Aluminum foil often encounters problems such as wrinkling, cross-layering, bulges, and poor shape during high-speed rolling. Any defect may cause the next pass to be scrapped, and the finished product rate will drop significantly. The author makes some qualitative analysis of the phenomenon of aluminum roll-up encountered in high-speed rolling production.
Definition of aluminum foil bulges
bulges refer to the partial or continuous bulge on the surface of the rolled aluminum foil along the rolling direction. The essence is that the aluminum foil at this place is looser, and the raised void ratio after coiling is larger than that at the flat place. As the kick gets heavier, the kick portion lifts the bar.
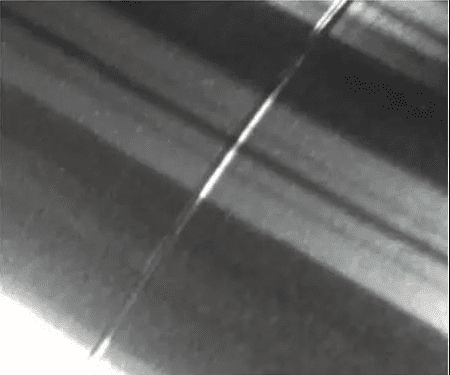
Reasons for aluminum foil bulges
During the aluminum foil rolling process, a large amount of deformation heat and friction heat will be generated. Keep the rolling deformation zone in a heated state all the time. If the local temperature of the roll in the deformation zone is too high. If the maximum cooling capacity of the rolling cooling oil is exceeded, the thermal expansion at this location will increase, and the aluminum foil at the outlet will become loose, such as it cannot being flattened during the aluminum foil coiling process. Then the porosity after coiling at this place is larger than that at the flat place, and after accumulation, a drum is formed, which is called a hot drum in some materials. In actual production, the main reasons for aluminum coiling are as follows:
(1) The rolling rod has a large convexity;
(2) The plate shape parameters are unreasonable. The billet has a large convexity;
(3) The coolant injection pressure is insufficient or the nozzle is blocked;
(4) The preparation of process lubricants is unreasonable
(5) The support roller has scratches;
(6) The pressure of the flattening machine is high;
(7) The pass reduction is large.
Common cause analysis and preventive measures
(1) The rolling stick has a large convexity
The roll crown of the high-speed aluminum foil rolling mill has a large difference in the speed-up stage and the normal operation, and the temperature of the roll is relatively low when the speed is up. The convexity is also small, especially for new rollers, the convexity is relatively smaller. When the convexity is small, the speed-up process is that the two sides of the material are loose. After a certain thermal convexity is established to make the material direction flat, the bottoming is too long, and the two sides of the material are too loose to form a bulge; Under the action of the aluminum foil on the bottom, it will also produce a lot of bulging due to the influence of the bulging material at the bottom, which not only makes it difficult to increase the speed of the bottom but also affects the shaving rate because a large amount of bulging at the bottom cannot be used. When the crown is large, the quality of the speed-up base will be significantly improved. However, due to the high thermal crown caused by high-speed rolling, the middle drum is often formed due to the loose shape of the middle part.
Therefore, it is one of the measures to prevent this kind of bulge to adjust the roll crown in time according to the shape of the bottoming at the exit side to ensure the quality of the bottoming and the control of the shape during normal rolling.
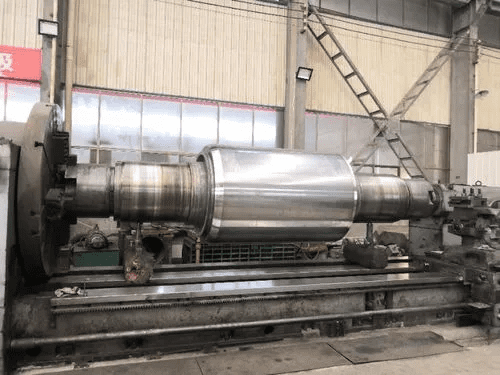
(2) Plate shape parameters are unreasonable
If the value of the shape parameter is determined according to the shape of the online outlet and the production situation of the next pass, if the setting of the shape parameter of the pass causes the material to be convex, and the transition with the shape parameter of the next pass is not appropriate. The deformation zone in the convex area is relatively long, the deformation heat in the middle of the roll is relatively large, the heat of the roll is relatively large, and the plate shape in the middle of the material is loose, and the middle bulging phenomenon may occur.
