The automotive industry is a dynamic landscape where innovation, performance, and efficiency are paramount. In recent years, aluminum die casting has emerged as a game-changer, revolutionizing the manufacturing processes within the automotive sector. This versatile and lightweight material offers a myriad of benefits, making it a preferred choice for producing components that are integral to the performance, safety, and fuel efficiency of modern vehicles.
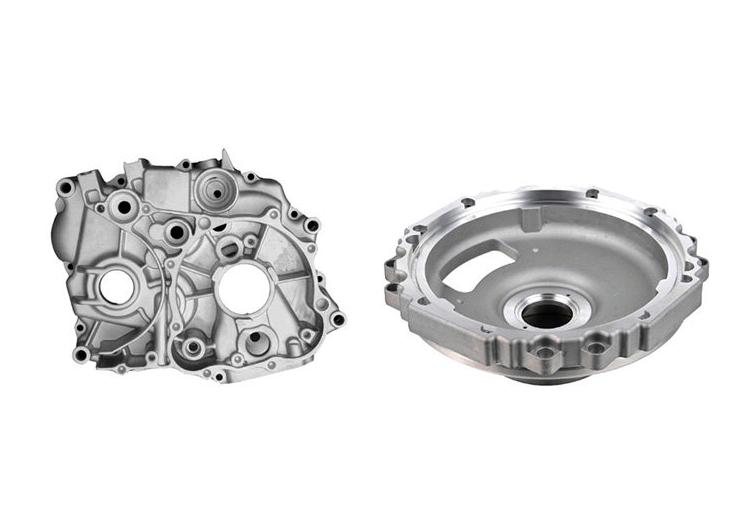
Benefits of Aluminum Die Casting for Automotive Parts
- Lightweight Advantage
One of the primary reasons aluminum die casting has gained traction in the automotive industry is its exceptional strength-to-weight ratio. Aluminum is significantly lighter than traditional materials like steel, contributing to reduced vehicle weight. Lighter vehicles, in turn, lead to improved fuel efficiency, lower emissions, and enhanced overall performance.
- Fuel Efficiency and Emissions Reduction
As global automotive standards emphasize fuel efficiency and environmental sustainability, aluminum die casting plays a pivotal role. The reduced weight of aluminum components translates to lower fuel consumption, making vehicles more eco-friendly and compliant with stringent emission regulations. This shift towards lightweight materials aligns with the industry’s commitment to sustainability and reduced carbon footprint.
- Enhanced Performance and Safety
Aluminum die casting allows for the production of intricate and complex shapes with high precision. This capability is crucial in manufacturing components that contribute to the vehicle’s performance and safety, such as engine parts, transmission housings, and structural components. The strength and durability of aluminum enhance overall vehicle safety without compromising on performance.
- Thermal Conductivity
Aluminum’s excellent thermal conductivity is a significant advantage in the automotive industry. It helps dissipate heat efficiently, contributing to the longevity and optimal performance of critical components like engine blocks and transmission parts. This thermal management capability is particularly valuable in high-performance and electric vehicles, where heat dissipation is a crucial factor.
- Design Flexibility
Aluminum die casting allows for intricate and highly detailed designs that meet the aesthetic and functional requirements of modern automotive designs. The flexibility in design enables manufacturers to create streamlined and aerodynamic components, contributing to improved vehicle aesthetics and performance.
- Sustainability and Recycling
Aluminum is highly recyclable, making it an environmentally sustainable choice for the automotive industry. The recycling process requires significantly less energy compared to primary aluminum production, further reducing the industry’s environmental impact. As sustainability becomes a focal point for both manufacturers and consumers, the use of recyclable materials is a key driver in the adoption of aluminum die casting.
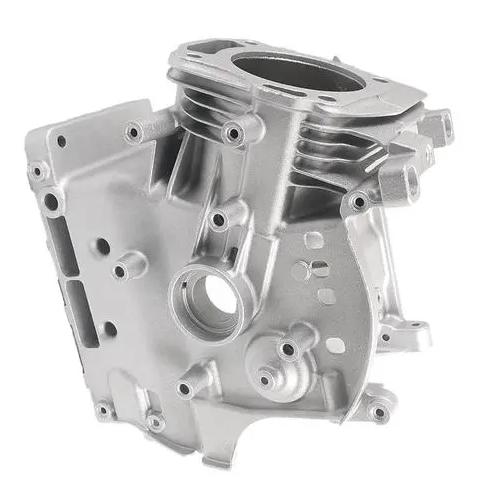
Applications of Aluminum Die Casting in the Automotive Industry
Aluminum die casting is used to create a variety of parts for the automotive industry, including:
- Engine blocks: Engine blocks are the main structural components of an engine. They are typically made of aluminum because of its lightweight and strong properties.
- Cylinder heads: Cylinder heads are the upper parts of an engine that contain the cylinders and valves. They are typically made of aluminum because of its heat-resistant properties.
- Transmission housings: Transmission housings are the enclosures that house the gears of a transmission. They are typically made of aluminum because of its strength and durability.
- Suspension components: Suspension components are the parts that connect the wheels of a vehicle to the chassis. They are typically made of aluminum because of its lightweight and strength properties.
- Wheels: Wheels are the parts that the tires are mounted on. They are typically made of aluminum because of its lightweight and strength properties.
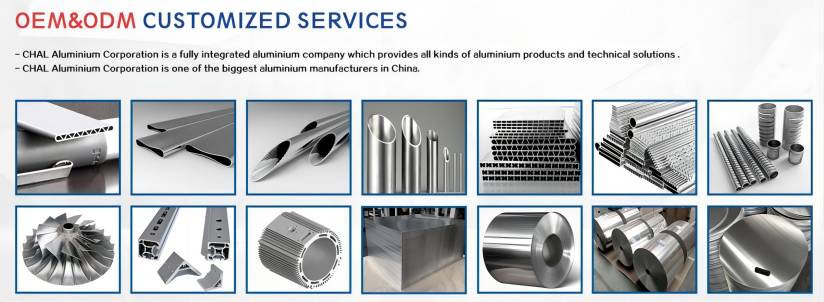
How to Choose an Aluminum Die Casting Manufacturer?
When choosing an aluminum die casting manufacturer, there are a number of factors to consider. These factors include:
- Experience: The manufacturer should have experience in die casting aluminum parts. They should also be familiar with the specific requirements of your industry.
- Equipment: The manufacturer should have the latest equipment to produce high-quality die cast parts.
- Quality control: The manufacturer should have a strong quality control program in place to ensure that all parts meet your specifications.
- Customer service: The manufacturer should have a good reputation for customer service. They should be responsive to your needs and willing to work with you to resolve any issues.
- Cost: The cost of die casting will vary depending on the complexity of the part and the volume of parts you need. Get quotes from several manufacturers to ensure you are getting the best price.
Conclusion
Aluminum die casting has emerged as a cornerstone technology in the automotive industry, reshaping the way vehicles are designed and manufactured. Its lightweight advantage, coupled with excellent strength, thermal conductivity, and recyclability, positions aluminum as a material of choice for critical components in modern vehicles. As the automotive industry continues to evolve towards sustainability and efficiency, the role of aluminum die casting is likely to expand, driving innovation and contributing to the development of the next generation of automobiles.