Aluminum alloys, renowned for their exceptional strength-to-weight ratio and corrosion resistance, find widespread applications in various industries. Among these, 5052 aluminum sheets and 5083 aluminum plates are particularly popular due to their outstanding mechanical properties and weldability. However, their welding characteristics differ, making it essential to understand their specific requirements to achieve optimal results. This article delves into the properties, welding techniques, and common defects associated with 5052 vs 5083 aluminum alloys.
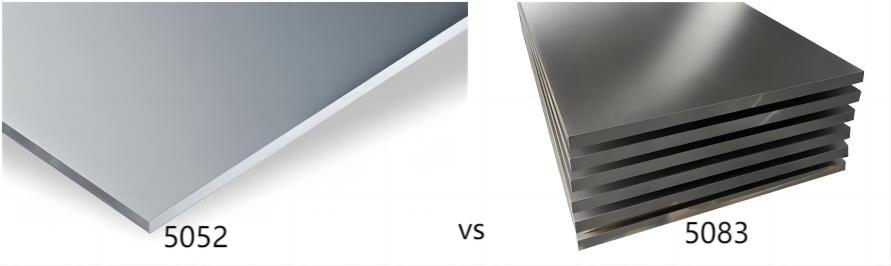
Properties of 5052 and 5083 Aluminum Alloys
5052 Aluminum Alloy
The 5052 aluminum sheet is a versatile alloy known for its excellent formability and corrosion resistance. It contains approximately 2.5% magnesium, which significantly enhances its strength and weldability. Common applications of 5052 include:
- Marine components
- Transportation equipment
- Chemical processing equipment
- Architectural products
5083 Aluminum Alloy
The 5083 aluminum plate is a high-strength, medium-alloy aluminum that offers superior strength and toughness compared to 5052. It contains approximately 4.5% magnesium and 0.7% manganese, contributing to its excellent mechanical properties. 5083 is widely used in:
- Aerospace structures
- Military vehicles
- Marine vessels
- Pressure vessels
How is the Welding Performance of 5052 vs 5083 Aluminum Alloys?
5052 Aluminum Alloy
5052 aluminum sheet is generally considered highly weldable. It can be joined using various welding techniques, including:
- Gas welding: Offers good results but requires careful control of flame temperature and shielding gas.
- Arc welding: Both shielded metal arc welding (SMAW) and gas metal arc welding (GMAW) can be used effectively.
- Resistance welding: Spot welding and seam welding are suitable for joining thin sections of 5052.
- Friction stir welding: A solid-state welding process that offers high-quality joints and minimal heat input.
However, it’s important to note that 5052 can be prone to hot cracking, particularly during argon arc welding. This can be mitigated by using appropriate welding parameters and filler metals.

5083 Aluminum Alloy
5083 aluminum plate is also highly weldable, but careful attention to welding parameters and techniques is required to avoid defects. Common welding methods for 5083 include:
- Gas tungsten arc welding (GTAW): Offers precise control over heat input and is ideal for critical applications.
- Gas metal arc welding (GMAW): Provides high deposition rates and is suitable for both thin and thick sections.
- Friction stir welding (FSW): A solid-state welding process that eliminates the need for filler metal and minimizes distortion.
One of the primary challenges in welding 5083 is the potential for porosity. This can be caused by various factors, including poor joint preparation, inadequate shielding gas coverage, and excessive moisture in the welding environment.
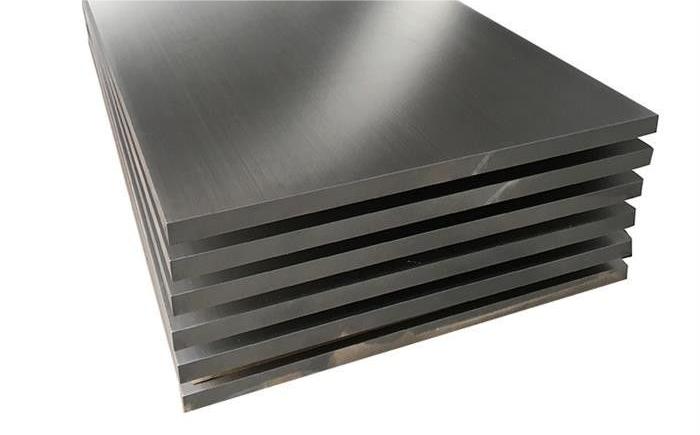
Common Defects in 5052 vs 5083 Aluminum Alloys Welding
Both 5052 and 5083 aluminum alloys can be susceptible to various welding defects, including:
- Poor weld formation: This defect occurs when the weld bead is not properly formed, resulting in a weak and irregular joint. It can be caused by improper welding parameters, poor joint preparation, or inadequate operator skill.