Therefore, the design of shape parameters must ensure that the shape of the exit door is flat while ensuring that the middle part is slightly tighter than the sides, that is, maintaining a certain middle height, and considering the reasonable transition of shape parameters between passes.
(3) Insufficient coolant injection pressure
When the high-speed aluminum foil rolling mill is in rough and medium rolling, the deformation zone will generate large deformation heat. The cooling effect of rolling oil is very important to maintain roll shape and stable rolling. If the injection pressure and flow rate of cooling oil are insufficient, the cooling effect will be affected. However, in the actual production process, the pressure and flow rate of cooling oil are monitored. Generally, there will be no problems. Many weathering problems are due to mechanical failures such as plugging of the oil rolling nozzle or falling off and rupture of the oil pipe connecting the nozzle, which leads to insufficient flow and pressure of the coolant sprayed in the working area, and the cooling effect is greatly reduced. The degree of rolling in the corresponding area is relatively high, and the shape of the plate is loose and bulging.
Therefore, the spraying effect of the nozzle should be checked regularly, once bulges occur. Stop the machine in time to check the working condition of the spray liquid, which is one of the measures to prevent bulging.
(4) The pressure of the flattening machine is high
Flattening rolls are very important to the stability of high-speed aluminum foil rolling. In foreign countries, servo valves are even introduced into both sides of the flattening rolls to participate in pressure control. Generally speaking, the speed refers to the linear speed of the roll, and the speed of the flattening roll pressed against the export aluminum coil is 20%~30 faster than the speed of the roll. If the speed of the rolling mill is 1500m/min, the flattening roll The linear speed of the roller can reach 1800m/min~2000m/min, and the linear speed of the flattening roller can reach 1800m/min~2000m/min.
In such a high-speed state, the pressing state of the flattening roller has a great influence on the coiling quality. If the pressure on the pressed aluminum coil is large, the frictional force on the material will increase. The locally generated heat will also loosen the hair. In actual production, the method of reducing the pressure of the flattening roller and the grinding convexity of the flattening roller is often used to reduce and eliminate bulges.
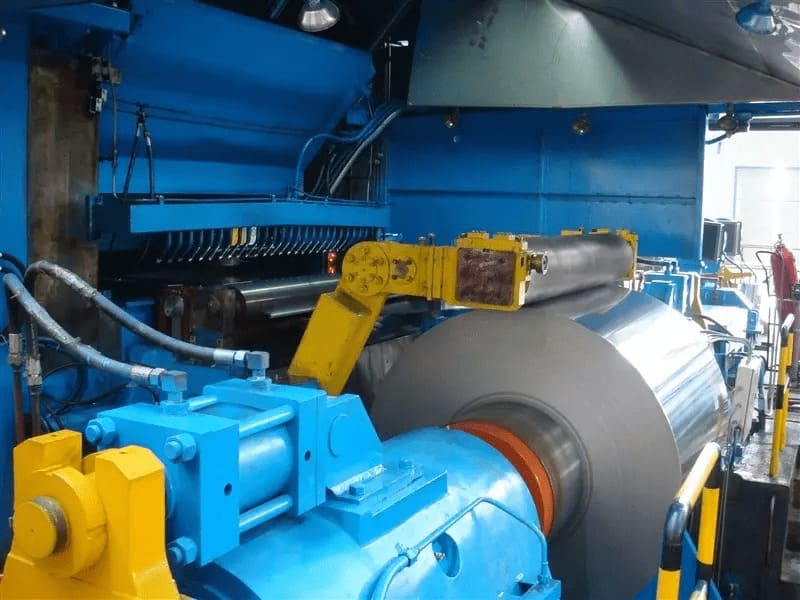
Summarize
Aluminum foil rolling is a problem often encountered in production, which is a reflection of the local deterioration of the plate shape. The reasons can be summarized into two aspects: mechanical and technological. Before the specific reasons are not clear, to prevent the occurrence of batch waste products, the method of lowering the temperature and speed is generally used for production, and at the same time, the specific reasons are found. Some of the measures to prevent bulges described in this article come from production practice and have been proven to be effective. I hope colleagues can help.