Aluminum tube is a hollow, elongated section of aluminum, typically manufactured in round, square, rectangular, or oval shapes, and widely used in various industries. Renowned for its lightweight yet robust properties, aluminum tubing finds applications in everything from furniture and bicycle frames to construction and aerospace components. This guide delves into the world of aluminum tubing, specifically focusing on understanding sizes, selecting the right type for your needs, and exploring its diverse applications.
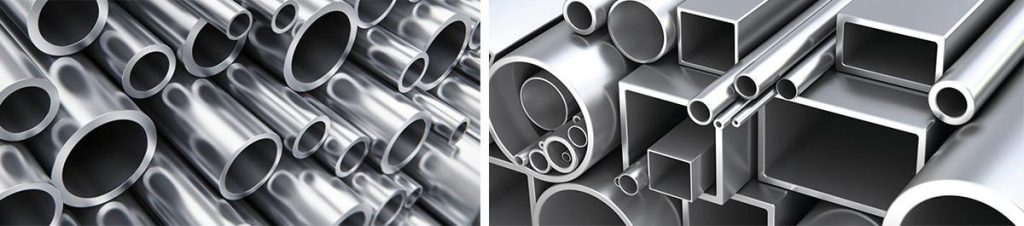
Understanding Aluminum Tube Sizes
Understanding the different size designations of aluminum tubing is crucial for selecting the appropriate material for your project. Two key measurements define the size of an aluminum tube: diameter and wall thickness.
1. Diameter and Wall Thickness
The diameter refers to the distance across the interior of the tube, measured in inches or millimeters. For instance, a 1-inch diameter aluminum tube has an internal width of 1 inch.
Wall thickness, on the other hand, signifies the distance between the inner and outer walls of the tube. It’s also commonly expressed in inches or millimeters. So, a 1-inch diameter aluminum tube with a 1/4-inch wall thickness would have an outer diameter of 1.5 inches (1-inch diameter + 1/4 inch wall thickness on each side).
Common size ranges for aluminum tubing vary depending on the application and desired properties. Here are some examples as follows:
1-inch diameter tubing: This size offers a good balance between strength and weight, making it suitable for a wide range of applications.
Wall thickness:
- 1/2-inch wall thickness increases the strength of the tubing, making it ideal for heavy-duty applications requiring exceptional load-bearing capacity. Examples include industrial equipment supports, lifting equipment components, and custom-built roll cages for off-road vehicles.
- 1/4-inch wall thickness provides a robust structure for applications demanding higher load-bearing capacity, such as furniture frames or bike frames.
- 1/8-inch wall thickness creates a lighter weight option, often used in applications where weight reduction is crucial, such as electrical conduits or handrails.
The size of the tubing significantly impacts its properties. A thicker wall translates to increased strength and load-bearing capacity but also adds weight. Conversely, thinner walls provide a lighter weight solution but may compromise strength. Selecting the optimal size requires careful consideration of the application’s specific requirements.
2. Standard vs. Custom Sizes
Aluminum tubing comes in a wide variety of standard sizes and is readily available from distributors. These standard sizes cater to the most common applications and offer several advantages:
- Cost-effectiveness: Manufacturing standardized sizes allow for economies of scale, making them more affordable than custom sizes.
- Availability: Standard sizes are readily available from various suppliers, ensuring quicker turnaround times for your project.
However, there are situations where standard sizes might not be ideal. For instance, a project might require a specific diameter or wall thickness that is not readily available in standard options. In such cases, custom tubing can be produced, although it typically comes with a higher cost and longer lead time.
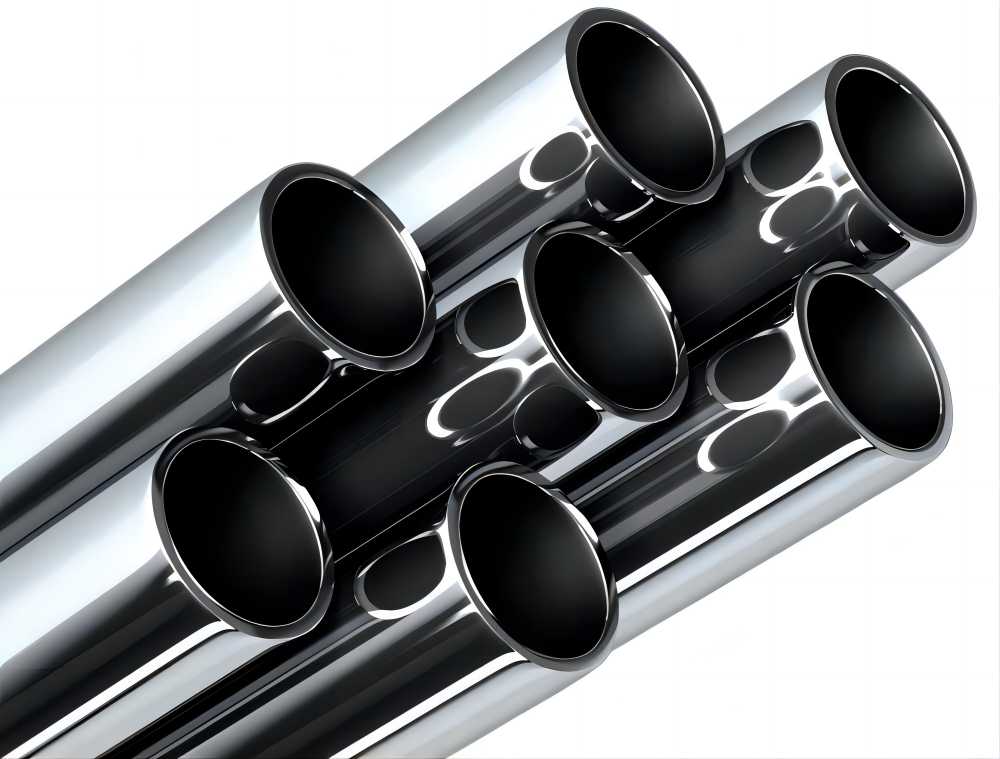
Selecting the Right Aluminum Tube
Choosing the appropriate aluminum tube for your project requires careful consideration of several factors:
1. Factors to Consider
- Application requirements: Identify the primary function of the tubing in your project. Will it be used for structural support, fluid flow, or something else? Understanding the application’s demands helps determine the required strength, weight limitations, and other crucial properties.
