Aluminum profile processing annealing is divided into strip annealing and foil annealing. The purpose of annealing: eliminate cold work hardening for continuous rolling or deep processing; control the state and performance of the product; remove rolling oil and improve surface quality.
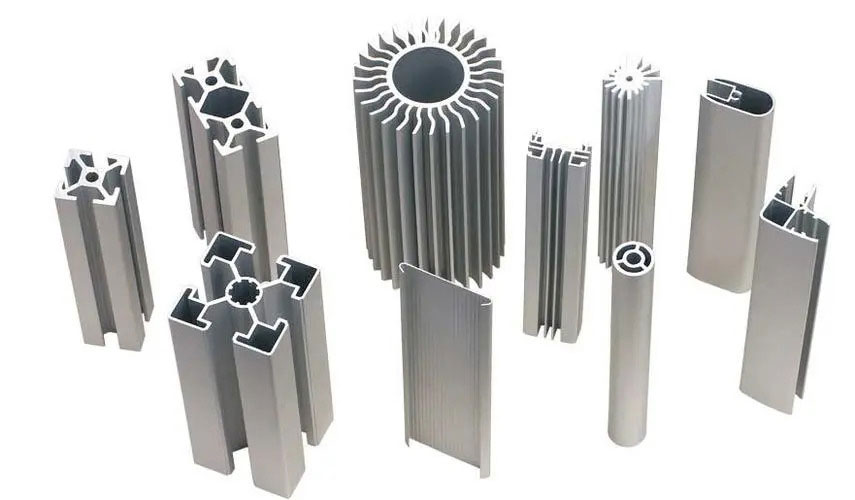
Equipment for annealing treatment of aluminum profiles
Aluminum annealing furnace is the most widely used equipment in aluminium profile processing and heat treatment. With the development of technology and the improvement of product quality requirements, higher requirements are put forward for the annealing of aluminum materials, such as the appearance quality of annealed products and the consistency of performance indicators.
The standard of the appearance quality of the annealing furnace is whether it is peeling, bubbles, oil spots, oxidation corrosion, surface finish, etc. Intrinsic quality includes mechanical properties, grain size, anisotropy, and so on.
In addition to the annealing process and equipment, the processing history of the product before annealing, such as ingredient composition, casting process, cold working rate, etc., also has an important impact on the intrinsic quality of the annealed product.
According to the production capacity and scale, aluminium annealing furnaces are divided into single annealing and annealing production lines composed of annealing furnace groups. The annealing production line is generally composed of several annealing furnaces, composite loading and unloading vehicles, out-of-furnace material tables, and cooling chambers.
The furnace body adopts a large air volume fan to circulate and heat the aluminum material. The diversion device in the furnace can effectively ensure that the airflow evenly passes through the aluminium material to make it evenly heated. The heater adopts a top-mounted integral structure, which is very convenient for disassembly and maintenance.
The furnace door is opened and closed by pneumatic pressing or mechanical transmission lifting mode. The advantage of this method is that the furnace runs smoothly and is well sealed. The fume extraction system of the furnace can effectively remove the oil film on the surface of the aluminium material and adjust the pressure in the furnace. The charging capacity of this kind of furnace is generally 10-50t.
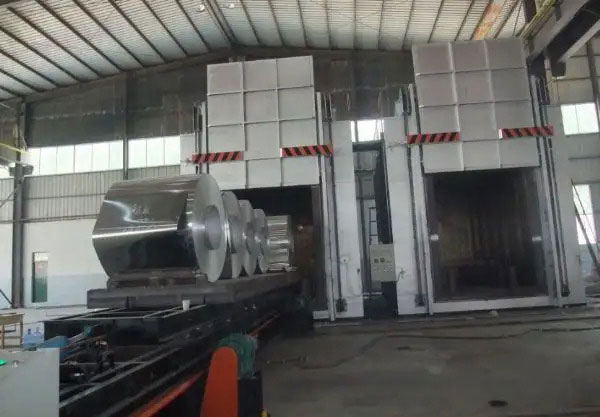
How to better complete the annealing treatment of aluminum profiles?
To improve the annealing quality of aluminum profile products, it is necessary to take improvement measures in furnace atmosphere, furnace temperature control, furnace type, and so on.
1. For annealed products with special requirements, a protective gas with very little oxygen and moisture content can be used as the atmosphere of the annealing furnace to prevent the rolling oil molecules from cracking during the volatilization process, producing hydrocarbons and free tiny carbon particles. , or oil spots on the surface of the product; at the same time, the thickness of the oxide film on the surface can be thinned, so that the product can maintain the original metallic luster after annealing.
2. When using protective gas, first heat the furnace to about 150°C, fill the furnace with protective gas after charging, and then heat the furnace. During the heating period, the oil film on the surface of the product volatilizes and is discharged from the exhaust port, and at the same time, the protective gas is supplemented to maintain the positive pressure of the furnace.
After the oil film is completely volatilized, high-temperature heating and heat preservation are carried out to recrystallize the product in a relatively short time, and then the temperature is lowered.
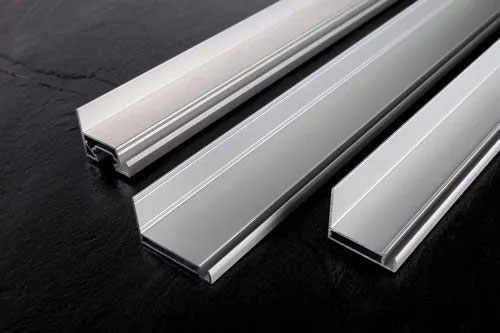
3. Vacuum annealing is a relatively new processing annealing technology for aluminium profiles. This technology prevents the cracking, oxidation, and polymerization of rolling oil molecules.
During vacuum annealing, the furnace is first pumped to a certain degree of vacuum and then heated. During the heating process, a small amount of protective gas needs to be filled to remove oil and gas, reduce the load of the vacuum pump, and accelerate the convective transfer of heat.
4. At the beginning of cooling, it is necessary to charge more protective gas than a normal operation to maintain a slight negative pressure or positive pressure in the furnace, and quickly cool down the furnace through convection fans and coolers.
The vacuum annealing furnace has strict sealing requirements, a large capacity of the vacuum pump, and high requirements for equipment. It is generally used for annealing high-purity aluminum foil of electrolytic capacitors.