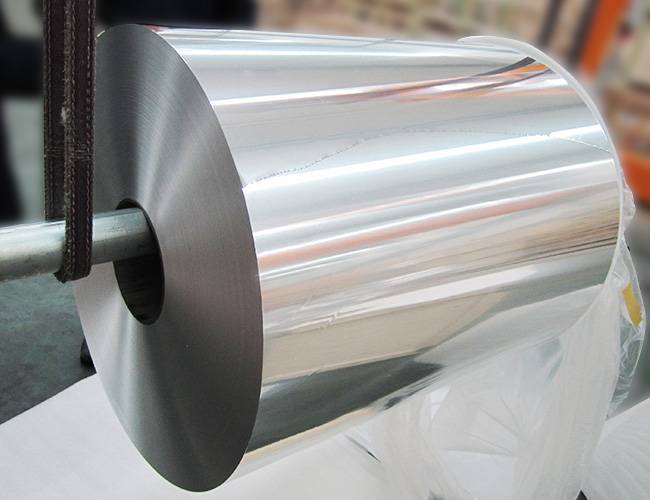
1. Used in Thermal Management
Critical Thermal Insulation for Rockets and Spacecraft
Heavy-duty aluminum foil is integral to Multi-Layer Insulation (MLI) systems, a cornerstone of spacecraft thermal protection. MLI employs alternating layers of highly reflective materials, primarily aluminum foil, and low thermal conductivity spacers. This stratified structure significantly mitigates heat transfer through radiation by reflecting incident thermal energy, while the vacuum environment between layers drastically reduces conduction and convection.
In the severe thermal gradients of space, ranging from cryogenic temperatures in shadowed regions to intense solar radiation, MLI is paramount. It safeguards delicate electronic payloads, propulsion systems, and life support apparatus, ensuring operational stability and mission longevity. The precise layering and material selection within MLI are tailored to specific mission profiles and environmental conditions.
High-Temperature Heat Shielding for Propulsion Systems
Rocket engines and exhaust plumes generate extreme thermal loads that necessitate robust heat shielding. Heavy-duty aluminum foil, often in conjunction with high-temperature alloys and ceramic coatings, is fabricated into heat shields. These shields function by reflecting radiant heat away from critical structural components and dissipating absorbed thermal energy.
The design of these shields involves intricate thermal analysis to optimize material selection, thickness, and geometry, ensuring effective protection against the intense heat fluxes encountered during launch and in-space maneuvers. This prevents thermal degradation and structural failure, maintaining the integrity of the propulsion system.
Precision Thermal Regulation in Aircraft and Satellites
Aircraft and satellites require sophisticated thermal management to maintain operational efficiency and reliability. Heavy-duty aluminum foil is employed for heat dissipation, thermal distribution, and localized insulation. It facilitates the transfer of heat away from electronic components and sensitive instruments, preventing overheating and ensuring stable performance.
In satellites, where orbital dynamics and solar exposure create significant temperature variations, aluminum foil-based thermal management systems are crucial. These systems often incorporate heat pipes, radiators, and active thermal control elements to maintain precise temperature control. The use of aluminum foil allows for lightweight designs that are essential for maximizing payload capacity and mission duration. In Aircraft, the foils are used to help distribute heat evenly or to protect heat sensitive components from heat generated from other components.
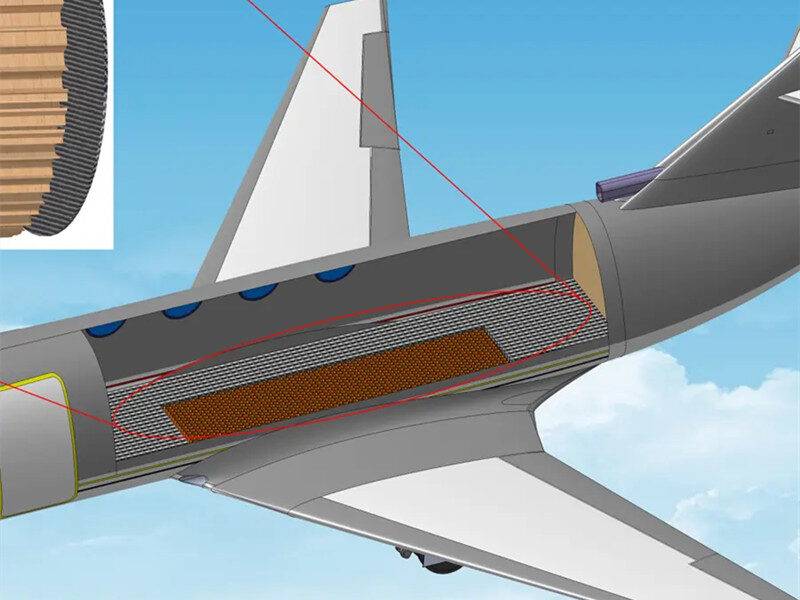
2. Used in Structural Materials
Enhanced Composite Material Reinforcement
Heavy-duty aluminum foil serves as a critical reinforcement layer within advanced composite materials utilized in aerospace applications. By integrating aluminum foil with fiber-reinforced polymers, such as those made with fiberglass or carbon fiber, engineers create hybrid composites exhibiting exceptional strength-to-weight ratios. This integration enhances the composite’s tensile strength, impact resistance, and overall structural integrity.
