Within the realm of industrial applications, aluminium asserts its presence through diverse formulations. Two prominent derivatives worthy of exploration are aluminium paste and alumina paste, often mistakenly treated as synonyms. This article dissects their unique constitutions, unveils their distinctive properties, and illuminates their contrasting avenues of implementation, guiding informed material selection within specific contexts.
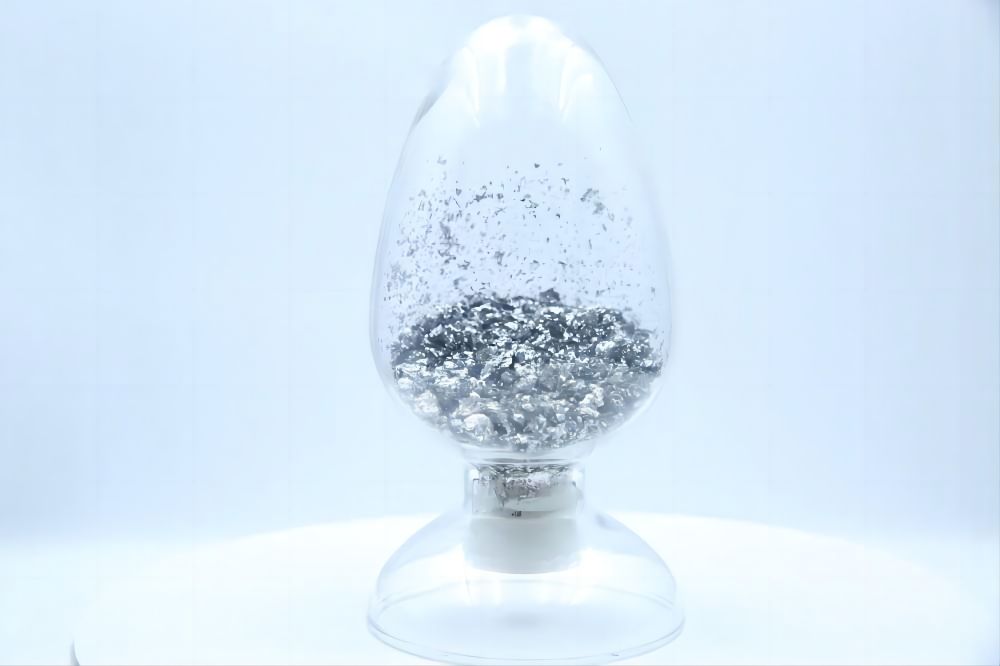
A Comparative Analysis of Aluminium Paste and Alumina Paste Compositions
The divergent material landscapes of aluminium paste and aluminium oxide paste begin at the fundamental level of their atomic constituents. Aluminium paste, at its core, harbours a suspension of finely micronized aluminium particles within a carefully chosen carrier medium. This carrier, typically a solvent or oil, acts as a medium for dispersing and manipulating the metallic flakes. The meticulous control over particle size, achieved through specialized milling processes, dictates the paste’s inherent properties. Coarser flakes, characterized by their larger surface area, excel in reflecting incident radiation, rendering them ideal for applications requiring high reflectivity. Conversely, finer particulates, owing to their increased surface area-to-volume ratio, promote smooth spreading and superior adhesion, making them suitable for applications demanding precise coating and uniform distribution.
Aluminium oxide paste, on the other hand, departs from the metallic realm and embraces a distinct chemical identity. This material originates from the intimate union of aluminium and oxygen, resulting in the formation of aluminium oxide (Al2O3), an inorganic compound with a crystalline structure. Unlike the flaky morphology of its metallic counterpart, aluminium oxide adopts a more ordered arrangement of atoms, manifesting as either dense, agglomerated granules or micron-sized, spherical particles. This crystalline structure imbues the material with unique properties, including exceptional hardness and controlled abrasive action, making it a valuable tool for material removal and surface refinement.
In essence, the compositional divergence between these two materials lies not only in the fundamental nature of their constituent elements but also in the arrangement of those elements at the atomic level. This disparity translates into a spectrum of unique properties, dictating the distinct applications for which each material is best suited.
