Aluminum heat sinks are pivotal in thermal management across various industries, from consumer electronics to high-performance machinery. The primary function of a heat sink is to dissipate heat generated by electronic components, machinery, or other devices, thus preventing overheating and ensuring optimal performance. The demand for efficient heat dissipation solutions has led to significant innovations in both material choices and manufacturing techniques. This article explores the various types of aluminum alloys used in heat sinks and examines the common manufacturing processes involved in producing efficient and cost-effective aluminum heat sinks.
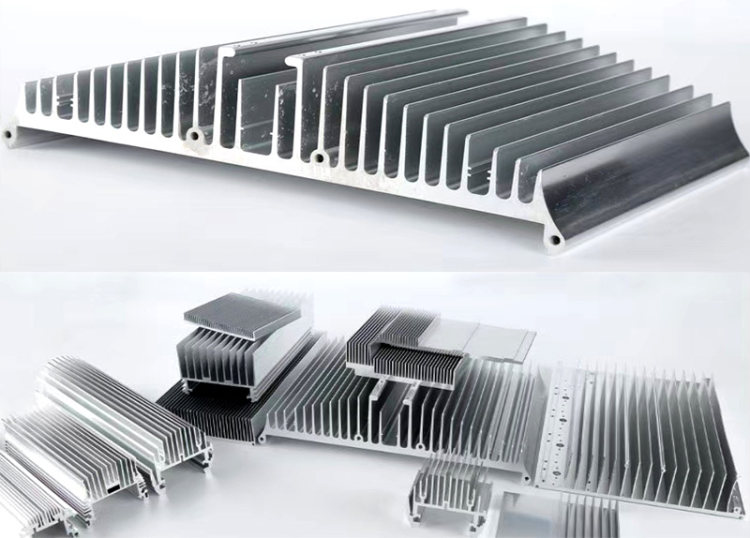
Aluminum Heat Sink Materials
The choice of aluminum alloy for a heat sink is crucial for determining its heat dissipation performance, mechanical strength, and cost efficiency. Here are the most commonly used alloys for aluminum heat sinks in the following table:
Aluminum Alloy | Description | Key Features | Applications |
3003 Aluminum Alloy | A popular aluminum-manganese alloy known for corrosion resistance and workability. Low-cost and easy to produce. | Good corrosion resistance 2. High ductility 3. Easily formable | General-purpose heat sinks 2. Household appliances 3. Small-scale electronics |
6061 Aluminum Alloy | A versatile alloy with magnesium and silicon, offering strength, machinability, and corrosion resistance. Ideal for demanding environments. | Excellent corrosion resistance 2. High strength-to-weight ratio 3. Good weldability | Industrial equipment heat sinks 2. Medium to high-performance heat sinks in telecommunications 3. Automotive industries |
6063 Aluminum Alloy | A specialized aluminum alloy known for its surface finish and extrudability, making it great for complex, heat-dissipating shapes. | Superior surface finish 2. Good corrosion resistance 3. Easy to extrude into complex profiles | Heat sinks for consumer electronics (laptops, desktops) 2. Aesthetic applications requiring good appearance and functionality |
6082 Aluminum Alloy | Known for its high tensile strength and durability, suitable for heat sinks requiring mechanical stress endurance. | High tensile strength 2. Good corrosion resistance 3. High durability | Heavy-duty heat sinks for industrial machinery 2. Large-scale air conditioning systems 3. Structural load-bearing and heat dissipation |
7075 Aluminum Alloy | A high-strength aluminum alloy with zinc as the main alloying element, delivering superior mechanical properties. Common in aerospace applications. | Exceptional strength 2. Lightweight 3. High fatigue resistance | High-performance heat sinks in aviation 2. Military equipment 3. Less common in consumer electronics due to higher cost |
ADC12 Aluminum Alloy | A die-casting alloy known for its excellent castability, thermal conductivity, and ability to form complex shapes. | High castability 2. Good thermal conductivity 3. Excellent vibration dampening | Automotive heat sinks 2. Electrical housings 3. High-volume manufacturing for complex shapes |
Common Manufacturing Processes for Aluminum Heat Sinks
The manufacturing process used to produce an aluminum heat sink can significantly affect its thermal performance, structural integrity, and cost. Below are some of the most common manufacturing techniques used in the industry:
1. Extrusion Process
The extrusion process is one of the most widely used methods for manufacturing aluminum heat sinks. In this process, aluminum billets are forced through a die to create long sections with specific cross-sectional profiles. These profiles can then be cut into desired lengths to form heat sinks.
