Aluminum extrusions have become a staple in various industries, thanks to their remarkable properties that make them an ideal choice for a wide range of applications. In this article, we’ll delve into the reasons why aluminum extrusions are widely used, exploring their strength, lightweight characteristics, corrosion resistance, ease of fabrication, and availability in diverse shapes and sizes.
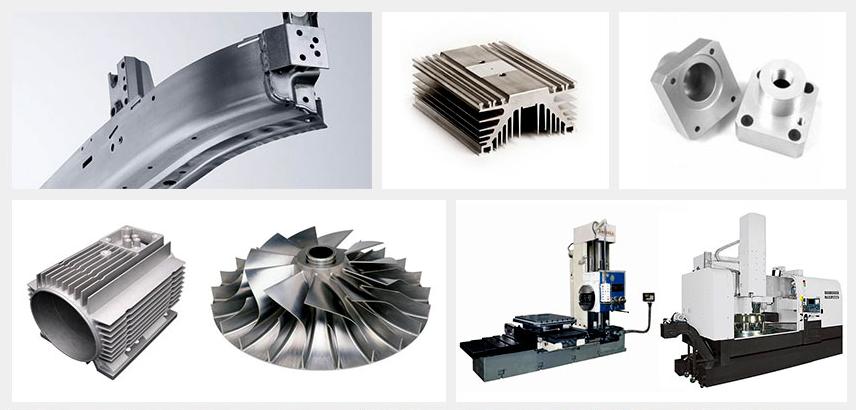
Why Use Aluminum Extrusions?
- Strength: One of the primary advantages of utilizing aluminum extrusions lies in their inherent strength and durability. This characteristic renders them highly suitable for applications that demand robust materials. The strength of an aluminum extrusion depends on factors like the alloy used and the thickness of the extrusion. Generally, extrusions are notably stronger compared to aluminum sheet metal, making them indispensable in industries that require dependable materials. Moreover, the strength of aluminum extrusions can be further enhanced through heat treatment processes. This allows for tailoring the material’s properties to meet specific requirements, offering a high degree of customization for diverse applications.
- Lightweight: The lightweight nature of aluminum extrusions is a crucial factor driving their popularity. Industries that prioritize weight reduction, such as automotive and aerospace, find aluminum extrusions to be an invaluable resource. Their low density and impressive strength-to-weight ratio make them an ideal choice, enabling significant advancements in fuel efficiency and overall performance.
- Corrosion resistance: Harsh environments pose a significant challenge to many materials, but aluminum extrusions rise to the occasion with their exceptional corrosion resistance. This property ensures longevity, making them an excellent choice for outdoor applications, marine environments, and structures exposed to corrosive elements. This resistance to corrosion extends the lifespan of products and reduces the need for frequent maintenance, resulting in cost savings over time.
- Easy to fabricate: The ease with which aluminum extrusions can be fabricated adds another layer of appeal to this versatile material. Various methods, such as machining, welding, and bending, allow for the creation of complex and intricate designs. Machining involves the use of cutting tools to shape the extrusion, while welding joins two pieces together using heat and pressure. Bending, on the other hand, imparts curvature to the material, expanding design possibilities.
- Available in a variety of shapes and sizes: Aluminum extrusions come in an extensive range of shapes and sizes, offering a level of versatility that few other materials can match. This adaptability allows for precise customization to meet the unique requirements of each project. Whether it’s a complex architectural component or a streamlined automotive part, aluminum extrusions provide the flexibility needed to turn ideas into reality.
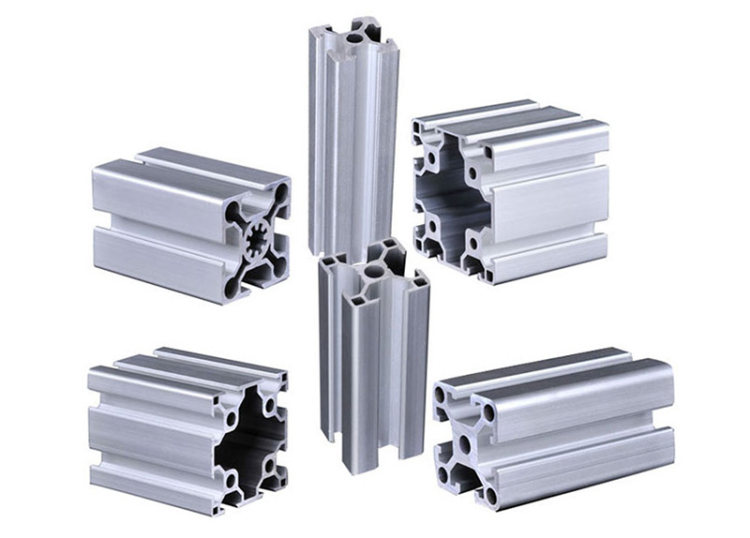
How to Fabricate Aluminum Extrusions?