The Properties of Aluminium Paste and Alumina Paste
The inherent compositions of aluminium paste and alumina paste translate into a diverse tapestry of properties, each with distinct advantages and limitations. Let us embark on a detailed exploration of these material characteristics.
Aluminium Paste
- Reflectivity: The metallic flakes within aluminium paste act as miniature mirrors, effectively reflecting incident light and thermal radiation across a broad spectrum. This property is governed by the size and distribution of the flakes. Larger flakes maximize reflectivity, making them ideal for applications like traffic signs and decorative coatings requiring high visibility. Conversely, finer flakes offer improved spreading and adhesion, finding use in thermal insulation applications where smooth, uniform coverage is crucial.
- Lubrication: The interlayer spacing between aluminium flakes exhibits lubricating properties, reducing friction between contacting surfaces. This characteristic makes aluminium paste valuable for applications in bearings, gears, and other mechanical components.
- Thermal Resistance: While not as exceptional as aluminium oxide paste, aluminium paste exhibits moderate thermal resistance due to its metallic nature. This allows its use in applications involving moderate heat exposure, such as engine components and heat sinks.
- Electrical Conductivity: The interconnected network of metallic flakes in aluminium paste readily conducts electricity, rendering it unsuitable for applications requiring electrical insulation. This property, however, finds use in electrical grounding and heat dissipation applications.
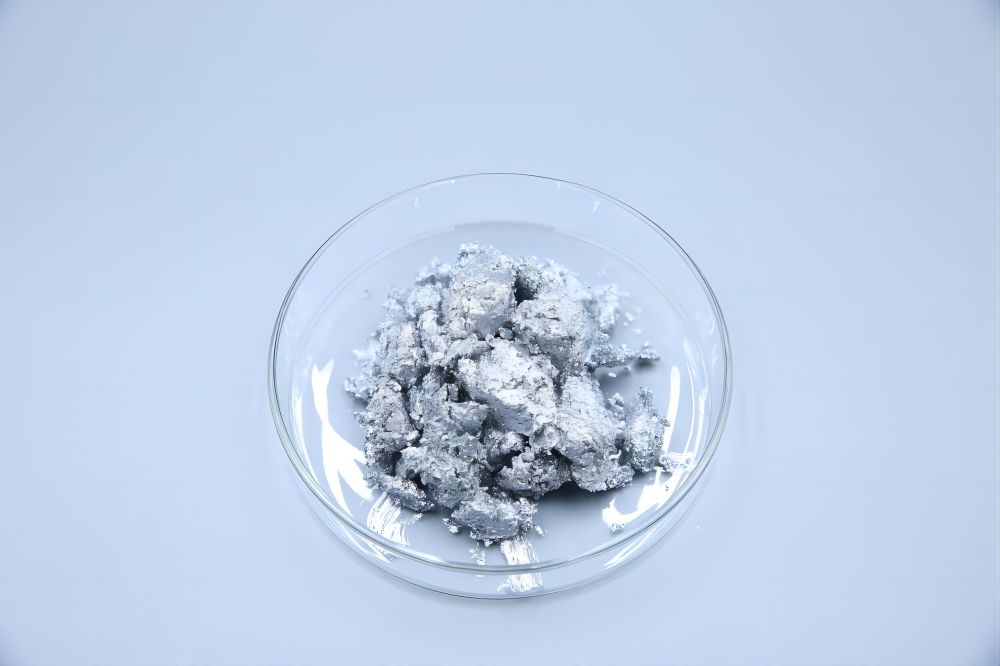
Alumina Paste
- Abrasiveness: The crystalline structure of aluminium oxide, characterized by sharp edges and inherent hardness, facilitates controlled material removal. This abrasive action is tunable based on particle size. Coarser particles offer aggressive abrasion for tasks like paint stripping and metal surface roughening, while finer particles provide gentle polishing suitable for delicate surfaces like gemstones and optical components.
- Thermal Stability: Aluminium oxide paste boasts exceptional thermal stability, surpassing that of aluminium paste. Its high melting point and resistance to thermal degradation make it ideal for high-temperature applications such as furnace linings, refractory coatings, and heat shields.
