Soldering aluminium presents unique challenges due to the presence of a natural oxide layer that inhibits proper bonding between the metal and solder. Traditional soldering techniques used for copper and other metals often fail when applied to aluminium, necessitating specialized approaches. One of the most effective solutions is the use of aluminium flux paste, which helps to break down the oxide layer and promote better adhesion of the solder.
Understanding the chemistry and application of aluminium flux soldering is essential for professionals and hobbyists working with aluminium components. This article will explore how aluminium flux paste works, compare it with aluminum solder paste, and provide a detailed guide on effectively soldering aluminium with flux.
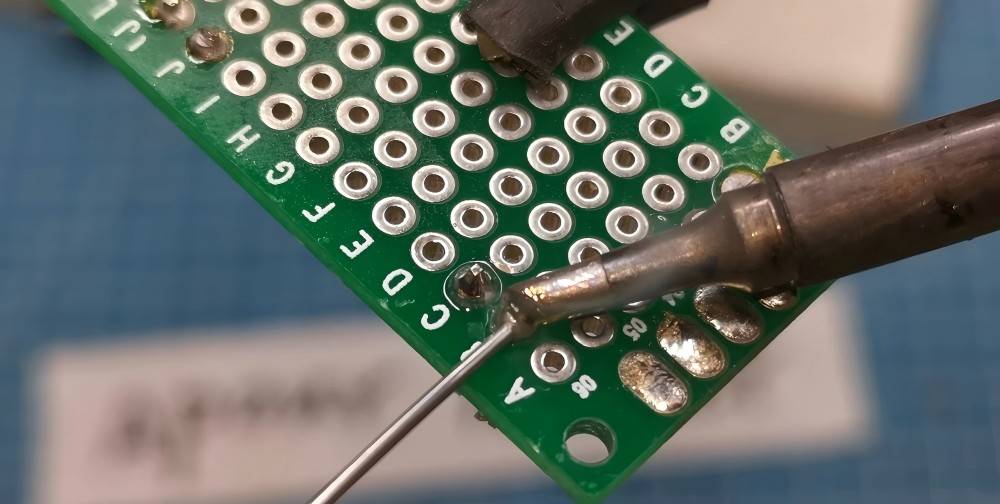
How Aluminium Flux Paste Works in Soldering
1. The Role of Flux in Soldering Aluminium
Flux is a chemical agent designed to remove oxidation and contaminants from metal surfaces to facilitate strong metallurgical bonds during soldering. Aluminium, in particular, forms an oxide layer almost instantly when exposed to air, which prevents molten solder from wetting the surface. Aluminium flux paste contains active ingredients that break down this oxide layer, allowing the solder to bond effectively.
2. Chemical Composition of Aluminium Flux Paste
Most aluminium flux pastes contain a combination of:
- Hydrofluoric acid salts – These aggressively break down aluminium oxide.
- Zinc chloride or ammonium chloride – These serve as additional cleaning agents.
- Organic binders and activators – These stabilize the flux and help with solder flow.
3. How Does Aluminium Flux Work in Soldering?
The efficacy of aluminium flux soldering hinges on its ability to perform several critical functions:
1) Chemical Reaction with Aluminium Oxide:
The flux’s corrosive components, often fluorides or chlorides, react with the aluminium oxide (Al₂O₃), converting it into soluble salts. This chemical reaction removes the oxide layer, exposing the clean aluminium surface.
2) Preventing Re-oxidation During Soldering:
During the heating process, aluminium rapidly re-oxidizes. The flux acts as a protective barrier, shielding the cleaned surface from atmospheric oxygen and preventing further oxide formation. This allows the solder to make direct contact with the base metal.
3) Promoting Wetting of the Solder:
Effective wetting, the ability of molten solder to spread and adhere to the base metal, is crucial for a strong joint. The flux reduces the surface tension between the molten solder and the aluminium, enhancing wetting and promoting a uniform bond.
4. Types of Aluminium Flux Pastes and Their Characteristics
Various flux paste formulations exist, catering to specific applications and aluminium alloys. Understanding their characteristics is essential for optimal performance.
- Corrosive fluxes: These are powerful, but require thorough cleaning post soldering to mitigate corrosion.
- Non-Corrosive fluxes: newer flux options that are less corrosive are becoming more common.
It is critical to follow the manufacturer’s data sheets for each flux, as they contain important information relating to safety, and cleaning.
