Aluminium is a lightweight, corrosion-resistant material that has become widely used in various industries, from automotive to aerospace, construction, and even the production of consumer goods. However, aluminium presents unique challenges during the welding process, particularly in terms of its susceptibility to distortion and difficulty in handling heat. This article will explore common methods used in aluminium pipe welding, including a focus on TIG welding aluminum tubes, which remains a highly favored technique for its precision and quality.
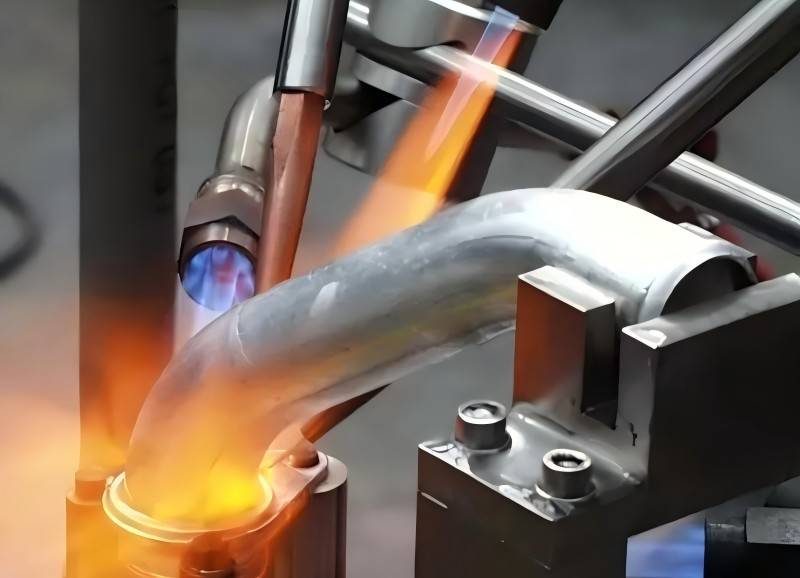
Understanding Aluminium Pipe Welding
Aluminium pipe welding requires specialized knowledge and techniques due to the metal’s properties. One of the main challenges is aluminium’s high thermal conductivity, meaning it rapidly absorbs heat, making it more difficult to control during the welding process. Additionally, aluminium forms an oxide layer on its surface, which must be removed prior to welding to ensure a clean and strong bond. Finally, its relatively low melting point can cause distortion if improper techniques or excessive heat are applied.
As a result, selecting the correct welding method is crucial. The method must account for factors like material thickness, the desired weld quality, cost, and production speed. Below are the most common techniques used for welding aluminium pipes.
Common Methods of Aluminium Pipe Welding
1. TIG Welding (Tungsten Inert Gas Welding)
TIG welding, also known as Gas Tungsten Arc Welding (GTAW), is one of the most popular methods for tig welding aluminum tubes due to its ability to produce high-quality welds. This method utilizes a tungsten electrode to create an arc that heats and melts the metal. Argon or helium gas is used as a shielding gas to protect the weld area from contamination by atmospheric gases.
Key Characteristics of TIG Welding:
- High-quality welds: The precise control of heat input and filler metal makes TIG welding ideal for producing strong, high-quality welds. This is especially important for industries like aerospace, where weld integrity is paramount.
- Flexibility: TIG welding can be used in a variety of positions and for complex joint geometries, making it a versatile choice for different types of aluminium pipe joints.
- Slow welding speed: One of the drawbacks of TIG welding is its relatively slow speed compared to other methods. However, the quality of the weld often justifies the extra time required.
- High heat input: TIG welding tends to input more heat into the metal, which can increase the risk of distortion if not carefully managed. However, experienced welders can control this effectively with the right techniques.
Applications of TIG Welding: TIG welding is often used in applications where precision and high-quality welds are critical, such as in the aerospace and automotive industries. It’s particularly well-suited for aluminium pipe welding, especially for thin-walled tubes where minimizing distortion is essential.
