Aluminum alloys are widely used across multiple industries due to their favorable strength-to-weight ratio, excellent corrosion resistance, and high workability. From aerospace and automotive applications to consumer electronics and structural components, these materials are integral to modern manufacturing. However, to fully harness the potential of aluminum alloys, heat treatment is often required. Heat treatment significantly enhances properties such as strength, hardness, and resistance to wear and corrosion.
Among the wide range of aluminum alloys, 6061 T6 and 7075 T6 stand out for their high performance and versatility. These two alloys are often used in demanding engineering applications that require specific mechanical and corrosion-resistant properties. This article will explore the principles of aluminum heat treatment, provide detailed analyses of the 6061 T6 and 7075 T6 heat treatment processes, and conclude with a comparative evaluation of their treatment procedures and resulting properties.
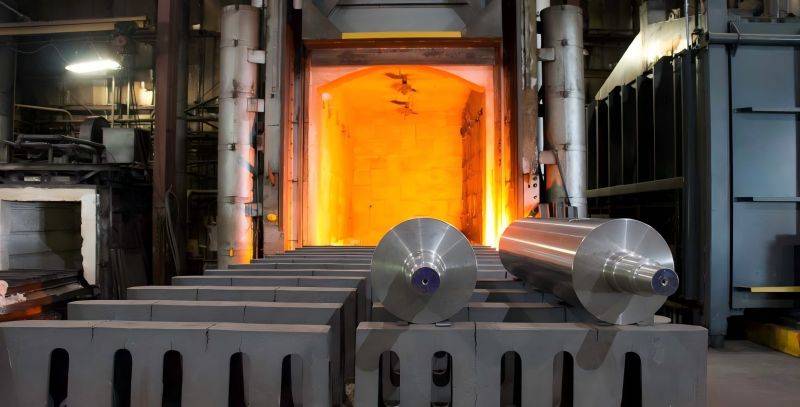
What is Aluminum Heat Treatment?
Aluminum heat treatment encompasses a series of thermal processes designed to modify the microstructure of aluminum alloys, thereby tailoring their mechanical properties such as strength, hardness, ductility, and corrosion resistance. The fundamental principle behind these processes lies in the manipulation of solid solubility and the precipitation of intermetallic phases within the aluminum matrix. The most common heat treatment procedures for age-hardenable aluminum alloys include solution heat treatment, quenching, and aging (precipitation hardening).
- Solution Heat Treatment: This initial stage involves heating the alloy to a specific elevated temperature, typically within a narrow range below its solidus temperature, and holding it for a sufficient duration. This allows the alloying elements to dissolve uniformly into the aluminum matrix, forming a supersaturated solid solution. The aim is to maximize the amount of solute atoms dissolved.
- Quenching: Following solution treatment, the alloy is rapidly cooled to room temperature or slightly below. This rapid cooling, known as quenching, suppresses the precipitation of equilibrium phases and retains the supersaturated solid solution at room temperature. The cooling medium (water, polymer solutions, air, or oil) and the quenching rate are critical parameters that influence the degree of supersaturation and the subsequent aging response.
- Aging (Precipitation Hardening): The supersaturated solid solution achieved after quenching is thermodynamically unstable. Aging involves heating the alloy to a lower temperature (either naturally at room temperature or artificially at elevated temperatures) and holding it for a specific time. During aging, fine, coherent, or semi-coherent precipitates form uniformly throughout the matrix. These precipitates act as obstacles to dislocation movement, significantly increasing the strength and hardness of the alloy. The “T6” temper designation indicates that the alloy has been solution heat-treated, quenched, and then artificially aged.
Different series of aluminum alloys (e.g., 2xxx, 5xxx, 6xxx, 7xxx) exhibit varying responses to heat treatment due to their distinct alloying elements. For instance, the 2xxx and 7xxx series alloys, primarily strengthened by copper and zinc/magnesium, respectively, are highly age-hardenable. The 6xxx series, containing magnesium and silicon, also responds well to precipitation hardening. Understanding the specific alloying constituents is crucial for designing and implementing effective heat treatment cycles.
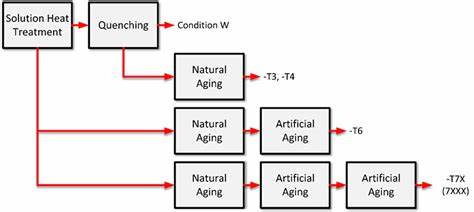
6061 T6 Aluminum Alloy Heat Treatment
1. Understanding 6061 Aluminum Alloy
6061 is a medium-strength aluminum alloy renowned for its excellent weldability, good corrosion resistance, and moderate machinability. Its principal alloying elements are magnesium (0.8-1.2%) and silicon (0.4-0.8%), which combine to form magnesium silicide (Mg₂Si) precipitates during aging, providing strengthening. 6061 aluminum alloy finds widespread applications in structural components, automotive parts, bicycle frames, and recreational equipment where a balance of strength and formability is required.
