Aluminum high-frequency welded tubes (HFW pipes) are a crucial component in various industries due to their lightweight yet robust characteristics. However, ensuring the quality of the weld joint formed during the high-frequency welding process is critical for the overall performance and reliability of the tube. This article delves into the intricacies of aluminum HFW pipe welding quality assurance, exploring the factors that influence weld quality and the strategies employed to guarantee a flawless final product.

Understanding Welding Quality Assurance
Welding quality assurance refers to a comprehensive set of practices and procedures implemented to guarantee that the welded joint in an aluminum HFW pipe fulfills the predefined quality standards. This encompasses meticulous control and optimization of various factors throughout the welding process. Maintaining consistent weld quality is paramount for several reasons:
- Structural Integrity: A high-quality weld joint ensures the HFW tube can withstand the intended loads and stresses without failure, thereby safeguarding the structural integrity of the final application.
- Leak Prevention: In applications involving fluids or gases, a flawless weld joint prevents leakage, maintaining system functionality and safety.
- Performance Optimization: A well-assured weld joint optimizes the overall performance of the HFW tube by minimizing potential weaknesses that could compromise its strength, ductility, and fatigue resistance.
What Factors Affect the Welding Quality?
Several key parameters significantly influence the quality of the weld joint in aluminum HFW tubes. A thorough understanding of these factors is essential for achieving optimal welding results.
1. Welding Process and Equipment
- Significance: The chosen welding process and the associated equipment play a pivotal role in determining the quality of the weld joint. Modern welding equipment offers distinct advantages compared to traditional methods:
- Stable Welding Current: Modern high-frequency welding power sources deliver a more consistent and stable welding current. This minimizes fluctuations in heat input, leading to a more uniform and predictable weld zone with fewer defects.
- Reduced Welding Defects: Consistent current control helps to reduce the formation of welding defects such as pores and cracks, which can compromise the integrity of the joint.
- Efficient Welding Speed: Advanced equipment allows for precise control of the welding speed. This enables the optimization of heat input into the material, minimizing the heat-affected zone (HAZ) around the weld. A narrower HAZ translates to less distortion and residual stress in the weld joint, ultimately enhancing its strength and toughness.
- Examples of Modern Welding Equipment: Solid-state high-frequency welding power sources are a prime example of modern equipment that offers the aforementioned benefits.
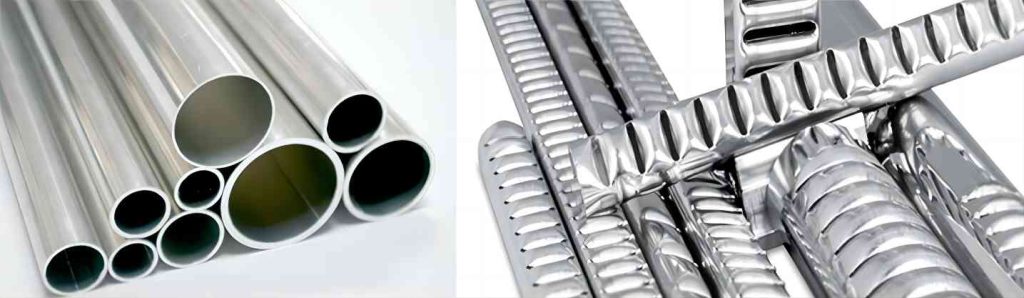
2. Material Selection
- Influence of Material Properties: The thermal properties of the aluminum material used for the HFW pipe significantly impact the welding process and the quality of the resulting joint. Two key material properties to consider are:
- Thermal Conductivity: Aluminum possesses a high thermal conductivity, meaning heat readily distributes throughout the material during welding. Selecting an aluminum alloy with a slightly lower thermal conductivity can help to concentrate the heat input in the weld zone, facilitating a more controlled and efficient welding process.
- Melting Point: The melting point of the aluminum alloy influences the welding temperature required. Choosing an alloy with a suitable melting point ensures sufficient heat input to create a proper weld pool without exceeding the melting point and causing material burn-through.
- Characteristics of Suitable Aluminum Materials: Aluminum alloys specifically formulated for good weldability are ideal choices for HFW pipes. These alloys typically possess:
- Balanced Alloying Elements: The alloying elements present in the aluminum material significantly influence its welding behavior. Alloys with a balanced composition that minimizes the formation of brittle intermetallic phases at the weld interface are preferred.
