Aluminum coils, boasting inherent advantages of low mass and robust corrosion resistance, are rapidly displacing their heavier, ferrous counterparts in a multitude of automotive applications. This article delves into the technical complexities of this material metamorphosis, exploring the specific alloys, diverse applications, and attendant challenges associated with integrating aluminum coils into modern automobiles.
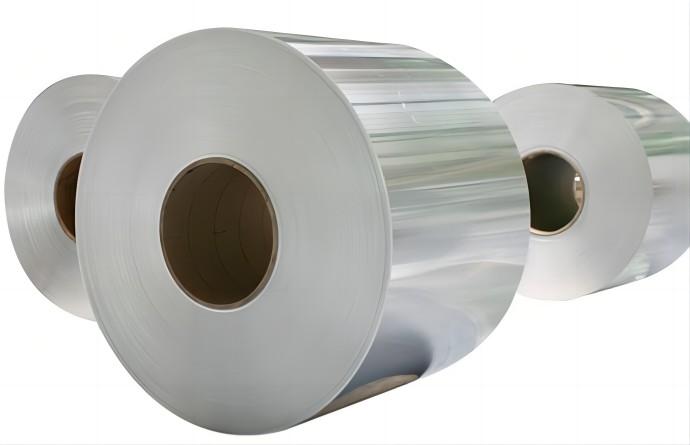
A Technical Analysis of Dominant Aluminum Choices
The landscape of automotive aluminum coils is dominated by three key alloys, each possessing distinct properties that dictate their suitability for specific applications:
5052 aluminum coil: This versatile “workhorse” alloy excels in formability, making it ideal for crafting complex body panels, hoods, and trunks. Its superior weldability simplifies assembly processes, while its robust corrosion resistance ensures long-term durability. However, compared to its higher-performance counterparts, 5052 exhibits lower tensile strength, limiting its use in high-stress applications.
6061 aluminum coil: When high strength reigns supreme, 6061 is the champion. This alloy’s exceptional strength-to-weight ratio makes it the preferred choice for critical components like engine blocks, suspension arms, and chassis reinforcements. Its excellent machinability facilitates precise shaping for intricate geometric designs, while its inherent corrosion resistance protects against the harsh underbody environment. However, compared to 5052, 6061 boasts less forgiving formability, requiring specialized manufacturing techniques and equipment.
1100 aluminum coil: Purity defines 1100 aluminum. Its unmatched electrical conductivity makes it the ideal candidate for heat exchangers like radiators and condensers, enabling efficient thermal transfer and improved engine cooling due to its high reflectivity. However, the trade-off for this exceptional conductivity is significantly lower tensile strength compared to 5052 and 6061, limiting 1100’s application to non-structural components where mechanical strength is less critical.
Applications of Aluminum Coils in Modern Automobiles
The versatility of aluminum coils extends far beyond the realm of aesthetics, permeating various automotive sub-systems with tangible benefits. Let’s delve deeper into specific applications across key vehicle domains:
- Exterior
- Body Panels: Aluminum’s inherent mass reduction translates to lighter body panels, leading to a quantifiable improvement in fuel efficiency (5-10% depending on vehicle size and panel coverage). This translates to reduced CO2 emissions, aligning with environmental goals. Additionally, the inherent elasticity of aluminum contributes to superior dent resistance, enhancing both aesthetics and passenger safety.
- Bumpers: Strategically employed aluminum in bumpers facilitates energy absorption during low-speed impacts, improving crashworthiness. Furthermore, its corrosion resistance eliminates concerns about rusting, ensuring long-term durability. Additionally, aluminum’s design flexibility allows for the creation of complex bumper shapes, enhancing vehicle aesthetics.
- Wheels: Lightweight aluminum wheels offer a significant reduction in unsprung weight, leading to improved handling agility, sharper turn-in response, and a smoother ride. This also translates to reduced fuel consumption due to lower rolling resistance.
- Interior
- Trim Components: Aluminum trim elements not only exude a premium aesthetic but also contribute to weight reduction (up to 2% depending on integration extent), further bolstering fuel efficiency.
- Heat Shields: Strategically placed aluminum heat shields surrounding the engine effectively mitigate excessive thermal intrusion into the cabin, improving passenger comfort and protecting interior components from heat-related degradation.
- Wiring Harnesses: The lightweight nature of aluminum wiring harnesses minimizes parasitic losses within the electrical system, leading to improved fuel efficiency (up to 0.5% potential gain).
- Powertrain
- Engine Components: Aluminum piston heads and manifolds exhibit superior heat dissipation compared to steel, enabling higher compression ratios and potentially boosting engine performance by up to 3%. Additionally, they contribute to weight reduction, further enhancing fuel efficiency.
- Transmission Components: Aluminum’s low friction coefficient reduces internal friction losses within the transmission, leading to improved fuel efficiency and smoother gear shifts.
