Aluminum fibers are a type of lightweight, high-strength material that have garnered attention in various industries due to their unique properties. In this article, we will delve into the properties, production methods, and applications of aluminum fibers.
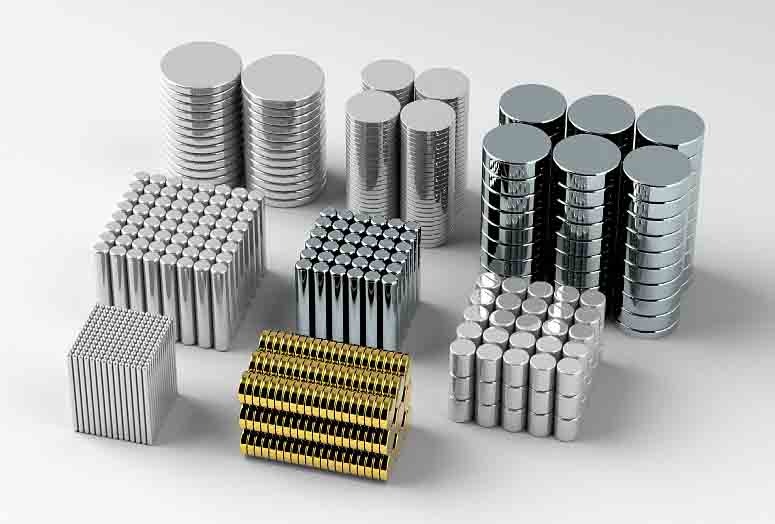
Properties of Aluminum Fibers
High Strength-to-Weight Ratio:
Aluminum fibers are known for possessing several desirable properties. First and foremost, they exhibit a high strength-to-weight ratio, meaning they are strong yet lightweight. This property exceeds that of many other materials, making them ideal for use in various applications that require high strength and low weight.
Excellent Electrical Conductivity:
Additionally, aluminum fibers have excellent electrical conductivity, which makes them useful in the production of electrical components.
Good Thermal Conductivity:
They also have good thermal conductivity, allowing them to be used in applications where heat transfer is important.
Corrosion Resistance:
Finally, aluminum fibers are resistant to corrosion, which makes them ideal for use in harsh environments where other materials may degrade over time.
Production of Aluminum Fibers
There are several methods for producing aluminum fibers, including:
Melt Extraction:
Aluminum fibers are typically produced using a process called melt extraction. In this process, pure aluminum or an aluminum alloy is first melted and then injected through a small orifice or nozzle at high velocity using inert gas or compressed air. As the molten aluminum exits the nozzle, it is rapidly cooled and solidified by contact with a spinning cylinder or drum that is cooled by water or air.
As the solidified aluminum ribbon or filament is pulled from the spinning drum, it is stretched and attenuated to reduce its diameter and increase its length. This stretching and attenuating process aligns the aluminum atoms and creates a high-strength fiber with excellent electrical conductivity. The final product may be either a continuous fiber or a staple fiber, depending on the application.
After the initial production step, the aluminum fibers may be further processed by drawing, twisting, or weaving to create different types of products, such as wire, yarn, cloth, or tape. The resulting products may be used in a wide range of applications, including aerospace, electronics, automotive, and construction industries.
Vapor Deposition:
Vapor deposition is a crucial step in the manufacturing process of aluminum fibers. It involves the deposition of aluminum onto a carbon or ceramic core through a chemical vapor deposition (CVD) process.
Firstly, the carbon or ceramic core is prepared and loaded into a reactor chamber. The chamber is then heated to a high temperature, typically between 800 and 1200°C, under a vacuum or a controlled atmosphere of inert gas. This step is crucial to ensure that the core material is clean and free of any contaminants that could affect the quality of the final product.
Next, a precursor gas, such as trimethylaluminum (TMA), is introduced into the reactor chamber. TMA is broken down by thermal decomposition, resulting in the deposition of aluminum atoms onto the core material. The aluminum atoms react with the surface of the core material, forming a thin layer of aluminum coating.
This process is repeated multiple times, with the thickness of the aluminum layer increasing after each cycle. The number of cycles and the deposition conditions, such as the temperature and pressure, can be adjusted to control the thickness and quality of the aluminum coating.
