Batteries are the lifeblood of our modern, mobile society, powering everything from smartphones to electric vehicles. As the demand for more efficient and sustainable energy solutions grows, manufacturers are constantly innovating to enhance the performance and longevity of batteries. One critical component that plays a pivotal role in the durability and safety of batteries is the battery cover. In recent years, aluminum has emerged as a material of choice for these covers due to its unique combination of properties. This article provides a comprehensive review of aluminum battery covers, examining the materials used, design considerations, and the manufacturing processes involved.
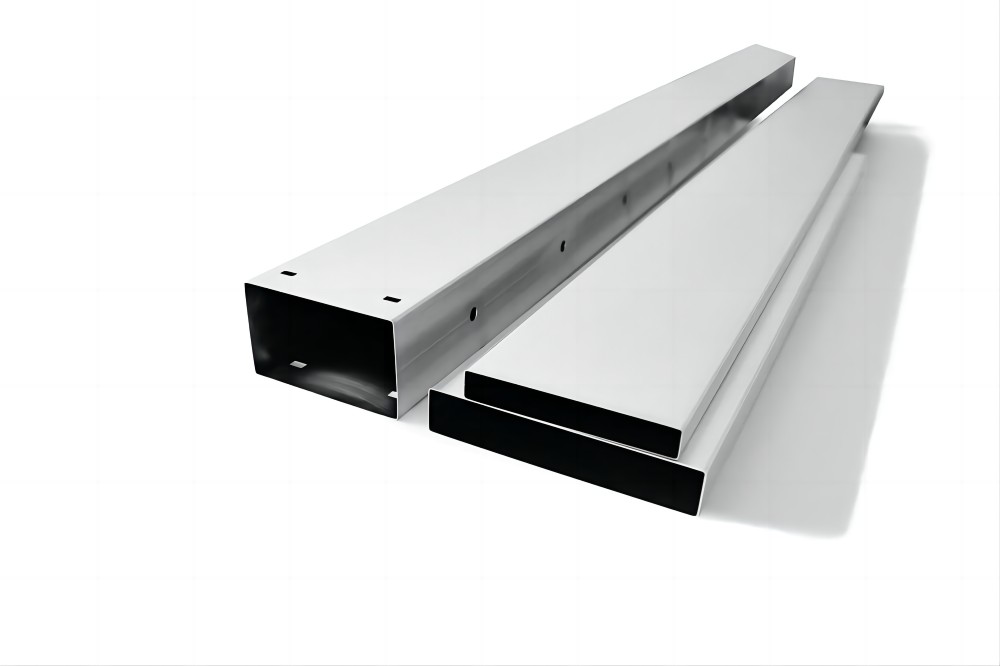
Materials: The Aluminum Advantage
The most common EV battery casing materials are:
- Aluminum: Aluminum is a lightweight and strong material that is well-suited for battery casings. It is also resistant to corrosion and can be easily formed into complex shapes. However, aluminum is more expensive than other materials, such as steel.
- Steel: Steel is a strong and durable material that is also relatively inexpensive. However, steel is heavier than aluminum and is more susceptible to corrosion.
- Composites: Composites are materials that are made from a combination of two or more different materials. Common composites used for EV battery casings include carbon fiber-reinforced plastic (CFRP) and glass fiber-reinforced plastic (GFRP). Composites are very strong and lightweight, but they can be more expensive than other materials.
The choice of battery casing material depends on a number of factors, including cost, weight, durability, and manufacturability. For example, a high-performance EV that needs to be lightweight may use a CFRP battery casing, while a more affordable EV may use a steel battery casing.
Aluminum is a lightweight, corrosion-resistant metal known for its excellent conductivity and strength-to-weight ratio. These properties make it an ideal choice for battery covers, which must balance structural integrity with weight considerations. Aluminum’s corrosion resistance is particularly crucial, as batteries often operate in challenging environments that can accelerate the degradation of other materials. The ability of aluminum to resist corrosion helps ensure the long-term reliability of battery covers.
Moreover, aluminum’s high thermal conductivity contributes to efficient heat dissipation, a critical factor in preventing the overheating of batteries during operation. This property is especially important in high-performance batteries, such as those used in electric vehicles, where excess heat can impact both safety and overall battery lifespan.
In recent years, there has been a growing interest in using composites for EV battery casings. Composites offer a number of advantages over traditional materials, such as aluminum and steel. Composites are stronger and lighter than traditional materials, which can improve vehicle performance and range. Composites are also more resistant to corrosion and can be molded into complex shapes, which can reduce assembly costs.
As the EV market continues to grow, we can expect to see more automakers using composites for battery casings. Composites offer a number of advantages over traditional materials, and they are likely to play an important role in the future of EV design.
