5052 aluminum plate is a versatile and widely used material in various industries due to its excellent combination of properties, including good strength, corrosion resistance, weldability, and formability. It is commonly found in applications ranging from building and construction to automotive and aerospace. Within the 5052 alloy series, two common tempers are H32 and H34, each with distinct characteristics and suitable for different applications.
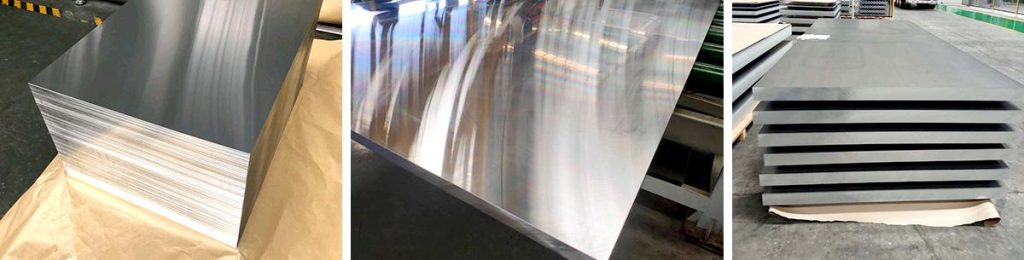
Understanding 5052 Aluminum Plate
5052 aluminum alloy is a non-heat-treatable alloy primarily composed of aluminum, magnesium, and chromium. It offers a balance of strength, ductility, and corrosion resistance, making it a popular choice for various applications. The alloy’s composition typically includes:
- Aluminum (Al): 97.2-98.6%
- Magnesium (Mg): 0.4-1.0%
- Chromium (Cr): 0.15-0.35%
- Iron (Fe): ≤0.4%
- Silicon (Si): ≤0.4%
- Copper (Cu): ≤0.2%
- Manganese (Mn): ≤0.1%
- Titanium (Ti): ≤0.05%
- Other elements (each): ≤0.05%
5052 H32 vs H34 Aluminum Plate: Properties and Applications
Category | 5052 H32 Aluminum Plate | 5052 H34 Aluminum Plate |
Description | 5052 H32 aluminum plate is a strain-hardened temper, meaning it achieves its strength and hardness through cold working processes like rolling or stretching. It is characterized by its good formability, making it suitable for bending, stamping, and other forming operations. | 5052 H34 aluminum plate is also a strain-hardened temper, but it undergoes a more extensive cold working process than H32, resulting in higher strength and hardness. While it retains some formability, it is generally less formable than H32. |
Properties | Tensile Strength: 240-280 MPa (35,000-41,000 psi) Yield Strength: 170-220 MPa (25,000-32,000 psi) Elongation: 25-30% Brinell Hardness: 90-100 HB | Tensile Strength: 280-320 MPa (41,000-47,000 psi) Yield Strength: 220-260 MPa (32,000-38,000 psi) Elongation: 20-25% Brinell Hardness: 100-110 HB |
Applications | Architectural structures Automotive body panels Shipbuilding and marine applications Mechanical components Heat exchangers Food processing equipment Storage tanks | High-pressure vessels Aerospace components Military equipment High-speed trains Precision machinery parts Dies and molds |

5052 H32 vs H34: Performance Comparison
5052 aluminum plates in H32 and H34 tempers exhibit distinct performance characteristics, making them suitable for different applications. Let’s delve into the key differences between these two variants:
- Mechanical Properties: H34 aluminum plates generally possess higher strength and hardness compared to H32 due to their elevated silicon content. This enhanced strength translates to better durability under heavier loads and in harsh environments.
- Corrosion Resistance: While both H32 and H34 belong to the 5052 aluminum alloy series and exhibit good corrosion resistance, H34 may offer superior resistance in specific environments, such as marine atmospheres, due to its higher silicon content.
- Welding Performance: H32 aluminum plates typically demonstrate better welding characteristics compared to H34. H34’s higher silicon content may lead to increased welding defects like cracks during the welding process.
- Processing Performance: H32 aluminum plates generally exhibit better processing properties, including cutting, drilling, and forming, due to their relatively lower silicon content. H34’s higher silicon content may necessitate specialized processing techniques and equipment.
- Heat Treatment Response: H34 aluminum plates are generally not suitable for heat treatment to enhance their mechanical properties due to their higher silicon content. H32 aluminum plates, on the other hand, can undergo heat treatment to improve their strength and hardness.
Manufacturing Process Difference Between 5052 H32 and H34 Aluminum
The manufacturing process for both H32 and H34 aluminum plates involves similar steps, including casting, rolling, and heat treatment. The key difference lies in the heat treatment process:
H32 Aluminum Plate: H32 aluminum plate typically undergoes an annealing process to soften the material and enhance its formability. Annealing involves heating the plate to a specific temperature, holding it for a controlled time, and then slowly cooling it. This process reduces internal stresses and refines the grain structure, making the material softer and more workable.
H34 Aluminum Plate: H34 aluminum plate, on the other hand, goes through a two-step heat treatment process:
- Solution treatment: The plate is heated to a temperature above its solidus temperature (the temperature at which the first solid phase begins to form from the liquid). This high temperature allows all the alloying elements to dissolve into the aluminum matrix, forming a supersaturated solid solution. The plate is then rapidly quenched (cooled quickly), typically by immersion in water. This rapid cooling traps the alloying elements in the supersaturated state, creating a metastable microstructure.
- Age hardening (precipitation hardening): The quenched plate is then reheated to a lower temperature (typically below 250°C) and held for a specific time. During this stage, the supersaturated solid solution becomes unstable, and the excess alloying elements begin to precipitate out of the aluminum matrix as fine particles. These precipitates strengthen the material by hindering dislocation movement (dislocations are imperfections in the crystal lattice that allow for plastic deformation).
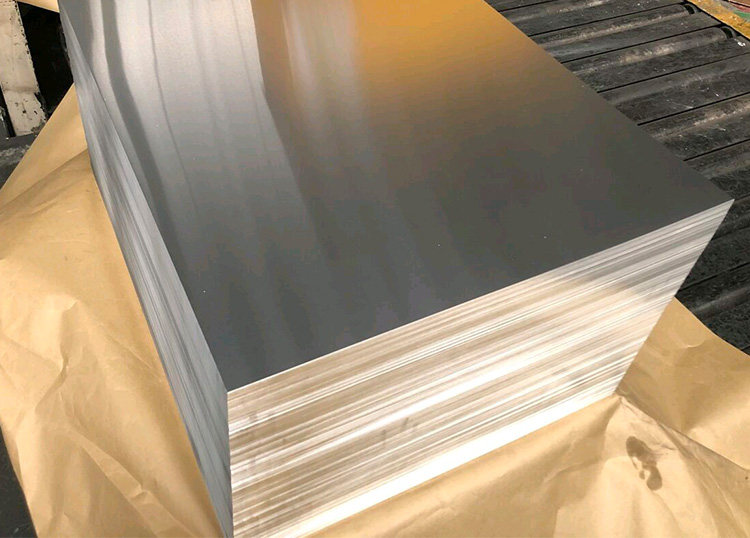
Conclusion
5052 aluminum plates in H32 and H34 tempers offer distinct advantages for various applications. Understanding their key differences in mechanical properties, formability, weldability, and suitability for specific heat treatment processes allows for informed material selection. Choosing the right aluminum plate ensures optimal performance, cost-effectiveness, and product longevity in your project.