Almost all welding methods can be used to weld the aluminum tube and weld the aluminum alloy. Today, this article will introduce everything about aluminum tube welding.
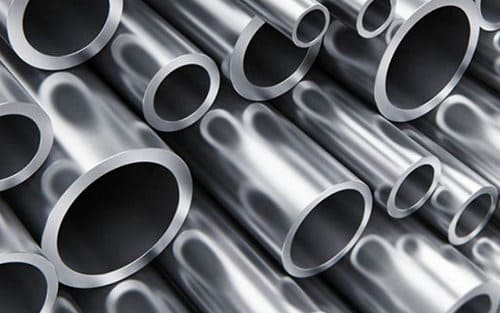
Basic Knowledge of Aluminum Tube
As for the aluminum tube, this part will tell you the chemical composition of the aluminum tube, and mechanical properties of the aluminum tube, and the chemical composition of the aluminum tube welding wire.
The chemical composition of the aluminum tube is shown in the table:
Aluminum Tube Specification |
Chemical Composition% |
||||
|
Si |
Fe |
Cu |
Mn |
Mg |
168.2×7.11 |
0.6-0.8 |
0.4 |
0.1-0.3 |
0.1 |
0.4-0.7 |
The mechanical properties of aluminum tubes are shown in the table:
Aluminum Tube Specification |
Mechanical Properties |
|||
Ob/Ma |
os/IWa |
o5/MPa |
Elastic modulus/MPa |
|
168.2×7.11 |
2.7 |
2.7 |
10 |
700 |
The chemical composition of the welding wire is shown in the table:
Chemical composition of the welding wire % |
|||||||
chemical element |
Si |
Fe |
Cu |
Mn |
Mg |
Ti |
Al |
content/% |
5.3 |
0.2 |
0.2 |
0.008 |
0.015 |
0.01 |
margin |
What Need to Know about Doing Aluminum Tube Welding?
1. When you do aluminum tube welding, you should not use a welding torch for the welding rod. You can heat it first and then dip it in the welding powder. The reason is that the melting point of the welding rod is too low.
2. As you know, the effect of a one-time successful welding aluminum tube is better, because the point of the aluminum tube melting rotary cutter is too low. The aluminum tube is easily deformed when it is reheated for the second time.
3. A wet towel must be placed in the liner of the aluminum tube to protect the aluminum tube in place. The welding space is very narrow, so you should be sure to pay attention to the protection of the refrigerator.
4. The flame of the torch should not be too long, and must be heated with a low flame. Otherwise, the aluminum tube of the dispersant will easily melt.
5. After the welding aluminum tube is completed, you need to wait for the special nylon slurry to cool for two to three minutes. And then the cement storage can be touched. Otherwise, the solder joints of the aluminum tube are easy to leak.
6. The welding rod of the aluminum tube must be evenly coated with flux to ensure the quality of solder joints.
7. The welding time of the aluminum tube should not be too long, because the melting point of the aluminum tube is too low. If the time of the aluminum tube welding is too long, it will easily cause the wall of the aluminum tube to melt or become thinner. Besides, the pressure will easily leak.
Operating Points of Aluminum Tube Welding
1. The first layer welding of aluminum tube welding
The ambient temperature of the first layer welding (root welding) is below 5°C, and the aluminum tube welding should be preheated at 100-150°C to avoid pores.
As for aluminum tube welding, the welding specification of the all-position welding method is the same as that of spot welding. you should start from the overhead welding position, weld half a circle to the flat welding position, and then weld another half circle.
When starting welding from the upward welding position (at 6 o’clock of the clock), the welding torch is tilted forward with an inclination angle of α=0°~10°. When welding other parts, the welding torch is tilted backward with an inclination angle of β=0°-15°. The inclination angle of the welding torch at each position of the all-position welding is shown in the figure. The change of the inclination angle is to make the groove fully penetrated, and the inclination angle cannot be too large, which is mainly to reduce spatter as much as possible.
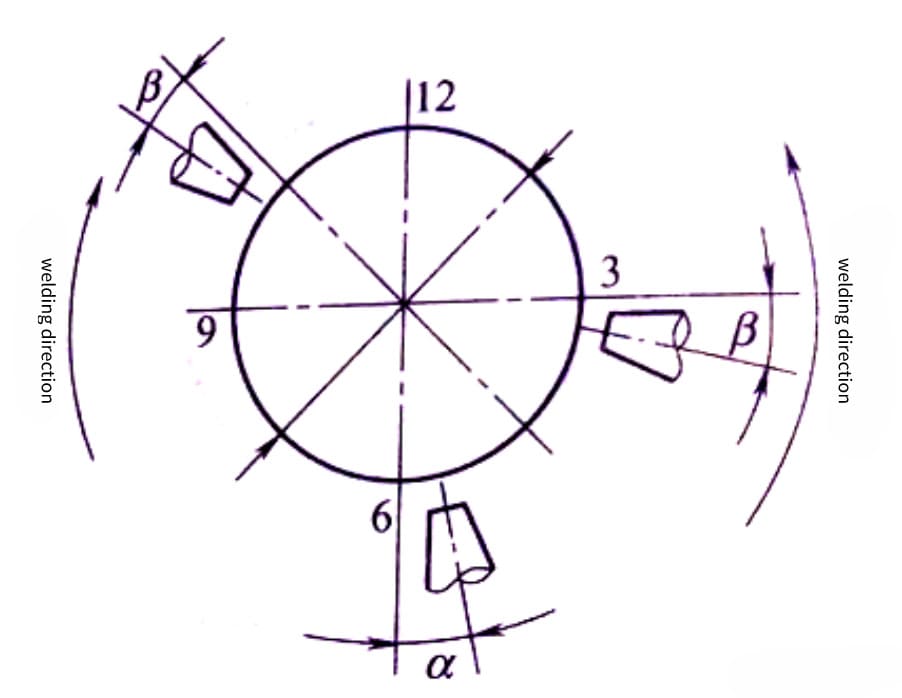
When you weld the first layer of the aluminum tube, there is no need to worry about welding through because there is a bushing. Thus, you should stay on both sides of the groove for a while to ensure full penetration. Due to the strong welding heat specification, to make the weld seam of the cover layer beautiful, the temperature between the welding layers should not exceed 200 ° C. The welding speed should not be too slow when you do aluminum tube welding. The weld height of the first layer is preferably 2/3 of the wall thickness.
2. Surface layer welding (cover welding) of the aluminum tube welding
After the first layer of the aluminum tube is welded, the surface of the weld seam should be cleaned with a copper wire brush to remove stains and scale. Besides, the surface layer can be welded after cooling. The degree of surface layer welding is the same as that of the first layer welding, and its specification is slightly weaker than that of the first layer welding. The speed at which the torch moves should be even to obtain a nice, smooth weld surface for the aluminum tube.
Precautions for Aluminum Tube welding
1. Welding wire and weldments for the aluminum tube must be clean.
2. To ensure the effect of gas protection, wind protection measures should be taken necessarily.
3. Ensure normal wire feeding, and the wire feeding tube should not be bent too much, to maintain the normal welding process of the aluminum tube.
4. Minimize the softening degree of welded joints, and the interlayer temperature should be <200°C during the aluminum tube welding.