Aluminum microchannel tubes are increasingly valued in applications demanding compact, efficient heat exchangers, including HVAC systems, automotive radiators, and electronics cooling. These tubes feature multiple microscopic channels that allow fluids to circulate in ways that maximize heat exchange between surfaces, achieving substantial efficiency within compact spaces. However, optimizing their performance is crucial to reduce energy consumption and improve overall thermal management. This article will examine the factors that influence heat exchange efficiency in aluminum microchannel tubes, alongside a step-by-step outline of the calculation process. We will explore key design considerations, material properties, and environmental factors impacting the efficiency of these systems.
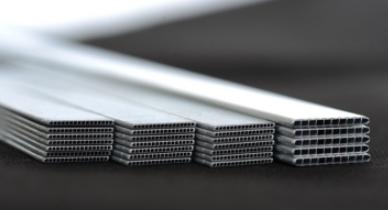
Section 1: Calculating Heat Exchange Efficiency of Aluminum Microchannel Tubes
1. Overview of Efficiency Calculation
Heat exchange efficiency is a measure of how effectively a system transfers heat between two fluids or between a fluid and its surrounding material. This efficiency is particularly significant in aluminum microchannel tubes because they are often used in high-stakes environments, where maximizing thermal efficiency helps lower energy usage and improve overall system reliability. By understanding how to calculate this efficiency, engineers and system designers can make informed adjustments to achieve optimal thermal performance.
2. Step-by-Step Calculation Process
Step 1: Determining the Heat Transfer Area and Geometric Parameters
The first step in calculating heat exchange efficiency involves understanding the specific geometric parameters of the microchannel tube. Microchannels are characterized by small cross-sectional areas and high aspect ratios, providing ample surface area for heat transfer. To start, measure or calculate the total surface area AAA available for heat transfer, as this forms the basis for calculating the efficiency.
Step 2: Calculating Fluid Heat Flow Rate
To determine the amount of heat transferred, it is essential to calculate the fluid’s heat flow rate QQQ:
Q=M·cp·ΔT
where:
- M is the mass flow rate of the fluid in kilograms per second,
- cp is the specific heat capacity of the fluid in joules per kilogram per kelvin,
- ΔT represents the temperature difference between the inlet and outlet of the fluid in kelvin.
This formula calculates the actual amount of heat transferred, making it foundational to understanding the system’s baseline performance.
Step 3: Determining the Overall Heat Transfer Coefficient
The overall heat transfer coefficient U quantifies how effectively heat moves across the surface. We calculate it using:
Q=U·A·ΔTlog
where:
- A is the total heat transfer area of the microchannel tube,
- ΔTlog is the log-mean temperature difference (LMTD), representing the driving force for heat transfer across the tube’s length.
The LMTD is defined as:
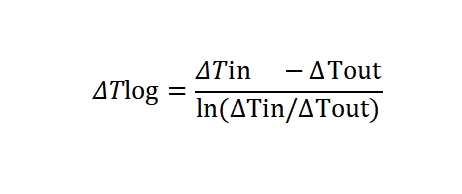
where ΔTin and ΔTout are the temperature differences of the fluids at the inlet and outlet, respectively.
Step 4: Calculating Efficiency
Finally, we calculate the system’s efficiency η using the following formula:
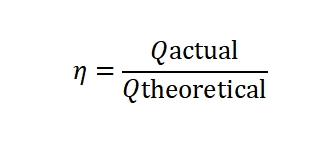
where:
- Qactual is the calculated heat transferred in step 2,
- Qtheoretical is the maximum potential heat transfer under ideal conditions.
Efficiency in aluminum microchannel tubes is often represented as a percentage, reflecting how close the system’s actual performance is to its theoretical maximum.
