Aluminium EV Battery Shell
- At present, our company mainly engages in three major sectors: thin-walled precision high-frequency welded pipes, precision stamping parts, and new energy long cell battery shells.
- Applied to: automotive water tanks, intercoolers, oil coolers, household air conditioners, and new energy vehicle power battery systems.
- The new energy vehicle long cell battery shell sector, as the company’s main strategic development direction in the future, will become the main sector for the company’s transformation from the traditional automotive industry to the new energy vehicle industry.
- EV power and thermal management related products:
- Aluminium EV Battery Shell
- Inverter cover plate
- Water-cooling plate
Core Components of Aluminium EV Battery Shell – Long Cell Battery Case
- The new energy long cell battery shell developed and produced by our company adopts a cold bending forming+high-frequency welding process, which breaks through the constraints of traditional deep drawing/extrusion processes and overcomes the welding technology of ultra-thin aluminum shells. We have successfully developed an ultra-long and ultra-thin aluminum shell battery with a thickness of 0.3mm。
- Breaking the traditional module concept of battery systems, utilizing the unique aspect ratio characteristics of batteries to achieve reasonable flattening under a certain volume, while also improving battery energy density and increasing cell heat dissipation area, greatly reducing battery manufacturing costs
Aluminium EV Battery Shell Parameters
Item | Data |
Width range(mm) | ≤240mm |
Height range(mm) | ≤40mm |
Thickness(mm) | T=0.3-0.5mm |
Material core | AA3003/AA3005 |
Length range(mm) | 200mm-5800mm |
Certificate | IATF16949-2016/CE-PED/ISO14001/DUNS |
Aluminium EV Battery Shell Manufacturing Process
Cold bending forming+high-frequency welding process:
The pipe making machine rolls a certain specification of raw materials (rectangular sheet material with coils) into the desired shape through different rollers, performs high-frequency welding, and then undergoes the shaping process to obtain the required specification of the product.
- Low heat loss, fast heating, and high thermal efficiency
- Clean production process, Less high temperature
- One-time forming, tightly combined, with high dimensional accuracy
- Unlimited length, up to 6000mm
Advantages of Aluminium EV Battery Shell
- High thin-walled strength: Aluminum alloy material, with thin pipe walls and high strength, thinnest pipe to nearly 0.3mm, effectively improving heat dissipation efficiency and reducing product weight.
- High temperature corrosion resistance: The simulated aging test of the aluminum alloy shell shows that its service life is more than 20 years. Among the metal materials, the aging resistance of aluminum far exceeds that of other traditional metal materials.
- Good heat conduction: The advantages of one-time forming include tight bonding, low thermal resistance, good heat condution, and low flow loss.
- High dimensional accuracy: The product has high dimensional accuracy and small tolerance, and can provide multiple sizes and lengths according to customer requirements.
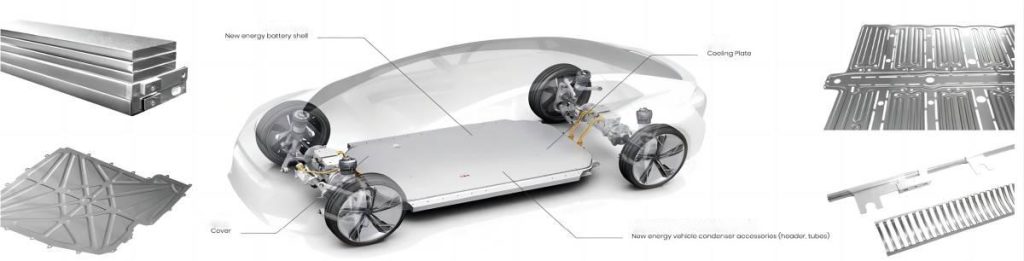
Comparisons Between Traditional Stretched Square Aluminum Shells and High-frequency Welded Long Cell Shells
High-frequency Welded Long Cell Shells
- The high-frequency welding shell is made of aluminum alloy material, with thin pipe walls and high strength. The thinnest pipe wall is close to 0.3mm, effectively improving heat dissipation efficiency and reducing product weight.
- High frequency welding, uninterrupted welding length from 100mm-6 meters, with a larger coverage range compared to stretched battery shell size, and can be flexibly customized according to needs.
