Aluminum welding is a critical process in various industries, from construction and automotive to marine and aerospace. The choice of welding wire significantly impacts the quality, strength, and durability of the final product. Among the numerous options available, two commonly used aluminum welding wires stand out: 5356 and 4043. This article delves into the key differences between these two types of wire to help you make informed decisions for your specific welding projects.
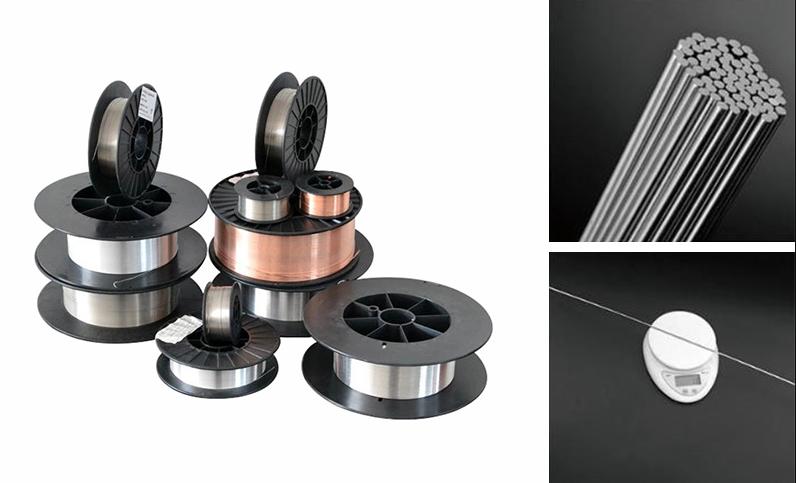
Key Differences Between 5356 and 4043 Aluminum Welding Wire
5356 and 4043 aluminum welding wires offer distinct properties that cater to different applications. Here we conclusion the key differences in composition, material properties, and welding characteristics:
1. Composition and Material Properties
5356 Aluminum Welding Wire:
- Composition: The 5356 welding wire is composed primarily of aluminum with around 5% magnesium, along with traces of manganese, chromium, and titanium. This composition gives the wire its high strength and makes it more suitable for structural applications.
- Material Properties: 5356 is known for its excellent corrosion resistance, particularly in marine environments. It offers good strength and ductility, making it ideal for applications where these properties are required. However, it has a slightly higher melting point compared to 4043, which can affect the welding process.
4043 Aluminum Welding Wire:
- Composition: The 4043 wire is mainly composed of aluminum and silicon (around 5%). The addition of silicon lowers the melting point and improves the fluidity of the molten weld pool, making it easier to weld.
- Material Properties: 4043 is favored for its ease of use, especially in applications where a smooth, crack-resistant weld is needed. It has a lower strength compared to 5356 but provides better fluidity and minimizes the risk of hot cracking. Its corrosion resistance is adequate for general purposes but not as high as 5356 in harsh environments.
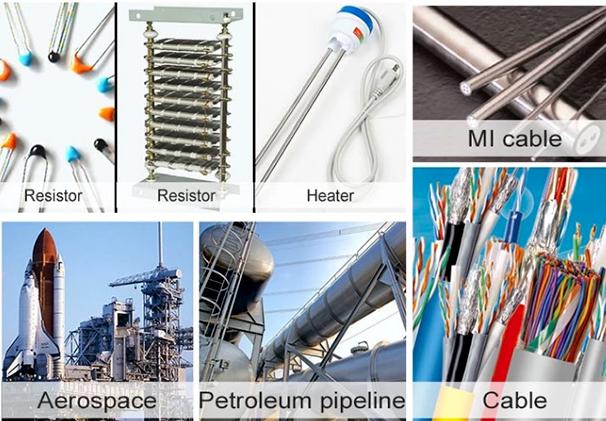
2. Applications and Suitability
Applications for 5356 Welding Wire:
The 5356 wire is typically used in industries such as shipbuilding, automotive, and railway, where high strength and corrosion resistance are critical. It is ideal for welding 5xxx series aluminum alloys and is commonly used in the fabrication of storage tanks, pressure vessels, and structural components.
