Microchannel tubes have emerged as a game-changer in various industries due to their exceptional heat transfer capabilities. When combined with the unique properties of aluminum, these tubes offer a powerful solution for thermal management applications. This article delves into the world of aluminum microchannel tubes, exploring their types, manufacturing processes, applications, advantages, and potential drawbacks.
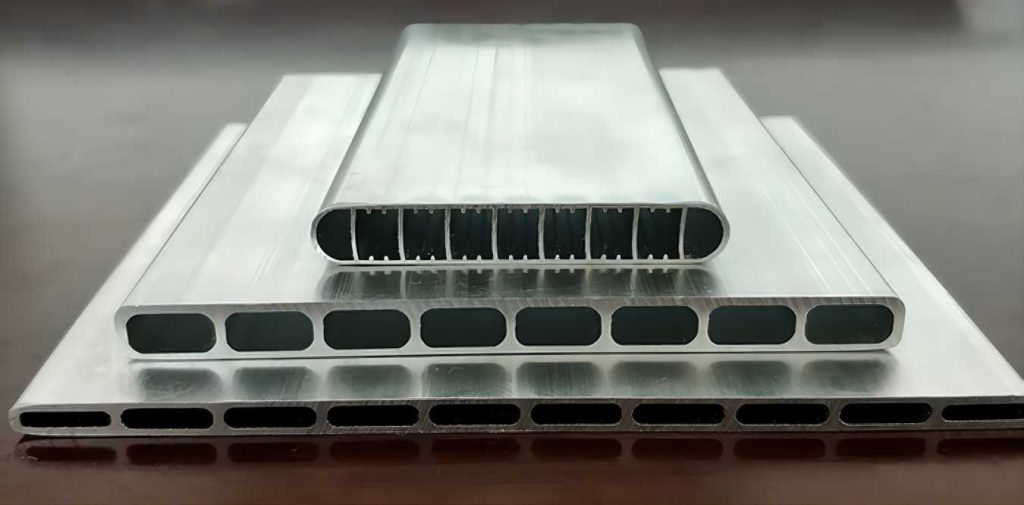
Understanding Microchannel Technology
Microchannel technology utilizes a network of miniature channels, typically ranging from 10 to 200 micrometers in diameter, to facilitate efficient heat transfer between fluids. The large surface area created by these tiny channels allows for rapid heat exchange, making them ideal for applications where thermal management is critical.
Here’s why microchannel tubes are so effective:
- Increased Surface Area: Compared to traditional tubes with a single, larger passage, microchannels significantly increase the surface area exposed to the flowing fluids. This enhanced area allows for faster heat exchange between the fluids and the tube walls.
- Reduced Flow Path Length: The shorter flow path within microchannels minimizes pressure drops across the tube. This translates to lower pumping power requirements, leading to improved energy efficiency.
Why Aluminum For Microchannel Tubes?
Aluminum possesses several properties that make it an excellent material for microchannel tubes:
- Lightweight: Aluminum is significantly lighter than other commonly used heat exchanger materials like copper. This weight reduction is crucial in applications where weight is a critical factor, such as aerospace and automotive industries.
- Excellent Heat Conductor: Aluminum boasts high thermal conductivity, enabling it to efficiently transfer heat away from the source and into the flowing fluid. This rapid heat dissipation helps maintain optimal operating temperatures for sensitive components.
- Corrosion Resistance: While pure aluminum can be susceptible to corrosion, various aluminum alloys offer excellent corrosion resistance, making them suitable for a wider range of applications.
By combining the benefits of microchannel technology with the properties of aluminum, aluminum microchannel tubes offer a unique solution for a variety of thermal management challenges.
