Aluminum machining parts are widely used across many industries, from aerospace to automotive and electronics. They offer excellent strength-to-weight ratios, corrosion resistance, and thermal conductivity, making them ideal for a range of applications. In this article, we’ll share tips for aluminum machining, discuss applications of aluminum parts, and analyze current trends in the industry.
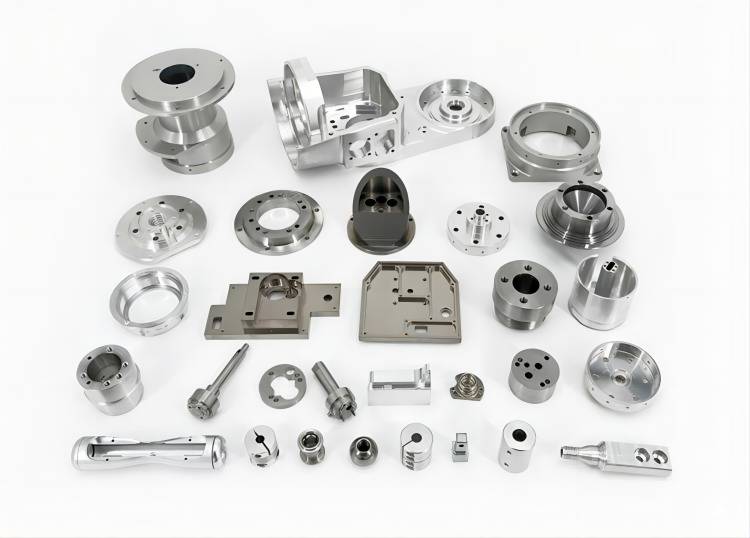
Tips for Aluminum Machining Parts
Machining aluminum can be challenging, but there are several tips that can help achieve accurate and efficient results. First, choose the right tooling. Carbide inserts are the most commonly used tooling for machining aluminum because they can handle the heat and abrasion associated with the process. High-speed steel (HSS) drills are also commonly used, as they create precise holes without damaging the material. When choosing the right cutting speeds and feeds, it’s essential to balance accuracy and efficiency. High cutting speeds and feeds can cause excessive heat, while low speeds and feeds can cause tool wear and poor surface finishes. The recommended cutting speed and feed rate vary depending on the specific material and tooling used. It’s also crucial to use proper coolant to prevent chip buildup and to deburr parts to ensure clean edges. Finally, using sharp tools is crucial to achieving accurate and efficient cuts. Dull tools cause poor surface finishes, which can lead to part failure.
Applications of Aluminum Machining Parts
Aluminum machining parts have a wide range of applications across various industries. In aerospace, aluminum parts are commonly used for structural components such as wing spars, fuselage frames, and landing gear. Aluminum alloys are also used for engine components, such as fan blades, compressor blades, and turbine disks, due to their high strength and low weight. In the automotive industry, aluminum is widely used for engine blocks, cylinder heads, and suspension and steering components. The use of aluminum in automotive parts can significantly reduce weight, which improves fuel efficiency and performance. In the electronics industry, aluminum is commonly used for circuit boards and heat sinks, thanks to its excellent electrical conductivity and thermal properties.
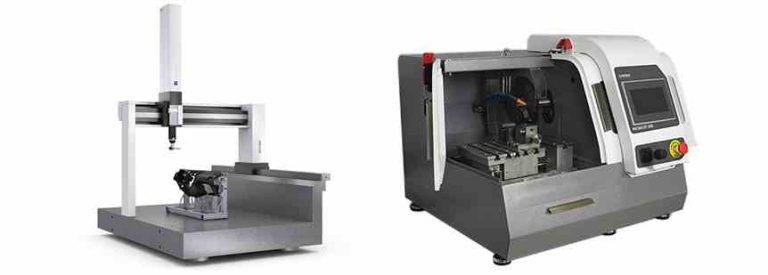
Trends in Aluminum Machining
The aluminum machining industry is constantly evolving, with new technologies, emerging markets, and changing customer demands shaping the landscape. One key trend is the growing demand for lightweight materials in the automotive and aerospace industries. As fuel efficiency and emissions standards become more stringent, manufacturers are turning to lightweight materials like aluminum to help meet these requirements. Another trend is the increasing use of automation and CNC machining. Automated systems can improve efficiency, reduce errors, and optimize production runs. Additionally, sustainability is becoming a key consideration for many businesses. Eco-friendly aluminum alloys and manufacturing processes are being developed to minimize environmental impact. Other emerging trends in the industry include the use of additive manufacturing and the development of new surface treatment technologies to improve the wear resistance and durability of aluminum parts.
Choosing the Right Aluminum Alloy for Your Application
Choosing the right aluminum alloy is critical to ensuring that your parts meet the required specifications and perform well in their intended application. There are many different aluminum alloys available, each with its own unique set of properties and characteristics. Some common aluminum alloys used for machining include 6061, 7075, and 2024.
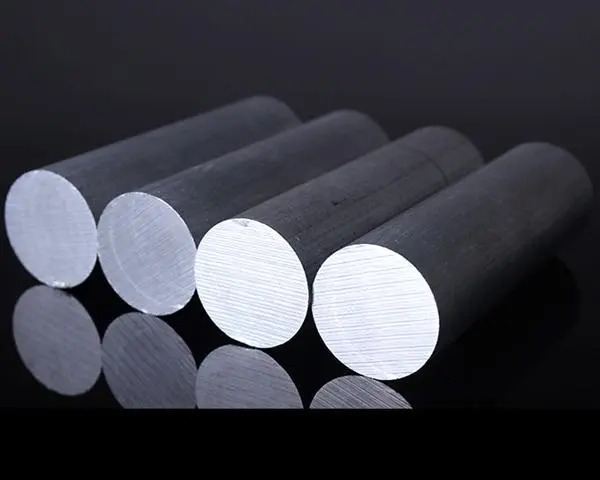
- 6061 is a widely used alloy that offers excellent corrosion resistance and good weldability. It’s commonly used for structural components, such as frames, chassis, and railings.
- 7075 is a high-strength alloy that offers excellent fatigue strength and resistance to stress corrosion cracking. It’s commonly used for aerospace applications, such as aircraft wing structures and fuselage frames.
- 2024 is a high-strength alloy that offers excellent fatigue resistance and good machinability. It’s commonly used for aircraft structural components, such as wing and fuselage skins.
When selecting an aluminum alloy, it’s essential to consider factors such as strength, weight, corrosion resistance, and machinability. The specific properties required will vary depending on the application and the operating conditions. Working with a knowledgeable supplier can help ensure that you select the right alloy for your needs.
Conclusion
Choosing the right aluminum alloy, along with proper tooling and machining techniques, can help businesses achieve accurate and efficient results when machining aluminum parts. By understanding the different applications of aluminum parts, businesses can identify new opportunities for growth. And by staying up-to-date on industry trends and innovations, businesses can remain competitive and meet the evolving needs of their customers. If you’re interested in learning more about aluminum machining parts or need help selecting the right aluminum alloy for your application, connect with us today.