Aluminum, renowned for its lightweight, corrosion-resistant, and versatile properties, finds extensive applications across numerous industries. The ability to precisely cut aluminum sheets is crucial for manufacturing components with accurate dimensions and desired shapes. This article delves into the various methods employed for aluminum sheet cutting, their respective advantages and limitations, and the key factors influencing the selection of the most suitable cutting technique.
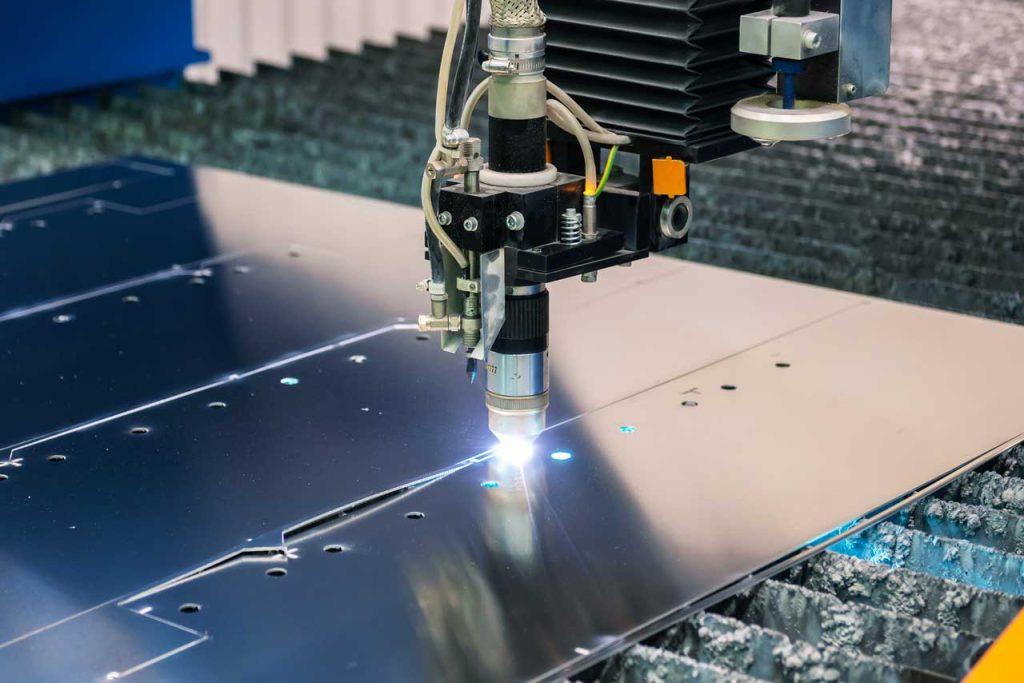
What are the Aluminum Sheet Cutting Methods and Techniques?
1. Laser Aluminum Cutting:
Laser aluminum cutting utilizes a highly focused beam of light, typically from a CO2 or fiber laser, to generate intense heat that melts, vaporizes, or burns away aluminum, resulting in a precise cut. As a non-contact process, it minimizes mechanical stress on the material, reducing distortion and producing a narrow kerf. Advanced laser systems often integrate computer numerical control (CNC), allowing for the creation of intricate and highly accurate designs. While the heat-affected zone remains small, aluminum’s high thermal conductivity must be considered during the process.
Applicable Range:
Laser aluminum cutting is exceptionally well-suited for thin to medium-thickness aluminum sheets, generally up to 20mm. However, the maximum thickness achievable is contingent upon the laser power, beam quality, and the specific alloy of aluminum being processed.
Fiber lasers have shown an increased ability to cut thicker aluminum when compared to CO2 lasers.
Advantages:
- High Precision: Laser aluminum cutting delivers exceptional accuracy and repeatability, making it ideal for intricate designs and tight tolerances.
- Smooth Edges: The process produces clean, smooth edges, minimizing the need for secondary finishing operations.
- Minimal Material Waste: The narrow kerf and precise control reduce material waste, optimizing resource utilization.
- High Speed: Laser aluminum cutting can be very fast for thinner materials.
Limitations:
- High Initial Investment: Laser aluminum cutting systems require a significant upfront investment.
- Thickness Limitations: While capable of cutting medium-thickness sheets, laser aluminum cutting may struggle with very thick aluminum, particularly without very high powered lasers.
- Reflectivity: Aluminum’s reflectivity can pose challenges, requiring higher laser power and careful parameter optimization.