- Reduced Oxidation: Certain alloying elements can help to minimize oxidation during the welding process. This is crucial for maintaining a clean weld zone and preventing the formation of oxide inclusions that weaken the joint.
- Examples of Suitable Aluminum Alloys: Common aluminum alloys well-suited for HFW pipe welding include 6061, 3003, and 5052. These alloys offer a good balance of strength, weldability, and corrosion resistance.
3. Welding Speed
- Impact on Cooling Rate: The welding speed directly affects the cooling rate of the weld joint. This, in turn, influences the microstructure and mechanical properties of the weld zone.
- Importance of Appropriate Speed: An appropriate welding speed ensures a relatively uniform cooling rate across the weld joint. This helps to prevent the formation of a coarse-grained microstructure within the HAZ, which can negatively impact the joint’s strength and ductility.
- Benefits of Controlled Speed: Maintaining a controlled welding speed offers several advantages:
- Improved Weld Joint Strength: A slower, more controlled cooling rate allows for the formation of a finer-grained microstructure in the weld zone, leading to enhanced strength and load-bearing capacity.
- Enhanced Weld Joint Ductility: A slower cooling rate also promotes the precipitation of strengthening precipitates within the weld zone. These precipitates contribute to the joint’s overall ductility, making it more resistant to crack initiation and propagation under stress.
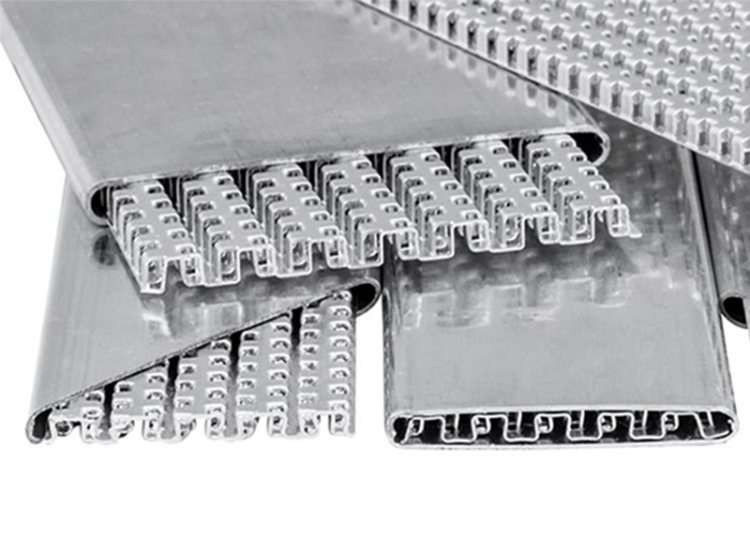
4. Heat Treatment
- Purpose: Heat treatment is a post-welding process employed to modify the microstructure and mechanical properties of the weld joint and the HAZ. This process aims to optimize the overall performance of the welded HFW pipe.
- Types of Heat Treatment: Two common types of heat treatment used for aluminum HFW tubes include:
- Stress Relief Annealing: This process involves heating the weldment to a specific temperature for a predetermined time, followed by slow cooling. This treatment helps to relieve residual stresses introduced during the welding process, thereby reducing the risk of stress corrosion cracking and improving the overall dimensional stability of the HFW pipe.
- Normalizing: This heat treatment involves heating the weldment to a temperature above the recrystallization temperature of the aluminum alloy, followed by air cooling. This process refines the grain structure within the weld zone and HAZ, leading to enhanced strength and toughness.
- Benefits of Heat Treatment: Implementing appropriate heat treatment after welding offers several benefits:
- Improved Microstructure: Heat treatment refines the grain structure within the weld zone and HAZ, leading to a more uniform and predictable mechanical performance.
- Enhanced Overall Performance: Heat treatment optimizes the overall performance of the HFW pipe by improving its strength, ductility, and resistance to cracking.
Quality Control Measures
Ensuring the quality of the weld joint in aluminum HFW tubes necessitates the implementation of rigorous quality control procedures. These procedures involve non-destructive testing (NDT) methods to evaluate the integrity of the weld without damaging the tube itself.
Importance of Inspection: Rigorous quality control measures are essential for several reasons:
- Early Detection of Defects: NDT methods enable the timely detection of potential welding defects such as cracks, pores, and incomplete fusion. This allows for corrective actions to be taken before the defects compromise the performance of the HFW pipe in the final application.