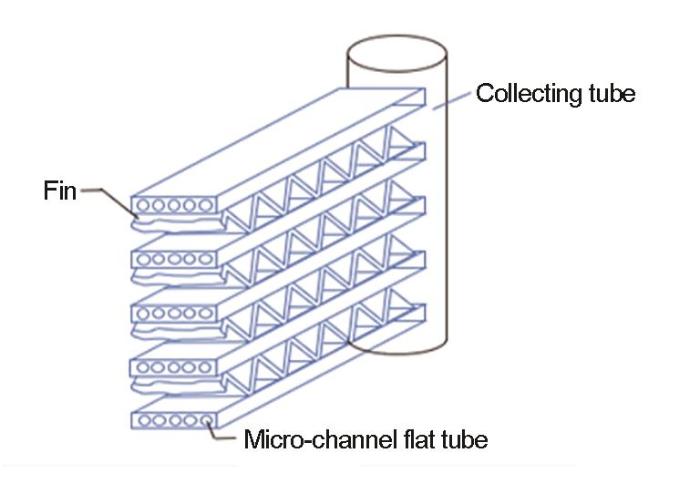
Section 2: Key Factors Influencing Heat Exchange Efficiency in Aluminum Microchannel Tubes
1. Fluid Properties
Fluid characteristics such as thermal conductivity, specific heat capacity, and viscosity impact heat exchange. For example:
- Thermal conductivity determines how well heat is conducted through the fluid, with higher conductivity generally improving efficiency.
- Specific heat capacity indicates the fluid’s ability to store heat energy; fluids with higher heat capacities absorb more heat per degree of temperature change.
- Viscosity impacts fluid flow within the microchannels, where high viscosity can increase flow resistance and reduce overall heat transfer.
Phase changes, like condensation or evaporation, can also significantly enhance heat transfer efficiency by adding latent heat.
2. Fluid Flow Rate
Higher fluid flow rates generally improve heat exchange by increasing the turbulence of the flow. In microchannels, turbulent flow enhances heat transfer by promoting better mixing of fluid layers, which reduces the temperature boundary layer thickness near the channel walls. However, increasing the flow rate also increases pressure drop, which could lead to system inefficiencies if the energy cost of maintaining the flow outweighs the benefits of heat transfer.
3. Microchannel Geometry and Structure
The shape, size, and number of microchannels within a tube impact heat transfer area and fluid dynamics:
- Channel width, depth, and shape dictate the surface area available for heat transfer and the fluid flow profile.
- Wall thickness affects thermal resistance; thinner walls provide better heat transfer but may sacrifice structural durability.
- The number of channels can increase heat transfer but add complexity to fluid distribution, possibly causing uneven flow and localized inefficiencies.
4. Aluminum Material Properties
Aluminum’s high thermal conductivity makes it an ideal material for microchannel tubes. However, impurities or defects in the aluminum can reduce its effective thermal conductivity. Additionally, surface finish and quality impact heat transfer. Smooth surfaces improve flow but may limit heat transfer, whereas rougher surfaces can promote turbulence and enhance heat exchange under specific conditions.
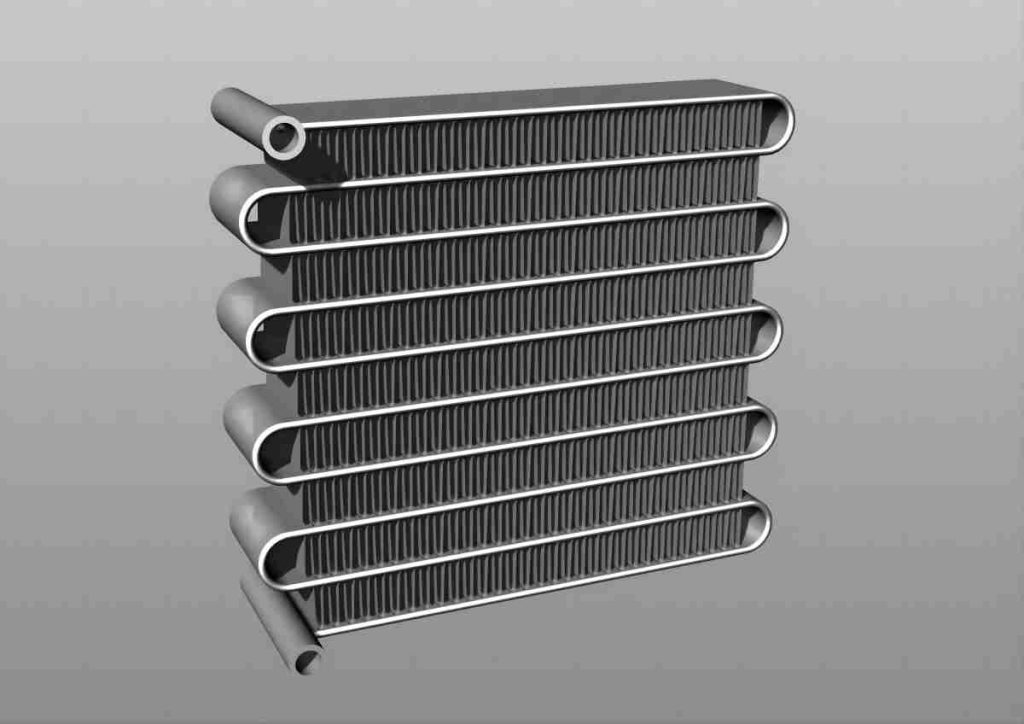
5. Temperature Difference
The efficiency of heat transfer is directly proportional to the temperature gradient between the fluid and the surrounding environment. Larger temperature differences yield greater heat transfer rates, boosting overall efficiency.
