Aluminum coils are versatile materials widely used in various industries, thanks to their exceptional properties and applications. Among the plethora of aluminum alloys available, two popular choices stand out: 6061 and 5052. In this article, we will delve into the properties, applications, and differences between these two aluminum alloys, helping you make an informed decision when selecting the right one for your specific needs.
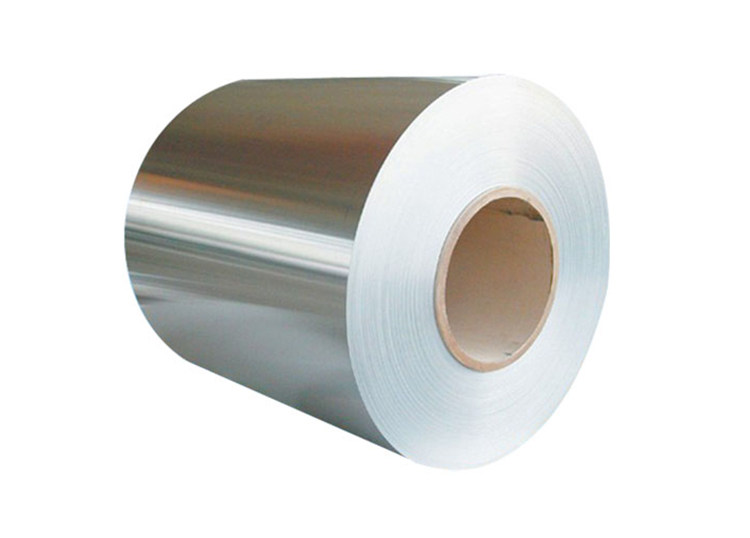
Properties of 6061 Aluminum Coil
6061 aluminum coil is a versatile alloy known for its excellent strength and corrosion resistance. Let’s explore some of its key properties:
- Chemical Composition
6061 aluminum is primarily composed of aluminum, magnesium, and silicon, with small amounts of other elements such as chromium and copper. This unique composition imparts remarkable properties to the alloy.
- Mechanical Properties
6061 aluminum exhibits impressive mechanical properties, making it suitable for a wide range of applications. It has a high tensile strength, typically around 40,000 psi, making it an excellent choice for structural components that require strength and durability. Its yield strength is approximately 35,000 psi, and it boasts good elongation properties, allowing it to withstand bending and forming processes effectively.
- Heat Treatment
One of the distinguishing features of 6061 aluminum is its ability to be heat-treated, which enhances its strength and hardness. This heat treatment process further broadens its application potential.
- Typical Applications
6061 aluminum coils find use in several industries, including aerospace, marine, and structural components. Its combination of strength, corrosion resistance, and heat treatability makes it a go-to material for various critical applications.
Properties of 5052 Aluminum Coil
5052 aluminum coil is another widely used aluminum alloy, known for its excellent corrosion resistance and formability. Let’s examine its properties:
- Chemical Composition
5052 aluminum consists primarily of aluminum, with small amounts of magnesium and chromium. This composition gives it remarkable corrosion resistance properties.
- Mechanical Properties
5052 aluminum possesses a good balance of mechanical properties. While it may not match the sheer strength of 6061, it still boasts decent tensile and yield strength. Its elongation properties are excellent, making it highly formable and adaptable.
- Heat Treatment
5052 aluminum is not heat-treatable in the same way as 6061. It relies on work hardening for increased strength, which occurs during cold working processes like rolling and drawing.
- Typical Applications
5052 aluminum coils find their place in industries such as architecture, automotive manufacturing, and sheet metal fabrication. Its corrosion resistance and formability make it a preferred choice for applications where exposure to the elements is a concern.
