Aluminum stamping parts are widely used in the aerospace industry due to their excellent properties such as lightweight, high strength, and corrosion resistance. Here we will talk about some of the common aerospace use aluminum stamping parts and the cost affected factors.
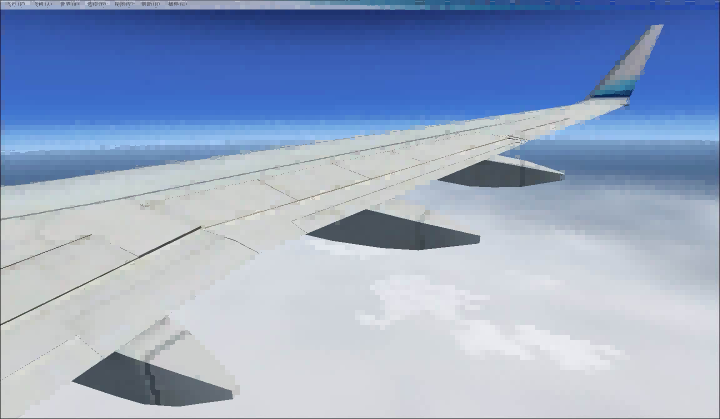
What are the Aluminum stamping parts of aerospace components?
Structural Components: Aluminum stamping parts are commonly used in the production of structural components such as wing panels, fuselage sections, and landing gear. The lightweight nature of aluminum helps to improve aircraft performance and fuel efficiency. The high strength character of aluminum stamping parts are designed to provide strength, durability, and stability to the aircraft.
Interior Components: Aluminum stamping parts are used in the production of interior components such as seat frames, Cabin partitions, Air conditioning ducts, cabinetry, and Lavatory components. The aluminum stamping parts are designed to be lightweight and strong, while also providing comfort and safety for passengers. Aluminum cabin partitions also can provide structural support. When aluminum stamping parts are used to create air conditioning ducts, It even can withstand the high temperatures and pressures involved in air conditioning systems. It is durable and easy to maintain and clean.
Engine Components: Aluminum stamping parts are used in the production of engine components such as engine mounts, turbine blades, Exhaust systems(such as exhaust cones and exhaust nozzles), Fuel system components(such as fuel tanks and fuel lines). The high strength and corrosion-resistant nature of aluminum make it ideal for use in harsh engine environments.
Avionics Components: Aluminum stamping parts are used in the production of avionics components such as instrument panels, antenna brackets, radar equipment(such as radar domes and mounting brackets), electrical components(such as circuit boards and connectors), and even the communication equipment is mounted on aluminum stamping parts. The excellent electromagnetic shielding properties of aluminum make it ideal for protecting sensitive electronic equipment from interference.
Overall, the versatility of aluminum stamping parts makes them ideal for various aerospace applications, from structural components to avionics and engine components etc. But you know the cost of aluminum stamping parts in the aerospace industry will be affected by a number of factors, perhaps some are as follows.
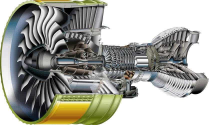
What factors affected the cost of Aluminum stamping parts in aerospace industry?
Material cost: The cost of the aluminum material used to make the stamping parts can vary based on factors such as the grade of aluminum, the quantity purchased, and the supplier(If you choose CHAL, we will give you a reasonable price with high quality). Higher grade aluminum alloys may be more expensive, but they can provide better strength, durability, and corrosion resistance.
Production volume: The volume of aluminum stamping parts being produced can also affect the cost. Larger production runs can often result in lower per-part costs due to economies of scale, while smaller production runs may be more expensive per part.
Tooling costs: The cost of tooling, such as dies and molds, can be a significant expense in the production of aluminum stamping parts. Tooling costs can vary based on factors such as the complexity of the part, the number of pieces required, and the type of tooling required.
Design complexity: The complexity of the design of the aluminum stamping parts can also impact the cost. Parts with intricate shapes, curves, or features may require more complex tooling or additional production steps, which will increase the cost.
Surface finish: The surface finish of the aluminum stamping parts can also affect the cost. Parts that require a high-quality finish, such as polishing or painting, may require additional processing steps that will increase the cost.
Quality requirements: The quality requirements of the aluminum stamping parts can also impact the cost. Parts that require tighter tolerances, higher strength, or special features may require additional processing or inspection steps so that increase the cost.
Industry regulations: Aerospace industry regulations can also impact the cost of aluminum stamping parts. Parts that must meet strict regulatory standards may require additional testing or certification, which will increase the cost.
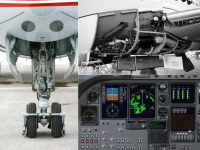
In conclusion, aluminum stamping parts are widely used in the aerospace industry due to their excellent properties such as lightweight, high strength, and corrosion resistance. If you choose CHAL to be your supplier, we can temper aluminum to different hardnesses, improving strength, stability, and wear of the aluminum stamping parts. Besides, our aluminum stamping parts accept a variety of finishes and coatings, such as chem-film, paint, and powder coating, which can increase its corrosion resistance, and thermal and electrical properties. So you do not worry about the quality of our products. Despite the cost challenges, the use of aluminum stamping parts in the aerospace industry is likely to continue due to their unique properties and benefits for aircraft performance, fuel efficiency, and safety.
Related Products
Related Articles