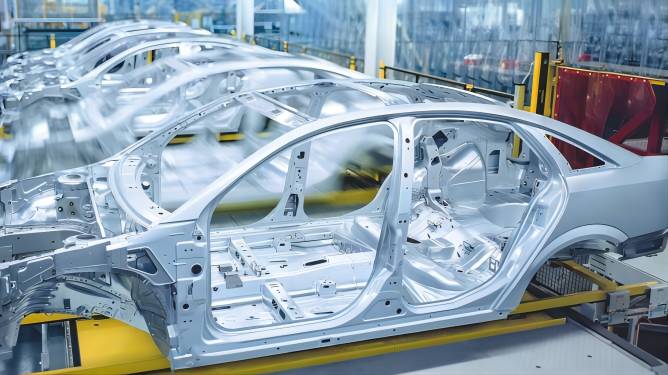
- Chassis and Suspension
- Suspension Parts: Aluminum control arms and knuckles offer significant weight reduction compared to steel, minimizing unsprung weight and enhancing handling dynamics. Improved agility, sharper turn-in response, and a smoother ride are some of the quantifiable benefits observed with aluminum suspension components.
- Chassis Components: Strategically reinforced chassis elements utilizing high-strength 6061 aluminum alloys maintain structural integrity while minimizing weight. This contributes to further fuel efficiency improvements and potentially enhances crashworthiness through optimized energy absorption pathways.
- Beyond the Core Structure
- Radiators and Condensers: Aluminum’s high thermal conductivity facilitates efficient heat transfer in radiators and condensers, improving engine cooling and potentially allowing for smaller and lighter components, further contributing to weight reduction.
- Air Conditioning Systems: Aluminum’s thermal properties enable the use of smaller and lighter air conditioning components while maintaining desired cooling capacity, reducing parasitic losses and contributing to improved fuel efficiency.
- Fuel Tanks (Emerging Application): While still in its early stages, aluminum fuel tanks offer potential benefits such as reduced weight and enhanced corrosion resistance compared to traditional steel tanks. This technology holds promise for future lightweight opportunities and improved fuel storage solutions.
Challenges in Aluminum Coil Integration: Technical Considerations and Future Directions
While aluminum coils offer significant advantages in automotive applications, their integration presents several challenges that require technical consideration and ongoing research:
1. Cost Competitiveness: Compared to steel, the initial cost of aluminum coils remains higher. This creates a trade-off between potential fuel efficiency gains and increased upfront manufacturing costs. Automotive manufacturers must carefully analyze the life-cycle cost benefits of aluminum, considering factors like fuel savings, reduced maintenance, and improved recyclability.
2. Dent and Scratch Resistance: While specific aluminum alloys like 5052 offer improved dent resistance compared to steel, the material’s inherent softness remains a concern. This necessitates the development of protective coatings and design strategies to minimize the risk of visible damage on exterior panels.
3. Joining Techniques: Joining aluminum coils with other materials, particularly steel, requires specialized techniques like riveting, welding, or adhesive bonding. These techniques often involve additional processing steps and infrastructure investment, impacting production costs and complexity. Ongoing research focuses on developing more efficient and cost-effective joining methods for optimized aluminum integration.
4. Strength and Stiffness Optimization: While high-strength aluminum alloys like 6061 exist, further research is vital to develop alloys with even greater strength and stiffness characteristics. This will expand the potential applications of aluminum beyond lightweight components and into structural elements where higher load-bearing capacity is crucial.
Addressing these challenges will be critical for maximizing the potential of aluminum coils in automobiles. Continued advancements in material science, joining technologies, and cost-reduction strategies will pave the way for even more widespread adoption of this lightweight and sustainable material in future vehicle designs.
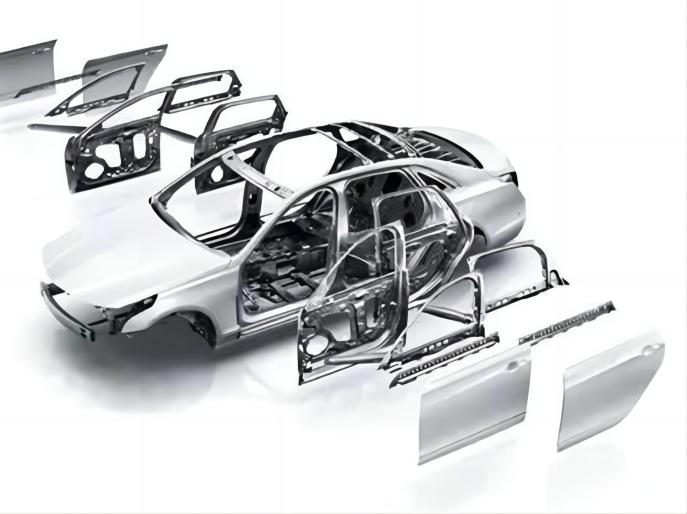
In conclusion, the integration of aluminum coils into modern automobiles represents a pivotal shift in automotive design philosophy. Driven by the pursuit of fuel efficiency and sustainability, this material metamorphosis is reshaping the very framework of vehicles. From shedding weight on body panels to optimizing the powertrain and chassis, aluminum coils offer a multitude of benefits, enhancing performance, reducing emissions, and contributing to a greener future. While challenges like cost and joining techniques remain, ongoing research and development promise to pave the way for even greater utilization of this lightweight wonder material. As the automotive industry continues its march towards ever-evolving efficiency and environmental consciousness, aluminum coils are poised to be the alchemized catalyst in the creation of the automobiles of tomorrow.