Heat exchangers are critical components in various industries, playing a vital role in transferring heat between fluids or surfaces. From automotive and aerospace to chemical processing and HVAC systems, the choice of material for a heat exchanger can significantly impact its efficiency, durability, and cost. Two popular materials often debated are aluminum and stainless steel. Each has distinct characteristics, offering advantages and disadvantages depending on the specific application. This article will provide a detailed comparison to help you decide which is the better choice for your heat exchanger: aluminum or stainless steel?
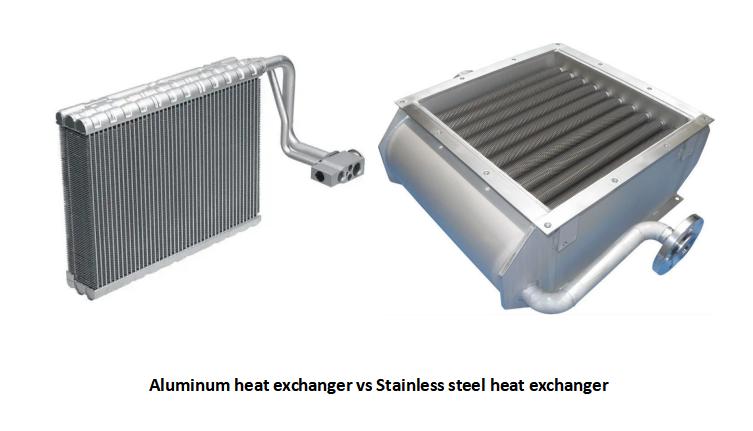
Understanding Heat Exchangers
A heat exchanger is a device designed to efficiently transfer heat between two fluids or between a fluid and a solid surface, widely used in refrigeration, heating, ventilation, air conditioning (HVAC), and power generation. The choice of material used in its construction is crucial, as it directly affects performance, longevity, and cost.
The material’s thermal conductivity, corrosion resistance, mechanical strength, and weight all play a vital role in how well a heat exchanger performs. Two of the most widely used materials are aluminum and stainless steel, both offering unique benefits for specific needs. Let’s explore the type of aluminum and stainless steel often used in heat exchanger.
Types of Aluminum Used in Heat Exchangers
- 3003 Aluminum Alloy: 3003 is one of the most commonly used aluminum alloys for heat exchangers due to its excellent formability, good corrosion resistance, and moderate strength. It is widely used in automotive radiators, HVAC systems, and refrigeration units. Its high thermal conductivity makes it ideal for transferring heat efficiently.
- 6061 Aluminum Alloy: Known for its strength and good corrosion resistance, 6061 aluminum is used in applications that require a combination of durability and thermal performance. It is popular in aerospace, marine, and automotive heat exchangers where slightly higher strength is needed than what 3003 offers.
- 1050/1100 Aluminum Alloy: These are pure aluminum grades (99% or more) that are used in heat sinks and low-stress heat exchangers because of their superior thermal conductivity. However, their strength is lower compared to alloyed aluminum types, which limits their use to applications where mechanical strength is not a primary concern.
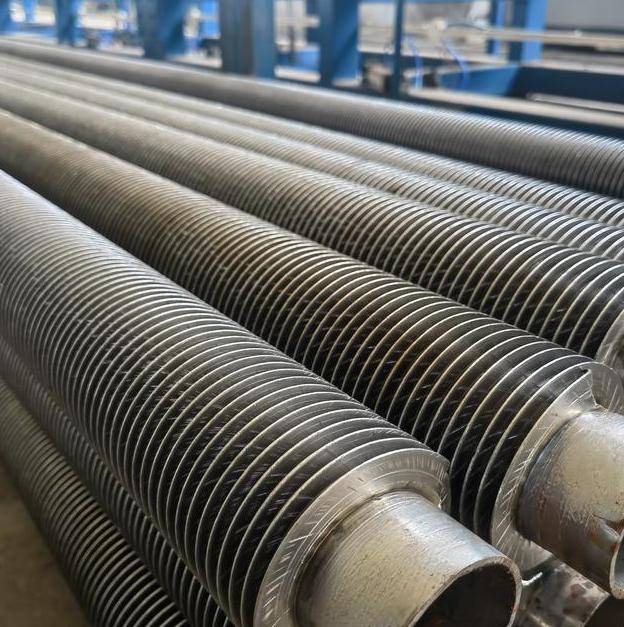
Types of Stainless Steel Used in Heat Exchangers
- 304 Stainless Steel (Austenitic): 304 stainless steel is the most commonly used grade of stainless steel in heat exchangers due to its combination of good corrosion resistance, durability, and affordability. It is widely used in food and beverage processing, chemical plants, and HVAC systems where moderate corrosion resistance is needed.
- 316 Stainless Steel (Austenitic): 316 stainless steel offers superior corrosion resistance compared to 304, particularly in harsh environments like marine and chemical processing industries. It is commonly used in applications where exposure to saltwater, acids, and harsh chemicals is prevalent.