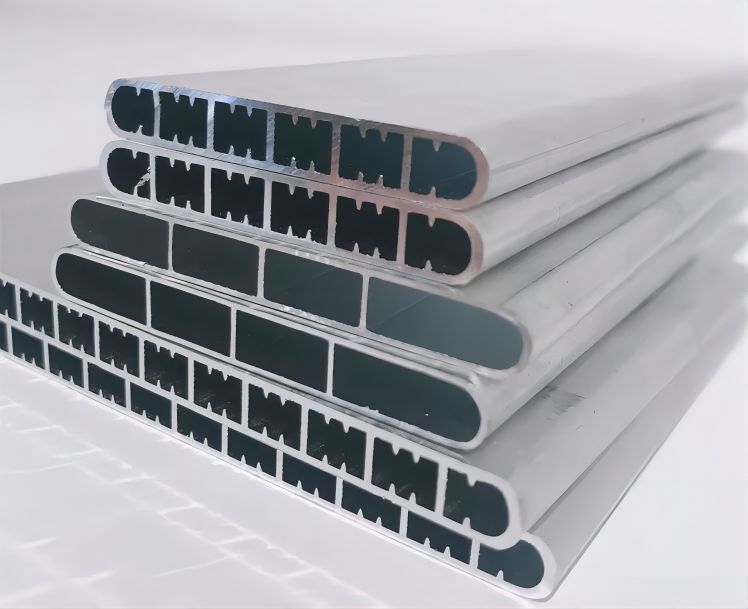
Types of Aluminum Microchannel Tubes
There are two primary configurations of aluminum microchannel tubes:
- Multi-Port Extruded Aluminum Tube: This type is manufactured using a high-precision extrusion process. The process forces molten aluminum through a die containing the desired microchannel pattern, resulting in a long, continuous tube with multiple internal channels. These tubes offer a high degree of design flexibility in terms of channel size, shape, and overall tube dimensions.
- Folded Aluminum Microchannel Tube: This variation utilizes a thin aluminum sheet that is precisely formed into a microchannel structure. There are two main subtypes:
- Two-Piece Folded Tube: This design involves forming separate pieces for the outer tube and the inner fin structure containing the microchannels. These pieces are then brazed together to create the final microchannel tube.
- One-Piece Folded Tube: This approach utilizes a single sheet of aluminum that is roll-formed into the desired microchannel configuration. This method offers a more streamlined manufacturing process compared to the two-piece design.
The choice between these types depends on factors such as the required channel geometry, production volume, and cost considerations.
Main Manufacturing Process of Aluminum Microchannel Tubes
The specific manufacturing process for aluminum microchannel tubes varies depending on the chosen type:
- Multi-Port Extruded Aluminum Tube: The process begins with molten aluminum being heated to a specific temperature. This molten metal is then forced through a precisely designed die containing the desired microchannel pattern. The extruded tube undergoes further processing, such as straightening, cutting, and cleaning, to achieve the final product.
- Folded Aluminum Microchannel Tube: For the two-piece design, separate sheets of aluminum are formed into the desired shapes using specialized forming tools. These formed pieces are then brazed together to create the final microchannel tube. In the one-piece approach, a single sheet of aluminum is continuously roll-formed into the microchannel configuration, eliminating the need for brazing.
Throughout the manufacturing process, strict quality control measures are essential to ensure the dimensional accuracy and integrity of the microchannels. Any deviation from the specified dimensions can significantly impact the heat transfer performance of the tubes.
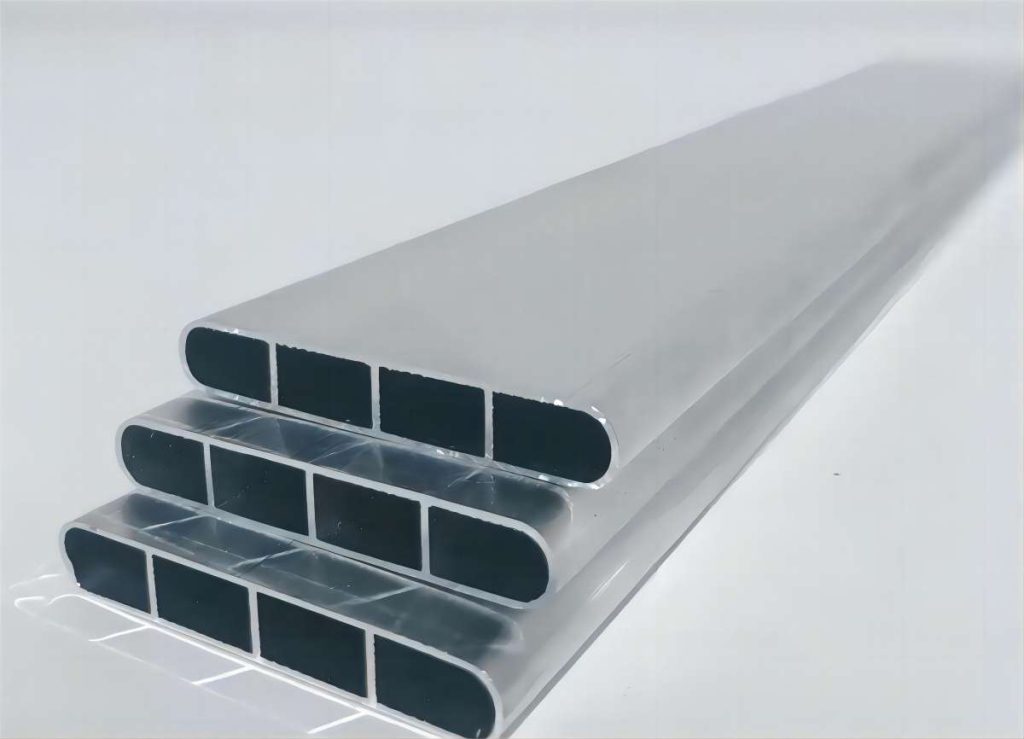
Applications of Aluminum Microchannel Tubes
Aluminum microchannel tubes find application in various industries due to their outstanding thermal management capabilities. Here are some key areas where they are making a significant impact:
- Heat Exchangers: In automotive applications, aluminum microchannel tubes are being employed in radiators and condensers for air conditioning systems. Their lightweight nature and efficient heat transfer improve fuel efficiency and overall performance. Similarly, HVAC systems are utilizing these tubes in condensers and evaporators to enhance efficiency and reduce energy consumption. The refrigeration industry also benefits from the use of aluminum microchannel tubes in condensers and evaporators for improved cooling performance.
