In modern manufacturing, the reliability and efficiency of metal connection technology directly determine the performance and life of the product. Its lightweight nature and corrosion resistance make it a highly desirable material across industries, from aerospace to automotive. However, traditional welding methods can be tricky, often leading to distortion, cracking, or weakening of the base metal. What if there was a more precise, reliable, and elegant solution? The secret lies in understanding and utilizing the power of aluminum brazing wire. This seemingly simple material holds the key to creating flawless, high-strength joints in aluminum and its alloys. Here we will delve into the world of aluminum brazing wire, revealing its properties, applications, and the techniques needed to master the art of flawless metal joining.
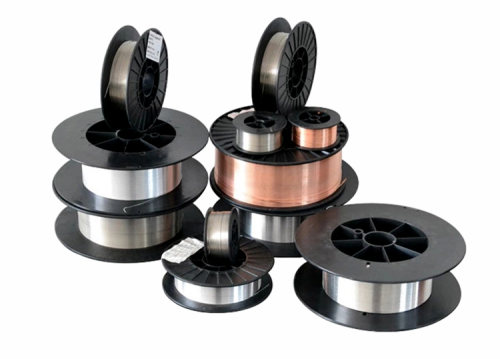
What is Aluminum Brazing Wire?
Aluminum brazing wire is a filler metal specifically designed for joining aluminum components through the brazing process. Unlike welding, which melts the base metals, brazing involves heating the base metals to a temperature below their solidus, while the brazing wire melts and flows into the joint, creating a strong metallurgical bond.
Composition and Properties:
Aluminum brazing wires are not pure aluminum. They are alloys, carefully formulated with other elements like silicon, magnesium, and copper to achieve specific properties. The typical composition is Al-Si series (such as 4043 alloy contains 5% Si, and 4047 alloy contains 12% Si). The addition of silicon significantly reduces the melting point (from 660℃ of pure aluminum to 570-600℃), while improving the fluidity and wettability of liquid metal. Some high-end welding wires also incorporate magnesium (Mg) or rare earth elements to enhance oxidation resistance and joint strength. Its core characteristics include:
- Low melting point: avoid deformation of the base material due to high temperature.
- High diffusivity: penetrate into micron-level gaps through capillary action.
- Corrosion resistance matching: form a homogeneous interface with the base material to reduce the risk of electrochemical corrosion.
Forms and Availability:
Aluminum brazing wire is available in various forms to suit different brazing methods and applications. Aluminum brazing wire is mainly made of wire with a diameter of 0.8-3.0mm and also has a strip or ring shape to adapt to automated production. The surface is often coated with flux such as potassium fluoroaluminate (KAlF₄) to achieve the “self-brazing” function. According to the application scenario, it can be divided into:
- Hard brazing wire (melting point > 450℃): used for high-strength connection of structural parts.
- Soft brazing wire (melting point < 450℃): suitable for precision welding of electronic components.
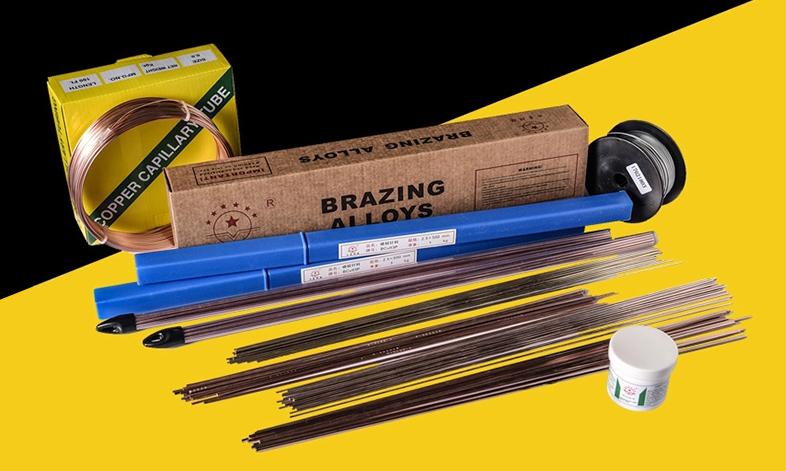
Why Aluminum Brazing Wire?
Compared with traditional fusion welding, brazing has the following advantages through the “metallurgical bonding” mechanism of non-melting parent materials:
- Low heat input: reduce grain coarsening in the heat affected zone (HAZ) and maintain the mechanical properties of the parent material.
- Complex structure compatibility: can connect dissimilar metals (such as aluminum-copper) or thin-walled components (<0.5mm).
- Process controllability: suitable for a variety of heat sources such as flame, induction, and furnace, with a yield rate of more than 95%.
