As the demand for aluminum profiles in the world is more urgent, at the same time, all aspects of the properties of aluminum profiles, such as profile surface quality, surface treatment performance, appearance color, mechanical properties, oxide film corrosion resistance, wear resistance, etc. requirements also getting higher. High-quality aluminum alloy extrusion profiles are the basis for obtaining high-quality building profiles. How ensure high-quality aluminum alloy ingots has become a particularly important part of the aluminum profile production process.
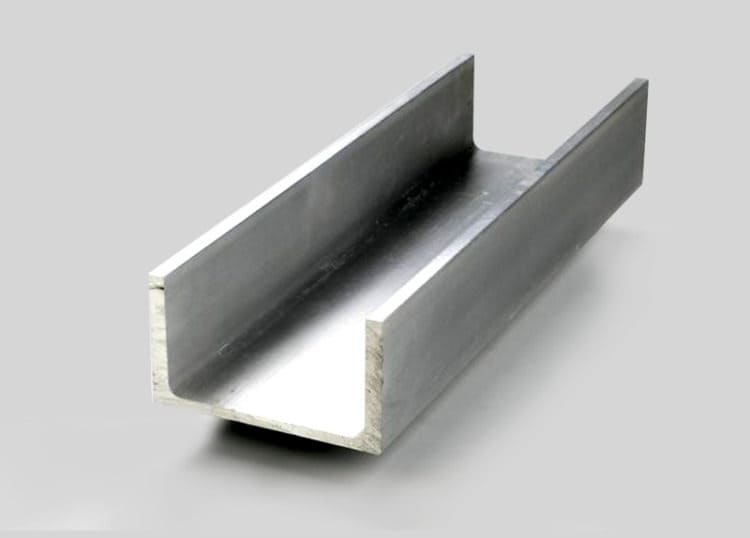
Factors Affecting The Crystallization Of Aluminum Alloy Ingots
The quality of the crystal structure of the aluminum alloy ingot not only affects the processing performance but also affects the quality of the final product. Therefore, in production, we strive to obtain a crystal structure with fine grains, dense structure, and uniformity. Generally, the effect of alloying factors on the ingot grains is not obvious, but in high magnesium alloys, with the increase of magnesium content, the grains can be refined, and alloys with less active trace elements are easy to form columnar crystals or coarse ones, etc. Axial grain structure, in order to stabilize and refine grains, grain refiners should be added in production. When the smelting is overheated, or when an inappropriately high temperature is used, the columnar crystal structure may be obtained. Increasing the cooling rate tends to reduce columnar crystallization, and if sufficient nuclei are formed, fine and uniform equiaxed crystals can be obtained. The casting speed is usually reduced, and the ingot grains are refined accordingly. The effect of ingot size usually results in grain refinement as the cross-sectional size of the ingot decreases.
Method For Refining Grains Of Aluminum Castings
Increase subcooling: This method is suitable for small and medium castings.
Modification treatment: Before the liquid metal crystallizes, add some small nucleating agents (also known as modifying agents, inoculants, or intermediate alloys) to make it evenly dispersed in the liquid metal as an artificial crystal nucleus, which can make the number of crystal grains significantly Increase, this method of grain refinement is called metamorphic treatment.
Vibration treatment: During crystallization, metal mechanical vibration, ultrasonic vibration, electromagnetic vibration, and other methods are applied to the molten metal.
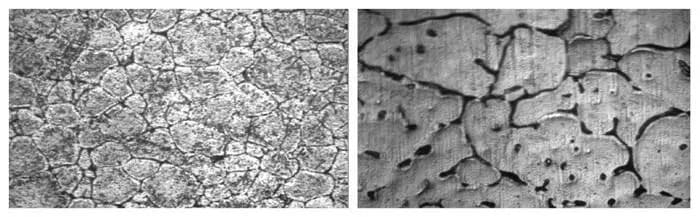
Selection Of Appropriate Casting Process Parameters
Casting process parameters also have a great influence on the quality of aluminum alloy ingots. The main process parameters that affect the quality of the ingot are cooling intensity, pouring speed, and pouring temperature. Although with the increase of cooling intensity, the tendency of the ingot to produce cracks increases, increasing the cooling intensity is beneficial to improve the ingot structure and mechanical properties and also helps to reduce the regional segregation of the ingot.