- Electronics Cooling: The ever-increasing heat generation of electronic components poses a significant challenge. Aluminum microchannel tubes are finding widespread use in cooling high-power processors, LED lighting fixtures, and power electronics. Their compact size and excellent heat transfer enable efficient thermal management in space-constrained electronic devices.
- Aerospace Applications: The aerospace industry prioritizes lightweight materials with superior thermal management capabilities. Aluminum microchannel tubes are ideal for applications like aircraft heat exchangers, spacecraft thermal control systems, and engine cooling systems. Their ability to efficiently dissipate heat while minimizing weight is crucial for optimizing aircraft performance and fuel efficiency.
- Medical Devices: The medical field also leverages the advantages of aluminum microchannel tubes. They are being used in blood analyzers, laser equipment, and dialysis machines for effective thermal management. Their compact size and efficient heat dissipation contribute to the development of more compact and efficient medical devices.
- Emerging Applications: The potential applications of aluminum microchannel tubes are constantly expanding. Research is ongoing to explore their use in battery thermal management systems for electric vehicles, fuel cell cooling systems, and concentrated solar power plants. As the technology matures and production costs decrease, we can expect to see aluminum microchannel tubes revolutionize thermal management across various industries.
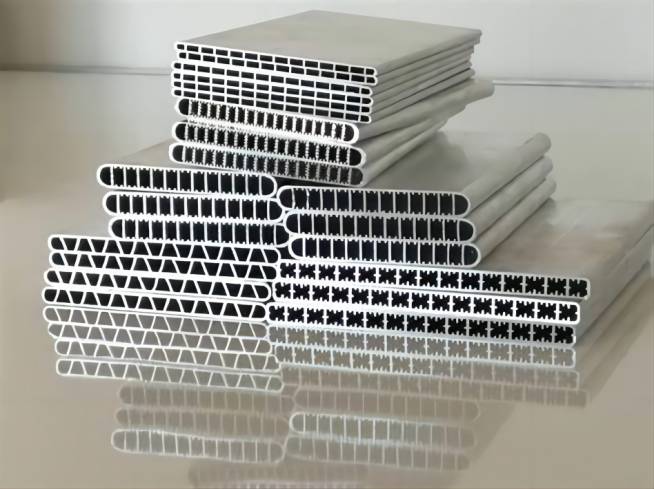
Weighing the Advantages and Disadvantages
While aluminum microchannel tubes offer numerous benefits, it’s important to consider their potential drawbacks:
- Manufacturing Complexity: The production process for aluminum microchannel tubes, particularly the multi-port extruded type, can be complex and require specialized equipment. This complexity can translate to higher upfront costs compared to traditional heat exchanger designs.
- Potential for Clogging: The small size of the microchannels can make them susceptible to clogging in applications involving fluids with high particulate content. Proper filtration systems are crucial to mitigate this risk.
Despite these limitations, the advantages of aluminum microchannel tubes often outweigh the disadvantages. With advancements in manufacturing techniques and ongoing research, the challenges associated with complexity and clogging are being continuously addressed.
Conclusion
Aluminum microchannel tubes represent a significant advancement in thermal management solutions. By combining the advantages of microchannel technology with the unique properties of aluminum, these tubes offer a lightweight, efficient, and versatile solution for various applications. As research and development efforts continue, the future of aluminum microchannel tubes is bright, promising even greater efficiency and innovation in thermal management across diverse industries.