Beyond mechanical reinforcement, the inclusion of aluminum foil also provides inherent radiation shielding properties. This is particularly valuable in spacecraft applications, where protection against ionizing radiation is essential for safeguarding sensitive electronic systems and crew members. The foil acts as a barrier, attenuating radiation and minimizing its detrimental effects on the composite structure and enclosed components. The bonding of the foil to the composite is a precise science, to ensure there are no weak points.
Lightweight, High-Rigidity Honeycomb Core Structures
Aluminum foil is extensively employed in the fabrication of honeycomb core structures, a cornerstone of lightweight aerospace design. By forming aluminum foil into a hexagonal cellular pattern, manufacturers create a core material that offers exceptional stiffness and compressive strength while minimizing weight.
These honeycomb core structures are integrated into sandwich panels, and used in aircraft wings, fuselage sections, and satellite structural components. The honeycomb core provides structural support and stability, while the outer face sheets, typically made of composite materials or aluminum alloys, provide surface integrity and load-bearing capacity. The precise cell size, foil thickness, and bonding techniques are meticulously controlled to optimize the structural performance of the honeycomb core, ensuring it meets the stringent requirements of aerospace applications. The honeycomb structure also provides a level of thermal and acoustic insulation.
3. Used in Electromagnetic Shielding
Precision Electromagnetic Interference (EMI) Mitigation for Critical Avionics
Aerospace electronic systems, crucial for navigation, communication, and control, are highly vulnerable to electromagnetic interference (EMI). Heavy-duty aluminum foil serves as a robust EMI shielding material, effectively attenuating electromagnetic radiation and preventing signal disruption. By encapsulating sensitive electronic devices and components within aluminum foil enclosures or applying foil coatings, engineers create Faraday cage-like structures that minimize EMI penetration.
The effectiveness of aluminum foil shielding is determined by its conductivity, thickness, and the frequency of the interfering radiation. Careful design and implementation of shielding techniques are essential to ensure the reliable operation of avionics systems in the complex electromagnetic environment of aerospace applications.
Shielding of Signal Transmission Lines for Data Integrity
In aerospace platforms, reliable signal transmission is paramount for maintaining data integrity and system functionality. Aluminum foil is employed to shield cables and connectors, preventing EMI from corrupting transmitted signals. This shielding is critical for high-speed data communication, sensor networks, and control systems.
The shielding effectiveness is achieved by wrapping cables and connectors with aluminum foil, creating a conductive barrier that diverts electromagnetic radiation. This technique minimizes signal loss, reduces noise, and ensures the reliable transmission of critical data. Specialized aerospace grade shielded cables are used to ensure that the shielding is not damaged by the vibrations and temperature changes present in aerospace applications.
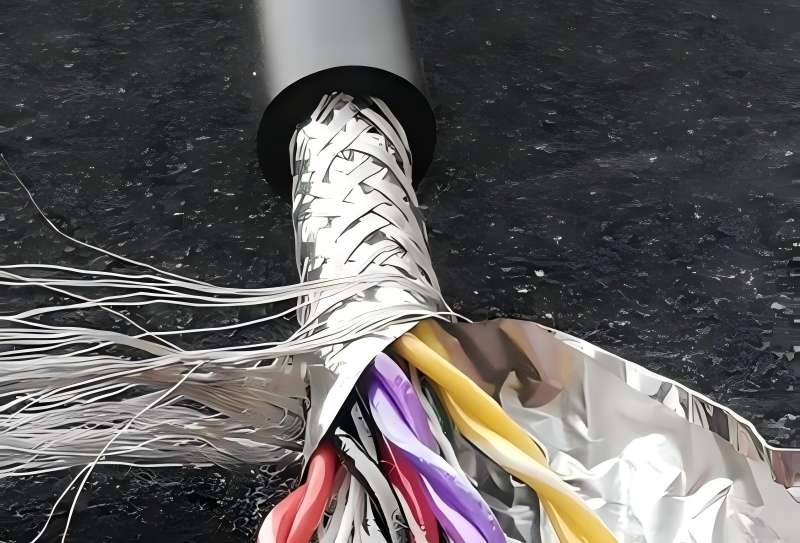
4. Used in Packaging and Sealing
Environmental Protection for Sensitive Aerospace Hardware
Heavy-duty aluminum foil is used to create protective packaging for sensitive aerospace components, safeguarding them against environmental hazards such as moisture, corrosion, and electrostatic discharge (ESD). The foil acts as a barrier, preventing the ingress of moisture and corrosive agents, while also providing ESD protection by creating a conductive path for static charges.
