Aluminum paste is a versatile metallic pigment known for its wide range of applications, primarily in paints and inks. This pigment is composed of flake aluminum particles suspended in a petroleum solvent, which together provide a unique metallic sheen and improved coverage. The use of aluminum paste spans various industries, from automotive and construction to electronics and fashion, due to its ability to enhance the visual and functional properties of coatings.
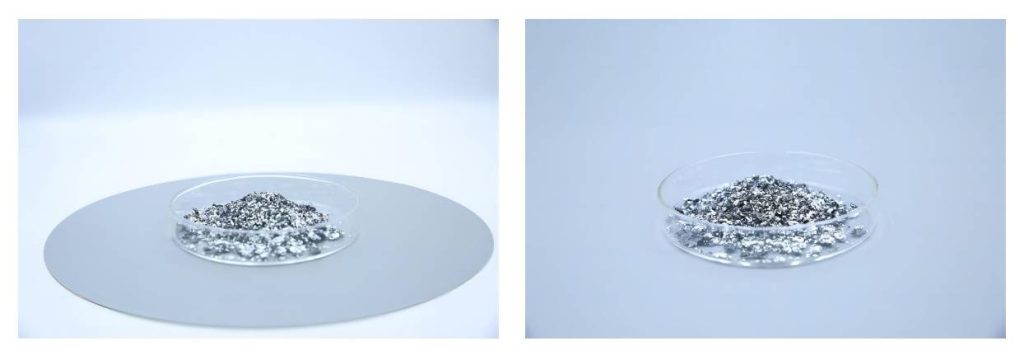
Classification of Aluminum Paste by Particle Size
One of the most critical factors influencing the properties and applications of aluminum paste is the size of its particles. Particle size affects the pigment’s dispersion, optical properties, and overall performance in the end product. Aluminum paste is typically classified based on the average diameter of its particles, measured in micrometers (μm). This classification helps in selecting the appropriate type of aluminum paste for specific applications. As the following table shows:
classification | Average Diameter | Characteristics |
Fine Aluminum Paste | 3-14μm | This category of aluminum paste features particles with high whiteness and excellent coverage. The fine particle size ensures a smooth and uniform metallic sheen, making it ideal for applications requiring a refined metallic finish. |
Fine Sparkling Aluminum Paste | 15-30μm | Fine sparkling aluminum paste offers moderate brightness and a noticeable sparkling effect. This type of paste is suitable for decorative applications where a balance between brightness and sparkle is desired. |
Sparkling Aluminum Paste | >30μm | Sparkling aluminum paste provides high brightness and a pronounced sparkling effect. Its larger particles create a more pronounced metallic appearance, making it suitable for applications that require a bold and shiny finish. |
These classifications highlight the different decorative effects and application scenarios of aluminum paste in coatings. Fine particles are used where a delicate metallic luster is needed, while coarse particles are chosen for their stronger covering power and striking visual impact.
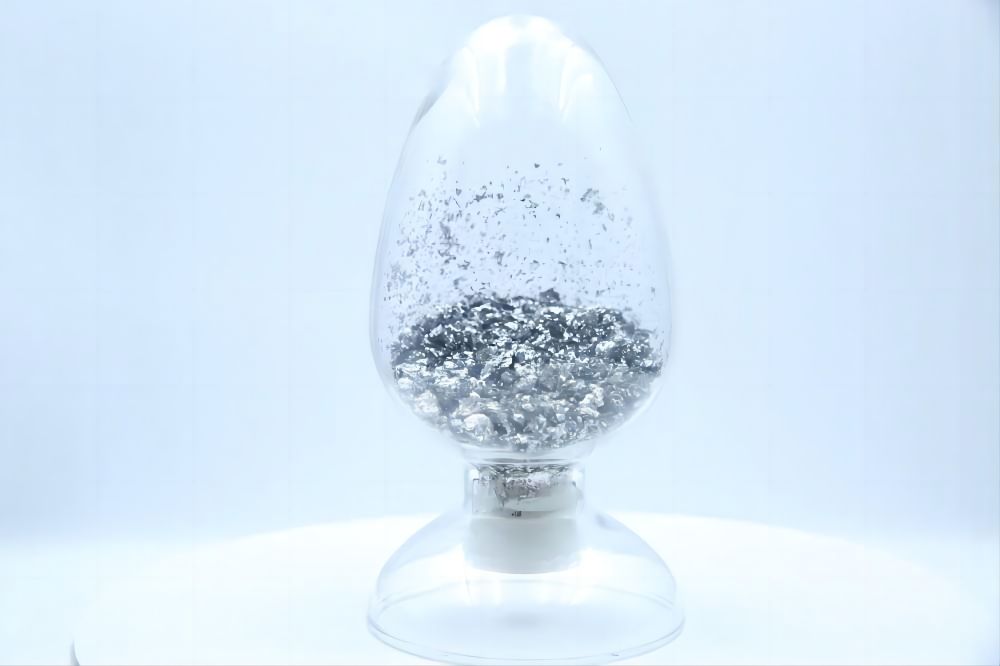
Composition of Aluminum Paste
Aluminum paste is not merely a simple mixture of aluminum particles and solvents; its formulation is carefully designed to achieve specific performance characteristics. Key components include:
- Aluminum Powder: The primary ingredient in aluminum paste, aluminum powder, imparts the silver-white metallic luster and provides the necessary coverage. The purity of aluminum powder used ranges from 99.3% to 99.9%, with particle shapes varying from snowflake and fish scale to coin-like forms. These different shapes influence the final product’s gloss and application effects.
