Aluminum U-channels are integral components in modern construction, providing versatile solutions for structural and aesthetic applications. Their unique shape and properties make them suitable for a variety of uses, from framing and support to decorative finishes. This article explores the characteristics, fabrication processes, installation techniques, and practical applications of aluminum U-channels in construction.
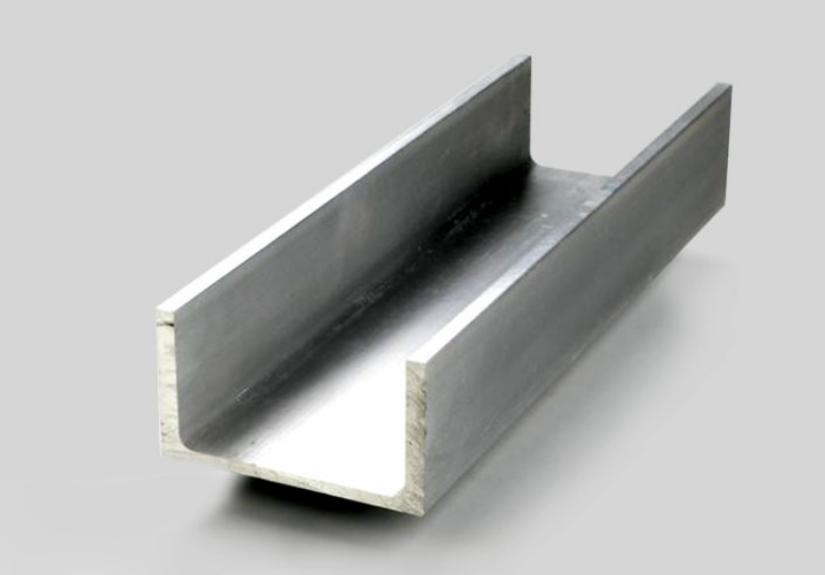
What is an Aluminum U-Channel?
An aluminum U-channel is a structural element characterized by its U-shaped cross-section. This shape provides a combination of strength, lightweight, and versatility, making it ideal for numerous construction applications.
Characteristics:
- Lightweight: Aluminum’s low density makes U-channels easy to handle and transport.
- Corrosion-resistant: Naturally resistant to corrosion, especially when treated, aluminum U-channels have a long lifespan even in harsh environments.
- Strong and Durable: Despite being lightweight, aluminum offers excellent strength and durability.
- Conductive: Aluminum is a good conductor of electricity and heat, which can be beneficial in certain applications.
- Recyclable: Aluminum is highly recyclable, supporting sustainable construction practices.
Applications
Aluminum U-channels are used in various construction scenarios including:
- Framing and Support: Used in windows, doors, and other framing structures.
- Railings and Fencing: Providing support and structure for railings and fences.
- Decorative Elements: Used for trim and other decorative purposes.
- Infrastructure: Utilized in bridges, walkways, and other civil engineering projects.
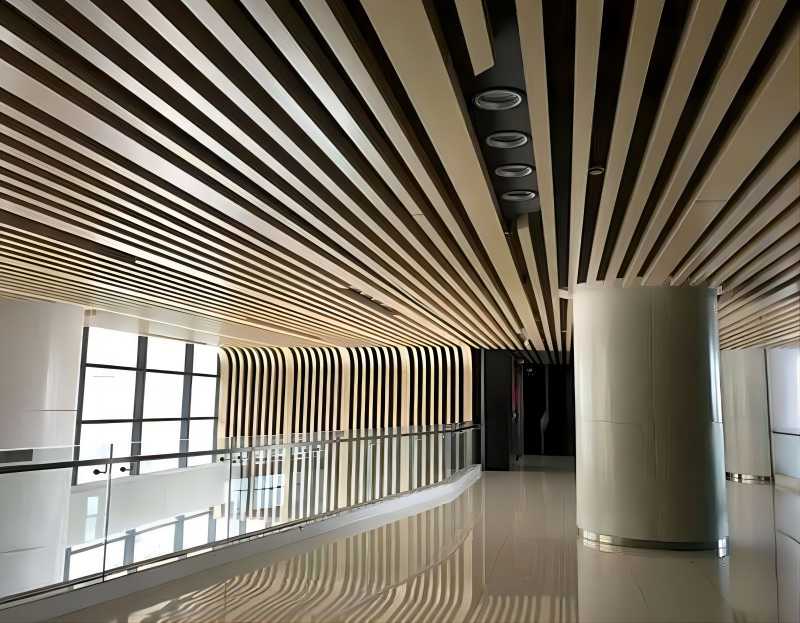
Fabrication Process of Aluminum U-Channels
The fabrication of aluminum U-channels involves several detailed steps, from selecting the appropriate alloy to the final surface treatment. Here’s an in-depth look at each stage of the process:
1. Selection of Aluminum Alloy and Grade
Choosing the right aluminum alloy and grade is crucial to ensure the U-channel meets the specific requirements of its intended application.