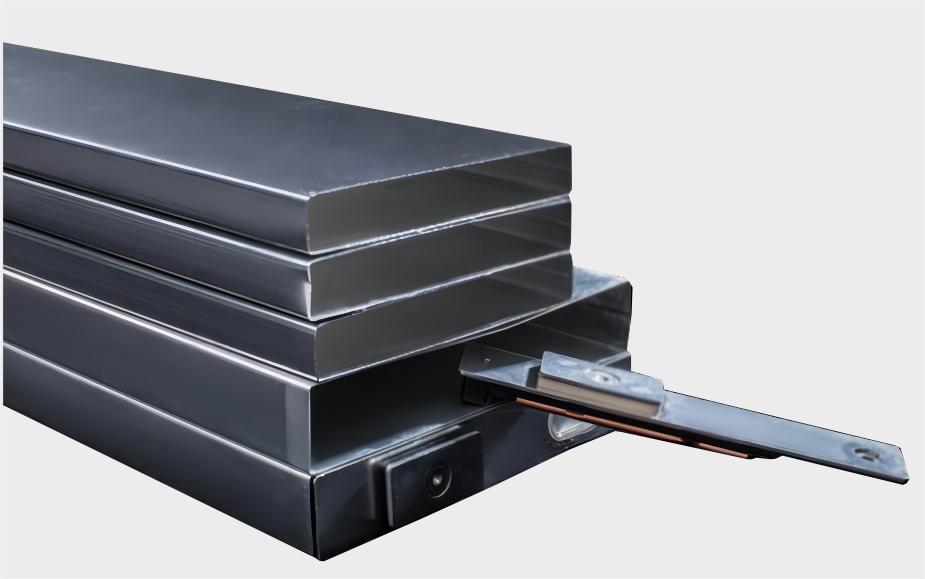
Design Considerations: Striking the Right Balance
The design of aluminum battery covers involves striking a delicate balance between structural integrity, weight, and manufacturability. Engineers must consider factors such as the specific battery type, size, and application when designing covers that offer optimal protection and performance.
One key design consideration is the integration of cooling features. Aluminum battery covers often incorporate fins, channels, or other heat-dissipating structures to enhance thermal management. These designs help regulate the temperature of the battery during operation, mitigating the risk of thermal runaway and improving overall efficiency.
Additionally, the design must account for ease of assembly, ensuring that the cover can be securely and efficiently integrated into the battery pack. The use of advanced modeling and simulation tools has become commonplace in the design phase, allowing engineers to optimize cover designs for both performance and manufacturability.
Manufacturing Processes: Precision and Efficiency
The manufacturing of aluminum battery covers involves a series of precise processes to ensure the final product meets the demanding requirements of modern battery technology. Common manufacturing techniques include die casting, extrusion, and stamping.
Die casting is a popular method for producing intricate and complex aluminum battery covers with high precision. This process involves injecting molten aluminum into a mold, allowing for the creation of detailed and geometrically complex designs. Die casting is not only efficient but also enables the production of covers with consistent quality.
Extrusion, on the other hand, is a cost-effective method suitable for simpler designs. It involves forcing aluminum through a die to create a specific shape. While not as intricate as die casting, extrusion remains a viable option for certain battery cover applications.
Stamping is another manufacturing process that involves cutting, bending, and shaping sheet metal into the desired form. This method is well-suited for high-volume production and offers a good balance between precision and cost-effectiveness.
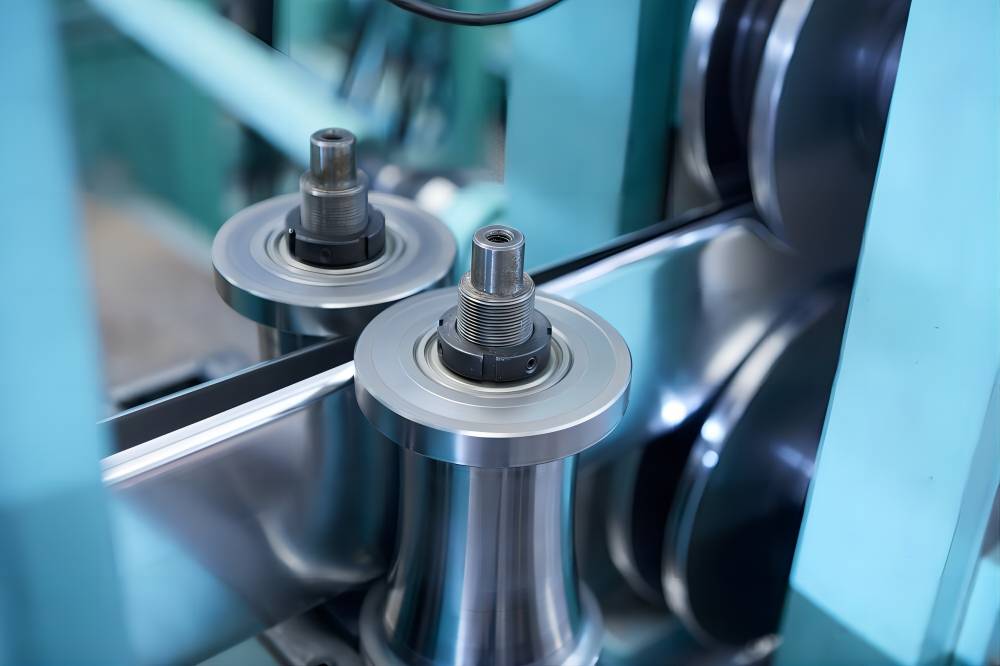
Conclusion: Advancing Battery Technology with Aluminum Covers
Aluminum battery covers are a critical component of EVs. They offer a number of benefits, including lightweight, durability, corrosion resistance, and recyclability. The market for aluminum battery covers is expected to grow significantly in the coming years due to the increasing popularity of EVs and the need for lightweight and durable battery covers. The automotive industry is investing heavily in the development of aluminum battery covers. For example, in 2022, Ford announced a $500 million investment in a new aluminum battery cover plant in Kentucky. Aluminum offers a number of advantages over traditional materials, such as steel, and it is likely to play an important role in the future of EV design.