Applications for 4043 Welding Wire:
4043 is often chosen for welding 6xxx series aluminum alloys, which are used in the construction, aerospace, and automotive industries. It is also preferred in situations where the weld needs to be aesthetically pleasing with a good finish, such as in aluminum furniture and frames. Additionally, 4043 is commonly used in cast aluminum repairs due to its excellent crack resistance.
3. Welding Characteristics
Welding Ease and Technique:
- 5356: This wire requires slightly more skill to weld due to its higher melting point and lower fluidity. It’s best suited for experienced welders who need to achieve strong, durable welds in structural applications.
- 4043: The 4043 wire is easier to use, especially for beginners, due to its lower melting point and higher fluidity. It flows more smoothly, reducing the chances of hot cracking and making it easier to achieve a clean, aesthetic finish.
Appearance and Finish of Welds:
- 5356: Welds made with 5356 tend to have a more matte finish and may require additional finishing work if a polished appearance is desired.
- 4043: Welds made with 4043 typically have a shinier, smoother appearance and often require less post-weld finishing. This makes 4043 a better choice when the weld’s appearance is a priority.
To draw a conclusion, here are the main differences:
Property | 5356 Aluminum Welding Wire | 4043 Aluminum Welding Wire |
Primary Composition | Aluminum with ~5% Magnesium | Aluminum with ~5% Silicon |
Other Elements | Manganese, Chromium, Titanium | Trace amounts of Magnesium |
Melting Point | Higher | Lower |
Strength | Higher strength, suitable for structural use | Lower strength compared to 5356 |
Ductility | Good, suitable for applications requiring flexibility | Moderate |
Corrosion Resistance | Excellent, especially in marine environments | Adequate for general use |
Fluidity | Lower fluidity, requires skilled welding | High fluidity, easier to weld |
Crack Resistance | Moderate | High, especially resistant to hot cracking |
Weld Appearance | Matte finish, may require additional finishing | Smoother, shinier finish, less post-weld work |
Common Applications | Marine, automotive, structural components | Construction, aerospace, aluminum repairs |
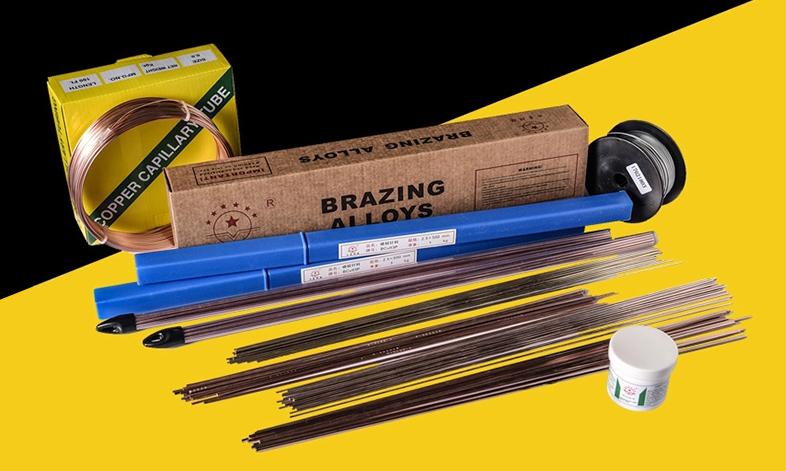
Considerations for Choosing Between 5356 and 4043
When deciding between 5356 and 4043 aluminum welding wires, several factors should be considered:
- Base Material Compatibility: Ensure that the wire is compatible with the base aluminum alloy. 5356 is generally used with 5xxx series alloys, while 4043 is more suitable for 6xxx series.
- Corrosion Resistance Requirements: If the welded part will be exposed to harsh environments, especially marine conditions, 5356 is the better choice due to its superior corrosion resistance.
- Weld Strength and Durability: For applications requiring higher strength, such as structural components, 5356 is preferred. However, if crack resistance and ease of welding are more critical, 4043 might be the better option.
- Aesthetic Requirements: If the appearance of the weld is important, especially for visible parts, 4043 provides a smoother and shinier finish with less post-weld processing.
In summary, both 5356 and 4043 wires are widely used in various industries, when selecting the right aluminum wires for your projects, please understand the differences between the two types. If you are interested in our aluminum wires products, you are welcome to contact our sales department at any time, and we will return you as soon as possible.