- Porosity: Porosity is the presence of small holes or voids within the weld metal. It can significantly reduce the strength and fatigue life of the weld. It can be caused by poor joint preparation, contamination, excessive moisture, or incorrect welding parameters.
- Cracks: Cracks can occur in the weld metal or the heat-affected zone. They can be caused by excessive thermal stresses, rapid cooling, or poor metallurgical properties.
- Incomplete penetration: This defect occurs when the weld metal does not fully penetrate the joint, resulting in a weak and unreliable joint. It can be caused by insufficient welding current, incorrect joint design, or poor operator technique.
- Inclusions: Inclusions are foreign particles, such as slag or tungsten, that become embedded in the weld metal. They can reduce the strength and ductility of the weld. They can be caused by poor joint preparation, inadequate cleaning, or incorrect welding techniques.
- Undercut: Undercut is a groove that forms along the edge of the weld. It can weaken the weld and reduce its fatigue life. It can be caused by excessive welding current, incorrect welding angle, or poor operator technique.
Preventive Measures to Avoid Welding Defects
To avoid these welding defects, it is essential to follow best practices and adhere to proper welding procedures. Some key preventive measures include:
- Proper joint preparation: Ensure that the joint is clean, free of contaminants, and properly fitted.
- Correct welding parameters: Select appropriate welding parameters, such as current, voltage, and travel speed, to ensure adequate penetration and minimize thermal stresses.
- Adequate shielding gas: Use a high-purity shielding gas, such as argon or a mixture of argon and helium, to protect the weld from atmospheric contaminants.
- Proper welding technique: Employ proper welding techniques, such as maintaining a consistent arc length and using proper welding motions.
- Post-weld heat treatment: In some cases, post-weld heat treatment may be necessary to relieve residual stresses and improve the mechanical properties of the weld.
- Non-destructive testing: Conduct non-destructive testing, such as radiographic testing or ultrasonic testing, to verify the quality of the weld.
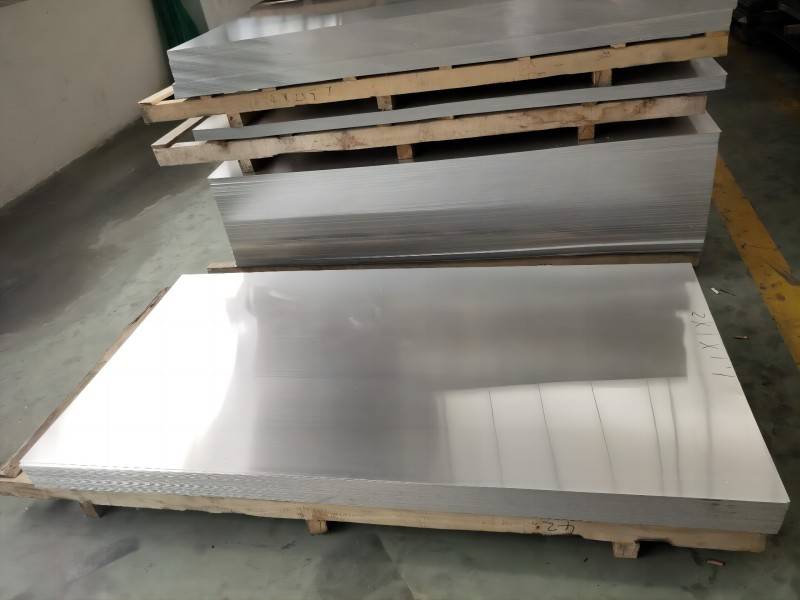
Comparison of 5052 and 5083 Aluminum Alloys in Welding
Feature | 5052 Aluminum Alloy | 5083 Aluminum Alloy |
Weldability | Generally good | Good, but requires careful control |
Common welding methods | Gas welding, arc welding, resistance welding, friction stir welding | Arc welding, friction stir welding |
Potential defects | Hot cracking, porosity | Porosity, cracking |
Preventive measures | Proper joint preparation, appropriate welding parameters, adequate shielding gas, high-quality filler metal, proper welding technique | Proper joint preparation, appropriate welding parameters, adequate shielding gas, high-quality filler metal, proper welding technique, post-weld heat treatment (in some cases) |
Both 5052 aluminum sheets and 5083 aluminum plates are highly weldable materials, but they require careful attention to welding parameters and techniques to achieve optimal results. By understanding the specific properties of each alloy and implementing appropriate welding practices, it is possible to produce high-quality, durable welds that meet the demanding requirements of various industries.