6061 Alloy: This alloy is known for its excellent mechanical properties, including high strength and good weldability. It is often used in structural applications where durability and robustness are essential.
6063 Alloy: This alloy is preferred for architectural applications due to its superior surface finish and excellent corrosion resistance. It is also highly extrudable, making it ideal for complex shapes and profiles.
2. Manufacturing Processes
Extrusion
- Billet Preparation: Aluminum billets (cylindrical blocks) are heated to around 900°F to 925°F (482°C to 496°C) to make them malleable.
- Extrusion Press: The heated billet is placed into an extrusion press where it is forced through a steel die that has the U-channel profile. The pressure causes the aluminum to take the shape of the die, creating a continuous length of U-channel.
- Cooling: The extruded U-channel is cooled immediately after exiting the die, usually with water or air to set its shape.
- Cutting to Length: Once cooled, the extruded U-channel is cut to the desired lengths using saws or automated cutting equipment.
Cutting and Machining
- Precision Cutting: For applications requiring exact dimensions, further cutting and machining are performed using tools like CNC machines, which ensure high precision and consistency.
- Deburring: Edges and surfaces are deburred to remove any sharp edges or rough spots that could affect the performance or safety of the U-channel.
Bending and Forming
- Custom Shapes: For specific requirements, U-channels may be bent or formed using specialized machinery. This process allows for the creation of custom shapes and angles that fit unique architectural or structural needs.
3. Surface Treatment Options
Surface treatments enhance the performance, durability, and appearance of aluminum U-channels. The main surface treatment options include:
Surface Treatment Option | Process Description | Benefits |
Anodizing | Immersing the U-channel in an electrolytic solution and applying an electric current to create a thick oxide layer on the surface. | Enhances corrosion resistance, Improves wear resistance, Allows for dyeing to achieve various colors |
Powder Coating | Applying a dry powder to the surface using an electrostatic gun, then heating in a curing oven to form a uniform finish. | Provides a thick, protective layer, Resistant to scratches, chipping, and fading, Available in a wide range of colors and finishes |
Painting | Applying liquid paint through spraying, brushing, or dipping, with multiple coats for desired thickness and finish. | Broad spectrum of colors and finishes, Useful for matching specific design aesthetics, Provides additional protective layers |

Installation Techniques of Aluminum U-Channels
Proper installation of aluminum U-channels ensures they perform effectively and safely in their intended applications. This process involves several critical steps: pre-installation preparations, selecting and implementing attachment methods, and adhering to safety considerations.
Pre-installation Preparations
1. Site Inspection
- Assessment: Evaluate the installation site to ensure it is suitable for the aluminum U-channels. This includes checking for any structural issues, moisture problems, or other factors that could affect the installation.
- Measurements: Accurate measurements are essential for a precise fit. Measure the length, width, and height of the installation area and verify these measurements against the specifications of the U-channels.
- Surface Preparation: Clean the installation surface to remove any debris, dust, or grease that could interfere with adhesion or secure attachment. Depending on the surface material, this might involve using specific cleaning agents or mechanical abrasion.
2. Tool Preparation
- Gather Tools: Ensure all necessary tools are available and in good working condition. Common tools include drills, screwdrivers, measuring tapes, levels, and saws.
- Safety Equipment: Assemble required personal protective equipment (PPE) such as gloves, safety glasses, helmets, and work boots. Ensure that all safety equipment meets regulatory standards.
