Aluminum and carbon fiber are two widely used materials in modern industries, each offering unique properties that make them suitable for various applications. Aluminum, a lightweight metal known for its excellent strength-to-weight ratio and corrosion resistance, has been a staple in industries such as construction, automotive, and aerospace for decades. On the other hand, carbon fiber, a high-performance composite material, has gained prominence due to its exceptional strength, stiffness, and low weight.
This article seeks to address a crucial question: Which is stronger, aluminum or carbon fiber? To answer this, we will analyze and compare these two materials based on their properties, strength-to-weight ratio, applications, and hybrid material developments.
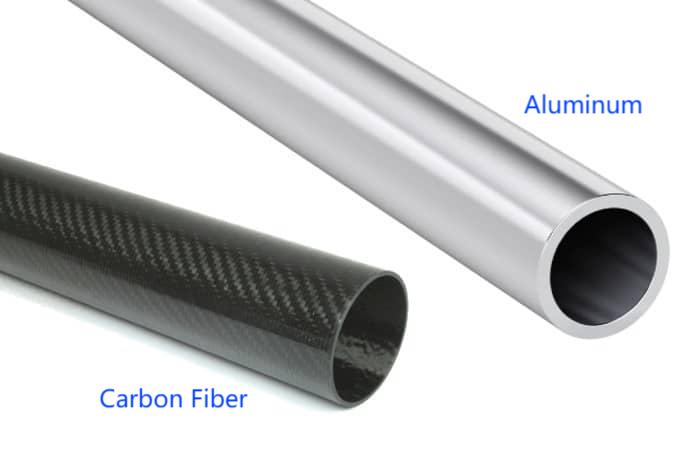
Material Properties Comparison Between Aluminum and Carbon Fiber
Aluminum: A Versatile Metal
Aluminum is a metallic element that belongs to the lightweight metal category. It is widely used in various industrial applications due to its advantageous properties:
- Varied Alloy Compositions: Aluminum is often alloyed with other elements such as copper, magnesium, and zinc to enhance its mechanical properties. However, its strength varies significantly based on the alloy composition. Common aluminum alloys, such as 6061 and 7075, offer different balances of strength, corrosion resistance, and machinability
- Corrosion Resistance: Aluminum naturally forms an oxide layer that protects it from rust and corrosion, making it suitable for outdoor and marine applications.
- Machinability & Cost Efficiency: Aluminum is relatively easy to machine, weld, and form, making it a cost-effective choice for manufacturing.
Carbon Fiber: A High-Performance Composite
Carbon fiber is a composite material made of thin strands of carbon atoms woven together and embedded in a polymer resin matrix. This structure gives it extraordinary mechanical properties:
- Customizable Strength and Stiffness: The arrangement of carbon fibers and the choice of resin can be tailored to specific applications, making it highly adaptable.
- Superior Strength-to-Weight Ratio: Carbon fiber is significantly lighter than aluminum while offering superior tensile strength and stiffness.
- Resistance to Fatigue and Corrosion: Unlike metals, carbon fiber does not suffer from corrosion or fatigue failure in the same way, making it highly durable in harsh environments.
Strength-to-Weight Ratio Analysis
What Is Strength-to-Weight Ratio?
The strength-to-weight ratio (also known as specific strength) is a key factor in evaluating a material’s performance, particularly in applications where weight reduction is critical. It is calculated as the strength of the material divided by its density.
Comparing Aluminum and Carbon Fiber
A material’s strength-to-weight ratio is crucial in determining its efficiency in applications requiring both lightness and durability.
- Tensile Strength: Carbon fiber has a tensile strength ranging from 3000 MPa to 6000 MPa, whereas aluminum alloys typically fall between 300 MPa to 500 MPa. This shows that carbon fiber is significantly stronger in tension.
- Density Comparison: Aluminum has a density of 2.7 g/cm³, while carbon fiber has a density of about 1.6 g/cm³. This means that for the same weight, a carbon fiber component can be significantly larger and stronger than an aluminum component.
- Impact Resistance: Aluminum has a better ability to absorb impacts without breaking, whereas carbon fiber, although strong, can shatter upon impact due to its brittle nature.