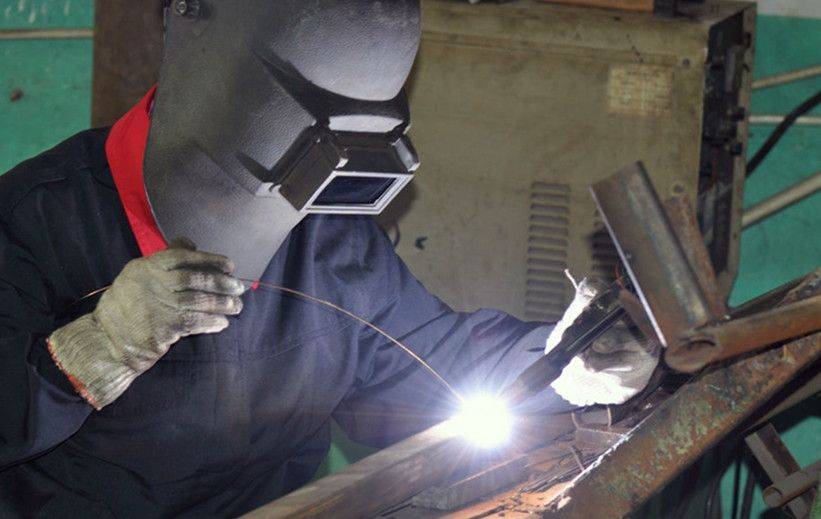
2. MIG Welding (Metal Inert Gas Welding)
MIG welding, also known as Gas Metal Arc Welding (GMAW), is another commonly used method for welding aluminium pipes. Unlike TIG welding, MIG welding uses a continuously fed wire electrode that melts and fuses with the base material, creating the weld.
Key Characteristics of MIG Welding:
- High production efficiency: MIG welding is faster than TIG welding due to its continuous wire feed. This makes it a more efficient option for high-volume production environments.
- Low distortion: MIG welding introduces less heat into the metal than TIG welding, reducing the risk of warping and distortion.
- Lower cost: Because of its faster speed and lower heat input, MIG welding is generally more cost-effective than TIG welding for thicker materials.
Applications of MIG Welding: MIG welding is best suited for welding thicker aluminium plates and pipes where high production rates and lower costs are a priority. It’s commonly used in industries like shipbuilding, structural welding, and heavy equipment manufacturing, where large, heavy aluminium components need to be welded efficiently.
3. Plasma Arc Welding
Plasma Arc Welding (PAW) is a specialized form of arc welding that uses a plasma torch to create a highly focused and intense heat source. This method is known for its ability to produce clean, high-quality welds with minimal distortion, making it ideal for certain types of aluminium welding.
Key Characteristics of Plasma Arc Welding:
- Concentrated heat source: The plasma arc is more concentrated than a traditional TIG arc, which results in faster welding speeds and lower heat input.
- High weld quality: Similar to TIG welding, Plasma Arc Welding produces high-quality welds with excellent strength and precision.
- Complex process: Plasma Arc Welding is a more complex process than TIG or MIG welding, requiring specialized equipment and trained operators.
Applications of Plasma Arc Welding: This method is often used in high-precision applications where weld integrity is critical, such as in the aerospace and electronics industries. For aluminium pipe welding, Plasma Arc Welding may be used when high strength and minimal distortion are required.
4. Laser Welding
Laser welding is a highly precise welding method that uses a focused laser beam to melt and fuse materials. This technique is known for its ability to create small, precise welds with minimal distortion, making it suitable for thin-walled aluminium pipes.
Key Characteristics of Laser Welding:
- Minimal distortion: Laser welding introduces very little heat into the workpiece, reducing the risk of distortion.
- High speed: The concentrated energy of the laser allows for fast welding speeds, making it efficient for high-volume production.
- High equipment cost: Laser welding requires expensive, specialized equipment, which can make it cost-prohibitive for some applications.
Applications of Laser Welding: Laser welding is used in applications where precision and minimal heat input are essential, such as in the electronics, medical device, and automotive industries. It is also used for tig welding aluminum tubes in cases where small, precise welds are required.
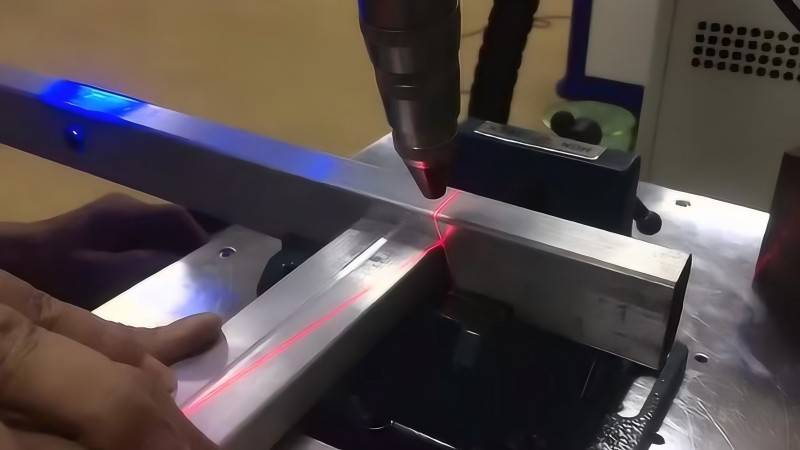
5. Friction Stir Welding
Friction Stir Welding (FSW) is a solid-state welding process that joins materials without melting them. Instead, a rotating tool is used to generate heat through friction, softening the metal and allowing it to be forged together.
