When it comes to welding aluminum, the choice of filler metal is crucial to achieving a strong and durable joint. Two of the most common aluminum welding wires are 5356 and 4043. While both are excellent options, they have distinct characteristics that make them suitable for different applications. This article will delve into the key differences between 5356 and 4043 aluminum welding wire, helping you make an informed decision for your welding projects.
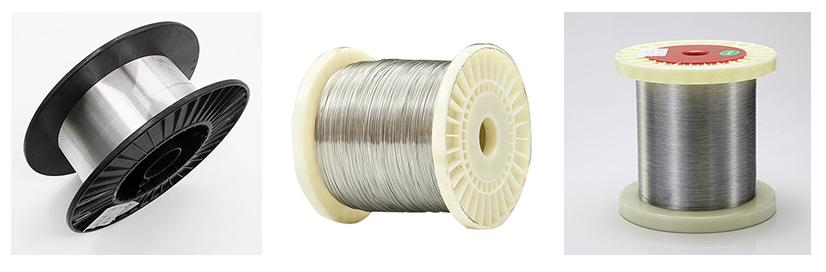
What is Aluminum Welding Wire 5356?
Aluminum welding wire 5356 is a magnesium-based alloy widely used in industries that demand high-strength and corrosion-resistant welds. It contains around 5% magnesium as its primary alloying element, giving it superior strength compared to other aluminum welding wires. This type of wire is particularly favored in environments where exposure to saltwater or other corrosive elements is a concern.
Key Characteristics of 5356:
- Strength: 5356 offers a higher tensile strength than many other aluminum wires, making it suitable for heavy-duty applications.
- Corrosion Resistance: Due to its magnesium content, 5356 provides excellent resistance to corrosion, especially in marine environments where saltwater exposure is common.
What is Aluminum Welding Wire 4043?
Aluminum welding wire 4043 is a silicon-based alloy with around 5% silicon content, known for its exceptional weldability and crack resistance. This wire offers smoother welds and is easier to handle, making it a popular choice for general fabrication tasks where appearance and ease of use are important.
Key Characteristics of 4043:
- Fluidity and Crack Resistance: 4043 has a lower melting point and offers excellent flow, which helps produce cleaner, more aesthetically pleasing welds. Its silicon content improves crack resistance, reducing the chances of weld failure.
- Heat Resistance: It is often used in applications where components are exposed to higher temperatures due to its higher melting point compared to 5356.
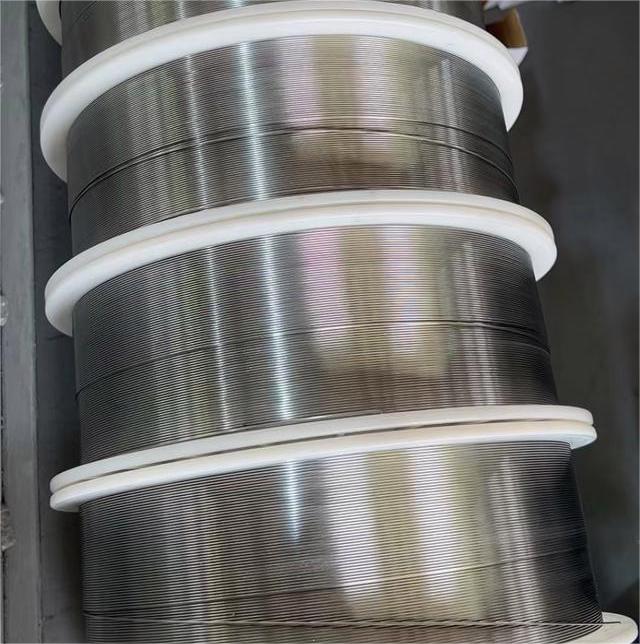
Key Differences Between 5356 and 4043
While both 5356 and 4043 are popular choices for aluminum welding, there are several key differences between the two that dictate their use in different applications.