Advantages:
- Cost-effective for large-volume production
- Excellent dimensional accuracy and surface finish
- Suitable for creating simple and medium-complexity heat sink designs
Limitations:
The extrusion process has some limitations in terms of aspect ratio (height-to-thickness) of the fins, meaning that extremely thin fins or very tall fin structures are difficult to achieve.
Applications:
Extruded heat sinks are ideal for medium-performance applications such as computer processors, LED lighting systems, and power converters.
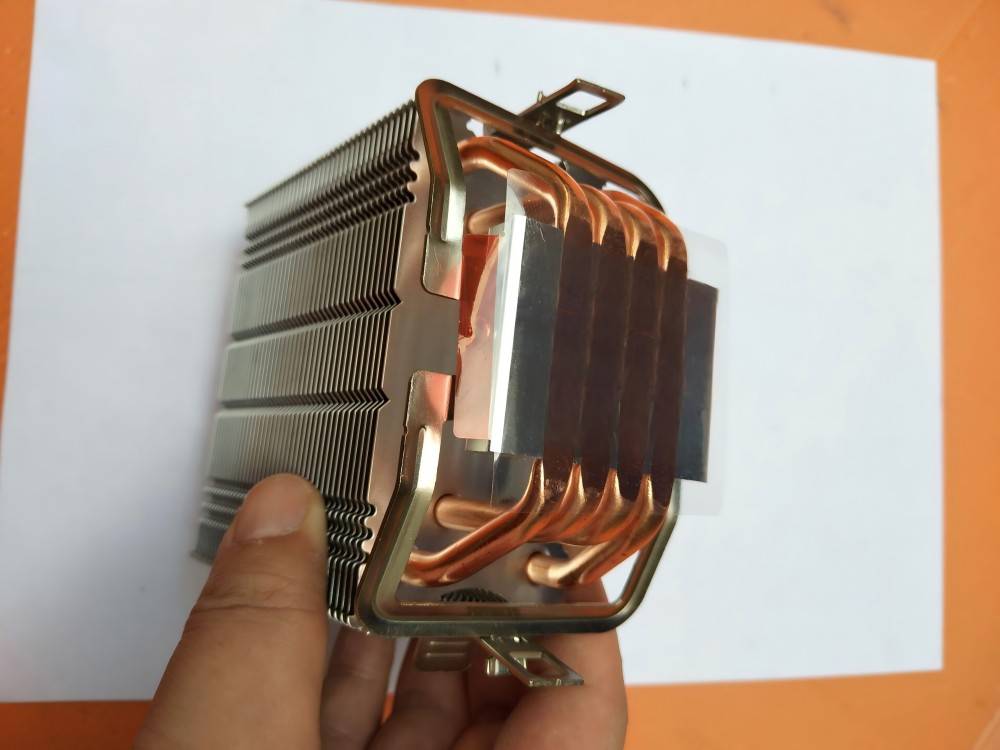
2. Die Casting Process
Die casting is a process in which molten aluminum is injected into a steel mold under high pressure. The mold defines the shape of the heat sink, allowing for the creation of complex geometries that are difficult to achieve through extrusion or other methods.
Advantages:
- Ideal for creating complex, thin-walled designs
- Suitable for mass production of intricate shapes
- Can integrate multiple components into a single casting
Limitations:
Die casting may negatively affect the thermal conductivity of the aluminum due to the introduction of internal porosity. Moreover, the high tooling costs make it less suitable for low-volume production.
Applications:
Die-cast heat sinks are often used in automotive applications, as well as in advanced telecommunications equipment where space constraints require compact and intricate heat sink designs.
