Researchers at Pacific Northwest National Laboratory have recently demonstrated an advanced fabrication process that can produce nanostructured rods and tubes directly from high-performance aluminum alloy powders. Using a new solid-phase treatment method, the research team reduced several steps in the traditional extrusion process of aluminum alloy powder, while significantly improving the ductility of the product. This is good news for automobiles and other industries because the high cost limits the use of high-strength aluminum alloy powder in manufacturing. The research results were published on Materialia.
New processing technology to obtain new aluminum profiles
High-performance aluminum alloy made of powder has been used for light components for a long time, and its cost is not a limiting factor for professional aerospace applications. However, these alloys are too expensive for the automotive industry.
The typical aluminum alloy powder extrusion process is high energy consumption and process intensive, which requires multiple steps for mass production. First, the loose powder must be put into a tank and vacuumized, which is called “degassing”. Then seal, hot press, preheat, and put the tank into the extruder. After extrusion, the cans are removed or “decanted” to show the extruded parts made of consolidated powder.
In this study, the team omitted some steps and used PNNL’s shear-assisted processing and extrusion technology or ShAPE ™ Nanostructured aluminum rods extruded directly from the powder. Aluminum alloy is directly extruded from powder metallurgy, canning, degassing, hot isostatic pressing, can stripping and billet preheating.
In ShAPE ™ In the process, in this case, the Al-12.4TM aluminum alloy powder provided by SCM Metal Products, Inc., a subsidiary of Kymera International, is poured into an open container. The rotary extrusion die is then pressed into the powder to generate heat at the interface between the powder and the die. The material is soft and easy to extrude, without canning, degassing, hot pressing, preheating, or decanting.
“This is the first time to use ShAPE ™ Such a single-step process is an example of combining aluminum alloy powder into a nanostructure extrusion, “said Scott Whalen, a PNNL material scientist in charge of the research. Follow the WeChat official account of Materials Science and Engineering to get more knowledge. “Eliminating the need for processing steps and preheating can greatly shorten the production time, and reduce the product cost and overall embedded energy, which may be beneficial for automobile manufacturers who want to manufacture passenger cars. They can provide consumers with more affordable, lighter, and more fuel-efficient products.”
In addition to providing Al-12.4TM powder, SCM Metals Products, Inc Mechanical tests were also carried out to verify the properties of the resulting materials. PNNL and SCM Metal Products, Inc. are currently cooperating on the DOE Technology Transformation Office project to expand the process of larger-diameter extrusion.
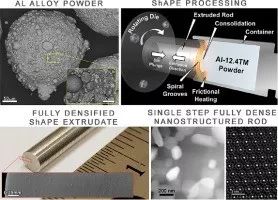
Aluminum profiles with better ductility
Cutting back on processing steps and heating was not the team’s only successful discovery. Although high-performance aluminum alloys have historically shown excellent strength, they are often hampered by poor ductility. However, the team found that ShAPE ™ The ductility of the aluminum alloy extruded by the method is significantly improved, and the measured ductility is two to three times that of the traditional extruded products and has the same strength.
To understand the reason for the significant increase in ductility, transmission electron microscopy was used to evaluate the microstructure of powders and extruded materials. The results show that ShAPE ™ The method improved the second phase in the powder – the micro-strengthening particles of nonaluminum materials. ShAPE ™ The particles can be reduced to nanometer size and uniformly distributed in the entire aluminum matrix, thus improving the ductility.