5. Safety Precautions When Using Aluminium Flux
Aluminium flux pastes often contain corrosive chemicals. Appropriate personal protective equipment (PPE), including gloves, eye protection, and respiratory protection, is mandatory. Proper ventilation is essential to avoid inhaling harmful fumes. Additionally, meticulous cleaning of flux residues after soldering is crucial to prevent long-term corrosion.
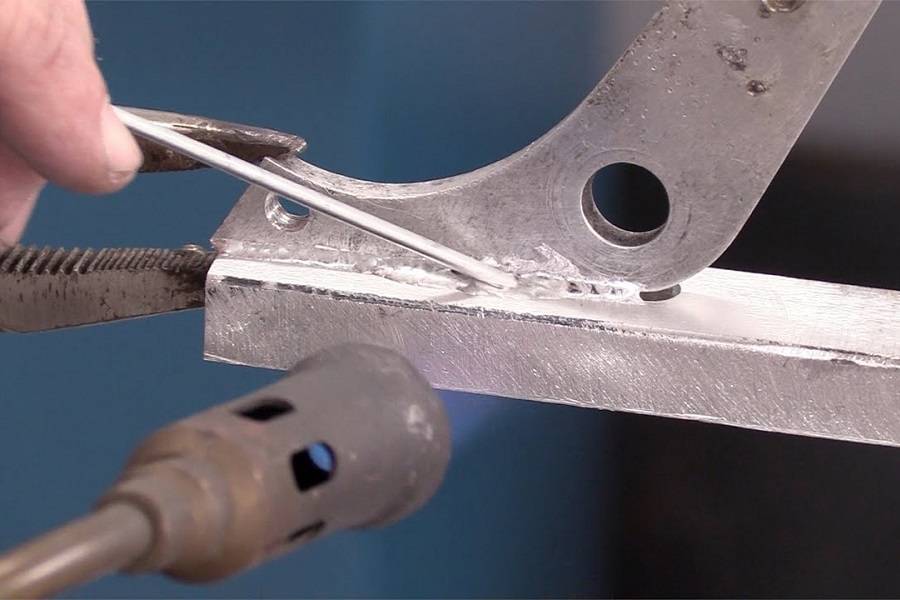
Aluminium Flux vs. Aluminium Solder Paste: Which One to Use?
Both aluminium flux paste and aluminum solder paste are used in aluminium soldering applications, but they serve different functions. Choosing the right product depends on the specific requirements of the project.
1. Aluminium Flux Paste
Aluminium flux paste is primarily a cleaning agent that facilitates solder adhesion by removing oxidation. It is used in conjunction with a separate solder alloy, typically an aluminium-compatible solder containing elements like zinc or tin. This method is preferred when working with large aluminium components or when precise control over solder application is needed.
Best for:
- Manual soldering with a soldering iron or torch
- Applications requiring strong mechanical joints
- Repairs and maintenance of aluminium components
2. Aluminium Solder Paste
Aluminium solder paste combines flux and solder particles in a single formulation, eliminating the need for separate flux applications. It is commonly used in surface-mount technology (SMT) and other precision soldering applications where automated or mass production processes are involved.
Best for:
- Surface-mount soldering of aluminium components
- Automated or reflow soldering applications
- Thin or small aluminium parts requiring minimal solder application
3. Choosing the Right Option
Feature | Aluminium Flux Paste | Aluminium Solder Paste |
Composition | Flux only | Flux + solder alloy |
Application | Manual soldering, repairs | Automated, precision soldering |
Oxide removal | Stronger | Moderate |
Use case | Large components, heavy-duty applications | SMT, small component soldering |
For general aluminium soldering with a soldering iron, aluminium flux paste is the preferred choice. However, for precision or automated applications, aluminum solder paste may be more effective.