2. What is the 6061 T6 Heat Treatment Process?
The T6 temper for 6061 aluminum alloy is achieved through a specific three-step heat treatment process:
- Solution Heat Treatment: The 6061 alloy is heated to a temperature range of 510-530°C (950-986°F) and held at this temperature for a sufficient time to allow the magnesium and silicon atoms to dissolve completely into the aluminum solid solution. The soaking time depends on the thickness of the part, typically ranging from 1 to several hours to ensure homogenization.
- Quenching: Following solution treatment, the alloy is rapidly cooled to room temperature to retain the supersaturated solid solution. Common quenching media for 6061 include water quenching (for maximum strength) or polymer quenchants (for reduced distortion). The cooling rate must be sufficiently rapid to prevent the formation of coarse, equilibrium Mg₂Si precipitates, which would hinder the subsequent aging response.
- Artificial Aging: The supersaturated solid solution is then artificially aged by heating it to a temperature of approximately 160°C (320°F) and holding it for 4-10 hours. During this stage, fine, coherent Mg₂Si precipitates form uniformly throughout the aluminum matrix, impeding dislocation movement and significantly increasing the strength and hardness of the alloy. The specific aging time is carefully controlled to achieve the optimal balance of strength and ductility.
3. Performance Characteristics of 6061 T6 Aluminum
The T6 temper imparts a desirable combination of mechanical properties to 6061 aluminum alloy. Typical properties include:
Property | Value |
Tensile Strength | Approximately 290 MPa (42 ksi) |
Yield Strength | Approximately 240 MPa (35 ksi) |
Elongation at Break | Typically 12-17% |
Hardness (Brinell) | Approximately 95 HB |
These properties make 6061 T6 aluminum suitable for a wide range of structural applications where moderate strength and good corrosion resistance are required.
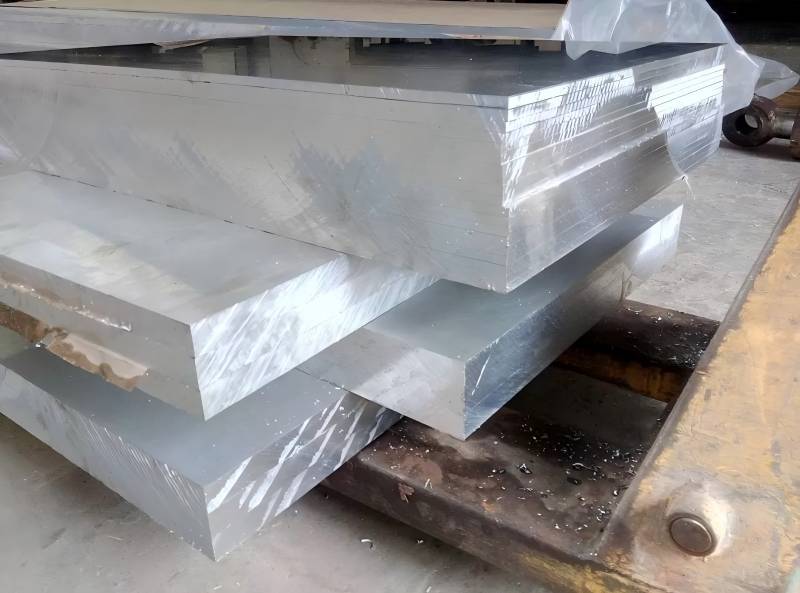
7075 T6 Aluminum Alloy Heat Treatment
1. Understanding 7075 Aluminum Alloy
7075 is a high-strength aluminum alloy, often referred to as an aerospace alloy due to its extensive use in aircraft structures. Its primary alloying elements are zinc (5.1-6.1%), magnesium (2.1-2.9%), and copper (1.2-2.0%). These elements contribute to the formation of fine η’ (eta prime) and η (eta) precipitates during aging, resulting in significantly higher strength compared to 6061.
2. What is the 7075 T6 Heat Treatment Process?
The T6 temper for 7075 aluminum alloy involves a slightly different and often more critical heat treatment cycle:
- Solution Heat Treatment: 7075 alloy is solution heat-treated at a temperature range of 460-480°C (860-896°F). Similar to 6061, the alloy is held at this temperature to ensure the dissolution of the zinc, magnesium, and copper constituents into the aluminum matrix. The soaking time is again dependent on the part thickness.