Category | 5356 Aluminum Welding Wire | 4043 Aluminum Welding Wire |
Chemical Composition | Magnesium-based, with around 5% magnesium content. | Silicon-based, with around 5% silicon content. |
Tensile Strength | Higher tensile strength, suitable for heavy-duty and structural applications. | Lower tensile strength, better suited for non-structural applications. |
Corrosion Resistance | Excellent corrosion resistance, especially in saltwater and marine environments. | Moderate corrosion resistance, not ideal for marine or highly corrosive environments. |
Crack Resistance | Moderate crack resistance, can be prone to cracking under certain conditions. | High crack resistance due to its silicon content, making it less prone to weld failure. |
Weld Fluidity | Offers decent weldability, but harder to handle for beginners. | Provides smoother, more fluid welds with easier application, especially for beginners. |
Post-Weld Appearance | Produces a matte finish, which is more compatible with anodized aluminum. | Creates a shinier, more aesthetically pleasing weld bead, but results in darker or inconsistent color after anodizing. |
Heat Resistance | Can handle moderate temperatures but not as well as 4043 in high-heat applications. | Better for high-temperature environments, often used in heat exchangers and automotive parts. |
Ease of Welding | Slightly more difficult to weld, requiring more experience to achieve perfect welds. | Easier to weld with, especially for general fabrication and decorative work. |
Anodizing Suitability | Moderate crack resistance can be prone to cracking under certain conditions. | Not suitable for anodizing, as it produces inconsistent and darker colors. |
Applications | Best for marine applications, structural components, pressure vessels, and projects requiring corrosion resistance. | Ideal for automotive parts, heat exchangers, general fabrication, and projects requiring smooth welds and crack resistance. |
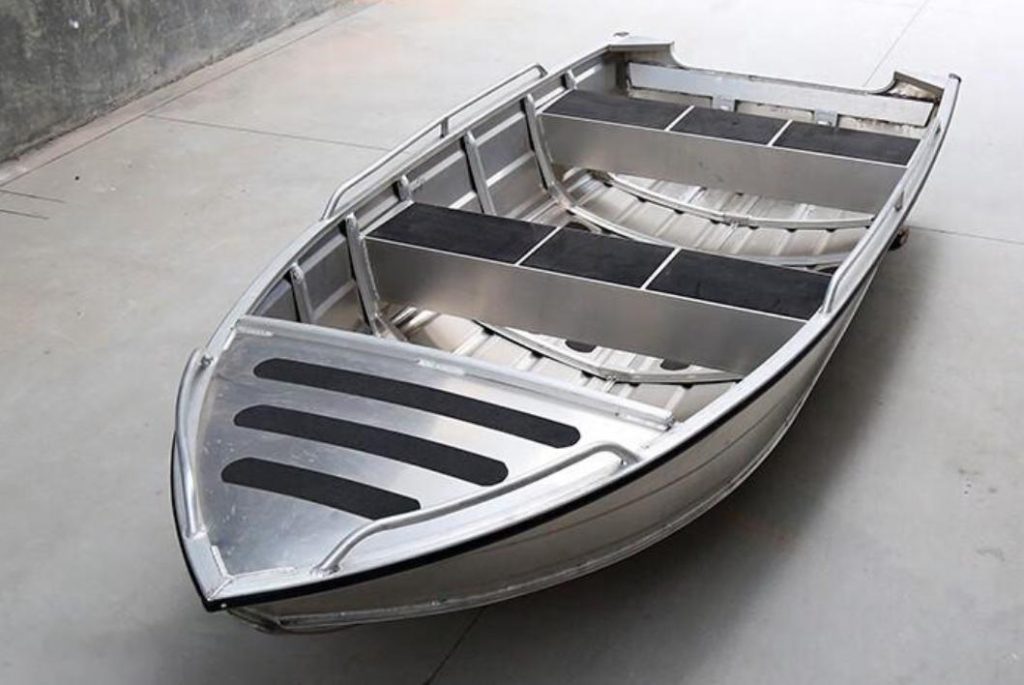
When to Choose 5356 or 4043?
Choose 5356:
- Marine Applications: Due to its excellent corrosion resistance, 5356 is the go-to wire for boats, ships, and any structure exposed to saltwater.
- Structural Parts: If your project requires strong welds for heavy-duty applications, 5356’s high tensile strength makes it ideal.
- Anodized Projects: For projects that will be anodized post-weld, 5356 is a better match for maintaining a consistent appearance after anodizing.
Choose 4043:
- General Fabrication: For projects where ease of welding and appearance are more important than strength, 4043 is the wire of choice.
- Automotive and Heat Exchangers: 4043’s crack resistance and ability to handle high temperatures make it ideal for automotive components and heat exchangers.
- Non-Anodized Applications: When anodizing is not a concern, 4043’s smooth finish and ease of use shine through, especially in decorative and general fabrication tasks.
Selecting between 5356 and 4043 boils down to the specific demands of your project. For strength and corrosion resistance, particularly in challenging environments, 5356 stands out. On the other hand, if ease of use and crack resistance are your top priorities, especially for indoor or decorative applications, 4043 is the more suitable choice.
Each wire has its strengths, making it important to match the wire to your project’s specific requirements – whether that’s strength, corrosion resistance, or ease of welding. By making an informed decision, you’ll ensure stronger, longer-lasting, and more reliable welds for your applications.