- Duplex Stainless Steel (2205): Duplex stainless steels, such as 2205, offer a balance of both strength and corrosion resistance. They are often used in oil and gas, power generation, and chemical processing industries where both high strength and corrosion resistance are required.
- Ferritic Stainless Steel (409, 439): Ferritic stainless steels such as 409 and 439 are used in applications where heat and corrosion resistance are required, but the cost is also a concern. They are used in automotive exhaust heat exchangers and other less corrosive environments.
Aluminum Heat Exchanger vs Stainless Steel Heat Exchanger
When selecting the ideal material for heat exchangers, understanding the advantages and limitations of each material is essential to making the right choice for specific applications, whether it be in automotive, HVAC systems, chemical processing, or other industries. In this section, we’ll explore the key differences between aluminum and stainless steel heat exchangers to help you determine which is the better option for your needs.
Pros and Cons of Aluminum and Stainless Steel Heat Exchangers
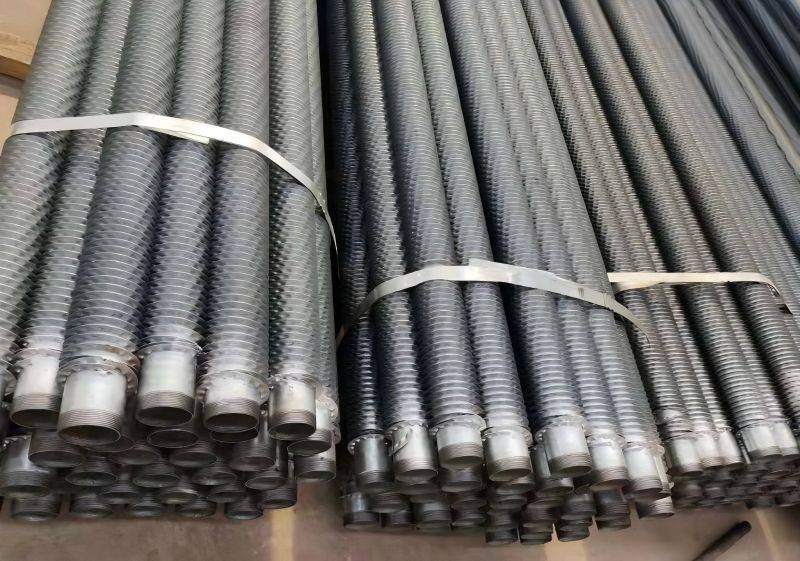
Aluminum Heat Exchangers | |
Pros | Cons |
Lightweight | Lower strength compared to stainless steel |
High thermal conductivity | Not suitable for extremely high-pressure or high-temperature applications |
Cost-effective | Prone to corrosion in highly corrosive environments (unless coated) |
Easily formable and malleable | Requires surface treatments (e.g., anodizing) for better corrosion resistance |
Good for mass production | May degrade faster in harsh chemical or salty environments |
Energy-efficient in heat transfer | Lower durability in industrial environments |
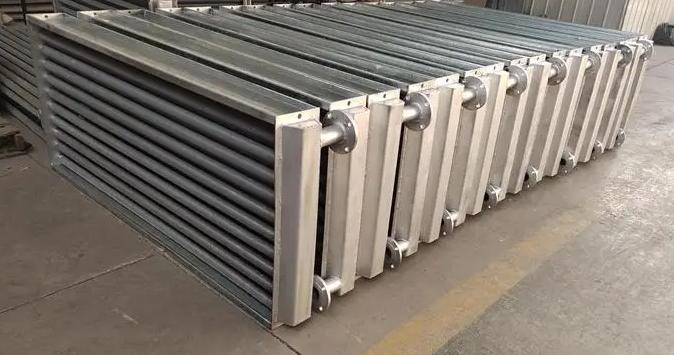
Stainless Steel Heat Exchangers | |
Pros | Cons |
Superior corrosion resistance | Heavier than aluminum, adding to overall weight of the system |
Durable and long-lasting | More expensive compared to aluminum |
Suitable for high-pressure and high-temperature applications | Lower thermal conductivity compared to aluminum |
Resistant to chemical attack | Harder to form and shape, requiring more complex manufacturing techniques |
High strength and structural integrity | Increased cost of production and maintenance due to complexity of fabrication |
Sanitary, ideal for food and pharmaceutical applications | Requires more energy for heat transfer due to lower conductivity |
Common Applications for Aluminum and Stainless Steel Heat Exchangers
Aluminum Heat Exchangers is commonly used in industries where high thermal conductivity and lightweight materials are prioritized. Some typical applications include:
- Automotive radiators: Aluminum heat exchangers improve fuel efficiency by reducing vehicle weight while efficiently dissipating heat.
- HVAC systems: Aluminum heat exchangers are often used in air conditioners and refrigerators due to their high heat transfer capabilities.