Aluminum extrusions can be fabricated using a variety of methods, including:
- Machining: Machining is a process that uses cutting tools to remove material from an aluminum extrusion to create a desired shape. This is the most common method for fabricating aluminum extrusions.
- The type of machining process used will depend on the shape of the extrusion and the desired results. For example, turning is used to create cylindrical shapes, while milling is used to create flat shapes.
- Welding: Welding is a process that joins two pieces of aluminum extrusion together using heat and pressure. This method is often used to create complex shapes or to repair damaged extrusions.
- The type of welding process used will depend on the alloy of the extrusion and the desired results. For example, gas metal arc welding (GMAW) is often used for 6061 extrusions, while friction stir welding (FSW) is often used for 7075 extrusions.
- Bending: Bending is a process that curves an aluminum extrusion into a desired shape. This method is often used to create curved or angled extrusions.
- The type of bending process used will depend on the shape of the extrusion and the desired results. For example, roll bending is used to create cylindrical shapes, while press bending is used to create flat shapes.
- Forming: Forming is a process that uses pressure to deform an aluminum extrusion into a desired shape. This method is often used to create complex shapes or to produce large quantities of extrusions.
- The type of forming process used will depend on the alloy of the extrusion and the desired results. For example, hydroforming is often used to create complex shapes, while deep drawing is often used to produce large quantities of extrusions.
Applications of Aluminum Extrusions:
Aluminum extrusions are used in a wide variety of applications, including:
- Construction: Aluminum extrusions are used in a variety of construction applications, such as windows, doors, and railings. They are also used in structural applications, such as beams and columns.
- Transportation: Aluminum extrusions are used in a variety of transportation applications, such as cars, trucks, and airplanes. They are used for structural components, such as frames and chassis, as well as decorative components, such as trim and molding.
- Furniture: Aluminum extrusions are used in a variety of furniture applications, such as tables, chairs, and beds. They are used for frames, legs, and other structural components.
- Electronics: Aluminum extrusions are used in a variety of electronics applications, such as laptops, smartphones, and tablets. They are used for housings, brackets, and other structural components.
- Machinery: Aluminum extrusions are used in a variety of machinery applications, such as CNC machines, robots, and printers. They are used for frames, components, and other structural parts.
- Medical devices: Aluminum extrusions are used in a variety of medical devices, such as wheelchairs, walkers, and surgical instruments. They are used for frames, components, and other structural parts.
- Sports and recreation: Aluminum extrusions are used in a variety of sports and recreation applications, such as bicycles, skis, and snowboards. They are used for frames, components, and other structural parts.
- Other industries: Aluminum extrusions are used in a variety of other industries, such as aerospace, defense, and packaging.
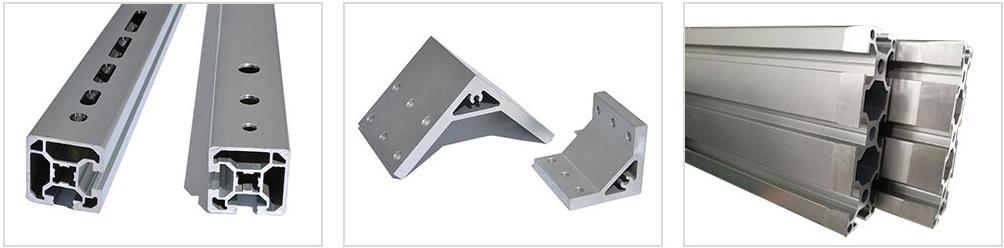
Conclusion
In conclusion, aluminum extrusions have cemented their place as a preferred material choice in numerous industries due to their exceptional properties. Their strength, lightweight nature, corrosion resistance, ease of fabrication, and availability in various shapes and sizes make them a versatile solution for a wide array of applications.
Whether it’s creating robust structural components, reducing weight in aerospace designs, or withstanding harsh environmental conditions, aluminum extrusions continue to play a pivotal role in shaping the modern world. As technology and engineering practices evolve, aluminum extrusions are likely to remain a vital resource for innovators seeking efficient, durable, and adaptable solutions to their manufacturing challenges.