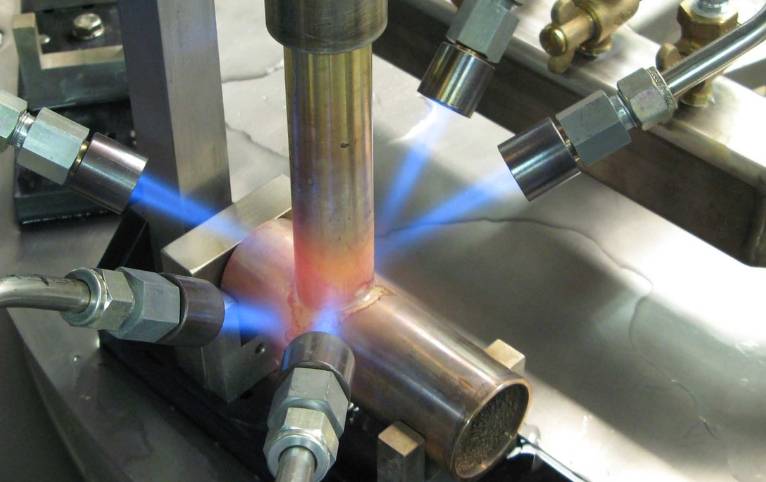
How to Solder Aluminium with Flux
Soldering aluminium with flux requires careful preparation and execution to achieve strong, reliable joints. Follow this step-by-step guide for the best results:
Step 1: Gather Required Materials
To solder aluminium, you will need:
- Aluminium flux paste
- Aluminium-compatible solder (e.g., zinc-based solder)
- A high-power soldering iron or torch (at least 50W)
- Clean lint-free cloths or a wire brush
- Isopropyl alcohol for cleaning
- Heat-resistant gloves and safety goggles
Step 2: Surface Preparation
Clean the aluminium surface thoroughly to remove dirt, grease, and existing oxidation:
- Use a wire brush or fine sandpaper to mechanically remove surface contaminants.
- Wipe the area with isopropyl alcohol to ensure it is free from grease and oils.
- Apply a thin layer of aluminium flux paste evenly over the soldering area.
Step 3: Heating the Aluminium
Aluminium dissipates heat quickly, so adequate heat application is crucial:
- Set your soldering iron to at least 350°C (662°F) or use a small torch.
- Apply heat evenly to the joint area until the flux becomes active (it may bubble or change color).
Step 4: Applying the Solder
- Once the aluminium is adequately heated, introduce the solder alloy.
- Ensure the solder wets the surface properly and forms a strong bond.
- Continue heating until the solder fully melts and spreads.
Step 5: Cooling and Cleaning
- Allow the joint to cool naturally to avoid thermal stress.
- Clean off flux residues with isopropyl alcohol to prevent corrosion.
Common Mistakes and Troubleshooting
Mistake | Cause | Solution |
Solder does not adhere | Incomplete oxide removal | Use more flux and heat evenly |
Excessive oxidation | Insufficient flux coverage | Apply flux more generously |
Weak solder joints | Incorrect solder type | Use an aluminium-compatible solder |
Overheating | Prolonged heat exposure | Use a controlled heating approach |
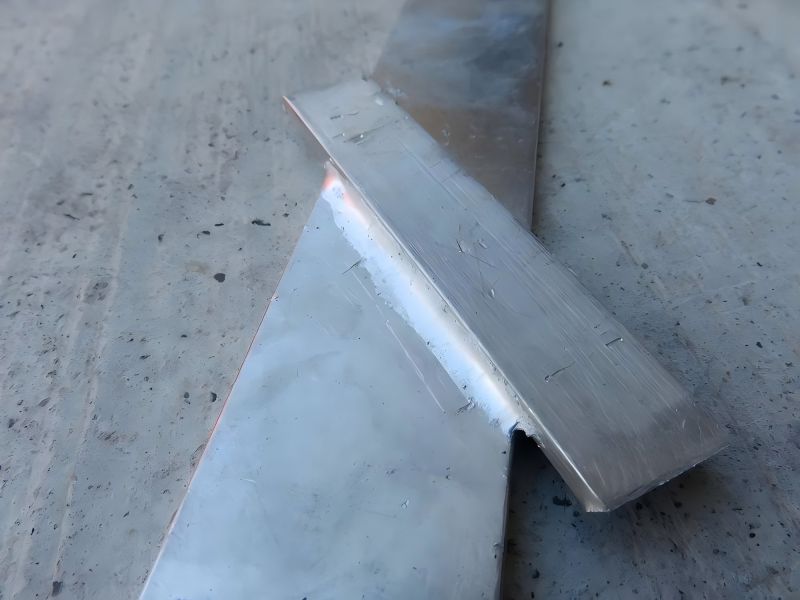
Wrap Up
Soldering aluminium effectively requires the use of aluminium flux paste to remove oxide layers and enhance solder adhesion. Whether choosing aluminium flux paste for manual applications or aluminum solder paste for automated processes, selecting the right product is critical for achieving strong, reliable joints.
By following proper preparation, heating, and soldering techniques, aluminium components can be successfully soldered for a variety of applications. Understanding the nuances of aluminium flux soldering ensures better results and prolonged durability of soldered joints in both industrial and DIY settings.