- Electrical Insulation: Unlike its metallic counterpart, aluminium oxide paste exhibits minimal electrical conductivity due to its non-conductive crystalline lattice. This property makes it a valuable material for electrical insulators in circuit boards, transformers, and other electronic components.
Additional Considerations
- Chemical Resistance: Both materials exhibit varying degrees of resistance to different chemicals. Aluminium paste is generally less resistant to acidic and alkaline environments compared to aluminium oxide paste, which offers superior chemical stability.
- Environmental Impact: The extraction and processing of both aluminium and aluminium oxide can have environmental consequences. Choosing recycled or sustainably sourced materials is crucial for minimizing environmental impact.
Where Aluminium Paste and Aluminium Oxide Paste Excel?
Aluminium Paste
- Reflective Coatings: Leveraging its exceptional light and thermal reflectance, aluminium paste finds extensive use in applications demanding high visibility. This includes traffic signs, safety markers, and roadway markings, where their reflective properties enhance visibility and improve safety conditions, particularly in low-light environments. Additionally, decorative paints and coatings for architectural elements and automotive components often incorporate aluminium paste to achieve a shimmering or metallic aesthetic.
- Thermal Insulation: The inherent thermal resistance of aluminium paste makes it a valuable material for applications requiring insulation and heat dissipation. It is commonly employed in piping systems, industrial vessels, and heat sink components, where its ability to reflect thermal radiation minimizes energy losses and optimizes system efficiency.
- Lubrication: The interlayer spacing between aluminium flakes exhibits lubricating properties, making it suitable for applications involving friction reduction. This includes bearings, gears, and other mechanical components where aluminium paste can minimize wear and tear and extend component lifespan.
- Electrical Grounding and Heat Dissipation: Aluminium paste’s high electrical conductivity makes it suitable for applications where efficient heat dissipation and electrical grounding are crucial. This includes electrical grounding straps and heat sinks for electronic components.
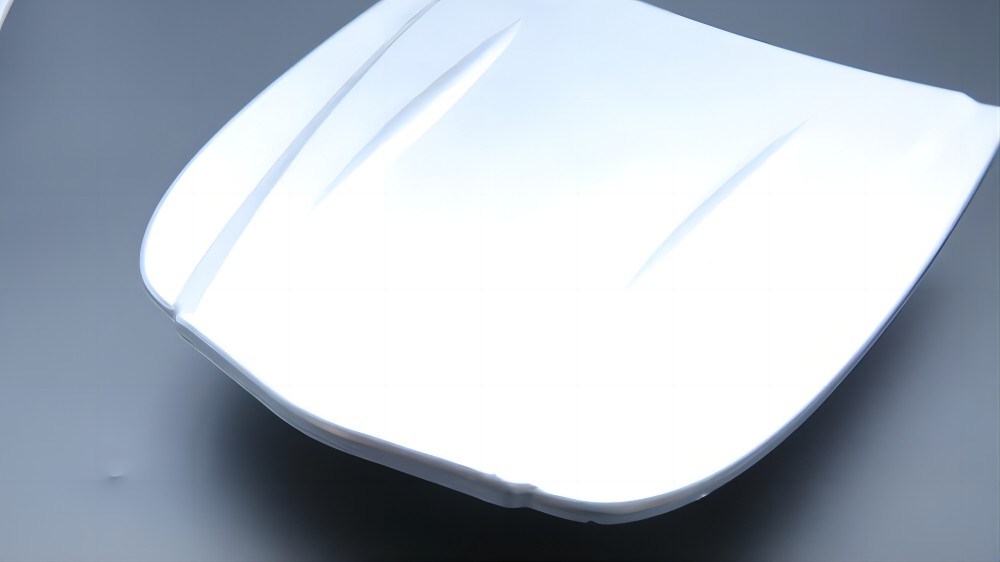
Alumina Paste
- Abrasive Polishing: The controlled abrasiveness of aluminium oxide paste, determined by particle size and distribution, makes it ideal for polishing various materials. Gemstone enthusiasts utilize finer grades to restore the pristine lustre of precious stones, while metalworkers rely on coarser grades for surface roughening and preparation prior to coating or finishing. Additionally, aluminium oxide paste finds application in the electronics industry for polishing circuit board traces and delicate electronic components.