- High frequency welding, one-time forming, uniform wall thickness, low thermal resistance, good heat transfer performance, low flow loss, and other advantages.
- High dimensional accuracy and small tolerance of products.
- Reliable raw material guarantee
Traditional Stretched Square Aluminum Shells
- The stretched shell is affected by the ductility of aluminum, with a minimum thickness of only 0.6mm, heavy weight, and low heat dissipation efficiency.
- The tensile limit length is below 370mm, and the optional size range is relatively narrow.
- Low dimensional accuracy and poor surface quality of the stretched shell.
- Variable wall thickness, large range of stretching operation, easy to stretch too high will produce surface water ripple Fried Dough Twists marks, low elongation, high hardness, brittle, low plasticity. Low tensile strength and hardness of the aluminum shell of the power battery can lead to low compressive strength and hardness, and the profile is prone to curved and tortuous shapes. Impact on battery stability
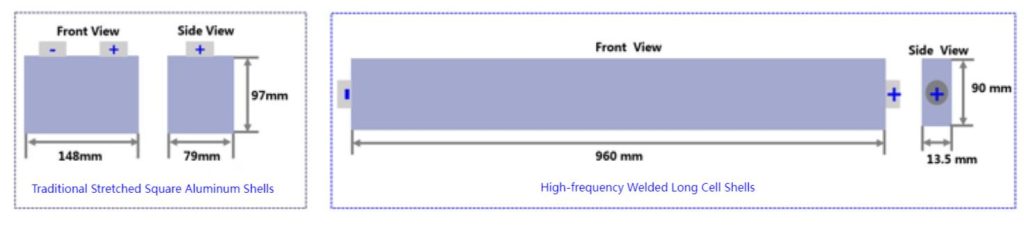
Comparisons Between Traditional Stretched Shell Battery Packs and High-frequency Welded Long Cell Shell Battery Packs
High-frequency Welded Long Cell Shell Battery Pack
- Improved battery energy density: The module design has been canceled, reducing many structural component designs. Meanwhile, the upper and lower boxes are tightly connected to the battery cells, resulting in a significant increase in volume energy density, with a 50% increase in volume energy density.
- Low cost: Canceled module design, optimized battery structure design, reduced the number of secondary components by 40% and applied a low-cost LFP system, which effectively reduced costs.
- Good structures: PACK is designed on the upper and lower sides of the battery cell, using structural adhesive to stick two high-strength plates, forming a structure similar to honeycomb aluminum plates, allowing each battery cell to serve as a structural beam. When there is a collision at the bottom of the battery, the battery cell can directly withstand a certain range of force.
- Excellent thermal management: The liquid cooling plate of high-frequency welded long cell batteries is arranged above the cell, and a thermal conductivity layer is designed between the cell and the cell. This scheme has a much larger heat exchange area than traditional square cells, which can effectively transfer the heat of the cell to the water cooling plate. In addition, high-frequency welded long cell batteries have good heat dissipation performance, so the thermal management design of high-frequency welded long cell batteries is excellent.
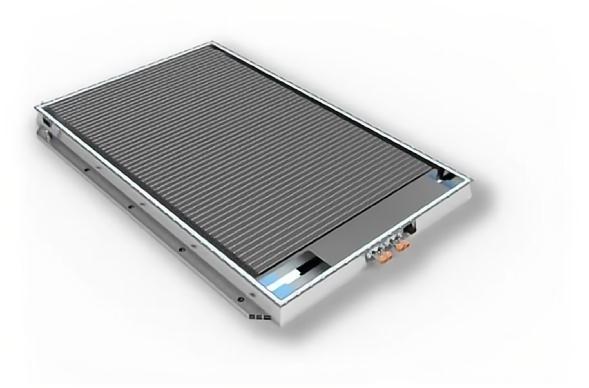
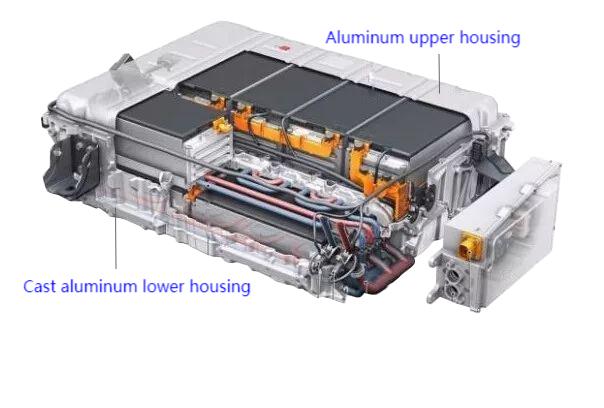
Traditional Stretched Shell Battery Pack
- Multiple cell units are arranged, resulting in high consumption of structural components, large volume, and spatial layout. Under the same conditions, the energy density is low.
