Aluminum stamping parts are highly sought after by various industries due to their lightweight nature, which offers cost savings without compromising structural integrity. However, the surface of aluminum stamping parts often requires specialized treatment to address potential issues and meet customer demands. This article delves into the world of surface treatment techniques for aluminum stamping parts, here are 4 common techniques enhancing aluminum stamping parts’ surface performance as below:
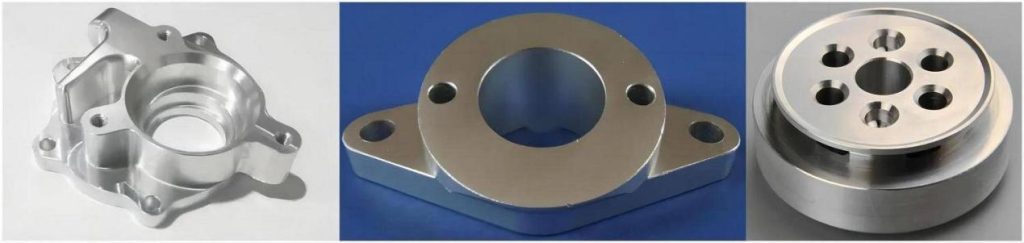
Metal Brushing Treatment
Metal brushing is a popular surface treatment option for aluminum stamping parts, offering a variety of classifications such as straight-line brushing, patterned brushing, spiral brushing, and external thread brushing. This technique leaves distinct, fine marks on the surface, resulting in a visually appealing product with a lustrous linear pattern. While surface treatment is typically required for most aluminum stamping parts, the specific method chosen depends on the customer’s specifications. In the absence of specific instructions, anodizing is commonly selected as the default treatment.
Aluminum Anodizing
Anodizing is a critical surface treatment process that enhances the strength, wear resistance, and visual appeal of aluminum stamping parts. By undergoing an electrochemical oxidation process, aluminum or its alloys react with a lithium-ion electrolyte under specific conditions, resulting in the formation of an oxide layer on the metal surface. Anodizing not only reinforces the surface of aluminum stamping parts but also improves their corrosion resistance. Furthermore, this treatment allows for the application of various colors, expanding the range of aesthetic possibilities and facilitating product customization.
Sandblasting Treatment
Sandblasting serves as an intermediate surface treatment process for aluminum stamping parts. By propelling abrasive materials at high speeds onto the surface, sandblasting effectively removes burrs and oil stains, resulting in a cleaner and more uniform surface. This treatment also enables manufacturers to achieve different levels of surface roughness based on the choice of abrasive material. Additionally, sandblasting enhances the adhesion between aluminum stamping parts and subsequent coatings, ensuring both durability and an appealing visual finish.
Polishing and Buffing Treatment
Polishing and buffing are surface treatment techniques that can elevate the appearance of aluminum stamping parts, providing them with a high-gloss, mirror-like finish. This process involves the mechanical removal of surface imperfections, resulting in a smooth and reflective surface. However, it is important to note that aluminum’s inherent properties make it challenging to maintain a long-lasting mirror-like effect through polishing and buffing alone. In such cases, stainless steel sheet materials are often recommended as an alternative for achieving a more durable mirror-like finish.
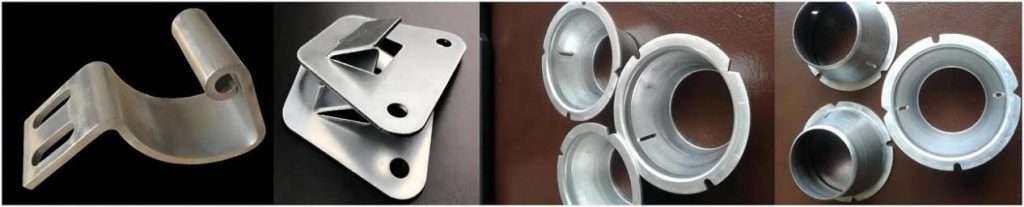
Conclusion
The surface treatment of aluminum stamping parts plays a pivotal role in enhancing their quality, durability, and aesthetic appeal. Metal brushing, anodizing, sandblasting, and polishing are among the commonly employed techniques, each offering unique benefits and characteristics.
By selecting the appropriate surface treatment technique, aluminum product manufacturers can improve the corrosion resistance, visual appeal, and lifespan of aluminum stamping parts. Adhering to customer specifications, industry standards, and robust quality control measures is essential for successfully implementing surface treatment techniques in the production of aluminum stamping parts.
Embracing the art of surface treatment ensures that aluminum stamping parts not only meet functional requirements but also exceed expectations in terms of aesthetics and performance. By leveraging the capabilities of metal brushing, anodizing, sandblasting, and polishing, aluminum product manufacturers can deliver aluminum stamping parts that stand out in terms of both form and function.