A general term for aluminum-based alloys. The main alloying elements are copper, silicon, magnesium, zinc, manganese, and the secondary alloying elements are nickel, iron, titanium, chromium, lithium, etc. Aluminum alloy is the most widely used non-ferrous metal structural material in the industry and has been commonly used in aviation, aerospace, automobile, machinery manufacturing, shipbuilding, and chemical industries.
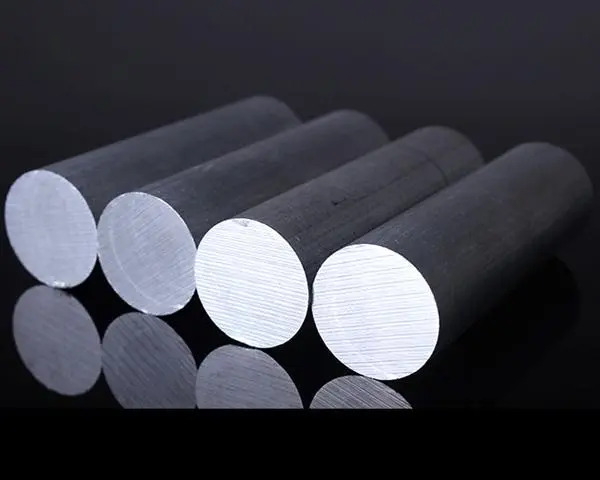
Aluminum alloy has low density, but relatively high strength, close to or surpassing high-quality steel, has good plasticity, can be processed into various profiles, has excellent electrical conductivity, thermal conductivity, and corrosion resistance, widely used in industry, second only to steel.
Aluminum alloys can be divided into ordinary aluminum alloys, ultra-high-strength aluminum alloys, heat-resistant aluminum alloys, and aluminum-based composite materials according to their properties and applications. Its application fields have different focuses, covering all application fields of aluminum alloys.
The market demand for aluminum alloys often determines the type, output, and performance characteristics of aluminum alloy products. Due to the wide variety of aluminum alloys, the development process and current situation at home and abroad are not the same. Some aluminum alloys will be used in the fields of automobiles, ships, and aerospace, so this part is classified and explained in terms of aluminum alloys.
1XXX series aluminum alloy
The main features of the 1xxx series are:
O strain hardening
O particularly high formability, corrosion resistance, and electrical conductivity
O Typical ultimate tensile strength range: 70 to 185 MPa (10-27 ksi)
O Easy connection by welding, brazing
The 1xxx series represent commercially pure (CP) aluminum from the baseline 1100 (99.00% min Al) to the relatively pure 1050/1350 (99.50% min Al) and 1175 (99.75% min Al). The 1xxx series alloys are strain hardenable but are not used when strength is the primary consideration.
The main use of the 1xxx series is in applications requiring extremely high corrosion resistance and formability (eg foils and strips for packaging, chemical equipment, tank or truck bodies, spun hollow parts, and complex sheet metal parts).
Electrical applications are one of the main uses for the 1xxx series, primarily 1350, with relatively tight controls over those impurities that can reduce conductivity. As a result, the International Annealed Copper Standard (IACS) for this material is guaranteed to be 62% electrical conductivity, which offers a cost advantage over copper in electrical applications due to the less dense and lighter weight of aluminum.
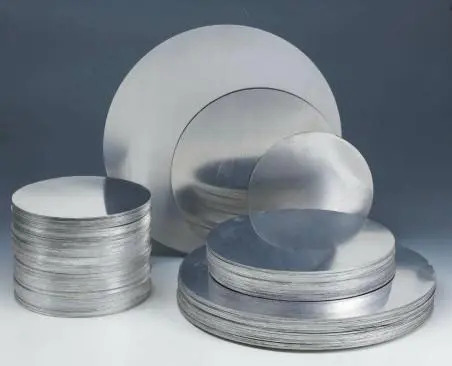
2XXX series aluminum alloy
2XXX (A1-Cu-Mg) series aluminum alloys have high tensile strength, toughness and fatigue strength, good heat resistance, processing, and welding properties, and are widely used in aerospace, automotive, and weapon industries. The main grades are 2A01, 2A02, 2A06, 2A11, 2A12, etc.
A series of alloys, such as 2024, 2124, 2524, and 2324 alloys, have been successively developed to improve strength, strength-toughness matching, and damage tolerance.
my country’s equipment models are developing in the direction of lightweight, long life, high reliability, and low cost, and have higher requirements on the fracture toughness, crack growth resistance, and corrosion resistance of the fuselage skin material.
Based on the 2024-T351 aluminum alloy thick plate, foreign countries have developed 2324, 2624, and other high damage-tolerance aluminum alloys for the lower wing surface with different strengths, toughness, fatigue, and corrosion resistance, and have achieved installed applications. We urgently need to develop high damage tolerance 2XXX series aluminum alloys. In the future, composite microalloying will be an important development direction of Al-Cu-Mg series high-strength aluminum alloys.
