When it comes to pharmaceutical packaging, the choice of material is critical to ensure the safety, efficacy, and longevity of the product. Packaging must protect contents from contamination, preserve quality, and offer ease of use, all while meeting environmental and regulatory standards. Among the popular choices, pharmaceutical aluminum tubes and plastic tubes both offer distinct advantages but cater to different needs. This article compares these two packaging options and delves into the key factors to consider when choosing between aluminum and plastic tubes for pharmaceutical products.
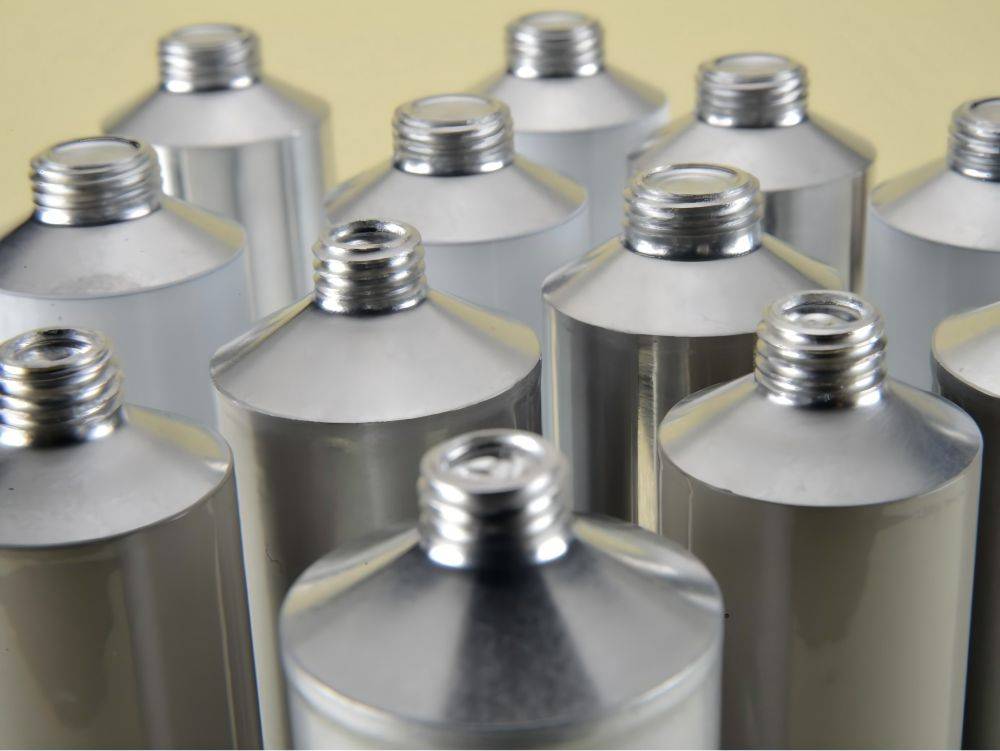
Overview of Aluminum and Plastic Tubes in Pharmaceuticals
Aluminum Tubes
Aluminum tubes are widely used in pharmaceutical packaging due to their excellent protective properties. The material provides a strong barrier against light, oxygen, and moisture, helping to maintain the integrity and shelf life of sensitive pharmaceutical products such as creams, ointments, and gels. Pharmaceutical aluminum tubes are also non-reactive, preserving the chemical stability of the contents. This level of protection is essential for pharmaceuticals that require an airtight, secure container to ensure product efficacy over time. Additionally, aluminum tubes are durable, recyclable, and compatible with a wide range of pharmaceutical products.
However, they can be more expensive than plastic tubes and may be susceptible to corrosion in certain environments.
Plastic Tubes
Plastic tubes are often chosen for their flexibility, cost-effectiveness, and ease of use. They are commonly made from materials such as polyethylene or polypropylene and are popular for products that require frequent dispensing. Plastic tubes are lightweight, easy to handle, and often provide a more convenient user experience, making them a viable option in certain pharmaceutical applications.
However, they may not offer the same level of barrier protection as aluminum tubes, especially against light and oxygen. Additionally, some plastic materials may leach chemicals into the product, potentially compromising its quality and safety.
In short, aluminum and plastic tubes have different strengths in pharmaceutical packaging. The choice depends on product-specific requirements such as the need for barrier protection, durability, or user convenience.
