In the upgrade and transformation of industrial compressed air systems, the innovation of pipeline materials is triggering an energy efficiency revolution. According to data from the International Compressed Air Association in 2024, 15% of the world’s industrial energy consumption comes from compressed air systems, of which pipeline losses account for as high as 25-40%. The annual average energy loss of traditional galvanized steel pipe systems is 80,000-120,000 kWh per kilometer, while the application of aluminum alloy pipes has reduced this figure to 30,000-50,000 kWh. This article will explore the technical necessity of aluminum pipes becoming the preferred pipe material for modern air compression systems from the perspectives of materials science, fluid mechanics and system engineering.
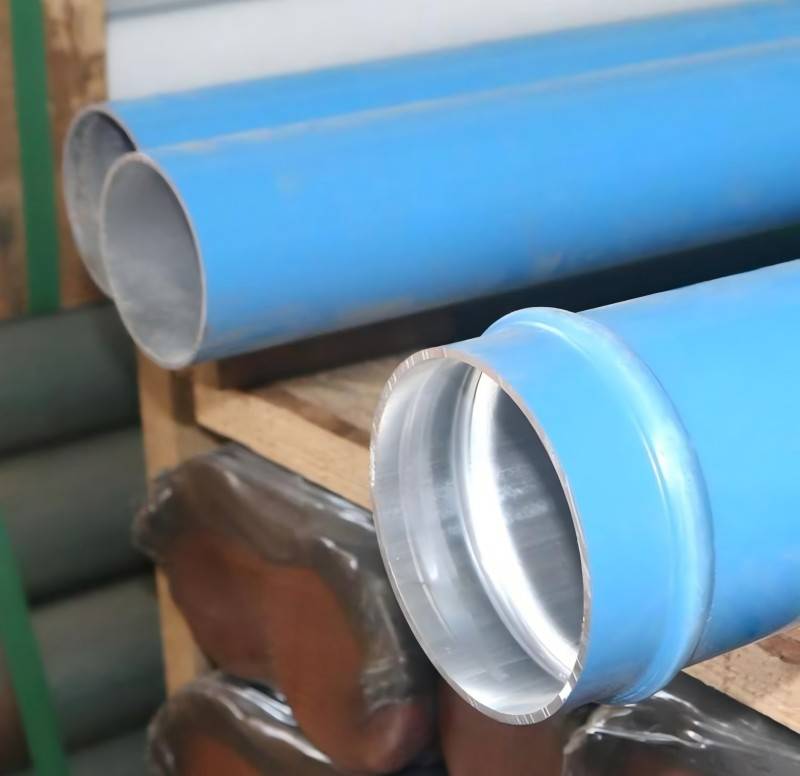
Material Properties
Aluminum possesses a unique set of material properties that make it exceptionally well-suited for compressed air applications.
Its lightweight nature, roughly one-third the weight of steel, significantly simplifies handling and installation. Furthermore, aluminum’s inherent corrosion resistance eliminates the risk of rust, a common problem with steel pipes that can lead to leaks, pressure drops, and contamination of the air supply. This non-corrosive nature of aluminum ensures that the internal surfaces remain smooth over time, preventing the accumulation of debris or rust. This maintains optimal airflow and reduces the risk of contamination in sensitive applications such as food processing or pharmaceuticals. The combination of lightweight and corrosion resistance translates to a longer lifespan, reduced maintenance, and improved air quality.
For example, the tensile strength of 6063-T6 aluminum alloy reaches 240MPa, the elongation is 12%, and its specific strength (strength/density) is 2.3 times that of 304 stainless steel. The unique anodizing treatment makes the surface hardness reach HV300, and the wear resistance is 5 times higher than that of galvanized pipe. Under 80℃ working conditions, the thermal expansion coefficient of 23.6×10⁻⁶/℃ can effectively alleviate the leakage of connectors caused by thermal stress.
By optimizing the alloy ratio and surface treatment process, aluminum tubes achieve a perfect balance between mechanical properties and weather resistance, providing reliable protection for industrial pipeline networks.
Fluid Dynamics
The smooth inner surface of aluminum pipes significantly enhances fluid dynamics. This feature reduces frictional losses, ensuring that compressed air flows efficiently throughout the system. Unlike pipes made from other materials, aluminum maintains a consistent internal diameter over time, as it is not prone to scaling or internal corrosion.
Improved fluid dynamics translate to lower pressure drops, which means compressors don’t have to work as hard to maintain desired pressure levels. This not only enhances system performance but also reduces energy consumption, contributing to cost savings and operational efficiency.
With better flow characteristics, aluminum pipes ensure that air compressor systems operate at peak efficiency, delivering consistent and reliable performance.