- Thick material, multiple attachments, and high cost
- The battery pack is heavy, the battery management system has multiple tasks, monitoring is difficult, and the range is low.
Application of Aluminium EV Battery Shell
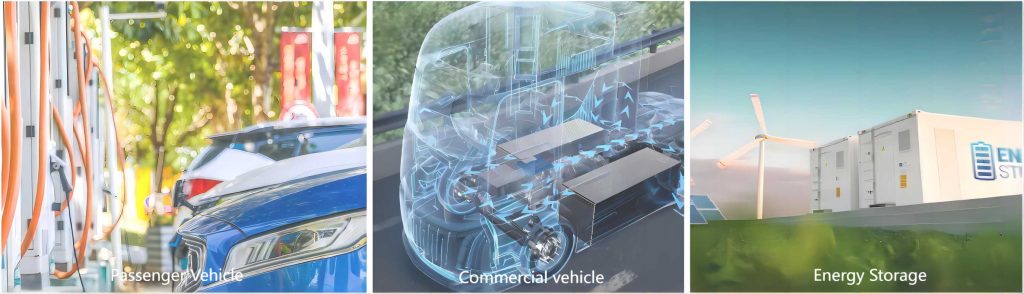
How to start our cooperation (procedures)?
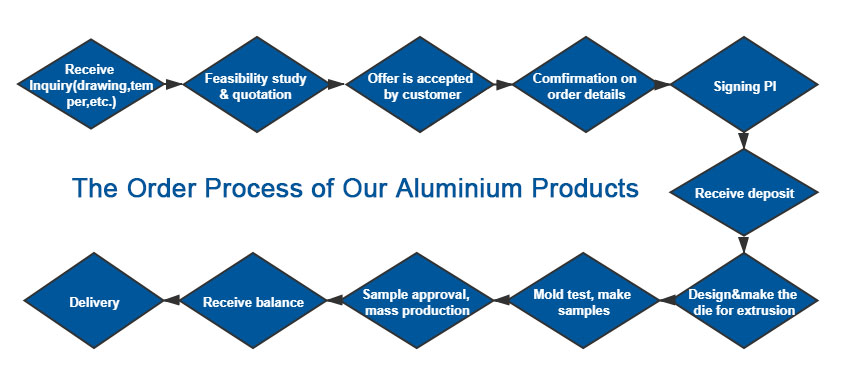
CHAL Aluminium Corporation focuses on the research and development of aluminum, we work with a famous academic institution and industrial association. Our researchers and academic partners take part in the business & technical development of the processing and producing aluminum products. We work on moving boundaries of how aluminium is used. We develop and design solutions that benefit the improvement of aluminum performance both technically and economically. CHAL Aluminium Group has 5 R/D centers across China.