6. Surface Characteristics and Fouling
Surface roughness can influence fluid dynamics, with rougher surfaces potentially enhancing turbulence and promoting better heat transfer. However, surface roughness also increases the risk of fouling, as impurities in the fluid may adhere to the microchannel walls over time, reducing the effective heat transfer area and increasing thermal resistance. Regular maintenance is required to mitigate fouling in microchannel tubes.
7. Contact Thermal Resistance
The contact points between aluminum microchannel tubes and other materials or components can create thermal resistance, which inhibits heat transfer. Minimizing this resistance using thermally conductive adhesives, coatings, or surface treatments helps improve heat exchange efficiency.
8. Environmental Conditions
External factors such as temperature, humidity, and pressure influence heat transfer efficiency. For instance, high ambient temperatures may limit the cooling efficiency of microchannel tubes, especially in applications like automotive radiators. Higher humidity can enhance cooling but may increase condensation on surfaces, impacting performance.
Section 3: Practical Design Considerations and Optimization Strategies
To optimize aluminum microchannel tube performance, designers should:
- Adjust geometry to balance surface area with flow rate and pressure drop requirements.
- Choose fluid properties compatible with the operating temperature range and phase change behavior.
- Apply surface treatments to reduce fouling or enhance turbulence where beneficial.
- Minimize contact thermal resistance through coatings or adhesives at interfaces between tubes and other components.
- Evaluate environmental conditions and potentially adjust operating parameters to suit real-world application environments.
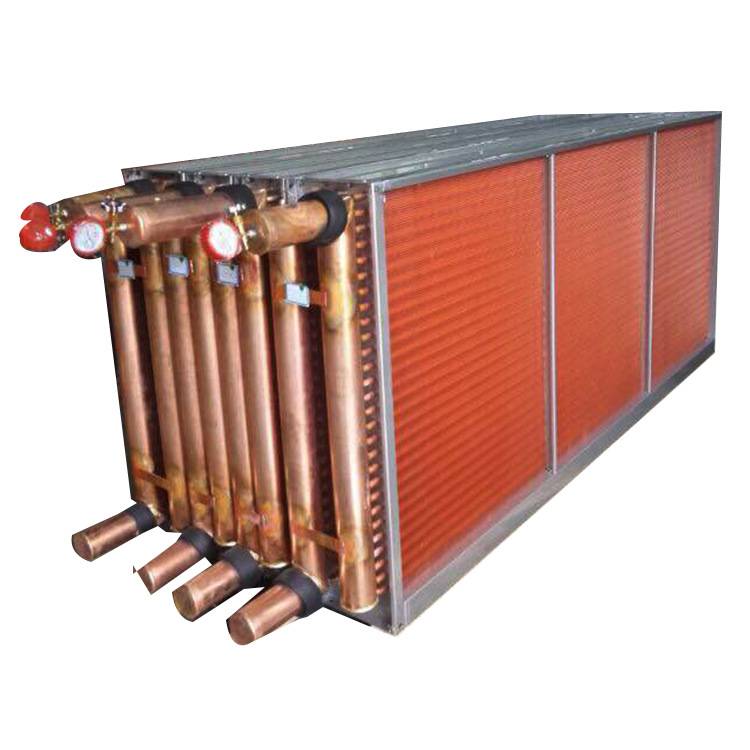
Flat Aluminum Microchannel Tubes in air condition system
Overall, Aluminum microchannel tubes are powerful tools for efficient heat exchange across a range of applications. By carefully considering fluid properties, flow rates, tube geometry, material quality, and external conditions, designers can significantly improve heat exchange efficiency. Through detailed calculation methods and strategic design adjustments, these systems offer reliable and effective solutions for advanced thermal management needs.