3. Forging Process
Forging involves applying mechanical pressure to shape aluminum billets into the desired form. This process can create heat sinks with very high fin density and excellent structural integrity.
Advantages:
- High fin density for maximum surface area
- Excellent mechanical strength and durability
- Suitable for producing high-performance heat sinks with thin and tall fins
Limitations:
Forging is typically more expensive than extrusion or die casting due to the high cost of tooling and slower production speeds. It is also less suitable for creating complex shapes.
Applications:
Forged heat sinks are used in high-end applications such as aerospace electronics, military systems, and premium-grade consumer electronics where performance is critical.
4. Stamping Process
Stamping involves cutting and forming aluminum sheets into fins, which are then assembled into a heat sink, often in conjunction with heat pipes to enhance thermal performance.
Advantages:
- High production speed and cost-efficiency for mass production
- Flexibility in creating various fin shapes and configurations
Limitations:
Stamped heat sinks may not have the same thermal efficiency as forged or extruded heat sinks due to the limitations of thin aluminum sheets and the assembly process.
Applications:
This process is often used for applications that require lightweight and compact heat sinks, such as in small consumer electronics or power modules.
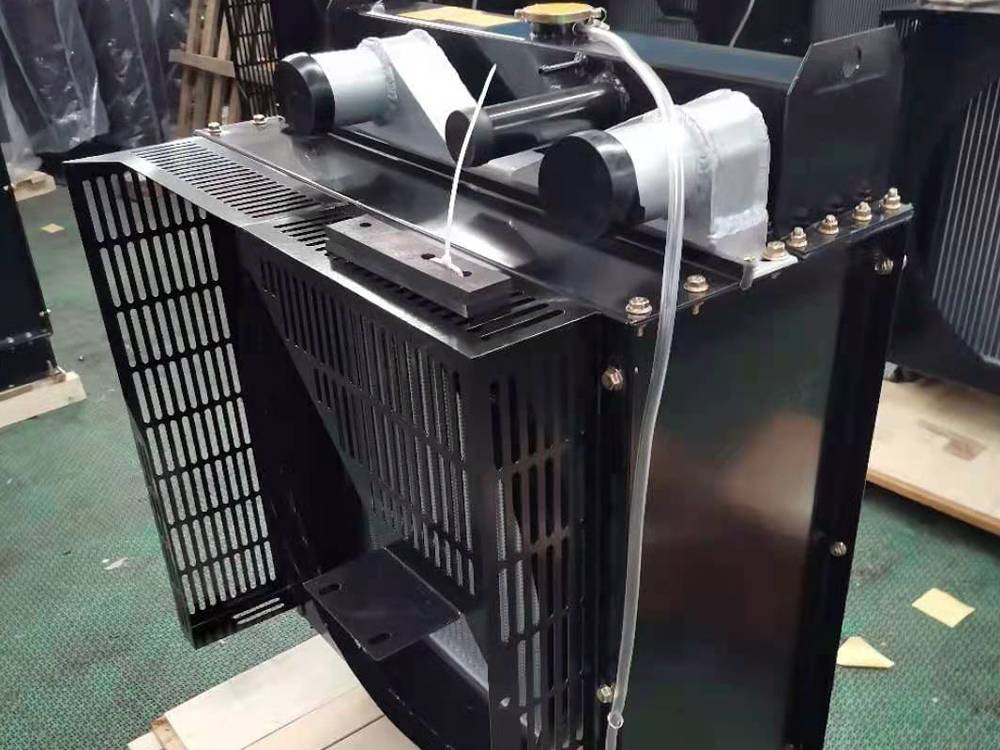
5. Skiving Process
Skiving is a specialized process in which thin slices of aluminum are peeled off from a solid block, and the peeled material is bent upward to form fins. This process is advantageous for creating heat sinks with extremely high fin density.
Advantages:
- High fin density and surface area
- Good thermal performance
- Lightweight designs
Limitations:
Skiving is more expensive than other methods and is generally limited to smaller or medium-sized heat sinks due to the constraints of the cutting process.