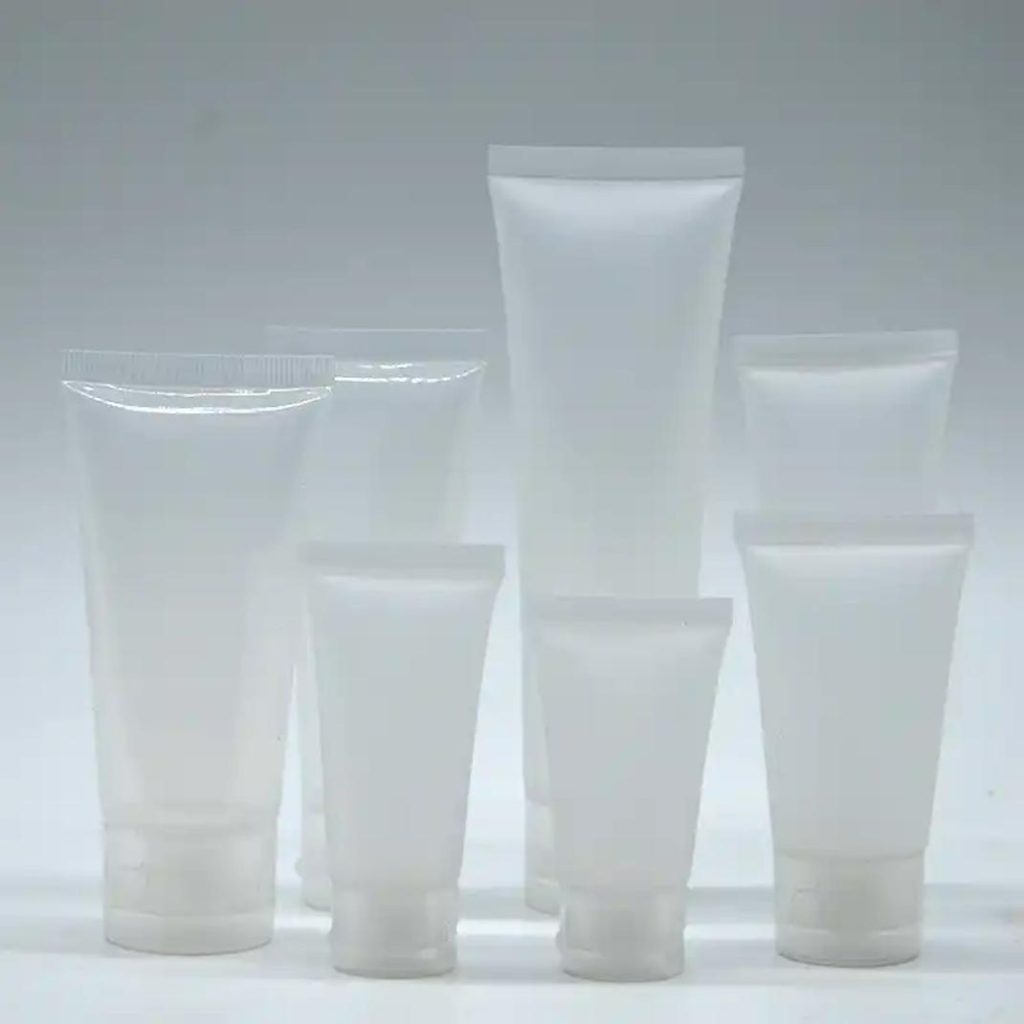
Key Comparison Factors for Pharmaceutical Packaging
To determine the optimal packaging choice, it’s essential to consider specific performance factors that influence how well aluminum and plastic tubes meet pharmaceutical requirements.
1. Barrier Protection
For pharmaceuticals, barrier protection is vital to prevent exposure to contaminants and preserve product stability. Aluminum tubes excel in this area due to their impermeability, effectively blocking out light, air, and moisture. This makes pharmaceutical aluminum tubes ideal for sensitive formulations that could degrade if exposed to external elements. Plastic tubes, while providing a basic barrier, are more permeable, meaning some oxygen or moisture could pass through, which could potentially affect certain medications.
In conclusion, for products requiring robust protection, aluminum is the superior choice.
2. Chemical Compatibility
The material’s interaction with the product it holds is a critical consideration in pharmaceutical packaging. Aluminum is highly resistant to reactions, meaning there’s minimal risk of the tube’s material leaching into the product. This chemical stability is especially important for active pharmaceutical ingredients (APIs) that may interact with other substances. Plastic tubes, however, can be more chemically reactive, depending on the formulation and the type of plastic used.
In short, aluminum is generally a safer option when dealing with chemically sensitive pharmaceuticals.