Key Characteristics of Friction Stir Welding:
- No melting required: Because the materials do not melt during the welding process, FSW produces very strong welds with minimal defects.
- Low distortion: The absence of a molten pool means that FSW introduces less heat into the workpiece, reducing the risk of distortion.
- Limited to flat or cylindrical joints: FSW is best suited for straight or cylindrical joints and is not typically used for more complex geometries.
Applications of Friction Stir Welding: FSW is often used in industries where high-performance joints are required, such as aerospace, automotive, and shipbuilding. It’s particularly useful for aluminium pipe welding in these high-performance applications, where joint strength is critical.
6. Oxy-Acetylene Welding
Oxy-Acetylene Welding, commonly referred to as gas welding, uses a flame produced by burning oxygen and acetylene gas to melt and fuse the base materials. While this method is not commonly used for aluminium welding due to its low heat concentration and higher risk of distortion, it is sometimes used for less critical applications.
Key Characteristics of Oxy-Acetylene Welding:
- Simple equipment: Oxy-acetylene welding requires relatively simple and inexpensive equipment compared to other welding methods.
- Higher risk of distortion: The flame produced by this process introduces a significant amount of heat into the workpiece, which can cause distortion in thin-walled aluminium pipes.
- Lower weld quality: Gas welding does not produce welds of the same quality as TIG or MIG welding and is therefore not recommended for applications where high weld strength is needed.
Applications of Oxy-Acetylene Welding: This method is often used in repair work or for welding applications where high weld quality is not a priority. In terms of aluminium pipe welding, oxy-acetylene is generally used for non-critical components or temporary repairs.
7. Manual Metal Arc Welding (Stick Welding)
Manual Metal Arc Welding, also known as stick welding, uses a consumable electrode coated in flux to create an arc that melts and fuses the base material. While this method is more commonly used for steel and other metals, it can be used for aluminium welding in certain applications.
Key Characteristics of Manual Metal Arc Welding:
- Simple equipment: Stick welding requires simple, portable equipment, making it a flexible option for fieldwork or repairs.
- Dependent on operator skill: The quality of the weld largely depends on the skill of the welder, making it less consistent than automated processes like TIG or MIG welding.
- Lower weld quality: Stick welding generally produces lower-quality welds than TIG or MIG, and it is not typically recommended for aluminium welding unless in repair scenarios.
Applications of Manual Metal Arc Welding: Stick welding is often used for repairs or in situations where more complex welding equipment is not available. It can be used for aluminium pipe welding in emergency repairs or non-critical joints but is not recommended for high-strength or high-quality welds.
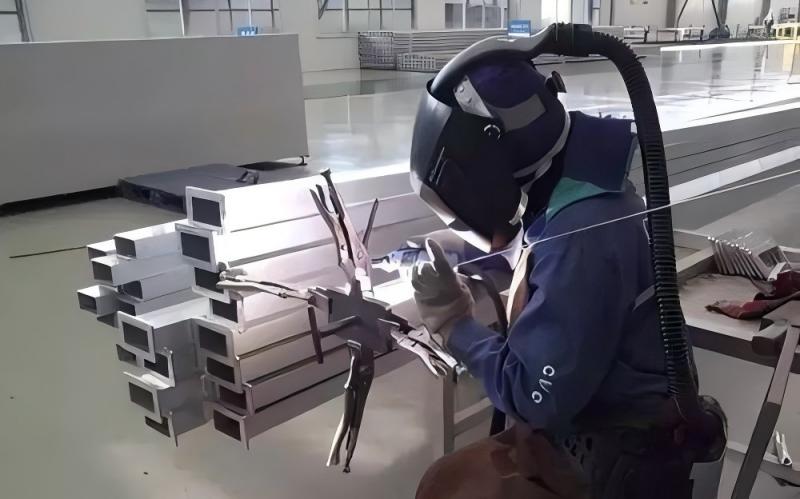
Each aluminium pipe welding method has its own unique advantages and limitations, in practical application, the most suitable technology should be carefully selected according to the specific needs and conditions. Although TIG welding aluminum tube stands out as a highly versatile and precise method for creating high-quality welds, particularly for thin-walled aluminium pipes, there are also other techniques like MIG welding, plasma arc welding, laser welding, and friction stir welding offering viable alternatives depending on the specific needs of the project. Selecting the right method for aluminium pipe welding is essential to ensuring strong, durable, and high-quality welds tailored to the application at hand.