- Verification of Weld Quality: NDT methods provide a means to verify that the weld joint meets the predefined quality standards. This ensures consistency in the production of high-quality HFW tubes.
Common NDT Methods: Two prevalent NDT methods employed for inspecting aluminum HFW tube welds include:
- Radiographic Testing (X-ray): This method utilizes X-rays to penetrate the weld joint and create an image on a film or digital detector. Internal defects within the weld zone appear as anomalies on the image, allowing for their identification and evaluation.
- Metallographic Analysis: This method involves preparing a cross-section of the weld joint and subjecting it to microscopic examination. This analysis allows for a detailed evaluation of the weld microstructure, revealing any potential irregularities or imperfections.
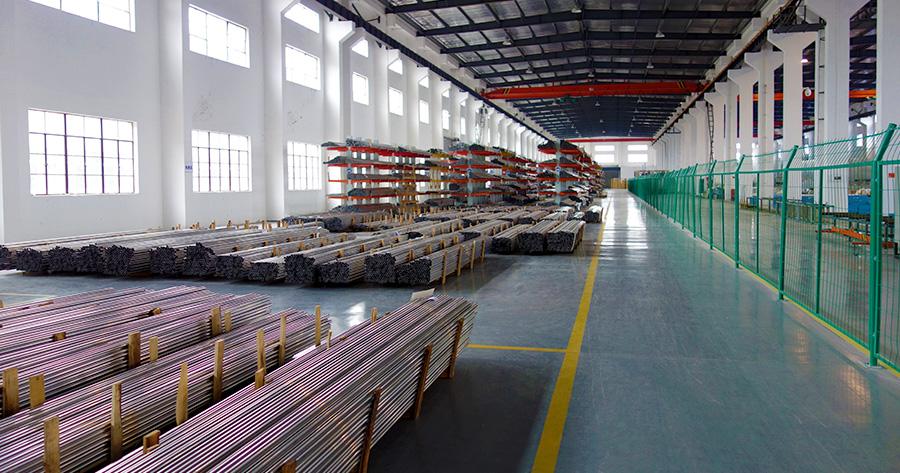
Treatment of Welding Defects
Despite implementing stringent quality control measures, the possibility of encountering welding defects during the HFW process cannot be entirely eliminated. Fortunately, various corrective actions can be taken to address these defects and ensure the integrity of the HFW pipe.
Common Defects: Two common types of welding defects encountered in aluminum HFW tubes include:
- Pores: These are gas cavities trapped within the weld metal. Pores can arise due to factors such as improper cleaning of the weld surfaces before welding or insufficient shielding gas during the process.
- Cracks: These are linear separations within the weld metal or HAZ. Cracks can be caused by excessive welding stresses, improper heat input, or the presence of unfavorable alloying elements.
Treatment Measures: Depending on the severity and type of defect identified, various corrective actions can be implemented:
- Rewelding: In some cases, the affected area of the weld joint can be re-welded to eliminate the defect. This approach requires careful grinding or machining of the defective zone to ensure proper penetration and fusion during the re-welding process.
- Local Heat Treatment: Localized heat treatment techniques can be applied to specific areas of the weld joint to address certain defects. For instance, stress relief annealing can be used to alleviate residual stresses that may contribute to crack formation.
Objectives of Defect Treatment: The primary goals of treating welding defects are:
- Maintaining Weld Joint Quality: By addressing identified defects, the overall quality and integrity of the weld joint are maintained. This ensures the HFW pipe meets the required performance specifications for its intended application.
- Ensuring Tube Integrity: Eliminating defects helps to safeguard the structural integrity of the HFW pipe. This minimizes the risk of failure under load, thereby enhancing the reliability and safety of the final product.
In conclusion, achieving optimal welding quality assurance for aluminum HFW tubes hinges on a comprehensive approach. This approach encompasses a deep understanding of the influencing factors, meticulous process control, rigorous quality control procedures, and the ability to address any arising defects. By adhering to these principles, manufacturers can guarantee the production of reliable and high-performing aluminum HFW tubes that meet the demands of diverse industrial applications. Furthermore, continuous advancements in welding technology and ongoing research on optimizing aluminum alloys for HFW applications hold promise for further enhancing the quality and performance of these essential components.