Finally, the coated core material is removed from the reactor chamber and undergoes post-treatment processes, such as heat treatment, to improve the mechanical properties and stability of the aluminum fibers.
Overall, vapor deposition plays a critical role in the production of high-quality aluminum fibers, allowing for precise control over the thickness and quality of the aluminum coating.
Electrospinning:
Electrospinning is a widely used method for the production of aluminum fibers. In this process, a polymer solution containing aluminum precursors is loaded into a syringe equipped with a metallic needle. The needle is connected to a high voltage power supply, which creates an electric field between the needle and a grounded collector. When the voltage is high enough, a jet of the polymer solution is ejected from the needle and stretches into a thin fiber under the influence of the electric field.
During the stretching process, the aluminum precursors are chemically converted into aluminum oxide, forming a ceramic shell around the polymer fiber. The ceramic shell helps to maintain the fiber’s structure and prevents it from breaking during subsequent processing steps. The resulting fibers are then collected on the grounded collector, where they can be further processed and heated to convert the aluminum oxide shell back into metallic aluminum.
One advantage of electrospinning is that it allows for the precise control of the fiber diameter and structure. By adjusting the processing parameters such as the voltage, flow rate, and distance between the needle and collector, the diameter of the resulting fibers can be tuned from tens of nanometers to several micrometers. The fibers can also be produced in various structures such as nanofibers, microfibers, and composite fibers, depending on the composition of the polymer solution and the processing conditions.
Overall, electrospinning is a versatile and effective method for producing aluminum fibers with excellent properties such as high strength, high thermal and electrical conductivity, and low density.
Applications of Aluminum Fibers

Aluminum fibers have a wide range of applications due to their unique properties.
Aerospace:
In aerospace, aluminum fibers are used in the production of components such as aircraft frames and panels, where their high strength-to-weight ratio and corrosion resistance are particularly useful.
Electrical and Electronics:
In electrical and electronics, aluminum fibers are used in the production of components such as wiring and printed circuit boards, where their excellent electrical conductivity is a key feature.
Heat Transfer:
In heat transfer, aluminum fibers are used in applications such as heat exchangers and thermal insulation, where their good thermal conductivity is important.
Medical:
Finally, aluminum fibers are also used in medical applications such as wound dressings and drug delivery systems.
Others:
In addition to the applications mentioned above, aluminum fibers have found use in other fields as well. For example, they are used in the production of sports equipment such as tennis rackets, where their high strength-to-weight ratio is a critical feature. They are also used in the automotive industry, where their corrosion resistance and thermal conductivity make them suitable for use in engine components.
Conclusion
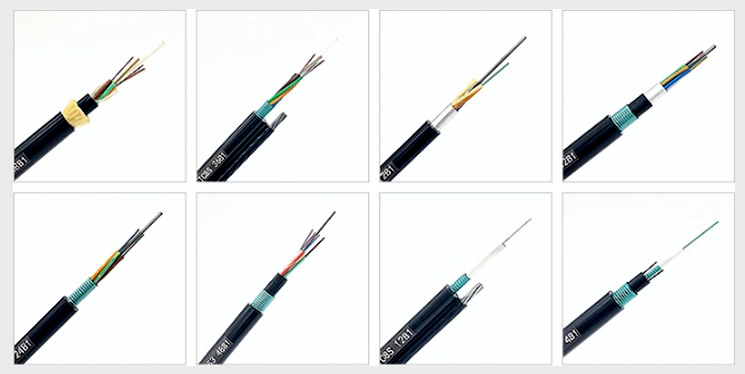
Aluminum fibers are a versatile material that possess a range of desirable properties, making them useful in various applications. With a variety of production methods available, aluminum fibers are used in aerospace, electrical and electronics, heat transfer, and medical industries. As technology advances, it is likely that new and innovative applications of aluminum fibers will continue to emerge, making them an exciting area of research and development.
Overall, aluminum fibers have become an increasingly important material due to their unique properties and diverse range of applications. With ongoing research and development, it is likely that they will continue to find use in new and innovative ways, further solidifying their position as a valuable material in various industries.