Aluminum microchannel tubes and multiport extruded aluminum tubes represent innovative solutions in heat transfer technology, each tailored for specific applications in automotive, electronics, and various industrial sectors. This article delves into their similarities, differences, and unique features, offering insights into their performance and suitability in different scenarios.
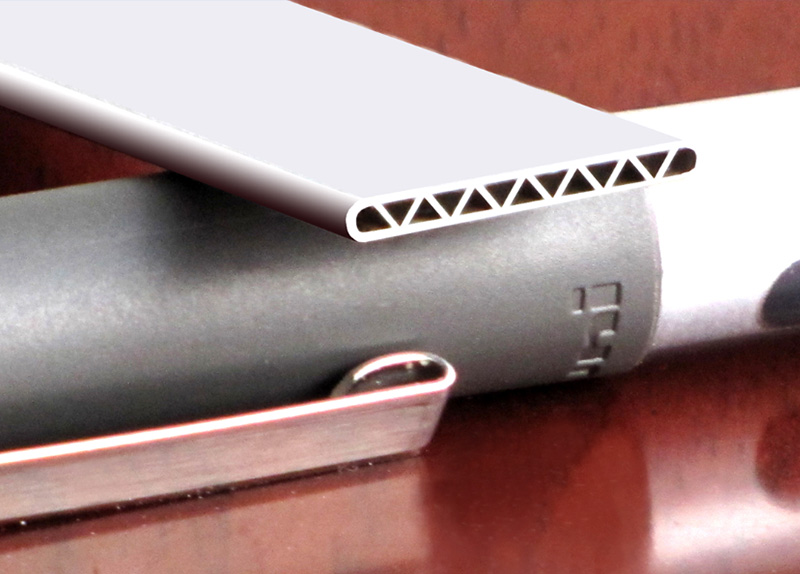
Commonalities
- Material Composition: Both aluminum microchannel tubes and multiport extruded aluminum tubes are constructed from aluminum, a material renowned for its excellent thermal conductivity and low density. Aluminum’s thermal properties make it ideal for applications requiring efficient heat transfer, while its lightweight nature contributes to reduced overall system weight.
- Application Areas: Both types of tubes are employed in high-efficiency applications such as automotive air conditioning systems, electronic device cooling, and other thermal management solutions. Their ability to facilitate effective heat exchange and fluid flow makes them suitable for various critical systems where performance is paramount.
Differences
1. Structural Characteristics
Aluminum Microchannel Tubes: These tubes feature an internal structure composed of multiple microchannels. This design provides a high surface area-to-volume ratio, significantly enhancing heat exchange efficiency. The microchannels create a complex internal geometry that facilitates better heat transfer by increasing the fluid’s contact area with the tube walls.
Multiport Extruded Aluminum Tubes: In contrast, multiport extruded tubes have a simpler internal structure with multiple ports for fluid entry and exit. While these tubes can manage multiple fluid paths, their internal geometry is less complex compared to microchannel tubes. This simplicity allows for straightforward fluid distribution but may not achieve the same level of heat transfer efficiency.
2. Heat Exchange Efficiency
Aluminum Microchannel Tubes: The microchannel design provides superior heat exchange efficiency. The high surface area-to-volume ratio allows for enhanced heat transfer, as the small channels promote turbulence in the fluid flow. This turbulence increases the interaction between the fluid and the tube walls, improving thermal performance.
Multiport Extruded Aluminum Tubes: While still effective in fluid management, multiport tubes generally have lower heat exchange efficiency. The simpler structure and potentially turbulent flow in the larger channels can lead to less efficient heat transfer compared to the microchannel design.
3. Application Scenarios
Aluminum Microchannel Tubes: Due to their superior heat exchange performance, microchannel tubes are often used in high-performance applications such as advanced automotive air conditioning systems and high-end electronic cooling solutions. Their ability to handle high thermal loads and provide efficient cooling makes them ideal for these demanding environments.
Multiport Extruded Aluminum Tubes: These tubes are typically used in systems where multiple fluid inlets and outlets are needed, but where heat exchange efficiency is not as critical. They are suitable for general fluid distribution and management tasks in various systems, where the primary concern is fluid flow rather than thermal performance.