3XXX series aluminum alloy
3 series aluminum alloy is also called the aluminum-manganese alloy. The content of the manganese element is 1-1.5%. It is a widely used anti-rust aluminum alloy series. The strength of 3 series aluminum alloy is higher than that of pure aluminum alloy, although it cannot be heat treated to strengthen its performance. , but it has good plasticity after cold working (supercooling mill rolling) and annealing process. Because of its good corrosion resistance and welding performance, it can be used in many industries, such as the building decoration industry, electronic manufacturing industry, automobile manufacturing, etc.
The main grades commonly used in 3 series aluminum alloys are 3003 aluminum plate, 3004 aluminum plate, 3104 aluminum plate, 3005 aluminum plate, 3105 aluminum plate, etc. Among them, the largest amount of aluminum alloy is 3003. The 3003 aluminum plate is easy to process and has good rust resistance. It can be coated with color paint on the surface of the original aluminum to make various decorative curtain wall panels and indoor aluminum ceiling gussets. The tile pressing machine bends the roof color aluminum tile, which is light and durable, and its service life is better than that of steel.
The price of 3003 is cheaper than that of 5052, and the welding performance is also very good. Some truck fuel tank material manufacturers also use 3003H24 aluminum plates to replace 5052 to make partitions in the fuel tank that do not require pressure, reducing costs without affecting the use. The strength of 3004 alloy is higher than that of 3003, and the forming performance is better. It can be used as the tank body of all-aluminum cans, and as a device for chemical production and storage of liquids.
3104 alloy and 3004 alloy are very similar in composition, have high strength, and are easy to process. In the TV manufacturing industry, 3104-O state plates are often used to make TV LCD backplanes, punch convex hulls, add electronic components, and form dense oxides after molding and oxidation. The film is not only resistant to corrosion and oxidation but also has good insulation, which reduces the total weight of the finished product and ensures good heat dissipation performance.
3005 alloy is mostly used in relatively high-end color-coated aluminum coils. It is produced in the building materials industry, roof partitions, prefab houses, etc. It can also be used to make air conditioners, refrigerators and other heat sinks, internal parts, etc. 3105 alloys can be mainly used to make stamping parts such as bottle caps and caps.
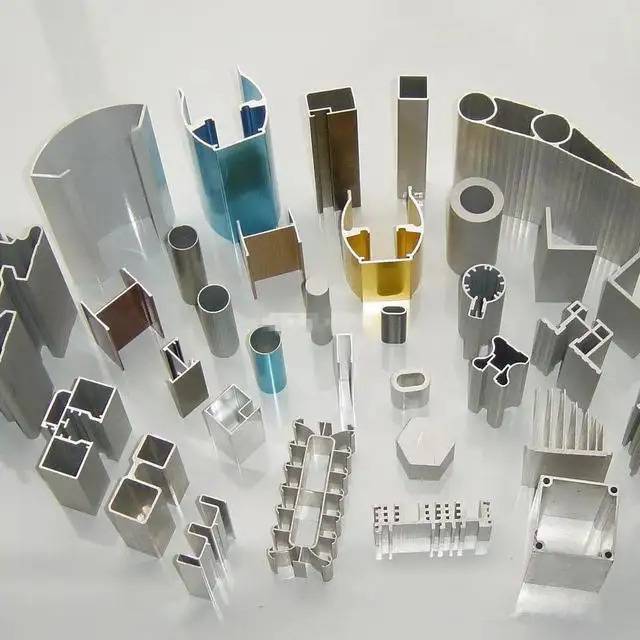
4XXX series aluminum alloy
At present, eutectic and hypoeutectic Al-Si alloys are mainly used in automobile pistons in my country, but with the continuous improvement of engine performance requirements, it is difficult to meet the performance requirements. Hypereutectic Al-Si alloys have low density, low coefficient of linear expansion, higher wear resistance, and volume stability, and are more ideal piston materials than hypoeutectic and eutectic Al-Si alloys.
Eutectic Al-Si alloy pistons have been mass-produced abroad and used in trucks and cars, such as A390 alloys in the United States, AC9A and AC8A (ZL109) alloys in Japan, and A390 alloys in Australia.
However, at present, there are very few manufacturers of eutectic Al-Si alloy pistons in my country, and most of them rely on imports. In addition, there is also a big gap between automotive turbocharged aluminum alloy materials and foreign countries, and high-performance automotive turbocharged aluminum alloy materials mainly rely on Japan and other countries. Therefore, it is imperative to develop key automotive aluminum alloy materials for high-performance pistons and turbocharged impellers.
5XXX series aluminum alloy
Al-Mg alloys, especially Al-Mg alloys with high Mg content, have high specific strength, good weldability, and corrosion resistance, and will become highly competitive materials in the fields of aerospace, high-speed trains, and oceans in the future.
6XXX aluminum alloy
The 6-series aluminum alloy is an aluminum alloy with magnesium and silicon as the main alloying elements and the Mg2Si phase as the strengthening phase. It belongs to the aluminum alloy that can be strengthened by heat treatment. The alloy has the advantages of medium strength, high corrosion resistance, no stress corrosion cracking tendency, good welding performance, unchanged corrosion performance in the welding zone, good formability, and process performance.