- Aerospace: The lightweight nature of aluminum makes it ideal for aerospace applications where every kilogram matters.
Stainless Steel Heat Exchangers is favored in environments that require resistance to corrosion, durability, and the ability to withstand extreme temperatures and pressures. Key applications include:
- Chemical processing: Stainless steel is ideal for handling corrosive chemicals and high-pressure conditions.
- Food and beverage: Stainless steel’s non-reactive nature makes it the preferred choice for hygienic environments where contamination must be avoided.
- Marine environments: Due to its high resistance to saltwater corrosion, stainless steel is commonly used in marine heat exchangers.
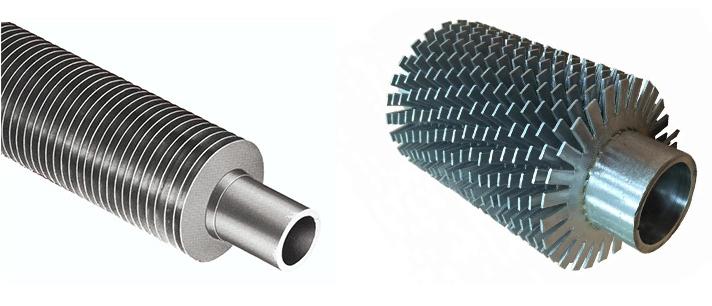
Choosing the Right Material for Your Heat Exchanger
When selecting the right material for your heat exchanger, several factors must be taken into consideration.
Key Factors in Choosing the Right Heat Exchanger Material
1. Thermal Conductivity
Thermal conductivity measures how well a material conducts heat, and this is perhaps the most critical factor in heat exchanger performance. Aluminum has significantly higher thermal conductivity than stainless steel, making it more efficient at heat transfer. In applications where rapid heat dissipation or absorption is required, aluminum often outperforms stainless steel.
2. Corrosion Resistance
Corrosion resistance is another essential factor, especially in environments where the heat exchanger is exposed to moisture, chemicals, or saltwater. While aluminum offers excellent resistance to corrosion in most environments, stainless steel is superior in more corrosive settings such as chemical processing plants, marine environments, and high-salinity conditions. Stainless steel’s higher resistance to corrosion translates into a longer lifespan in harsh conditions.
3. Durability and Strength
In terms of mechanical strength, stainless steel is far stronger than aluminum. Stainless steel heat exchangers can handle higher pressures and temperatures without deforming, which is critical in industrial applications requiring robust performance. However, aluminum is more malleable and can be shaped into more intricate designs, offering greater flexibility in certain engineering requirements.
4. Weight and Design Flexibility
Aluminum is much lighter than stainless steel, making it ideal for applications where weight is a concern, such as automotive and aerospace industries. Lighter weight reduces the overall load and can improve energy efficiency. Stainless steel, while heavier, offers better structural integrity, making it the preferred choice for heavy-duty applications where durability is critical.
5. Cost and Maintenance
Aluminum is generally more affordable than stainless steel, both in terms of material cost and manufacturing. It is also easier to machine, reducing production costs. However, maintenance may be more frequent with aluminum, particularly in corrosive environments, where it may require additional protection. Stainless steel, while more expensive upfront, offers lower maintenance costs over time due to its superior durability and resistance to corrosion.
- Environmental Impact
Both aluminum and stainless steel are recyclable, but aluminum is often considered more environmentally friendly due to its higher recyclability rate and lower energy consumption during production. Stainless steel, however, is valued for its long lifespan and resistance to wear, reducing the need for replacements.
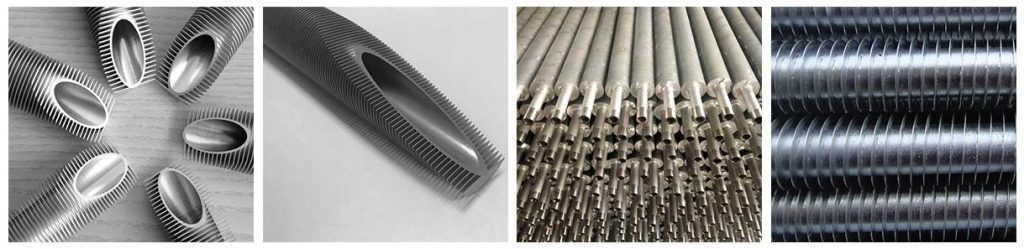
Both aluminum and stainless steel offer unique benefits in heat exchanger applications, and the choice ultimately depends on the specific requirements of your operation. Aluminum stands out for its excellent thermal conductivity, lightweight nature, and cost-effectiveness, while stainless steel is unmatched in its strength, corrosion resistance, and long-term durability. By carefully considering factors such as environment, performance demands, and cost, you can make an informed decision on which material is the better choice for your heat exchanger. CHAL provides a full range of finned tubes for heat exchangers with reliable quality, high performance, complete designs and competitive prices. Please feel free to contact us.