- Material properties: Aluminum comes in various alloys, each offering distinct properties in terms of strength, corrosion resistance, and workability. Selecting the right alloy ensures the tubing possesses the necessary characteristics for your project’s needs. We’ll delve into common aluminum alloys used in tubing later in this guide.
- Joining methods: Consider how you plan to connect the tubing to other components in your project. Common joining methods for aluminum tubing include welding, brazing, and mechanical fasteners. The chosen method might influence the selection of tubing material and wall thickness.
- Cost considerations: Aluminum tubing prices vary depending on size, alloy, and wall thickness. Balancing costs with the required properties is essential for a successful project.
2. Common Aluminum Alloys for Tubing
Several aluminum alloys are well-suited for tubing applications. Here’s a closer look at some commonly used alloys:
- 6061 Aluminum: This versatile alloy offers a good balance between strength, weight, and corrosion resistance. It’s readily weldable and often used in general-purpose structural applications. A 1-inch diameter 6061 aluminum tube with a 1/4-inch wall thickness is a popular choice for furniture frames, bike frames, and various industrial structures due to its ability to handle moderate loads without excessive weight.
- 6061-T6 Aluminum: This is a heat-treated version of the versatile 6061 alloy. The heat treatment process (designated by the “T6” temper) significantly enhances the strength of the material compared to the non-heat-treated version. A 1-inch diameter 6061-T6 aluminum tube with a 1/2-inch wall thickness becomes a robust option for applications demanding high load-bearing capacity. While heavier than thinner-walled tubes, it can handle substantial weight without compromising structural integrity. This makes it suitable for heavy-duty furniture frames, industrial equipment supports, and even some structural components in construction (depending on specific load requirements and building codes).
- 6063 Aluminum: This alloy boasts superior strength compared to 6061 while maintaining good corrosion resistance and weldability. It’s often used in applications requiring higher load-bearing capacity, such as heavy-duty furniture, truck components, and industrial machinery. While not as common as 6061 in 1-inch diameter aluminum tube, it can be a suitable option for projects needing extra strength in this size with a 1/4-inch wall thickness.
- 5052 Aluminum: This alloy prioritizes excellent corrosion resistance and workability. It’s not the strongest option but it finds applications in environments prone to corrosion, such as marine applications, food processing equipment, and outdoor signage. 1-inch diameter 5052 aluminum tube with a 1/8-inch wall thickness might be suitable for handrails or lightweight structural components in non-demanding environments.
- 7075 Aluminum: This alloy prioritizes strength and is often used in aerospace applications. It offers superior strength compared to 6061, even without heat treatment. However, it’s also less weldable and more susceptible to corrosion. A 1-inch diameter 7075 aluminum tube with a 1/2-inch wall thickness is ideal for projects requiring exceptional strength, such as heavy machinery components, lifting equipment, or even custom-built roll cages for off-road vehicles. Due to the focus on strength, weight might be a consideration, and alternative materials or designs might be explored for weight-sensitive applications.
It’s important to note that these are just a few examples, and numerous other aluminum alloys cater to specific needs. Consulting with a qualified aluminum tube supplier can help you identify the optimal alloy for your project based on the required strength, corrosion resistance, and other factors.
