Aluminum Sheet 5052 stands as a cornerstone in the realm of materials, celebrated for its exceptional qualities in diverse applications. Within the 5052 alloy family, two key tempers, H32 and H34, emerge with distinct characteristics that play a pivotal role in shaping their applications. In this comprehensive comparative analysis, we embark on a journey to unravel the intricacies of 5052 H32 and 5052 H34, shedding light on their shared attributes and key differences. As we navigate through the mechanical nuances, formability factors, and real-world applications, the aim is to empower decision-makers with the knowledge needed to choose the right temper for their specific project requirements.
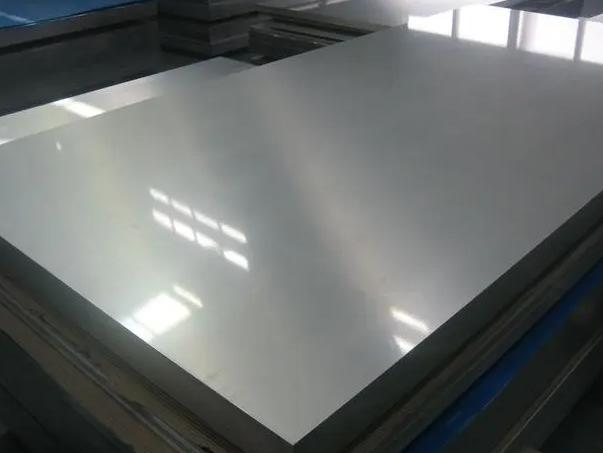
Similarities of 5052 H32 and 5052 H34 Aluminum Sheets
5052 H32 and 5052 H34 are two temper designations for aluminum alloy 5052. Despite having some differences in mechanical properties, they share several similarities, making them both popular choices in various applications. Here are the key similarities of 5052 H32 and 5052 H34 aluminum sheets:
- Chemical Composition:
Both H32 and H34 tempers are primarily composed of aluminum alloy 5052. This composition provides a solid foundation for their mechanical and corrosion-resistant properties.
- Corrosion Resistance:
One of the notable similarities is their excellent corrosion resistance. Both H32 and H34 exhibit a high resistance to corrosion, making them suitable for applications in environments with exposure to moisture and other corrosive elements.
- Weldability:
Both tempers are highly weldable. Their weldability allows for various fabrication processes, providing flexibility in manufacturing and construction applications.
- Recyclability:
Both 5052 H32 and 5052 H34 aluminum sheets are environmentally friendly due to their recyclability. Recycling these alloys doesn’t compromise their fundamental properties, contributing to sustainable practices.
These shared characteristics make 5052 H32 and 5052 H34 aluminum sheets versatile materials for a range of industries, including construction, marine, automotive, and general manufacturing. Understanding these similarities is essential when considering which temper is most suitable for specific applications based on other distinguishing factors like mechanical properties and formability.
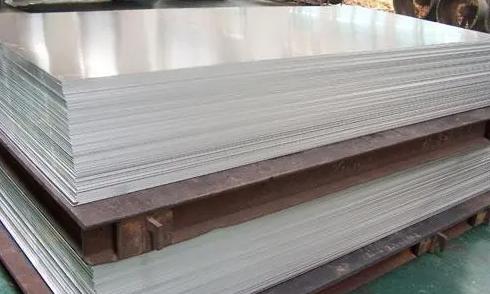
Key Differences of 5052 H32 vs 5052 H34 Aluminum Sheets
The key differences between 5052 H32 and 5052 H34 aluminum sheets lie in their mechanical properties, tempering processes, and specific applications. Here are the primary distinctions:
1. Mechanical Properties:
- Tensile Strength: 5052 H34 generally has higher tensile strength compared to 5052 H32. H34 undergoes a more extensive cold working process, resulting in increased strength.
- Yield Strength: Similar to tensile strength, 5052 H34 typically exhibits higher yield strength than 5052 H32.
- Elongation: 5052 H32 tends to have higher elongation values, indicating better formability. H34, due to its increased strength, may have slightly lower elongation.
2. Hardness and Tempering:
The designations “H32” and “H34” refer to the tempering processes applied to the aluminum sheets.
- H32 (Quarter Hard): This temper is strain-hardened and stabilized, providing good formability while maintaining a certain level of strength.
- H34 (Stabilized): This temper involves a higher degree of strain hardening, resulting in increased strength and hardness compared to H32.
3. Formability:
- 5052 H32: Known for its excellent formability, making it suitable for applications where shaping and bending are critical, such as in construction and architectural uses.
- 5052 H34: While still formable, it may be less malleable than H32 due to its higher level of strain hardening. It is often chosen for applications requiring increased strength and resistance.
4. Machinability:
Both tempers are generally considered to have good machinability. However, due to the increased hardness of H34, it may present some challenges in certain machining processes compared to H32.