Patents
35 Invention Patents and 198 Utility Model Patents are certified.
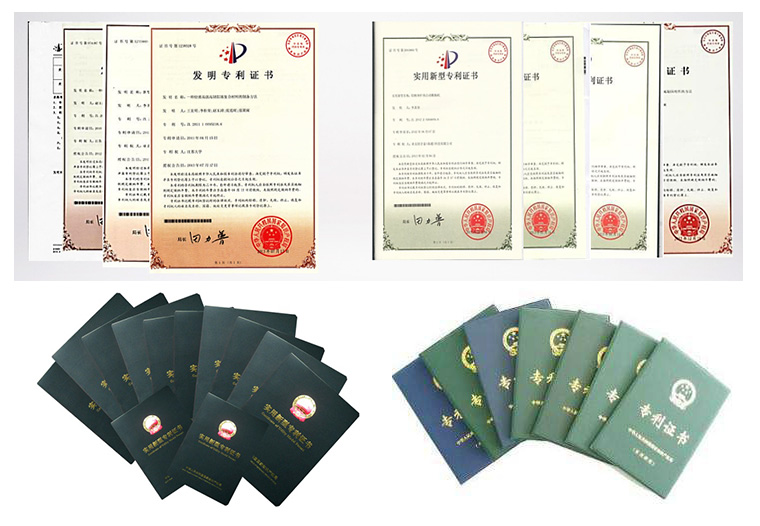
Certificates
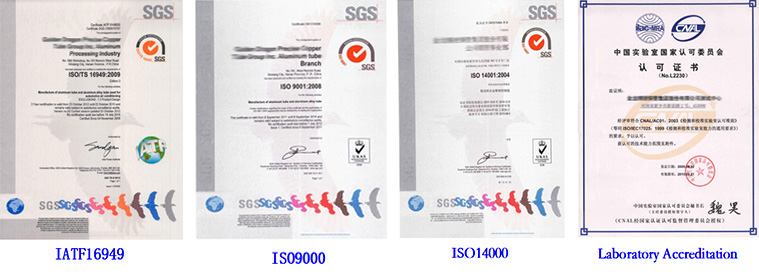
Testing Instruments
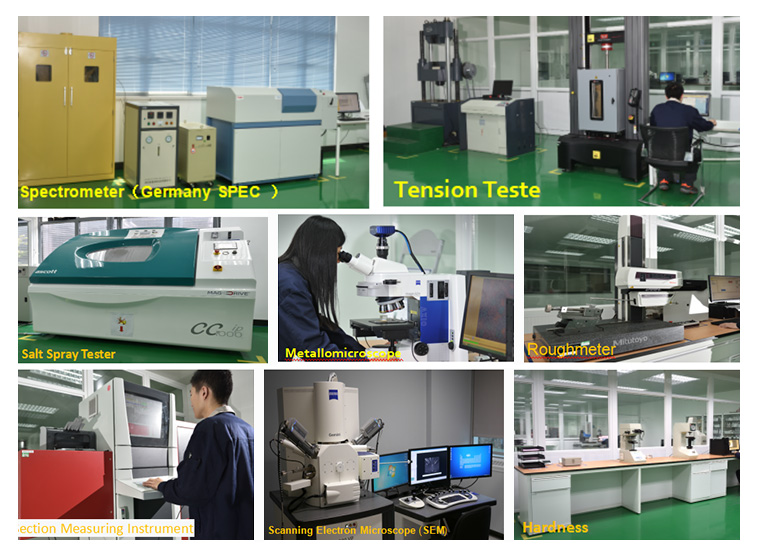
Cooperation Partners
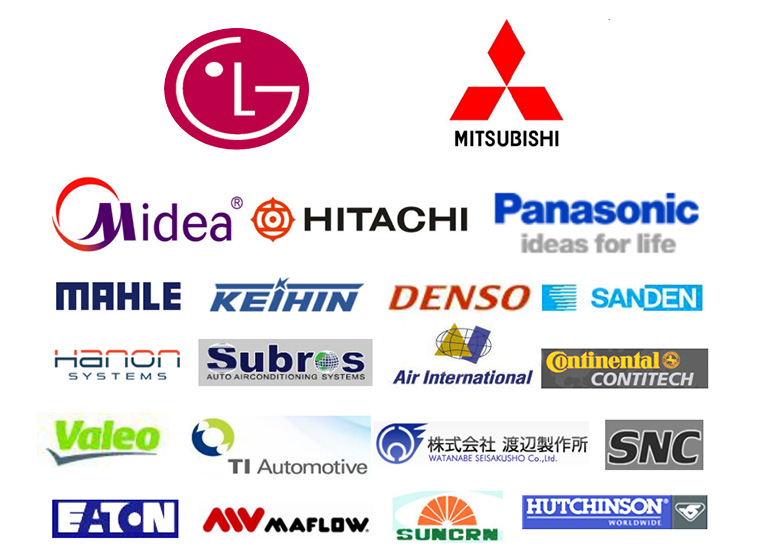