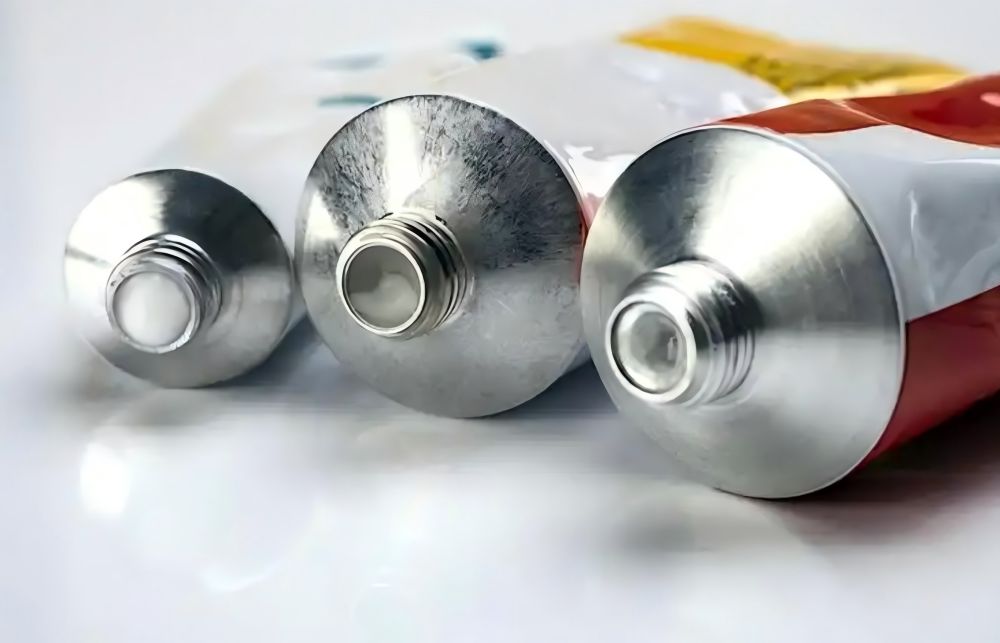
3. Durability and Flexibility
Aluminum and plastic differ significantly in durability and flexibility. Aluminum tubes are more puncture-resistant and provide strong protection against physical damage, making them durable and reliable for transport and storage. However, they are less flexible than plastic, which may affect user experience during dispensing. Plastic tubes, by contrast, are lightweight, flexible, and easy to squeeze, enhancing ease of use.
For products where durability is paramount, aluminum is preferred, while plastic offers a practical solution when flexibility and dispensing ease are prioritized.
4. Sustainability and Environmental Impact
With the increasing focus on sustainability, aluminum’s recyclability gives it an edge in pharmaceutical packaging. Aluminum can be recycled without losing its properties, supporting a circular economy and reducing environmental impact. Plastic, on the other hand, is less sustainable due to limited recyclability and the environmental challenges associated with plastic waste. Although some recyclable plastics exist, the infrastructure for effective recycling remains limited.
In terms of environmental impact, aluminum’s recyclability and lower environmental footprint make it a more sustainable choice.
5. Cost Considerations
Cost plays a key role in packaging decisions, as it affects the overall budget of pharmaceutical production. Aluminum tubes tend to be more expensive due to the cost of raw materials and manufacturing processes. However, the enhanced protection and durability may offset these costs for products that require high stability. Plastic tubes are generally more affordable, making them attractive for cost-sensitive products where moderate protection is sufficient.
In summary, while aluminum may require a higher initial investment, it often provides better value for products with specific packaging needs.
6. User Experience and Ease of Use
User experience is critical, particularly in pharmaceutical packaging, as it affects how easily patients can access and use the product. Plastic tubes, due to their flexibility, offer a more convenient dispensing experience, allowing users to squeeze out the contents with ease. Aluminum tubes, while more durable, can be rigid, making it harder to dispense the product, especially in cold conditions.
Ultimately, the user experience factor may influence the choice between aluminum and plastic depending on the product’s dispensing requirements and the frequency of use.
Choosing between aluminum and plastic tubes for pharmaceutical products involves carefully evaluating each material’s protective, functional, and environmental qualities. Pharmaceutical aluminum tubes provide exceptional barrier protection, chemical stability, durability, and environmental benefits, making them ideal for products that require robust preservation and safety. Although they come at a higher cost, aluminum’s reliable protection can be invaluable for sensitive pharmaceuticals. Plastic tubes, on the other hand, offer affordability, flexibility, and convenience, making them suitable for products with moderate stability requirements. Ultimately, selecting the right packaging solution requires balancing product-specific needs with considerations for durability, environmental impact, and user experience to ensure the highest quality and effectiveness in pharmaceutical packaging.