When the alloy contains copper, the strength of the alloy can be close to that of the 2-series aluminum alloy, and the process performance is better than that of the 2-series aluminum alloy, but the corrosion resistance deteriorates, and the alloy has good forging properties. The most widely used 6-series alloys are 6061 and 6063 alloys, which have the best comprehensive properties. The main products are extruded profiles, which are the best extruded alloys. The alloys are widely used as building profiles.
At present, 6 series aluminum alloy grades are produced: 6005, 6060, 6061, 6063, 6082, 6201, 6262, 6463, 6A02. The following is a detailed introduction to their respective uses.
The main purpose of the 6 series aluminum alloy
6005 extruded profiles and pipes are used for structural parts that require strength and height greater than 6063 alloys, such as ladders, TV antennas, etc.
6009 Auto Body Panel
6010 Sheet: Automotive Body
6061 requires various industrial structures with a certain strength, high weldability, and high corrosion resistance, such as pipes, rods, shaped materials, plate
6063 Industrial profiles, building profiles, irrigation pipes, and extruded materials for vehicles, benches, furniture, fences, etc.
6066 Forgings and Welded Structural Extrusion Materials
6070 Heavy-duty welded structures and extruded materials and pipes for the automotive industry
6101 High-strength rods, electrical conductors, and radiator materials for buses
6151 is used for die-forging crankshaft parts, machine parts, and production rolling rings, which are required to have good forge ability, high strength, and good corrosion resistance.
6201 High-strength conductive rods and wires
6205 Thick Plates, Pedals, and High Impact Extrusions
6262 Threaded high-stress parts requiring corrosion resistance better than 2011 and 2017 alloys
6351 Extruded structural parts of vehicles, pipelines for water, oil, etc.
6463 Architectural and various utensil profiles, and automotive trim parts with a bright surface after anodizing
6A02 Aircraft engine parts, forgings and die forgings with complex shapes.
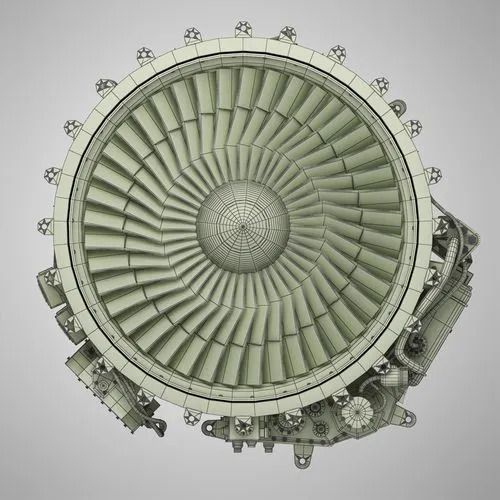
7XXX aluminum alloy
Recently, 7055 alloys (Al8Zn-2.05Mg-2.3Cu-0.16Zr) have been developed abroad, and its yield stress exceeds 620 MPa in the T77511 state, which is used for Boeing 777 aircraft, and the weight is reduced by 635 kg.
At present, my country’s aviation 7XXX series aluminum alloy lacks systematic alloy design and preparation processing technology, and some products are completely imported. Due to a large number of alloying elements, wide solidification interval, large casting stress, easy oxidation/segregation of alloy elements, etc., the metallurgical quality of the ingot is poor, and the room temperature formability is low. The development of the new 7XXX series aluminum alloy is of great importance. significance.
8. Aluminum-lithium (Al-Li) alloy
Aluminum-lithium alloy is the most rapidly developing lightweight material in aviation materials in recent years. It has the characteristics of low density, high elastic modulus, high specific stiffness, good fatigue performance, and corrosion resistance. After replacing conventional aluminum alloys, the mass can be reduced by 10%. ~20%, stiffness increased by 15%~20%.
ALCOA Corporation of the United States launched the “ALCOA Aviation 20/20 Plan” at the beginning of the 21st century, with the goal of reducing the cost and weight of aviation aluminum alloys by 20% within 20 years.
Connian Aluminium has developed 2050 and 2198 aluminum-lithium alloys (Al-Cu-Li-Mg-Ag) with low density, high toughness, and high damage tolerance properties.
There are very few Al-Li alloy grades independently developed in my country, only 1420 alloy has been applied, and the Al-Li alloy used in the C919 passenger aircraft is provided by Alcoa.
Only limited alloy grades such as 1420, 2195, 2197, and 2A97 can be produced in China, and the ingots are only flat ingots below ((310~400)×1280×4000) mm and round ingots below ϕ650 mm.
For high-end aerospace applications, flat ingots (2B16) with a thickness of more than 60 mm and a width of more than 1500 mm, and ingots with a diameter of more than 1500 mm (2B16) have not yet achieved industrial production. Therefore, it is of great significance to develop new aluminum-lithium alloy designs, super-sized ingot preparation, and deep processing technology.