- Additives: Additives are incorporated to improve the dispersion and stability of aluminum powder in the coating. Common additives include stearic acid, saturated and unsaturated fatty acids, and oleic acid. These substances help to adjust the surface tension of the aluminum paste, ensuring uniform distribution within the coating medium or the formation of a surface layer.
- Solvents: Solvents are used to adjust the viscosity of aluminum paste, making it suitable for different coating processes. The choice of solvent depends on whether the aluminum paste is water-based or oil-based and the required application performance.
- Surface Treatment Agents: To enhance the corrosion resistance and weatherability of aluminum powder, surface treatments such as silanization or chromization are applied. These treatments improve the adhesion of aluminum powder to the coating substrate, ensuring durability and longevity.
The specific formulation of aluminum paste can vary based on the manufacturer’s technology and the specific requirements of the application. High-quality aluminum paste provides excellent metallic effects and long-term durability, making it widely used in automotive coatings, architectural paints, electronic products, and printing inks.
Aluminum Paste Applications in the Coating Industry
Aluminum paste plays a vital role in the coating industry, offering unique decorative effects and performance enhancements across various types of coatings. Some specific applications include:
- Decorative Coatings: Aluminum paste imparts a metallic sheen and vibrant appearance to coatings. It is commonly used in decorative coatings for automobiles, bicycles, and household appliances, enhancing their aesthetic appeal.
- Functional Coatings: Due to its excellent reflectivity and heat resistance, aluminum paste is used in functional coatings that provide sun-blocking and heat-insulating effects. For example, exterior wall coatings with aluminum paste can reduce building interior temperatures and lower energy consumption.
- Coil Coatings: In the production of pre-coated metal sheets, aluminum paste is used in topcoats, backcoats, and primers. It enhances the corrosion resistance of the substrate while providing a decorative finish.
- Safety Signage and Equipment: Aluminum paste is used in reflective coatings to enhance nighttime visibility. It is applied in traffic signs, road markings, and other safety equipment to improve safety and visibility.
- Leather and Textiles: In the fashion industry, aluminum paste is used to add visual appeal to products by providing a unique metallic texture. This application enhances the aesthetic value of leather goods and textiles.
These applications demonstrate the versatility and multifunctionality of aluminum paste in the coating industry. It not only improves the appearance of products but also provides additional protection and functionality. With the growing demand for environmentally friendly and high-performance coatings, the application prospects of aluminum paste are promising, and it is expected to play a significant role in more innovative products.
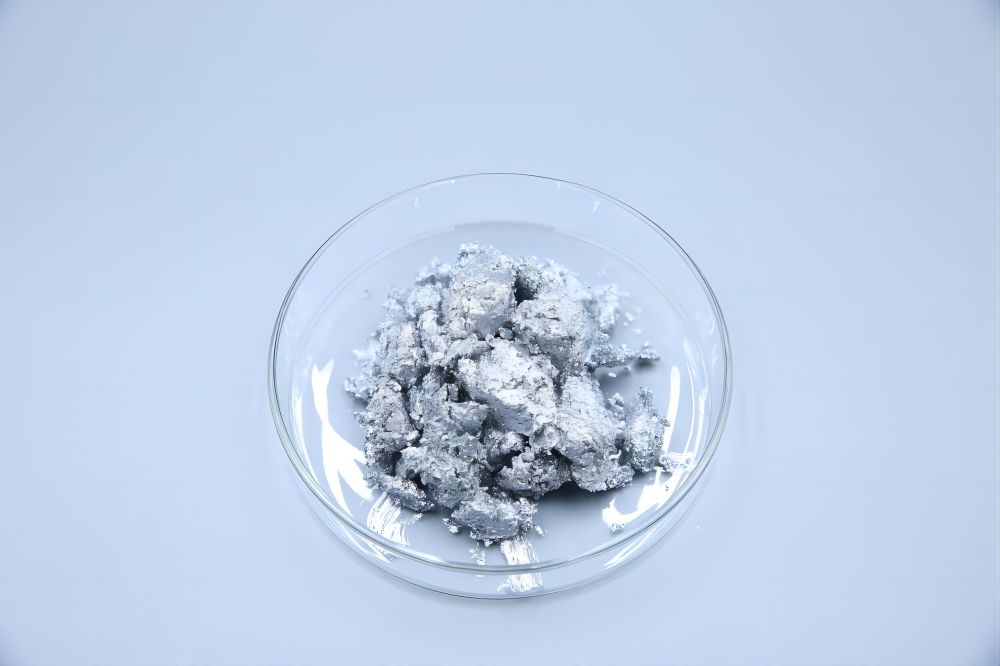
Impact of Aluminum Paste Particle Size on Performance
The performance of aluminum paste, including its dispersion, gloss, coverage, and durability in coatings, is significantly influenced by the particle size of the aluminum paste. Here are some critical aspects of how particle size affects performance:
1. Dispersion
- Smaller Particles: These generally have a larger specific surface area, which improves dispersion in the coating medium. Better dispersion ensures a uniform metallic effect and optimal coverage. However, smaller particles are prone to aggregation, requiring careful handling and dispersion measures during production.