So, is carbon fiber stronger than aluminum? In terms of strength-to-weight ratio, yes, carbon fiber outperforms aluminum. However, aluminum remains preferable in applications requiring ductility and impact resistance.
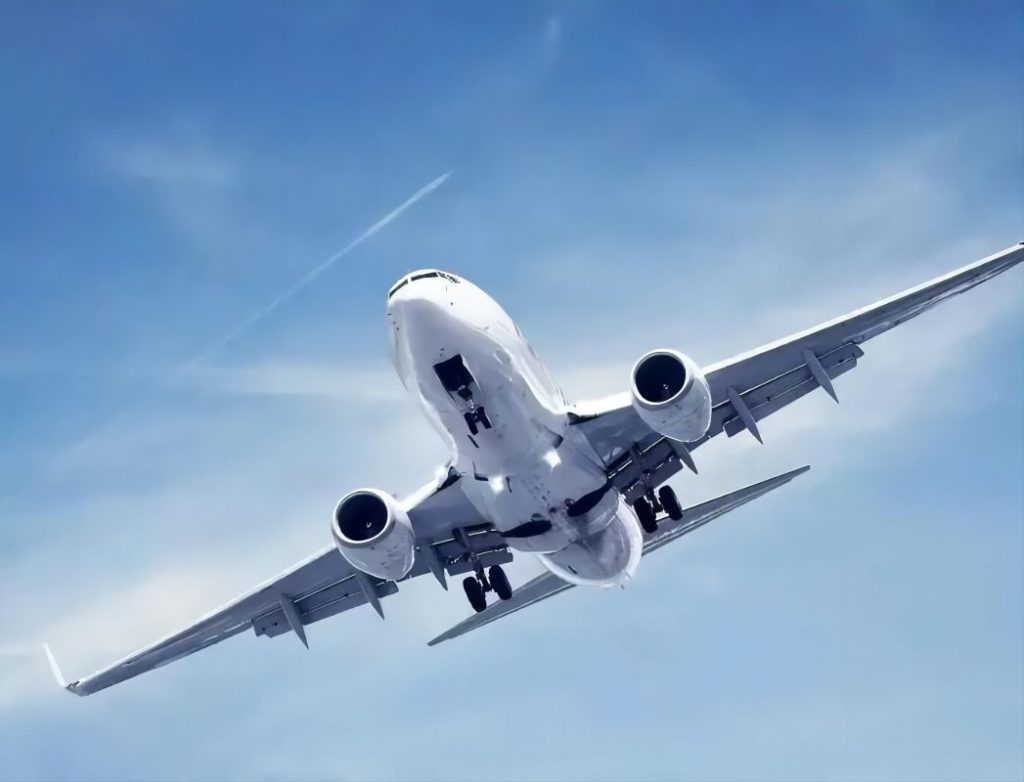
Differences in Application Fields of Aluminum and Carbon Fiber
Aluminum: Traditional and Versatile
Due to its cost-effectiveness, ease of manufacturing, and good mechanical properties, aluminum is widely used in:
- Construction: Used in structural frameworks, window frames, and roofing due to its corrosion resistance and strength.
- Automotive Industry: Many vehicle components, including engine blocks, chassis, and wheels, are made from aluminum to reduce weight and improve fuel efficiency.
- Packaging Industry: Aluminum is a key material in cans, foils, and other packaging due to its lightweight and recyclability.
Carbon Fiber: High-Performance Applications
Carbon fiber is preferred in industries where weight reduction and superior performance are critical, such as:
- Aerospace: Aircraft structures, wings, and fuselages incorporate carbon fiber to enhance fuel efficiency and structural integrity.
- Sports and Recreation: Bicycle frames, tennis rackets, and golf clubs use carbon fiber for increased strength and reduced weight.
- High-Performance Automotive: Supercars and Formula 1 cars use carbon fiber components to improve speed, aerodynamics, and crash resistance.
The Synergistic Potential of Aluminum and Carbon Fiber Composite Materials
The development of composite materials that integrate carbon fiber and aluminum represents a strategic engineering approach, designed to capitalize on the complementary strengths of each constituent. This hybridization addresses inherent limitations found in each material when used independently.