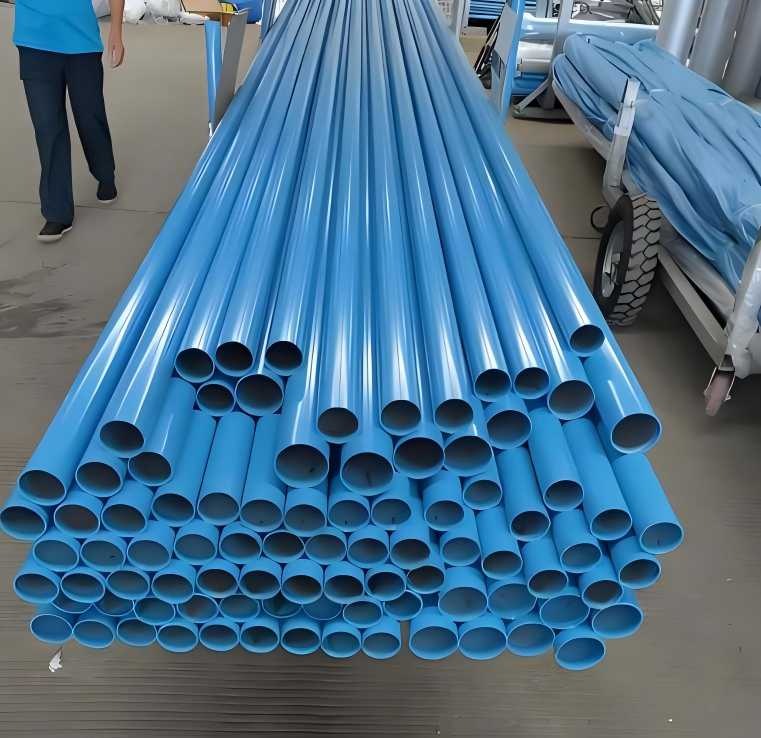
Economic Benefits
While the initial cost of aluminum piping might be slightly higher than some alternatives, the long-term economic benefits are substantial. The ease of installation, thanks to its lightweight nature and readily available push-to-connect fittings, significantly reduces labor costs. The corrosion resistance of aluminum minimizes maintenance requirements and extends the lifespan of the piping system, reducing replacement costs. Furthermore, the improved energy efficiency resulting from reduced pressure drop translates to lower operating costs over time. These combined factors make aluminum a cost-effective choice in the long run.
Considering the entire lifecycle costs, including installation, maintenance, and energy consumption, aluminum piping often proves to be a more economically sound investment compared to other materials.
Installation and Maintenance
Aluminum pipes are designed for quick and easy installation. Their lightweight nature allows for simpler handling, and many aluminum piping systems feature modular designs with push-to-connect fittings. This reduces installation time and labor costs compared to traditional welded or threaded piping systems.
Maintenance requirements for aluminum pipes are minimal due to their corrosion resistance and durable construction. Unlike steel pipes, which may require regular inspections and replacement of rusted sections, aluminum pipes remain reliable over time with minimal upkeep.
The ease of installation and low maintenance needs make aluminum pipes a practical and efficient choice for air compressor lines, reducing downtime and ensuring uninterrupted operations.
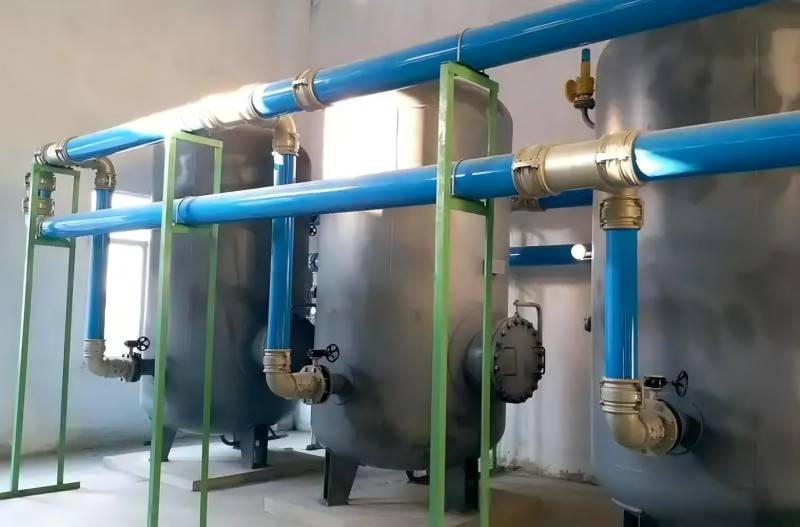
Environmental Adaptability
Aluminum performs exceptionally well in a wide range of environmental conditions. It retains its strength and structural integrity even in extreme temperatures, making it suitable for applications in both hot and cold climates. Additionally, its corrosion resistance ensures reliable performance in humid or chemically harsh environments.
This adaptability ensures that aluminum pipes can be used across diverse industries and locations without compromising on performance, offering unparalleled versatility and reliability.
By choosing aluminum pipes, businesses can ensure that their air compressor systems are equipped to handle a variety of environmental challenges, maintaining efficiency and durability.
Energy Efficiency Improvement
As mentioned earlier, the smooth interior of aluminum piping minimizes friction and pressure drop, leading to improved energy efficiency. This is a critical factor in compressed air systems, as energy consumption is a significant operational cost. By reducing the energy required to maintain adequate pressure, aluminum piping contributes to lower energy bills and a reduced carbon footprint.
Sustainable Development Characteristics
Aluminum is a recyclable material, making it an eco-friendly choice for air compressor lines. At the end of its service life, aluminum can be recycled without losing its inherent properties, reducing waste and promoting circular economy practices.
The carbon footprint of recycled aluminum pipes is only 5% of that of virgin aluminum, and their 100% recyclability allows the material to be recycled 8-10 times.
Choosing aluminum pipes supports a greener future, enabling industries to minimize environmental impact while maintaining high performance and efficiency.
Summary
Aluminum pipes are the ideal choice for air compressor lines, offering a unique combination of durability, efficiency, and environmental benefits. Their superior material properties, enhanced fluid dynamics, cost-effectiveness, ease of installation and maintenance, adaptability, energy efficiency, and sustainability make them a standout solution for modern compressed air systems.
By opting for aluminum piping systems, businesses can ensure reliable performance, reduce operational costs, and contribute to a more sustainable future. Whether you’re upgrading an existing system or planning a new installation, aluminum pipes are a smart investment that delivers long-term value and peace of mind. If you are looking for a aluminum pipe supplier, please feel free to contact CHAL.