- Versatility: it allows for the joining of complex shapes and dissimilar thicknesses, often with minimal distortion to the base metal. The resulting joints are typically strong, corrosion-resistant, and aesthetically pleasing.
Aluminum brazing wire is based on “precision metallurgy” and reconstructs the metal interface at a microscopic scale. It is an ideal choice for both efficiency and performance.
The Art of Flawless Joining: The Brazing Process
Achieving flawless joints with aluminum brazing wire requires precise coordination of temperature, time, and environment:
- Preparation is Key: Cleanliness is paramount. The surfaces to be joined must be free from oxides, grease, and other contaminants. Mechanical cleaning (wire brushing, sanding) and chemical cleaning (using appropriate degreasers and etchants) are commonly employed. If necessary, use fluorotitanic acid to activate the surface.
- Choosing the Right Flux: Aluminum readily forms an oxide layer that inhibits the brazing process. Fluxes are chemical agents that remove this oxide and promote wetting of the base metal by the brazing wire. Selecting the correct flux for the specific aluminum alloy and brazing method is essential.
- Brazing Techniques: Several brazing techniques can be used with aluminum wire, including torch brazing, furnace brazing, vacuum brazing, and induction brazing. The choice of technique depends on the complexity of the joint, production volume, and required quality.
- Controlling the Heat: Precise temperature control is crucial. Overheating can lead to distortion or cracking, while insufficient heat will prevent the brazing wire from flowing properly. The brazing temperature must be within the specified melting range of the chosen alloy. For flame brazing, adjust the acetylene/oxygen ratio to a neutral flame (temperature about 3100℃). Induction heating achieves rapid local heating through frequency selection (10-50kHz).
- Filler Metal Filling: Use “pre-placed welding wire” or “wire feeding machine” to ensure that the molten filler metal spreads evenly under capillary action. The filling rate needs to be >90%.
- Cooling Stage: Use gradient cooling (such as nitrogen protection cooling) to avoid cracks caused by residual stress.
Careful consideration of these factors will ensure the selected brazing wire delivers the desired performance and longevity in the final product.
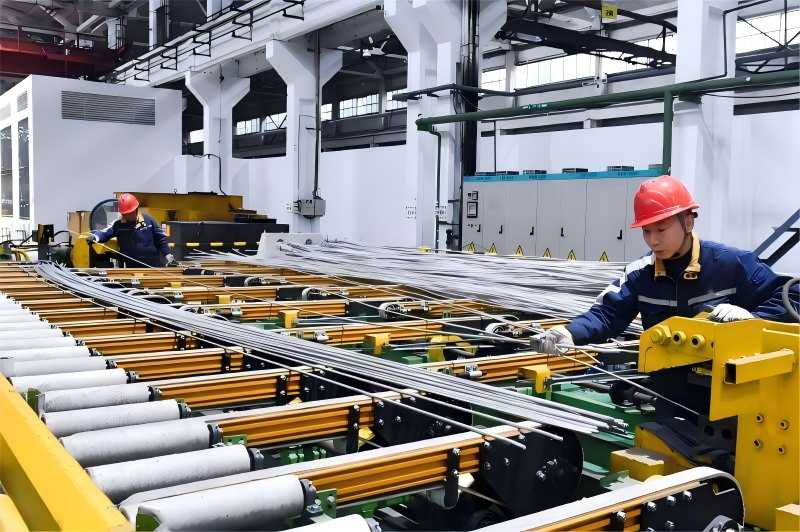
How to Choose the Right Aluminum Brazing Wire?
Choosing the right aluminum brazing wire is essential for achieving flawless joins. Here are key factors to consider:
- Alloy Compatibility: Match the brazing wire’s alloy to the base material for optimal bonding. Common alloys include 4043, 5356, and 4343, each suited for specific applications.
- Melting Point: Select a wire with a melting range lower than the base material to avoid distortion.
- Application Requirements: For automotive heat exchangers, use wire designed for thermal conductivity. For aerospace, prioritize lightweight and high-strength options.
- Environmental Conditions: Opt for corrosion-resistant wires for outdoor or high-moisture environments.
Careful selection of brazing wire tailored to your project’s needs will significantly enhance joint quality and durability. Don’t hesitate to consult aluminum brazing wire manufacturers when in doubt.
Aluminum brazing wire is more than just a filler metal; it’s a key enabler of flawless metal joining for aluminum. By understanding its properties, mastering the brazing process, and selecting the right wire for the application, manufacturers can create strong, reliable, and aesthetically pleasing joints. From the smallest electronic component to the largest structural element, aluminum brazing wire plays a vital role in realizing the full potential of this versatile material. The “secret” to flawless joining lies in the careful application of knowledge and technique, transforming aluminum brazing wire into a powerful tool for modern manufacturing.