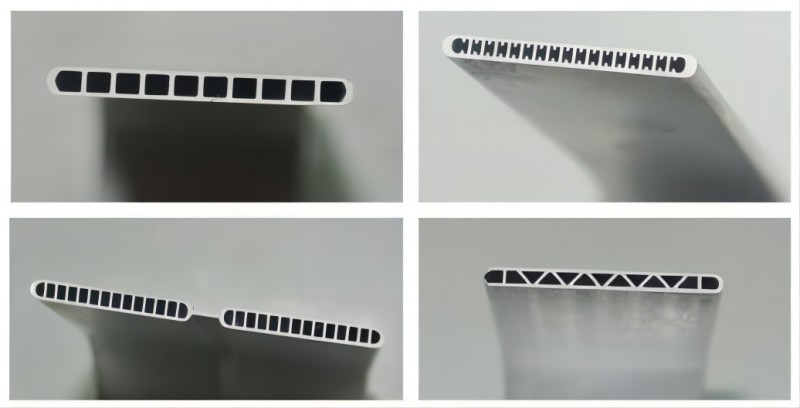
4. Production Difficulties and Manufacturing Process
Aluminum Microchannel Tubes: The production of aluminum microchannel tubes involves advanced and intricate techniques, such as continuous extrusion and flow welding extrusion.
- Continuous Extrusion: This method involves extruding aluminum billets through a specially designed die to create tubes with complex microchannel structures. The process demands precise control and specialized equipment to ensure a consistent microchannel pattern and high precision. Continuous extrusion is complex and often incurs higher costs due to the technical expertise required.
- Flow Welding Extrusion: In this technique, aluminum is extruded through a die with flow channels that are subsequently welded together in a controlled environment. This method produces tubes with well-defined microchannel structures, offering stability and strength. Despite its benefits, flow welding extrusion is challenging and requires careful control of process parameters to maintain performance.
Overall, the production of microchannel tubes is more complex and demanding compared to other types of tubes, involving higher costs and technical expertise.
Multiport Extruded Aluminum Tubes: In contrast, multiport extruded aluminum tubes are produced using a more straightforward and conventional extrusion process.
- Extrusion Process: This process involves heating aluminum billets and extruding them through a die to form tubes with multiple ports. The method is less complex and more suited for high-volume production. It results in tubes with uniform wall thickness and multiple channels designed to facilitate fluid flow. Due to its simplicity and established nature, the extrusion process for multiport tubes is more cost-effective and easier to implement.
In summary, while aluminum microchannel tubes require advanced production techniques and are more costly and complex to manufacture, multiport extruded aluminum tubes benefit from a simpler, more cost-effective extrusion process suitable for high-volume production.
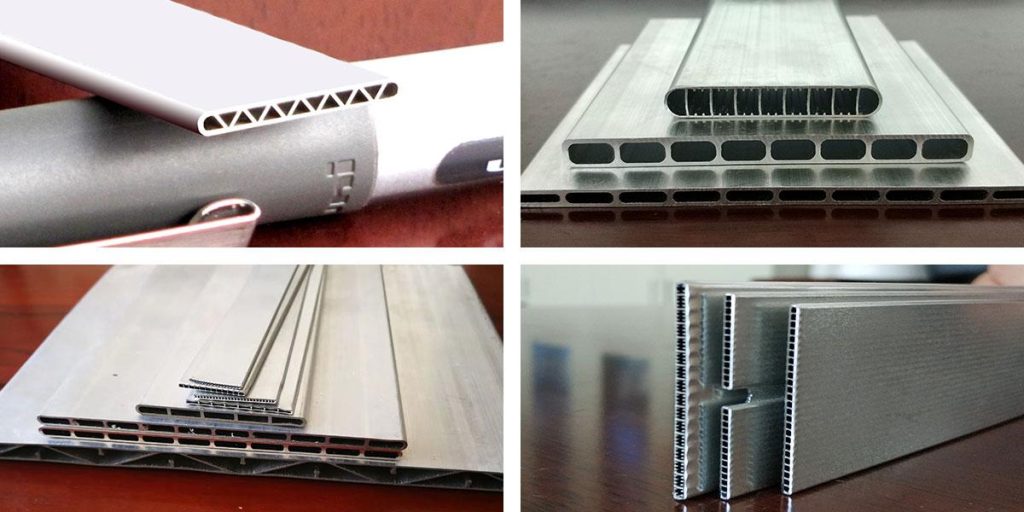
Why Is the Thermal Efficiency of Microchannel Over Multiport Extruded?