This packaging is essential for maintaining the integrity of electronic components, optical sensors, and other delicate hardware during storage, transportation, and handling. The use of specialized packaging techniques, such as vacuum sealing and inert gas purging, further enhances the protective capabilities of aluminum foil packaging.
High-Integrity Sealing for Aerospace Systems
Aluminum foil tape, specifically designed for aerospace applications, is used to create reliable seals for aerospace equipment. These seals prevent gas or liquid leaks, which are critical for maintaining the integrity of pressurized systems, fuel tanks, and hydraulic systems.
Aerospace grade aluminum tape is designed to withstand extreme temperatures, vibrations, and chemical exposure, ensuring long-term sealing performance. These tapes are often used in conjunction with other sealing materials, such as elastomers and adhesives, to create robust and reliable seals.
Specialized Aerospace Tape Applications
Thermal Spray Masking: Heavy-duty aluminum foil tape is indispensable in thermal spray processes, where it serves as a precise masking material. It shields specific areas from the deposition of thermal spray coatings, ensuring accurate and controlled coating application.
General Repair and Sealing: Due to its exceptional durability and resistance to environmental factors, aerospace-grade aluminum foil tape is extensively used for general repair and sealing tasks on aerospace vehicles. This includes patching damaged surfaces, sealing joints, and providing temporary repairs in challenging environments. The tape’s ability to conform to complex shapes and its resistance to temperature extremes make it a versatile tool for aerospace maintenance.
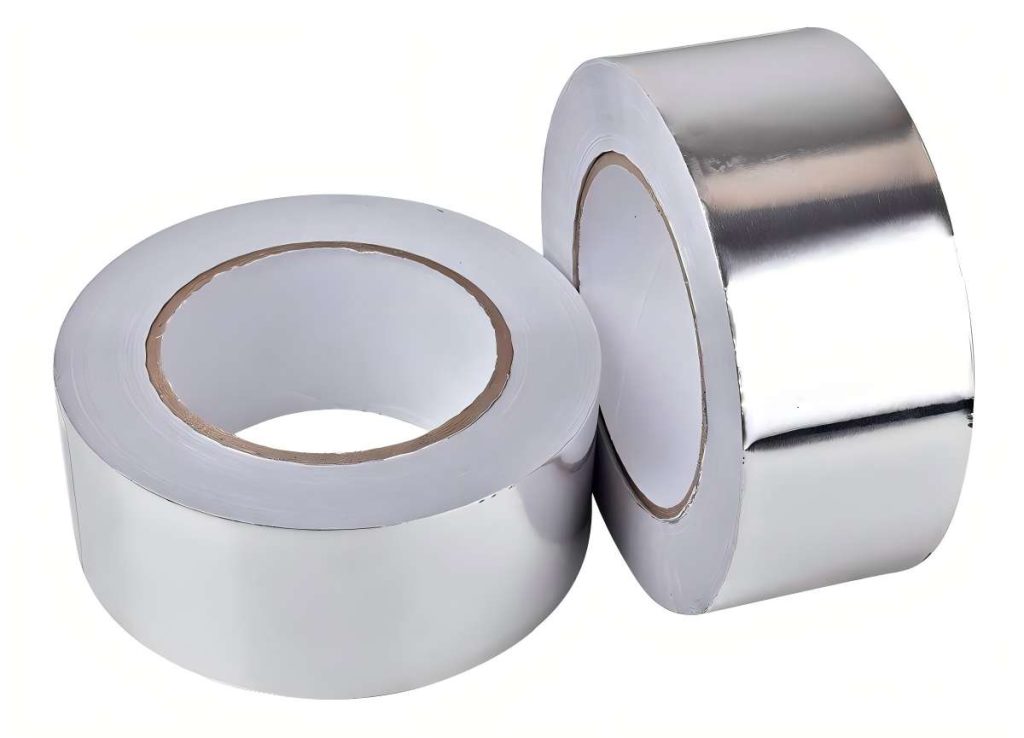
In a word, heavy-duty aluminum foil is an indispensable material in the aerospace industry, contributing to the safety, efficiency, and performance of space exploration and air travel. Its unique combination of properties makes it ideal for a wide range of applications, from thermal management and structural reinforcement to electromagnetic shielding and packaging. As aerospace technology continues to advance, heavy-duty aluminum foil will remain a critical component in future innovations.