Applications:
Skived heat sinks are used in applications requiring maximum thermal efficiency with minimal weight, such as in high-end electronics and portable computing devices.
6. Welding Process
Welding is a process that involves joining multiple components to form a unified heat sink. The welding process may involve traditional welding techniques or more advanced methods like diffusion bonding, which ensures seamless integration of different parts.
Advantages:
- Allows for complex, multi-part designs
- Can integrate different materials for hybrid heat sinks
- Suitable for large and high-performance heat sinks
Limitations:
Welding can introduce thermal resistance at the joint if not done carefully. Additionally, it is a labor-intensive process that may increase production costs.
Applications:
Welded heat sinks are commonly used in high-performance applications such as servers, telecom equipment, and power electronics, where large or intricate heat sink structures are required.
Factors Impact on Selecting the Right Manufacturing Process
Choosing the appropriate manufacturing process for aluminum heat sinks depends on several factors:
- Design Requirements: The complexity of the heat sink’s shape, size, and performance needs will dictate which process is most suitable. For simple designs, extrusion may suffice, while die-casting or skiving is better for more intricate shapes.
- Thermal Performance: If maximizing thermal performance is the goal, forging or skiving will offer better heat dissipation compared to die-casting or stamping.
- Cost Considerations: For high-volume, low-cost applications, extrusion or stamping processes may be more appropriate, while forging and die-casting are typically more expensive due to higher tooling and material costs.
- Material Characteristics: Different aluminum alloys perform better under certain conditions, so the choice of material will also influence the selection of the manufacturing process.
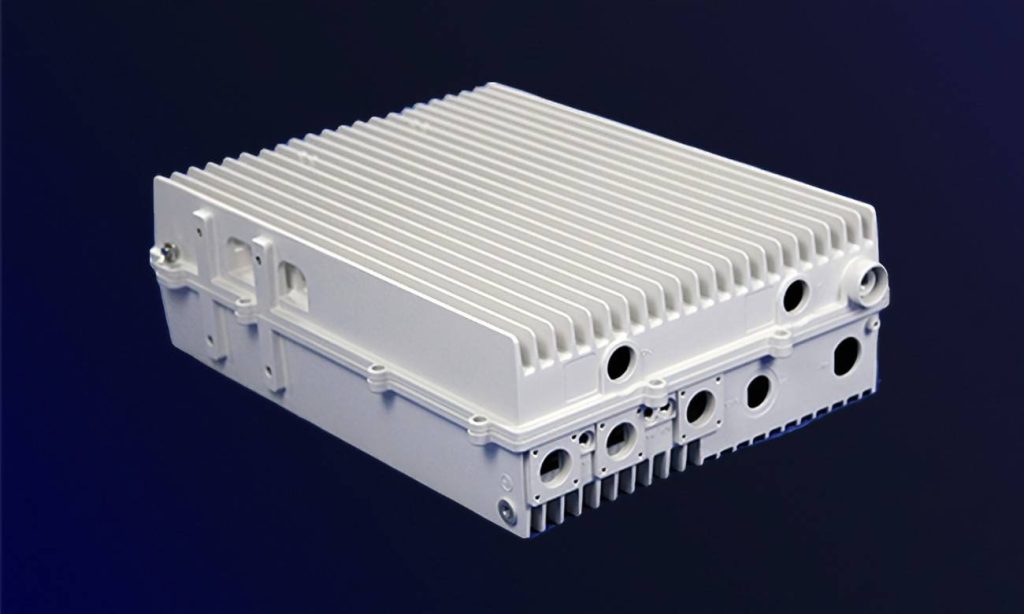
In conclusion, aluminum heat sinks are crucial for effective thermal management in various industries. The choice of aluminum alloy and manufacturing process directly affects the heat sink’s performance, cost, and design flexibility. Understanding the properties of different alloys and the strengths of each production method enables manufacturers to create optimized solutions for specific applications. With their balance of cost-efficiency and thermal performance, aluminum heat sinks remain essential for ensuring the longevity and reliability of electronic and mechanical systems.