The relentless pursuit of efficiency in thermal management has led to the development of innovative solutions. Among these advancements, aluminum microchannel tubes stand out for their exceptional heat transfer capabilities and lightweight design. This article delves into the world of aluminum microchannel tubes, exploring their structural features, diverse applications, and the difficulties encountered in their production.
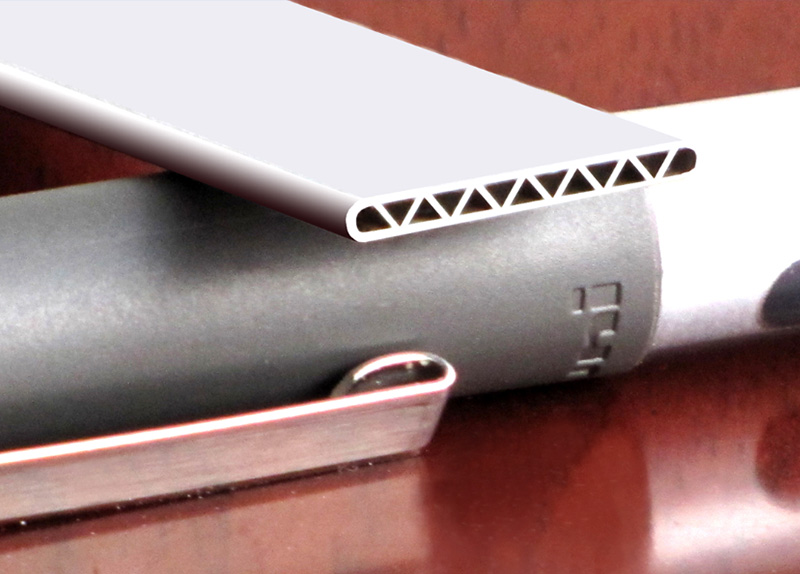
Structural Features of Aluminum Microchannel Tubes
Unlike conventional aluminum tubes, microchannel tubes boast a unique structure. Imagine a flat, rectangular tube extruded from aluminum. Within this tube lie several miniature channels, often rectangular or oval in shape. These channels are the heart of the microchannel tube, significantly increasing the surface area available for heat transfer. This high surface area-to-volume ratio is the key to their exceptional thermal performance.
The size and configuration of these channels can be meticulously tailored for specific applications. Channel dimensions typically range from a few hundred microns to a few millimeters, offering engineers the flexibility to optimize heat transfer based on the specific needs of a system. Additionally, the number of channels within a single tube can vary, allowing for further customization of the thermal performance.
Another crucial structural feature of aluminum microchannel tubes is the material itself. Aluminum offers a compelling combination of properties that make it ideal for this application. It possesses excellent thermal conductivity, efficiently transferring heat away from the source. Furthermore, aluminum is lightweight, a critical factor in industries where weight reduction is paramount, such as automotive and aerospace.
Applications of Aluminum Microchannel Tubes
The unique nature of aluminum microchannel tubes opens the door to a wide range of applications in various industries. Here are some outstanding examples of areas where these tubes have a significant impact:
- Automotive Industry: In a world striving for fuel efficiency, aluminum microchannel tubes play a vital role in automotive thermal management systems. They are used in engine oil coolers, transmission coolers, and air conditioning systems, contributing to improved engine performance and fuel economy. Their lightweight nature also aligns perfectly with the automotive industry’s focus on weight reduction.
- HVAC Systems: Heating, ventilation, and air conditioning (HVAC) systems rely heavily on efficient heat transfer. Aluminum microchannel tubes are finding increasing use in condensers and evaporators, the core components responsible for heat exchange. Their compact size allows for the creation of smaller, lighter heat exchangers, while their high surface area facilitates efficient heat transfer, leading to improved system performance and energy savings.
- Electronics Cooling: As electronic devices become more powerful, the challenge of managing heat dissipation becomes increasingly critical. Aluminum microchannel tubes offer a solution for thermal management in electronic components like CPUs, GPUs, and power electronics. Their ability to efficiently transfer heat away from sensitive components helps to ensure optimal performance and prevent overheating.
- Medical Devices: The medical field also benefits from the advantages of aluminum microchannel tubes. They are being used in dialysis machines, blood analyzers, and other medical equipment where precise temperature control is essential. Their compact size and efficient heat transfer make them ideal for these applications.
- Aerospace Industry: Weight reduction is paramount in the aerospace industry. Aluminum microchannel tubes, with their lightweight construction and excellent thermal performance, are being explored for use in aircraft heat exchangers and thermal management systems for spacecraft.
These are just a few examples of the diverse applications of aluminum microchannel tubes. As research and development continue, we can expect to see even more innovative uses emerge in the future.
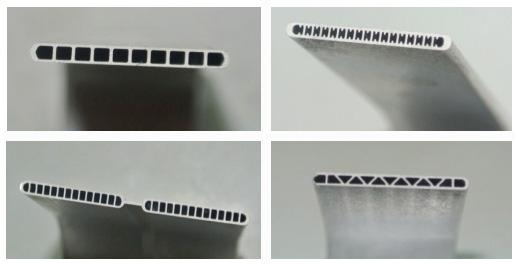
Aluminum Microchannel Tube Manufacturing Challenges
Although aluminum microchannel tubes are widely used in various industries, the manufacturing process of aluminum microchannel tubes is extremely complex and requires specialized technology. Overcoming these challenges is critical to ensuring consistent performance and reliability. Here, we delve into key manufacturing barriers and explore strategies to overcome them.