- Larger Particles: While they may offer slightly less efficient dispersion, larger particles can enhance the electrical conductivity of the coating, which is beneficial for specific applications.
2. Optical and Functional Properties
- Fine Particles: Offer finer metallic luster and better coverage, providing a smooth, glossy finish.
- Coarse Particles: Enhance brightness and the sparkling effect, giving a more striking visual appearance.
3. Coating Uniformity
- Uniform Particle Size Distribution: Essential for achieving a smooth, continuous metallic effect in coatings.
- Uneven Distribution: Larger particles tend to settle faster, while smaller particles remain suspended longer, leading to uneven coating, potential spotting, streaking, or color inconsistencies.
Factors Influencing Aluminum Paste Particle Size Selection
Selecting the ideal particle size range for aluminum paste is a complex decision that involves considering several factors:
- Application Requirements: Different industries have varying requirements for gloss, coverage, and visual effects. For instance, automotive coatings demand high gloss and color consistency, whereas architectural paints may prioritize cost-efficiency and durability.
- Optical Effects: Particle size directly impacts the optical properties such as gloss and color shift effects. Fine particles usually provide a more refined metallic appearance, while larger particles offer a more pronounced, reflective look.
- Dispersion: The ability of aluminum paste to disperse uniformly in the coating matrix is crucial. Particle size and shape, along with the choice of additives, significantly affect dispersion.
- Coating Performance: Smaller particles tend to create a more uniform coating, while larger particles can contribute to increased permeability, affecting the coating’s protective properties.
- Cost Considerations: Producing fine particle aluminum paste is generally more expensive. Therefore, a balance between performance and cost must be struck, often opting for medium particle sizes to achieve satisfactory results without excessive costs.
In practical terms, selecting the right aluminum paste involves a careful evaluation of these factors, combined with laboratory testing and sample evaluation, to ensure that the chosen particle size meets the specific needs of the application.
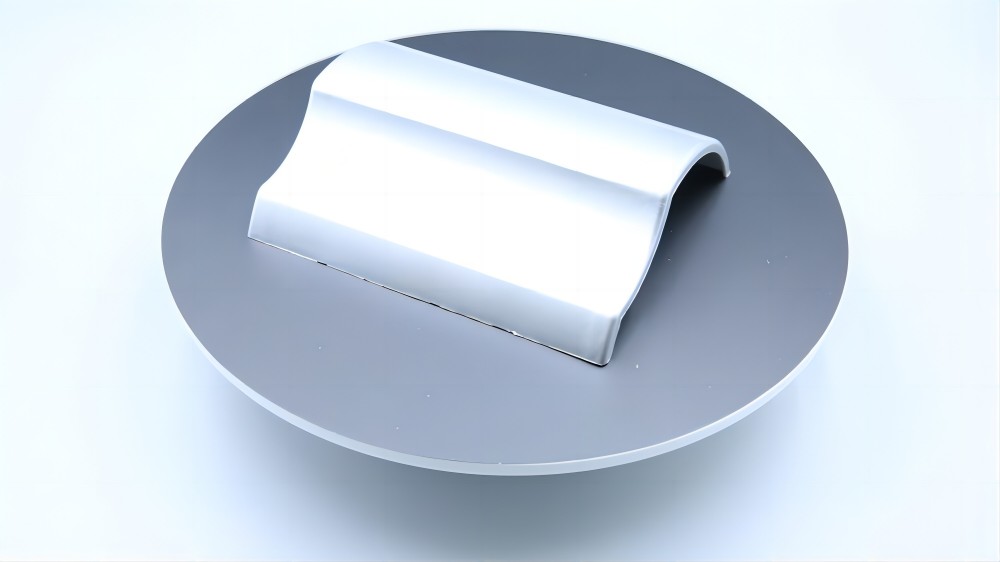
Conclusion
The classification and application of aluminum paste based on particle size play a crucial role in its effectiveness and versatility across various industries. The careful selection of particle size can significantly impact the dispersion, optical properties, and overall performance of the coatings. With its wide range of applications, from decorative to functional coatings, aluminum paste continues to be an essential component in modern coating technologies. As the demand for high-performance and environmentally friendly coatings grows, aluminum paste is poised to become an even more integral part of innovative product development.