5. Applications:
- 5052 H32: Commonly used in applications where formability and ease of fabrication are crucial, such as in building panels, automotive components, and general sheet metal work.
- 5052 H34: Preferred in applications requiring higher strength and resistance to environmental factors, making it suitable for marine components, shipbuilding, and other demanding environments.
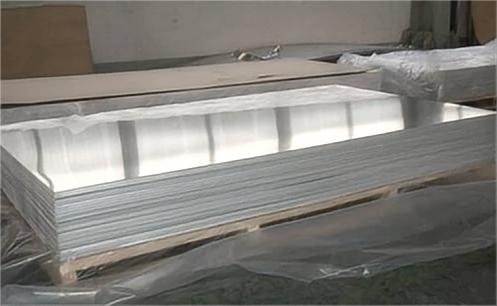
The following table summarizes the key distinctions between 5052 H32 and 5052 H34 aluminum sheets in various properties and applications.
Properties | 5052 H32 | 5052 H34 |
Tensile Strength | Lower | Higher |
Yield Strength | Lower | Higher |
Elongation | Higher (better formability) | Slightly Lower |
Hardness | Moderate | Higher |
Tempering Process | Strain-hardened and stabilized | More extensive strain hardening |
Formability | Excellent | Good, but less than H32 |
Machinability | Generally good | Good, but may present some challenges |
Applications | Building panels, automotive components, general sheet metal work | Marine components, shipbuilding, applications requiring higher strength and resistance |
Understanding these key differences allows engineers and manufacturers to choose the most appropriate temper for specific applications based on the desired combination of mechanical properties and performance characteristics.
How to Choose the Right Material between 5052 H32 and 5052 H34 Aluminum Sheets?
Choosing the right material between 5052 H32 and 5052 H34 aluminum sheets depends on various factors related to your specific project requirements. Here’s a step-by-step guide to help you make an informed decision:
- Understand Project Requirements:
Clearly define the requirements of your project, including mechanical properties, formability, and environmental conditions.
- Consider Mechanical Properties:
Evaluate the mechanical properties needed for your application, such as tensile strength, yield strength, and elongation. If higher strength is crucial, H34 may be preferred.
- Assess Formability Needs:
If your project involves extensive forming, bending, or shaping, consider the excellent formability of 5052 H32. For applications with less formability requirements and a focus on strength, H34 may be suitable.
- Evaluate Environmental Factors:
Consider the environmental conditions your material will be exposed to. If your project involves marine or harsh environments, where increased strength and corrosion resistance are critical, H34 may be the better choice.
- Review Machinability Requirements:
Assess the machining processes involved in your project. If machinability is a key factor, both H32 and H34 generally offer good machinability, but H32 may be slightly easier to machine.
- Perform Cost Analysis:
Consider the cost implications of each temper. Evaluate whether the potential increase in performance or specific properties justifies any additional costs associated with choosing H34.
- Seek Expert Advice:
Consult with material experts, engineers, or suppliers who specialize in aluminum alloys. They can provide guidance based on their experience and knowledge of the material properties. A trusted supplier contributes to the overall success of your project.
By systematically considering these factors, you can make an informed decision between 5052 H32 and 5052 H34 aluminum sheets, aligning the material properties with the specific requirements of your project.
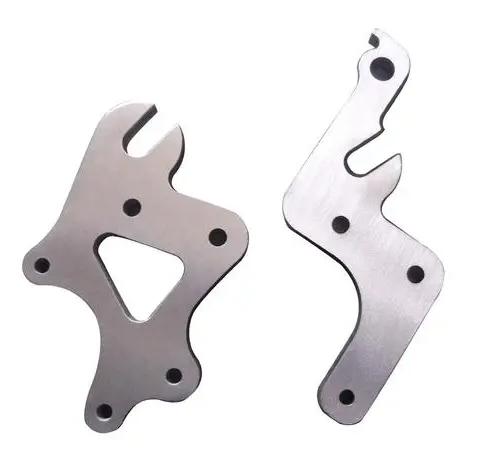
Conclusion
In the realm of aluminum alloys, the comparative analysis between 5052 H32 and 5052 H34 has revealed a nuanced landscape of properties and applications. As we conclude this exploration, it becomes evident that the choice between these tempers is not merely a technical decision but a strategic one, aligning the material characteristics with the demands of the project at hand.
For those embarking on endeavors where precision, strength, and corrosion resistance are paramount, 5052 H32 emerges as a stalwart choice. Conversely, in marine applications where resilience against harsh environmental conditions is crucial, 5052 H34 stands resilient.
In making this decision, access to quality materials becomes paramount. Therefore, we recommend partnering with a reputable 5052 aluminum sheet supplier. The right supplier ensures that the chosen alloy not only meets industry standards but exceeds expectations in performance and reliability. So, whether it’s for construction, marine engineering, or any other application, choosing a reliable 5052 aluminum sheet supplier is the final key to unlocking the full potential of these versatile alloys.