The high thermal efficiency of aluminum microchannel tubes is attributable to several key factors:
- High Surface Area-to-Volume Ratio: The microchannel design provides a large surface area within a compact volume, enhancing heat transfer capabilities. This structure allows for more effective thermal exchange between the fluid and the tube walls.
- Fluid Dynamics Optimization: Microchannel tubes often maintain laminar flow within the channels, which reduces energy losses associated with turbulence. This optimized flow pattern ensures more uniform heat transfer and minimizes inefficiencies.
- Reduced Thermal Resistance: The small channel sizes in microchannel tubes shorten the fluid’s flow path, reducing thermal resistance. This design allows for a more efficient transfer of heat from the fluid to the surrounding environment.
- Minimized Fluid-Induced Vibration: The design of microchannel tubes reduces the potential for fluid-induced vibrations, which can lead to additional heat loss and structural fatigue. By minimizing these vibrations, microchannel tubes maintain stable thermal performance.
- Advances in Manufacturing Techniques: Modern manufacturing methods enable precise control of microchannel dimensions and ensure consistent performance. These advancements contribute to the overall efficiency of the heat exchange process.
Advantages of Aluminum Microchannel Tubes in Electronic Cooling
In the realm of electronic cooling, aluminum microchannel tubes offer several advantages over multiport extruded aluminum tubes:
- Enhanced Heat Exchange Efficiency: The high surface area to volume ratio of microchannel tubes facilitates superior heat exchange, crucial for maintaining the operating temperatures of high-performance electronic components.
- Improved Thermal Management: Microchannel tubes enable more uniform temperature distribution within electronic devices, reducing hot spots and improving the overall reliability and lifespan of the electronics.
- Lightweight and Compact Design: The compact design of microchannel tubes reduces the weight and volume of cooling systems, making them particularly suitable for portable and space-constrained devices.
- Adaptability to Complex Cooling Requirements: The customizable internal structure of microchannel tubes can be tailored to meet the specific cooling demands of various electronic components, making them versatile in different application scenarios.
- Superior Manufacturing Process: Advanced manufacturing techniques used in the production of microchannel tubes ensure high product consistency and performance, which is critical for the high-reliability standards of electronic devices.
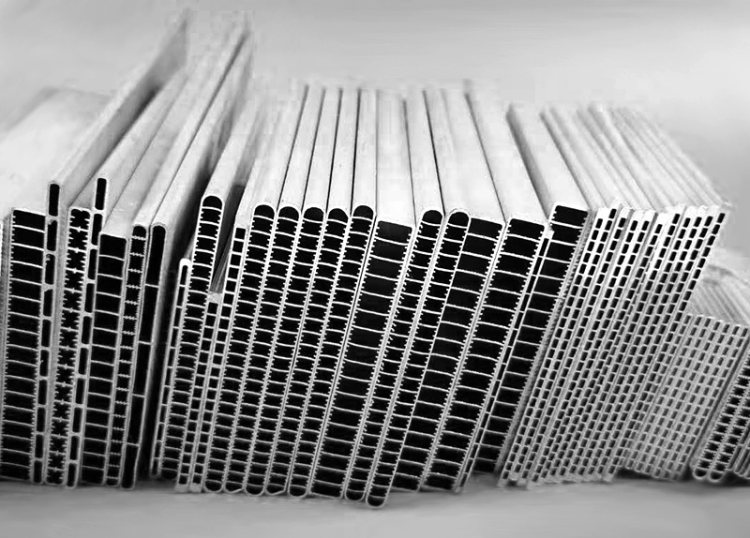
Conclusion
In summary, aluminum microchannel tubes and multiport extruded aluminum tubes, while both serving heat transfer functions, have distinct features and applications. Aluminum microchannel tubes, with their intricate microchannel design, excel in high-performance heat exchange scenarios, particularly in advanced automotive systems and high-end electronics cooling. Conversely, multiport extruded aluminum tubes, with their simpler structure and multiple ports, are well-suited for applications requiring fluid management without the need for the high heat exchange efficiency provided by microchannel tubes. Understanding the specific requirements of each application is key to selecting the most appropriate technology for heat transfer solutions.