- High-Temperature Applications: Due to its exceptional thermal stability and resistance to degradation at high temperatures, aluminium oxide paste is a preferred material for refractory coatings and furnace linings. These applications demand materials that can withstand extreme heat exposure without compromising structural integrity or performance.
- Electrical Insulation: The non-conductive crystalline structure of aluminium oxide paste makes it a valuable electrical insulator. Circuit boards, transformers, and other electronic components often utilize this material to prevent electrical leakage and ensure safe and efficient operation.
Comparative Analysis of Aluminium Paste and Alumina Paste
To further elucidate the disparities between these two materials, a comparative table summarizing their key attributes is presented:
Feature | Aluminium Paste | Aluminium Oxide Paste |
Composition | Finely ground aluminium particles in a carrier medium | Aluminium oxide (Al2O3) |
Appearance | Shiny, metallic | White or grey |
Reflectivity | High | Low |
Abrasiveness | Low | High |
Thermal Resistance | Moderate | High |
Electrical Conductivity | High | Low (insulator) |
Particle Shape | Flakes | Granules/Spheres |
Main Applications | Reflective coatings, thermal insulation, lubricants | Abrasive polishing, high-temperature coatings, electrical insulation |
Examples of Applications | Traffic signs, decorative paints, heat sinks | Gemstone polishing, metal finishing, circuit board traces, furnace linings |
Key Advantages | High visibility, thermal resistance, lubrication | Controlled abrasion, high-temperature stability, electrical insulation |
Key Limitations | Not electrically insulating, susceptible to some chemicals | Low reflectivity, requires specific processing techniques |
Environmental Impact | Extraction and processing can be energy-intensive | Extraction and processing can generate waste |
Sustainability Considerations | Choose recycled or sustainably sourced materials | Choose recycled or sustainably sourced materials |
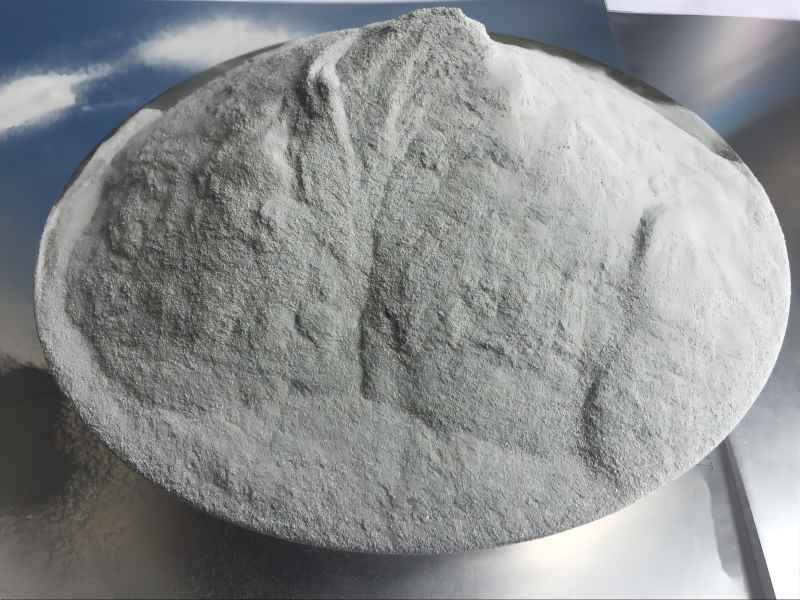
Conclusion
Navigating the diverse world of materials is akin to traversing a labyrinth. While both aluminium paste and aluminium oxide paste appear deceptively similar, their inherent compositions unlock a treasure trove of distinct properties and applications. Aluminium paste, adorned in its metallic cloak, shines brightest in the realm of light and heat management, while aluminium oxide paste, with its crystalline fortitude, reigns supreme in the domain of controlled abrasion and thermal resilience. Ultimately, the optimal choice hinges upon the specific needs of the endeavor. Whether seeking to illuminate the world with dazzling reflectivity or to refine it with meticulous abrasion, understanding the unique strengths and limitations of these materials empowers informed decision-making, paving the way for successful material selection in the ever-evolving tapestry of industrial and scientific endeavors.