Under allowable conditions, high cooling intensity should be used as much as possible. High pouring speed and pouring temperature will increase the temperature gradient in the crystallization area of the ingot, thereby increasing the tendency to generate central cracks and form coarse-grained structures. If the pouring temperature and pouring speed are too low, it is easy to cause bright crystal grains and cold insulation, which is also not conducive to obtaining high-quality ingots. In actual production, the pouring temperature is generally 710℃-730℃, the cooling water temperature is not higher than 25℃, and the pouring speed should be determined according to the cooling strength and pouring temperature. On the premise of no defects, a high pouring speed should be used. to improve production efficiency. When pouring, it should be kept horizontal from the furnace mouth to the mold to prevent the liquid flow from destroying the oxide film on the surface of the melt and wrapping the oxide film in the melt due to the drop. At the same time, uniform flow should be ensured to avoid uneven distribution of liquid flow. Uniform flow can reduce temperature gradients, make the crystalline structure uniform, and help eliminate internal stress and cracks in the ingot.
In addition, the accurate selection of the raw materials for configuring the aluminum alloy is of great significance for controlling the alloy composition, ensuring the quality of the ingot, saving raw materials, and improving productivity and economic benefits.
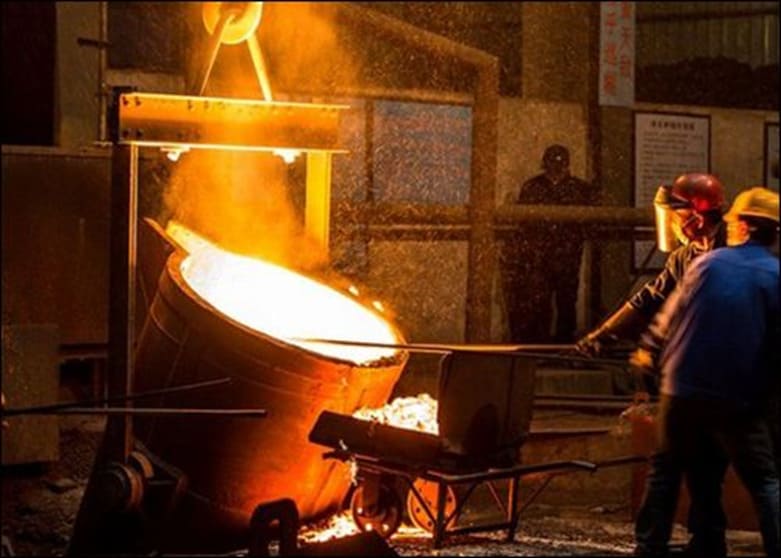
Aluminum Alloy Ingot Homogenization Treatment
Due to the existence of various segregation and low melting point eutectic structure and intermetallic compounds distributed in the intergranular and grain boundaries, the chemical composition and structure of the aluminum alloy ingot are not uniform, and the thermoplasticity of the ingot is weakened and the processability is reduced. This unbalanced structure eventually becomes the internal structure of the product, such as 3A2l alloy, the manganese segregation formed during casting, if not homogenized, will form coarse grains during final annealing.
In the ingot without homogenization, the impurity phase on the grain boundary and dendrite network is coarse Mg2Si, which will cause the following hazards during extrusion:
Increase squeeze force
Reduced extrusion speed
The strength index of aluminum profiles decreased
Poor quality of aluminum profiles
Reduce the life of the mold
In the extrusion process, when other reasonable processes are determined, if the cooling strength used in the cooling stage of the aluminum alloy ingot is not annealed or de-homogenized annealing is insufficient, it may lead to the occurrence of “die blocking.” Treatment can improve the inhomogeneity of chemical composition and structure, improve the plasticity of the alloy, reduce the deformation resistance, improve the processing performance of the ingot, and increase the extrusion speed to improve the processability and performance of the material.
Summary
The quality of extrusion ingots has a decisive influence on the quality of aluminum profiles, and high-quality extrusion ingots are the basis for obtaining high-quality aluminum profiles. This paper discusses the technical ways to improve the quality of aluminum alloy extrusion ingots from the aspects of the casting process parameters of aluminum profiles and the homogenization treatment of the ingots.