The aluminum plastic film is a crucial material in the lithium battery industry chain’s upstream packaging, representing 10-20% of total material cost for pouch batteries.
Compared to other battery materials such as diaphragms, electrolytes, and electrodes, the production technology of aluminum plastic film is more difficult and not yet fully localized in the lithium battery industry.
However, recent technological advancements and production capacity improvements by related enterprises have facilitated the localization of aluminum plastic film.
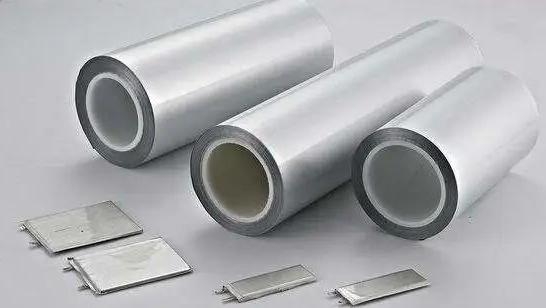
What is Aluminum Plastic Film?
The aluminum plastic composite film, referred to as aluminum plastic film, is a composite flexible packaging shell material used to package lithium-ion batteries and is often used in soft pack batteries and blade batteries.
Sealing the assembled monolithic cells with aluminum plastic film can play an important role in protecting the internal electrodes and isolating the external environment.
Since the material of the packaged cell must resist the swelling, dissolution, and absorption of the electrolyte, and at the same time ensure a strict barrier of oxygen and moisture, the aluminum plastic film must have five characteristics: puncture resistance, high barrier properties, electrolyte resistance, high-temperature resistance, insulation properties, and high cold stamping formability.
The Structure of the Aluminum Plastic Film
The aluminum plastic film must be constructed of three layers of materials held together with adhesives in order for it to have the aforementioned properties. The structure is the outer resistance layer, the barrier layer, and the heat sealing layer from the outside to the inside.
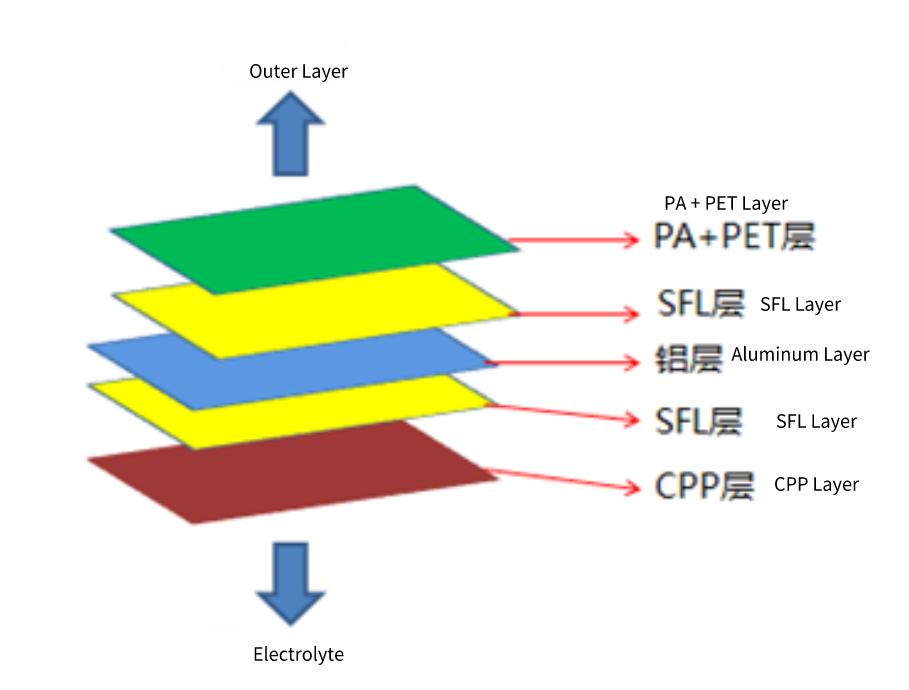
The material of the outer resistance layer is generally nylon, which is required to have the properties of impact resistance, puncture resistance, friction resistance, heat resistance, insulation, etc., to protect the aluminum foil in the middle from being scratched. The outer resistance layer also prevents air penetration, while ensuring that the packaging aluminum foil has good deformability.
The barrier layer is usually composed of aluminum foil, which has good pinhole resistance and double-sided composite property and can be stably formed after processing. Metal aluminum reacts with air at room temperature to form an oxide film, thereby preventing water vapor from penetrating and protecting the internal battery core. This layer is also the main structure of the deep deformation of the aluminum plastic film.
The material of the heat-sealing layer must have good heat-sealing adhesion, insulation, and resistance to electrolyte corrosion, so polypropylene film (CPP) is generally the main material. Its main function is to heat, melt and bond the PP layer during the packaging process, and at the same time prevent the leaked electrolyte from corroding the aluminum foil.
The adhesive compounded by the above three layers of materials has strong electrolyte resistance, high-temperature resistance and aging resistance, and good bonding performance. In general, the substance is a solvent-free polyurethane adhesive or a benzene-free polyurethane adhesive (alcohol-soluble or water-based).
Aluminum Plastic Film Production Process
The mainstream manufacturing process of aluminum plastic film can be divided into the dry method and the thermal method.
The dry process is to directly bond aluminum foil and CPP through an adhesive and then press them together. Since the CPP does not need secondary crystallization after the high temperature in this process, the dry-processed aluminum plastic film has good drawing performance and good appearance. The majority of its applications are high-capacity soft-pack consumer batteries and power batteries due to its excellent anti-short circuit performance. In the dry process, the electrolyte is easy to corrode CPP and reacts with the adhesive, so the requirements for CPP are higher, and better barrier properties are required.
The thermal process is to bond aluminum foil and CPP through modified polyethylene (MPP), and perform thermal synthesis at a certain temperature. The metal aluminum will become more brittle over a prolonged period of high-temperature baking, which will also affect how well the aluminum plastic film can be drawn. However, the aluminum plastic film under the thermal process has good electrolyte and water resistance properties and can be used in consumer batteries with low capacity requirements.
Related Products
Related Articles