As a multi-purpose building material, aluminum profile is a sustainable non-ferrous metal with “green” environmental protection characteristics due to its good performance, easy processing, recyclability, lightness, corrosion resistance, and irreplaceable advantages of other building materials. High-quality aluminum alloy profile extrusion is the basis for high-quality aluminum alloy building profiles. How ensure high-quality extrusion ingots has become a particularly important part of the aluminum profile production process.
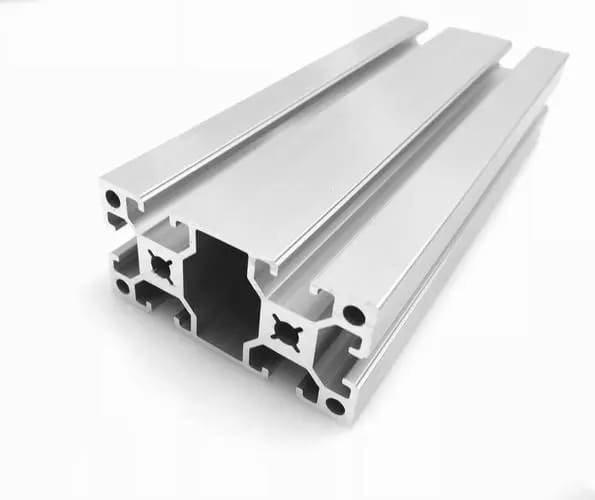
The Strict Control Of Chemical Composition
The content range of chemical elements of the aluminum alloy profile is relatively wide, and online chemical composition control is relatively easy. The influence of alloy properties ensures that ideal properties are obtained, and the yield is improved to achieve better economic benefits.
The main alloying elements of aluminum alloy profile extrusion profiles are magnesium and silicon. As the main alloying element, magnesium will produce solid solution strengthening and improve the work-hardening rate of the alloy. Magnesium can form β (Mg5Al8) phase with aluminum, but cannot produce precipitation. Strengthening, the size, and distribution of β(Mg5Al8) phase have a significant impact on the corrosion resistance of the alloy. If it is distributed in the grain boundary in a chain shape, it will cause intergranular corrosion and stress corrosion cracking. If it is uniformly dispersed in the grain and grain boundaries, the corrosion resistance is improved.
The Strict Control Of Smelting Operations
To ensure that the impurity content in the alloy is within the control range, the smelting operation process of smelting raw materials should also be strictly controlled. The impurity elements mainly come from raw materials, especially the wastes used with the original aluminum ingots generally have a high content of impurity elements, and the proportion of the original aluminum ingots and scraps should be paid attention to when batching. Generally, aluminum ingots for remelting are used, no or less scrap aluminum is used, and an appropriate amount of aluminum alloy scrap can be used. In addition, it is also important to clean and wash the smelting furnace, which helps to remove residual impurities in the furnace. The operation during the smelting process may increase the iron content, and attention should be paid to coating the surface of the operating tool with isolation and a protective layer.
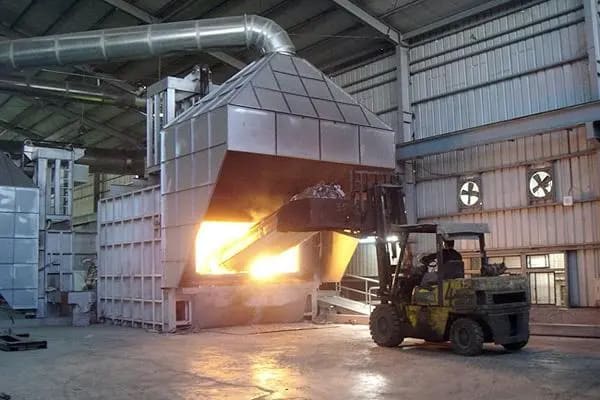
Ensure The Melt Quality Of The Aluminum Alloy Profile
Ensuring the melt quality of the aluminum alloy profile is of great help in improving the quality of the ingot. The melt temperature is not uniform or overheated, the residence time is long, the melt burning loss is large, the slag and gas content increases, the chemical composition is not easy to control, and the tendency of the ingot to produce central cracks and columnar crystal structure will also increase. The melt temperature should be avoided to be too high, the time of the melt in the furnace and the standing furnace should be shortened, and a large temperature gradient should be avoided when the casting is cooled. However, the melt temperature should not be too low, otherwise, the melt fluidity will be weakened, and defects such as cracking on the surface of the ingot are prone to occur. Therefore, it is very important to select the appropriate melt temperature, ensure uniform temperature, and shorten the melting time. Generally, it is more appropriate to keep the temperature of the melt between 740-760 °C.
The presence of gas and slag is very harmful to the quality of the ingot. To reduce the slag and gas content in the melt as much as possible, the melt should be refined with flux and gas twice during the smelting process. To obtain a good degassing and slag removal effect, the content and purity of each component in the solvent refining agent and refining gas must be guaranteed, and the existence of impurities and moisture must be minimized.
After the refining is completed, to prevent the melt from re-oxidation and gettering, a covering agent is used to cover the melt surface. Before pouring, the alloy melt is filtered by glass cloth and foam ceramic filter plate to further reduce the content of impurities in the melt and purify the melt.
Summarize
To obtain high-quality aluminum alloy profile extrusion ingots, reasonable chemical components should be selected and controlled within a certain range. At the same time, the charge and smelting process should be strictly controlled to ensure the effect of melt quality.