2. Plasma Aluminum Cutting:
Plasma aluminum cutting employs a high-temperature ionized gas stream, or plasma, to melt and remove material. This plasma is created by forcing a gas, such as compressed air or nitrogen, through a constricted nozzle while applying an electrical arc. The intense heat rapidly melts the aluminum, while the high-velocity gas jet expels the molten material. Known for its effectiveness in cutting electrically conductive materials, plasma aluminum cutting offers a fast and efficient method for processing aluminum and other metals.
Applicable Range:
Plasma aluminum cutting is a versatile method capable of handling a broad range of aluminum thicknesses, making it suitable for medium to thick sheets. It is often favored for applications where high cutting speed and cost-effectiveness are paramount.
Advantages:
- High Cutting Speed: Plasma aluminum cutting offers rapid cutting speeds, particularly for thicker materials.
- Lower Cost: Compared to laser aluminum cutting, plasma aluminum cutting systems typically have lower initial and operating costs.
- Thick Material Capability: Plasma aluminum cutting can effectively cut thicker aluminum sheets.
Limitations:
- Lower Precision: Plasma aluminum cutting generally provides lower precision compared to laser cutting.
- Wider Heat-Affected Zone: The process produces a wider heat-affected zone, potentially leading to material distortion.
- Rougher Edges: The cut edges may be rougher and require secondary finishing.
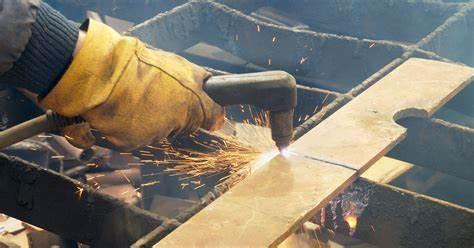
3. Waterjet Cutting:
Waterjet cutting uses a high-pressure stream of water, often mixed with abrasive particles like garnet, to erode and cut materials with precision. The water is forced through a small nozzle, creating a powerful and focused jet capable of cutting aluminum effectively. Abrasive waterjet cutting is commonly employed for aluminum to enhance cutting power. As a cold cutting process, it eliminates the risk of a heat-affected zone, preserving the material’s structural integrity.
Applicable Range:
Waterjet cutting is exceptionally versatile, capable of cutting aluminum sheets of virtually any thickness, including very thick plates.
It is especially valuable when heat distortion or material property changes must be avoided.
Advantages:
- No Heat-Affected Zone: Waterjet cutting is a cold-cutting process, eliminating heat-induced distortion and preserving material properties.
- Complex Shape Capability: The process can create intricate shapes and complex contours with high precision.
- Versatility: Capable of cutting many different materials.
Limitations:
- Slower Cutting Speeds: Waterjet cutting typically has slower cutting speeds compared to laser and plasma cutting.
- Higher Operating Costs: The process requires high-pressure water pumps and abrasive materials, leading to higher operating costs.
4. Saw Cutting:
Saw cutting utilizes a toothed blade, usually made of high-speed steel or carbide, to mechanically remove material. Depending on the application, different types of saws, such as circular saws, band saws, and reciprocating saws, are used. As a simple and well-established cutting method, it remains a reliable choice for various material processing needs.
Applicable Range:
Saw cutting is suitable for cutting aluminum sheets of various thicknesses, particularly for straight cuts and simple shapes. It is often used for rough cutting or when high precision is not required.
Advantages:
- Lower Equipment Costs: Saw cutting equipment is generally less expensive than laser or plasma cutting systems.
- Thick Material Capability: Saw cutting can effectively cut thick aluminum sheets.
Limitations:
- Lower Precision: Saw cutting typically provides lower precision compared to other methods.
- Potential for Burrs: The process can produce burrs or rough edges, requiring secondary finishing.
- Slower Cutting Speeds: Saw cutting is generally slower than laser or plasma cutting.
5. CNC Milling:
CNC milling is a subtractive manufacturing process that uses a rotating cutting tool, guided by computer numerical control (CNC), to remove material from an aluminum sheet. With the ability to move in multiple axes, the cutting tool allows for the creation of complex 3D shapes and intricate designs with high precision.
Applicable Range:
CNC milling is highly versatile and can be used on many different thicknesses of aluminum. It is particularly well-suited for applications requiring high precision and complex 3D shapes.
Advantages:
- Very High Precision: CNC milling delivers exceptional accuracy and repeatability.
- Complex 3D Shape Capability: The process can create highly complex 3D shapes and intricate designs.