Specifically, carbon fiber-reinforced aluminum composites (CFRP-Al) are engineered to merge the exceptional tensile strength and stiffness characteristic of carbon fiber with the inherent ductility and superior thermal conductivity of aluminum. This combination yields a material system exhibiting enhanced performance profiles suitable for demanding applications.
These advanced composites find critical application in sectors such as aerospace, automotive engineering, and high-performance machinery, where the simultaneous optimization of structural integrity, weight reduction, and thermal management is paramount. The ability to precisely tailor the composite’s mechanical and thermal properties through meticulous control of fiber orientation, volume fraction, and matrix composition enables the creation of application-specific solutions that surpass the performance capabilities of either material alone.
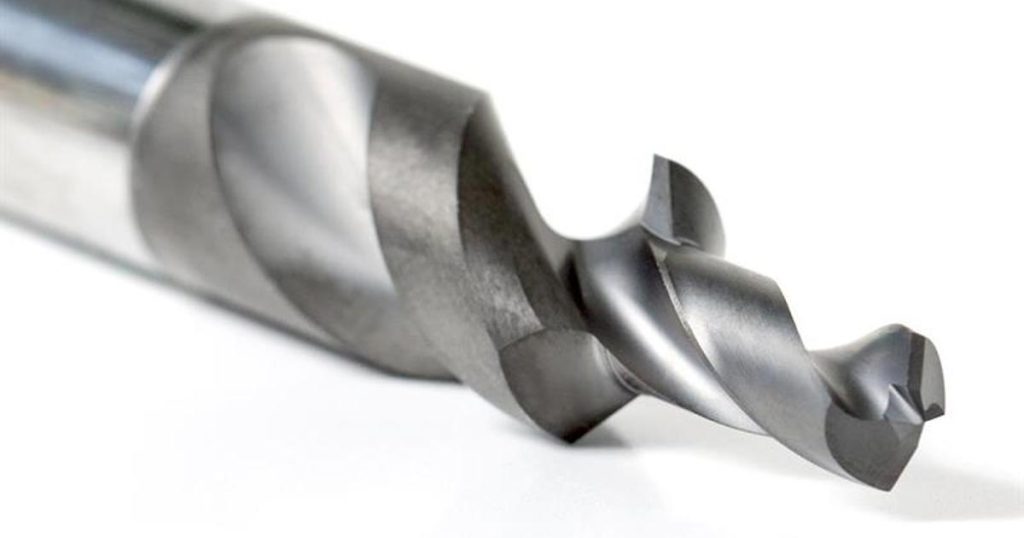
Aluminum or Carbon Fiber? Practical Considerations and Selection
Choosing between aluminum and carbon fiber depends on various factors:
- Economic Considerations: Aluminum’s production and processing costs are substantially lower than those associated with carbon fiber. This economic advantage positions aluminum as the dominant material for large-scale manufacturing and cost-sensitive applications.
- Manufacturing Complexity: Carbon fiber fabrication necessitates specialized and often complex manufacturing techniques, including precise molding, resin infusion, and autoclave curing. These processes contribute to increased production costs and limit scalability. Conversely, aluminum’s machinability and weldability offer greater ease of fabrication, facilitating complex designs with established manufacturing processes.
- Environmental Durability: Carbon fiber exhibits superior corrosion resistance compared to aluminum, eliminating the need for protective coatings in harsh environments. However, carbon fiber is susceptible to impact damage, potentially leading to delamination and structural failure, whereas aluminum, while vulnerable to corrosion, is more resilient to certain types of mechanical impact.
In Summary
The question “Which is stronger, aluminum or carbon fiber?” does not have a one-size-fits-all answer. Carbon fiber has a significantly higher strength-to-weight ratio and is preferred for high-performance applications, whereas aluminum is more affordable, easier to work with, and widely used in everyday industries.
Ultimately, the choice between aluminum and carbon fiber depends on the specific application’s requirements. If the priority is lightweight strength and high performance, carbon fiber is superior. However, if cost, manufacturability, and durability in variable conditions are the primary concerns, aluminum remains an excellent choice.
As technology advances, hybrid materials like carbon fiber-reinforced aluminum will likely play an increasingly important role in bridging the gap between these two materials, offering the best of both worlds in future engineering solutions.