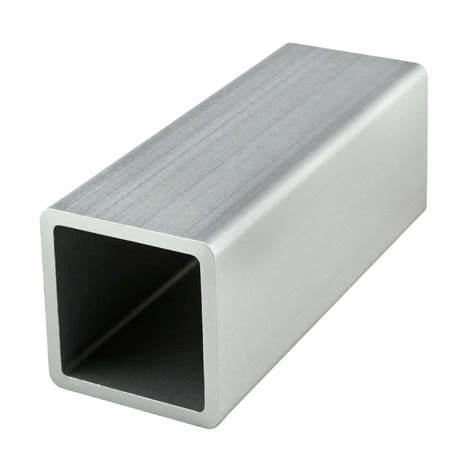
Applications of Aluminum Tubing
The versatility of aluminum tubing extends across numerous industries. Let’s explore some applications categorized by size and wall thickness as follows:
- 1-inch diameter aluminum tube with 1/2-inch wall thickness: This size offers exceptional strength due to its thick wall, making it ideal for applications requiring high load-bearing capacity. Here are some examples:
- Heavy-duty furniture frames: Industrial workbenches and machinery stand that need to support significant weight can benefit from the strength offered by a 1-inch diameter aluminum tube with a 1/2-inch wall thickness.
- Industrial equipment supports: In factories and workshops, this size tubing can be used to create supports for various industrial machinery.
- Lifting equipment components: Some components of lifting equipment, such as lifting arms or support structures, can utilize this size tubing due to its high strength-to-weight ratio.
- Custom-built roll cages for off-road vehicles: A 1-inch diameter aluminum tube with a 1/2-inch wall thickness can provide exceptional protection. The thick wall ensures the roll cage can withstand significant impact forces, enhancing occupant safety.
- 1-inch diameter aluminum tube with 1/4-inch wall thickness: This size and wall thickness combination offers a good balance between strength and weight, making it suitable for various applications, including:
- Furniture frames: The robust nature of this combination provides a strong foundation for chairs, tables, and other furniture structures.
- Bike frames: The strength-to-weight ratio allows for lightweight yet rigid frames for bicycles.
- Industrial equipment: This tubing can be used for frames, supports, and various components in machinery and industrial equipment.
- 1-inch diameter aluminum tube with 1/8-inch wall thickness: This combination prioritizes weight reduction while maintaining adequate strength for specific applications, such as:
- Electrical conduit: This lightweight tubing is ideal for protecting electrical wires while minimizing weight in building construction and electrical applications.
- Handrails: The combination provides a sturdy handrail structure without adding excessive weight, particularly beneficial in applications like staircases or balconies.
- Signage and displays: This tubing can be used for lightweight frames for signage and display structures.
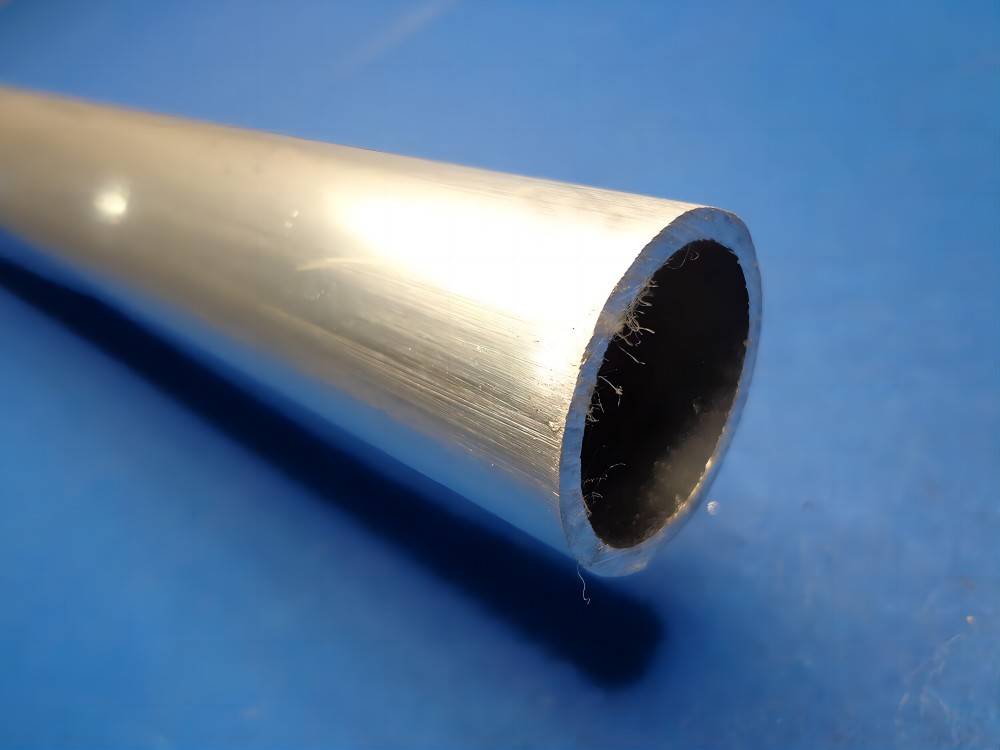
Conclusion
Aluminum tubing offers a compelling combination of strength, weight savings, versatility, and formability. By understanding the different size designations (diameter and wall thickness), the importance of selecting the right alloy for your project’s needs, and exploring the vast array of applications, you can leverage the many benefits of aluminum tubing to bring your project to life.