Limitations:
- Slower Process: CNC milling is generally slower than other cutting methods.
- High Equipment Costs: CNC milling machines are expensive.
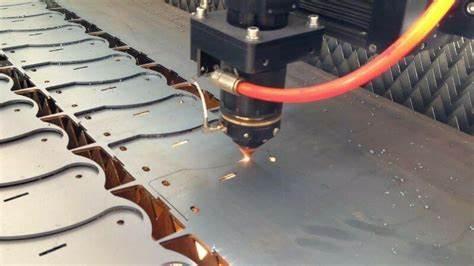
Optimal Methods for Cutting Different Aluminum Thicknesses
Selecting the right cutting method for aluminum is crucial to achieving precise results while minimizing waste, heat distortion, and machining time. The best cutting technique depends on the thickness of the aluminum being processed. Below are the optimal methods categorized by aluminum thickness:
Thin Aluminum Sheets (Less than 3mm)
For aluminum sheets in this range, precision and edge quality are top priorities. The following methods are optimal:
- Laser Aluminum Cutting: This method provides exceptional accuracy, producing smooth and clean edges with minimal burring. It is highly efficient for intricate designs and complex cuts.
- High-Speed Saw Cutting: A cost-effective solution for straight cuts, particularly when working with large batches. Carbide-tipped saw blades enhance efficiency and prolong tool life.
Medium-Thickness Aluminum Sheets (3mm – 20mm)
For medium-thickness aluminum, a balance between speed, precision, and cost-effectiveness is essential. Recommended techniques include:
- Plasma Aluminum Cutting: A fast and economical method capable of cutting through aluminum efficiently. While it may introduce slight heat distortion, it remains a popular choice for industrial applications.
- CNC Milling: When precision is paramount, CNC milling is ideal. It ensures high accuracy, smooth finishes, and tight tolerances, making it suitable for applications requiring fine details or complex geometries.
Thick Aluminum Sheets (Greater than 20mm)
When dealing with thick aluminum plates, cutting methods must minimize material stress and heat effects. The most effective options are:
- Waterjet Cutting: The preferred method for thick aluminum sheets, as it eliminates heat-related distortions while providing highly precise cuts. Waterjet cutting can handle exceptionally thick plates without compromising edge quality.
- Plasma Aluminum Cutting: While plasma cutting is still viable for thick aluminum, it generates significant heat, which can lead to distortion and hardened edges. Proper cooling techniques and post-processing may be required.
By selecting the appropriate cutting method based on aluminum thickness, manufacturers can optimize efficiency, reduce material waste, and ensure high-quality results.
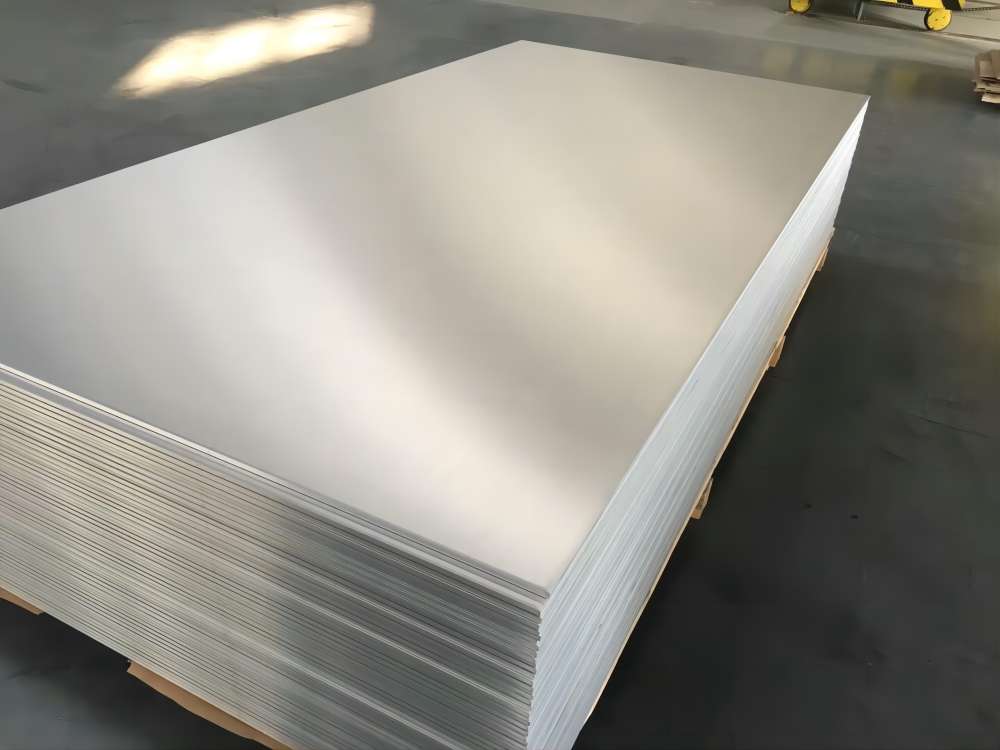
Applications of Aluminum Sheet Cutting in Various Industries
Different cutting methods are employed based on industry-specific requirements, such as precision, efficiency, and cost-effectiveness. Below are key industries that rely on aluminum sheet cutting and the preferred cutting techniques used in each sector.