- Quenching: Rapid quenching is even more critical for 7075 than for 6061 due to its higher susceptibility to the formation of coarse precipitates that can negatively impact strength and corrosion resistance. Water quenching is the most common method, and any delay in quenching after solution treatment can significantly reduce the final properties.
- Artificial Aging: 7075 T6 typically undergoes a two-step artificial aging process to achieve optimal strength and stress corrosion cracking resistance:
- Step 1: The alloy is heated to a lower temperature of 120-130°C (248-266°F) and held for 6-8 hours. This initial lower-temperature aging promotes the formation of fine, coherent Guinier-Preston (GP) zones and intermediate η’ precipitates.
- Step 2: The alloy is then heated to a higher temperature of 160-170°C (320-338°F) and held for an additional 2-4 hours. This second, higher-temperature aging leads to the further growth and transformation of the precipitates, resulting in peak strength.
3. Performance Characteristics of 7075 T6 Aluminum
The two-stage aging process allows 7075 T6 to achieve significantly higher strength levels compared to 6061 T6:
Property | Value |
Tensile Strength | Approximately 570 MPa (83 ksi) |
Yield Strength | Approximately 500 MPa (73 ksi) |
Elongation at Break | Typically 10-11% |
Hardness (Brinell) | Approximately 150 HB |
These superior strength properties make 7075 T6 aluminum ideal for high-stress applications, particularly in the aerospace industry.
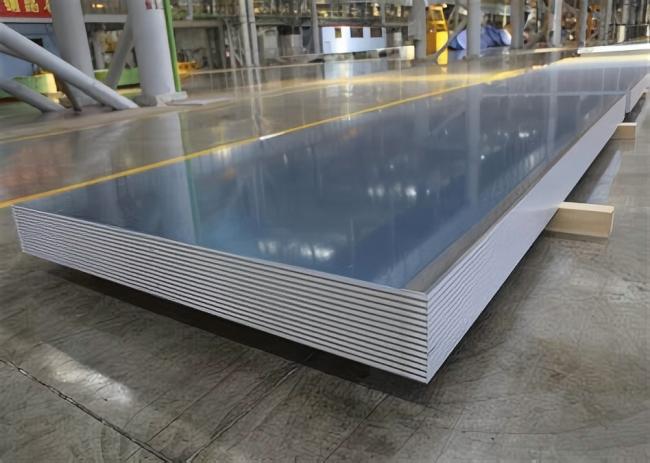
Differences Comparison of 6061 T6 and 7075 T6 Heat Treatment Processes
While both 6061 T6 and 7075 T6 undergo the fundamental stages of solution treatment, quenching, and artificial aging, significant differences exist in their specific processing parameters, primarily due to their distinct chemical compositions:
Feature | 6061 T6 | 7075 T6 |
Solution Treatment Temp | 510-530°C (950-986°F) | 460-480°C (860-896°F) |
Quenching Sensitivity | Water, Polymer Solutions | Water (critical for rapid cooling) |
Aging Process | Single-stage: ~160°C (320°F) for 4-10 hrs | Two-stage: 120-130°C for 6-8 hrs, then 160-170°C for 2-4 hrs |
Primary Strengthening Precipitates | Mg₂Si | GP Zones, η’, η |
Tensile Strength | ~290 MPa | ~570 MPa |
Yield Strength | ~240 MPa | ~500 MPa |
Weldability | Excellent | Poor |
Corrosion Resistance | High | Moderate |
The lower solution treatment temperature for 7075 reflects the different solubility characteristics of its alloying elements. The critical need for rapid water quenching in 7075 underscores its higher sensitivity to cooling rates in preventing the formation of coarse, strength-reducing precipitates. The most notable difference lies in the aging process: 6061 T6 typically employs a single-step artificial aging, while 7075 T6 utilizes a two-step aging process to optimize the precipitation sequence and achieve superior strength and improved resistance to stress corrosion cracking.
Wrapping Up
Heat treatment is a vital process that dramatically influences the properties of aluminum alloys. Through a detailed examination of 6061 T6 and 7075 T6, we observe distinct differences in heat treatment temperatures, aging protocols, and resulting mechanical properties. These differences are primarily driven by alloy chemistry and intended end-use requirements.
Understanding the nuances of aluminum heat treatment allows engineers and manufacturers to select the most appropriate alloy and process combination. As research continues into new precipitation mechanisms and more energy-efficient processing methods, the future of aluminum heat treatment promises even more optimized material performance for next-generation applications.