Attachment Methods
1. Screws and Bolts
- Drilling Holes: Pre-drill holes in the aluminum U-channel and the mounting surface to prevent the material from splitting or cracking. Use a drill bit appropriate for aluminum.
- Fastening: Use corrosion-resistant screws or bolts to attach the U-channel. Ensure fasteners are tightened securely but not over-tightened, which could deform the channel or strip the threads.
- Spacing: Space the fasteners evenly along the length of the U-channel to distribute the load uniformly. Follow recommended spacing guidelines to ensure structural integrity.
2. Welding
- Surface Preparation: Clean the surfaces to be welded to remove any oxidation or contaminants. Use a wire brush or grinder if necessary.
- Welding Technique: Use appropriate welding techniques for aluminum, such as Tungsten Inert Gas (TIG) welding or Metal Inert Gas (MIG) welding. Ensure the welding machine settings are suitable for the aluminum thickness and type.
- Cooling: Allow the welded areas to cool slowly to prevent warping or cracking. Inspect the welds for any defects and perform additional passes if necessary.
3. Adhesives
- Selection: Choose adhesives specifically designed for bonding aluminum. Epoxy-based adhesives or polyurethane adhesives are commonly used.
- Application: Apply the adhesive evenly along the contact surface of the U-channel. Press the U-channel firmly into place and hold it until the adhesive sets, following the manufacturer’s instructions for curing time.
- Support: Temporary supports or clamps may be needed to hold the U-channel in place while the adhesive cures fully.
Safety Considerations
1. Personal Protective Equipment (PPE)
- Gloves: Wear gloves to protect your hands from sharp edges and to provide a better grip on tools and materials.
- Safety Glasses: Use safety glasses or goggles to protect your eyes from debris, especially during cutting, drilling, or welding.
- Helmets and Boots: Helmets protect your head from falling objects, while steel-toed boots protect your feet from heavy materials.
2. Safe Handling
- Lifting Techniques: Use proper lifting techniques to avoid strain or injury. Lift with your legs, not your back, and get assistance for heavy or awkward pieces.
- Securing Materials: Ensure all materials are securely fastened during transport and installation to prevent them from shifting or falling.
3. Secure Scaffolding and Ladders
- Stability: Ensure scaffolding and ladders are stable and on a level surface. Secure ladders at the top and bottom to prevent slipping.
- Height Safety: Use fall protection gear, such as harnesses, when working at heights. Follow all safety regulations regarding working at elevated positions.
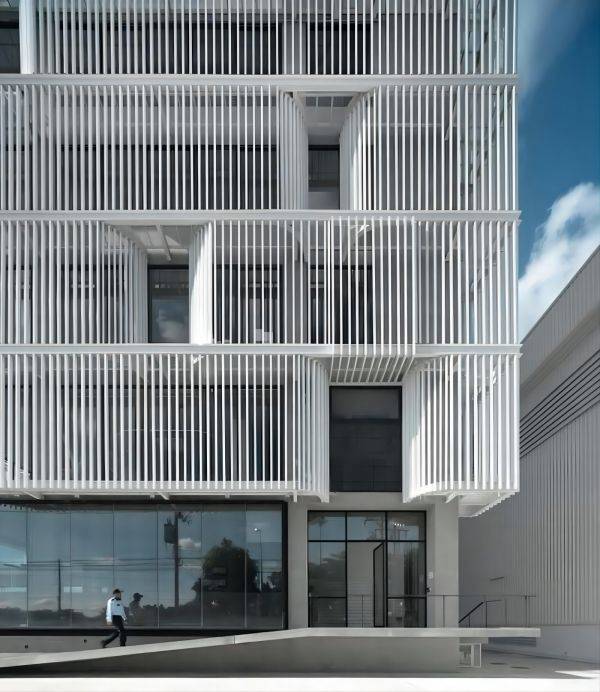
Conclusion
Aluminum U-channels are indispensable in construction, combining strength, durability, and versatility with ease of fabrication and installation. From structural applications to decorative uses, they play a vital role in modern construction projects. Understanding their characteristics, fabrication, and installation processes helps in making informed decisions for various construction needs, ensuring both functionality and aesthetic appeal.