1. Aerospace Industry
The aerospace industry demands the highest levels of precision and performance when it comes to aluminum sheet cutting.
Applications in Aerospace:
- Fuselage Panels & Wing Structures: Large aluminum sheets are cut into precise shapes to form the skin of aircraft, which requires smooth edges and minimal thermal distortion.
- Interior Components: Lightweight aluminum panels are used for cabin partitions, seats, and overhead storage compartments.
- Engine Components & Heat Shields: High-temperature-resistant aluminum alloys are used in specific engine parts and shielding systems.
Preferred Cutting Methods:
- CNC Milling: Used for machining intricate aerospace-grade aluminum components that require extreme precision. This method ensures smooth surfaces and allows for complex geometries.
- Laser Aluminum Cutting: Suitable for cutting thin aluminum sheets used in aircraft skins, offering fast processing speeds with minimal material wastage.
- Waterjet Cutting: Ideal for cutting thick aerospace-grade aluminum without causing thermal stress, ensuring the integrity of high-performance components.
2. Automotive Manufacturing
Aluminum is increasingly used in the automotive sector due to its lightweight nature, which helps improve fuel efficiency and reduce carbon emissions.
Applications in Automotive Manufacturing:
- Body Panels & Structural Parts: Lightweight aluminum panels contribute to vehicle weight reduction while maintaining strength and crash resistance.
- Engine Components: Aluminum sheets are used in the production of cylinder heads, transmission cases, and intake manifolds due to their excellent heat dissipation properties.
- Heat Shields & Exhaust Systems: High-temperature-resistant aluminum sheets are used for heat shields that protect surrounding components from engine heat.
Preferred Cutting Methods:
- Laser Aluminum Cutting: Ideal for precision-cutting body panels and trim pieces with smooth edges and minimal finishing requirements.
- Plasma Aluminum Cutting: Used for cutting thicker aluminum sheets in structural components, providing faster cutting speeds and cost-effectiveness.
- Waterjet Cutting: Used when high precision and no heat-affected zones are required, especially in sensitive automotive parts.
3. Construction and Architecture
Aluminum is extensively used in modern construction and architectural applications due to its aesthetic appeal, durability, and resistance to corrosion.
Applications in Construction & Architecture:
- Building Facades & Cladding Panels: Aluminum composite panels (ACPs) are widely used for exterior cladding due to their lightweight nature and corrosion resistance.
- Roofing & Structural Elements: Aluminum roofing panels are durable and often preferred in commercial and residential buildings.
- Decorative & Interior Panels: Aluminum sheets are used in ceilings, staircases, signage, and wall panels for modern architectural designs.
Preferred Cutting Methods:
- Saw Cutting: Commonly used for bulk cutting of aluminum sheets for large-scale construction projects.
- Waterjet Cutting: Ideal for intricate architectural designs where precision and material integrity are required.
- Laser Aluminum Cutting: Used for cutting decorative elements, signage, and panels that require clean and precise cuts.
4. Electronics and Medical Equipment
Applications in Electronics & Medical Equipment:
- Electronic Enclosures & Casings: Used in laptops, smartphones, and communication devices for heat dissipation and lightweight protection.
- Heat Sinks & Circuit Boards: Aluminum sheets are widely used in electronics for heat management in power supplies and LED lighting systems.
- Medical Equipment Frames & Components: Many medical devices, such as imaging equipment, hospital furniture, and surgical tools, use aluminum for its corrosion resistance and ease of sterilization.
Preferred Cutting Methods:
- CNC Milling: The preferred method for machining high-precision aluminum components for medical and electronic devices.
- Laser Aluminum Cutting: Used for cutting intricate patterns and small parts with high accuracy.