1. Overcoming the Hurdle of Ultra-High Extrusion Ratio
The extrusion process is the core of manufacturing aluminum microchannel tubes. During the extrusion process, the heated aluminum billet is forced to be shaped into the desired flat rectangular shape with internal channels through specially designed molds. The challenge lies in achieving ultra-high extrusion ratios, typically exceeding 400 times, which far exceed the capabilities of traditional aluminum extrusion processes.
To address this challenge, manufacturers are shifting towards specialized extruders equipped with high tonnage capacity and precise control systems. These presses can generate the enormous force required to create complex microchannel structures of aluminum-plastic while maintaining consistent wall thickness and channel dimensions. In addition, advanced mold design plays a crucial role in ensuring uniform flow distribution and preventing defects during the extrusion process.
2. Achieving Ultra-High Dimensional Precision
Aluminum microchannel tubes require excellent dimensional accuracy. The channel size usually ranges from a few hundred micrometers to a few millimeters, and even small deviations can significantly affect heat transfer performance. For example, the width dimension may need to be controlled between ± 0.01 and ± 0.02 millimeters.
To achieve this level of accuracy, meticulous control of the entire manufacturing process is required, from selecting high-quality raw materials to implementing strict quality control measures. Using advanced machining techniques such as precision CNC milling and grinding, the pipeline is precision machined to the required dimensions and tolerances.
3. Ensuring Impeccable Gas Tightness
Aluminum microchannel tubes are commonly used for sealing systems, such as automotive air conditioning and refrigeration circuits. Any leakage, even a small one, can lead to system failure and refrigerant loss. Therefore, achieving impeccable airtightness is crucial.
To ensure leak integrity, manufacturers have adopted various technologies. These technologies include strict cleaning processes to remove any pollutants or residues that may damage the seal, precision brazing or welding techniques to form a strong leak proof joint between the pipeline and manifold, and non-destructive testing methods such as X-ray photography and eddy current testing to detect any defects or defects in the channel.
4. Utilizing High-Quality Aluminum Billets
The quality of the aluminum billets used in the extrusion process directly impacts the final properties and performance of the microchannel tubes. Due to the thin walls of these tubes, often as thin as 0.13 mm, even minute impurities or defects in the aluminum can lead to failures.
To address this challenge, manufacturers employ high-purity aluminum billets that undergo rigorous refining processes to remove any contaminants or inclusions. These billets are also carefully inspected for defects before being used in the extrusion process.
5. Mastering Surface Zinc Spraying Technology
The quality of aluminum billets used in extrusion technology directly affects the final characteristics and performance of microchannel tubes. Due to the thin walls of these tubes, usually only 0.13 millimeters, even small impurities or defects in aluminum can cause malfunctions.
To address this challenge, manufacturers use high-purity aluminum billets that have undergone strict refining processes to remove any pollutants or inclusions. These billets will also undergo careful defect inspection before being used in the extrusion process.
6. Implementing Advanced Inline Flaw Detection
The complex nature of microchannel tubes requires real-time defect detection during the manufacturing process. This ensures that only defect free products can enter the next stage, thereby preventing expensive rework and potential system failures.
To achieve this goal, manufacturers are shifting towards advanced online defect detection technologies, such as ultrasonic testing, eddy current testing, and optical detection systems. These systems can scan pipelines in real time and identify any defects in the pipeline or pipe walls, such as cracks, inclusions, or blockages.
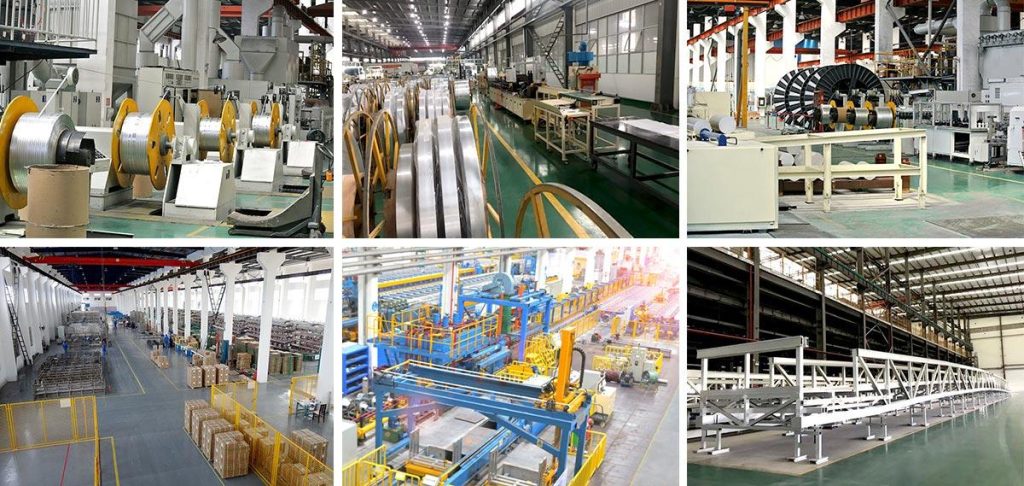
Conclusion
Aluminum microchannel tubes are an integral component in a variety of applications due to their unique properties such as lightweight, good thermal conductivity, and ease of manufacture. Their potential applications in areas such as biomedicine, environmental engineering, and automotive technology highlight their importance in addressing contemporary challenges. However, the continued development of aluminum microchannel tubes requires constant research and innovation to overcome the challenges associated with their manufacture and further improve their performance. Looking ahead, aluminum microchannel tubes are likely to play a more critical role in promoting scientific and technological progress.
If you are looking for aluminum microchannel tube suppliers, CHAL is a good choice. If you have any needs, please feel free to contact us at any time.