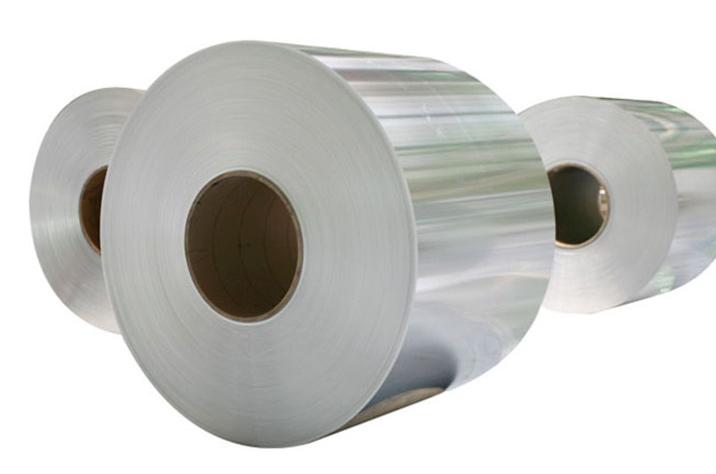
Comparison of 6061 and 5052 Aluminum Coils
Now, let’s compare these two aluminum alloys across various key factors:
Property | 6061 Aluminum Coil | 5052 Aluminum Coil |
Strength and durability | Higher tensile and yield strength | Decent strength, but not as suitable for heavy-duty structural components |
Formability and workability | Slightly less formable due to its higher strength | Highly formable, making it an excellent choice for applications that require complex shapes and bending |
Corrosion resistance | Good corrosion resistance, especially when properly finished or coated | Exceptional corrosion resistance, making it suitable for marine and outdoor applications without additional surface treatments |
Weldability | Weldable but may require more care due to its heat-treatable nature | Easily weldable, with fewer concerns about heat treatment effects |
Cost considerations | Generally slightly more expensive than 5052 due to its higher strength and heat-treatable properties | Less expensive |
Weight-to-strength ratio | Offers a higher strength-to-weight ratio due to its superior strength | Has a lower strength-to-weight ratio but is lighter and more formable |
Availability and sourcing | Readily available from numerous suppliers and in various forms | Readily available from numerous suppliers and in various forms |
Factors Influencing the Choice Between 6061 and 5052 Aluminum Coils
When deciding between these two aluminum alloys, several factors come into play:
- Specific Application Requirements
- Choose 6061 for structural components and applications requiring high strength.
- Choose 5052 for applications where corrosion resistance and formability are paramount.
- Environmental Conditions
- In harsh environments or marine settings, 5052 may be the better choice due to its superior corrosion resistance.
- Budget Constraints
- Consider the cost difference between the alloys, as 5052 is generally more cost-effective.
- Manufacturing Processes
- The fabrication method you plan to use, such as welding or forming, can influence your alloy choice.
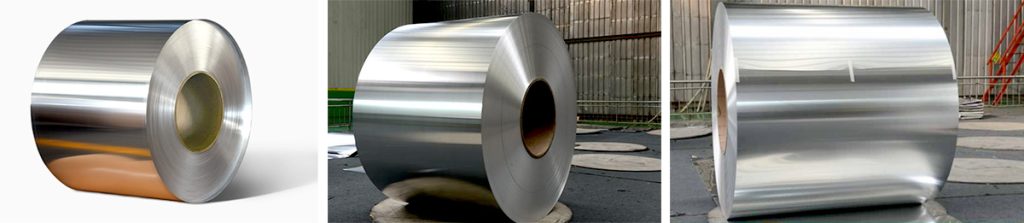
Conclusion
In the choice between 6061 and 5052 aluminum coils, understanding the specific needs of your application is crucial. Both alloys have their strengths and weaknesses, and selecting the right one can significantly impact the performance and longevity of your project. Whether it’s the high strength of 6061 or the corrosion resistance of 5052, each alloy brings its unique advantages to the table. By carefully evaluating your requirements and considering the factors discussed in this article, you can confidently choose the aluminum coil that best suits your needs, ensuring the success of your project.