- Waterjet Cutting: Ensures precision cutting for sensitive components without affecting material properties.
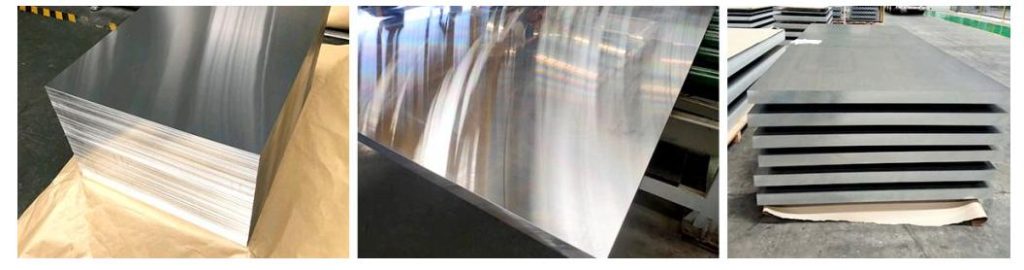
Key Material Characteristics to Consider During Aluminum Sheet Cutting
When cutting aluminum sheets, understanding the material’s unique properties is essential for selecting the best cutting method and achieving optimal results. The table below summarizes the primary challenges and solutions that should be considered to enhance efficiency, precision, and overall cut quality.
Material Characteristic | Challenges in Cutting | Solutions & Best Practices |
High Thermal Conductivity (Aluminum dissipates heat quickly, affecting cutting efficiency in thermal-based methods) | – Rapid heat dissipation: Reduces efficiency in laser and plasma cutting. | – Use optimized power settings: Adjust laser/plasma cutting parameters for better heat control. |
– Inconsistent cutting quality: Uneven heat distribution may lead to rough edges, especially in thick sheets. | – Apply cooling techniques: Water-based cutting fluids in CNC machining help dissipate heat effectively. | |
– Risk of material warping: Thin aluminum sheets may deform due to localized heating. | – Use multiple passes: For thick sheets, lowering feed rates and making multiple cutting passes prevent overheating. | |
High Reflectivity (Aluminum reflects a large portion of laser energy, making laser cutting less efficient and increasing the risk of equipment damage.) | – Reduced energy absorption: Laser beams may not effectively penetrate aluminum. | – Use fiber lasers instead of CO₂ lasers: Fiber lasers have better absorption rates for aluminum. |
– Risk of back-reflection: Reflected laser beams can damage optical components. | – Apply anti-reflective coatings: Coating aluminum surfaces with black oxide or similar materials enhances laser efficiency. | |
– Limited effectiveness on thick sheets: The higher the thickness, the greater the reflectivity, requiring more powerful lasers. | – Pre-etching techniques: Creating a rougher surface through light engraving before laser cutting can improve absorption. | |
Softness and Burr Formation (Aluminum’s ductility causes burr formation and tool wear in mechanical cutting processes.) | – Burr formation: Saw cutting and CNC milling often leave rough edges requiring additional finishing. | – Use carbide-tipped or coated tools: Reduces wear and prevents aluminum buildup on cutting edges. |
– Material adhesion to tools: Aluminum chips may stick to cutting tools, reducing tool life. | – Implement deburring processes: Sanding, tumbling, or chemical deburring smooths rough edges. | |
– Reduced edge quality in plasma and waterjet cutting: Rough edges may require extra post-processing. | – Opt for high-pressure waterjet cutting: Produces clean, burr-free cuts, reducing the need for post-processing. | |
Oxidation Layer Effects (Aluminum naturally forms an oxide layer, which can interfere with cutting methods.) | – Higher melting point of oxide layer: Requires more power in laser and plasma cutting. | – Pre-treat aluminum sheets: Use mechanical brushing or chemical etching to remove the oxide layer before cutting. |
– Increased tool wear in CNC machining: The hard oxide layer can damage cutting tools. | – Adjust laser parameters: Using high-power lasers with oxygen assist gas improves oxide layer penetration. | |
– Surface contamination issues: The oxide layer can affect welding or post-processing treatments. | – Select coated carbide tools: Reduces tool wear when cutting through oxidized aluminum surfaces. |
Aluminum sheet cutting is a critical process across diverse industries, requiring careful consideration of various factors. The selection of the optimal cutting method depends on the aluminum thickness, desired precision, production volume, and cost considerations. As technology advances, we can expect further developments in aluminum sheet cutting techniques, leading to increased efficiency, precision, and sustainability.