Aluminum welding, widely used in industries like automotive, aerospace, and construction, demands precision and expertise. However, it presents unique challenges compared to other metals, particularly due to its high thermal conductivity and reactivity with oxygen. One crucial aspect of successful aluminum welding is the proper selection and use of filler metals. By understanding the common mistakes associated with aluminum filler metals and effective tips to avoid them, welders can significantly improve the quality and efficiency of their work.
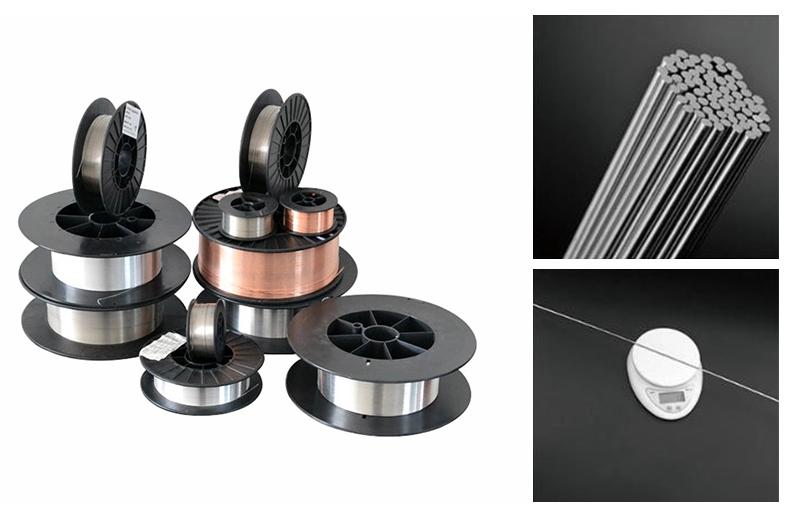
What are Aluminum Filler Metals?
Aluminum filler metals are essential in welding, as they join aluminum components together while maintaining the structural and functional integrity of the base metal. These filler metals are available in various forms, such as rods and wires, and are designed to provide compatibility with specific aluminum alloys.
Types of Aluminum Filler Metals
Different aluminum filler metals are suited to different applications, with popular types including:
- 4043 Aluminum Filler Metal: Known for its fluidity and ease of use, 4043 is commonly chosen for general-purpose aluminum welding. It provides good crack resistance and is suitable for cast aluminum and wrought alloys.
- 5356 Aluminum Filler Metal: This filler metal is often selected for high-strength applications and is popular in marine and automotive industries. It’s corrosion-resistant, but less fluid than 4043, requiring more control during welding.
- 4047 Aluminum Filler Metal: With a high silicon content, 4047 is ideal for applications that demand minimal thermal expansion. It also offers better flow and is commonly used in heat-sensitive projects.
Considerations When Choosing Aluminum Filler Metals
Choosing the correct aluminum filler metal involves considering factors such as:
- Base metal composition: The filler metal should be compatible with the base metal alloy to ensure proper fusion and weld quality.
- Welding process: Different welding processes, such as TIG, MIG, and GTAW, may require specific filler metal types and sizes.
- Desired mechanical properties: The filler metal should be selected to meet the required strength, ductility, and corrosion resistance of the weld.
Understanding the types and purposes of aluminum filler metals is foundational to achieving high-quality welds. By selecting a filler metal suited to the application, welders can reduce the risk of issues like cracking and incompatibility, enhancing both durability and appearance.
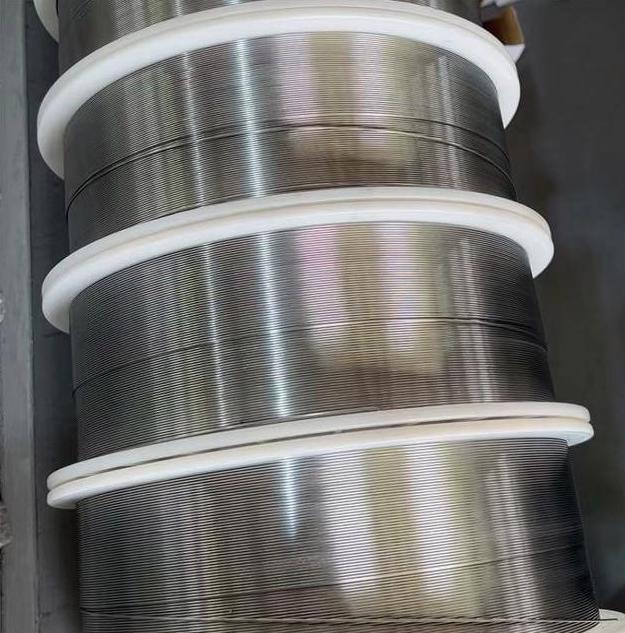
Common Mistakes When Using Aluminum Filler Metals
Even experienced welders can make common mistakes when using aluminum filler metals, leading to weak joints, porosity, or poor aesthetics. Recognizing these pitfalls is key to improving welding outcomes and avoiding costly rework.
Mistake 1: Choosing the Wrong Filler Metal
Many welders overlook the importance of matching filler metal to base metal. Incompatible filler metals can lead to welds that are prone to cracking or corrosion. Always refer to compatibility charts and guidelines to select a filler metal that complements the aluminum alloy you’re welding.
Mistake 2: Inadequate Cleaning and Surface Preparation
Aluminum is highly susceptible to oxidation, which can hinder the bonding process. Failure to clean the aluminum surface properly allows contaminants to interfere with the weld, resulting in porosity or weak joints. Prior to welding, remove any oxide layer and clean the surface with an aluminum-specific solvent or brush.
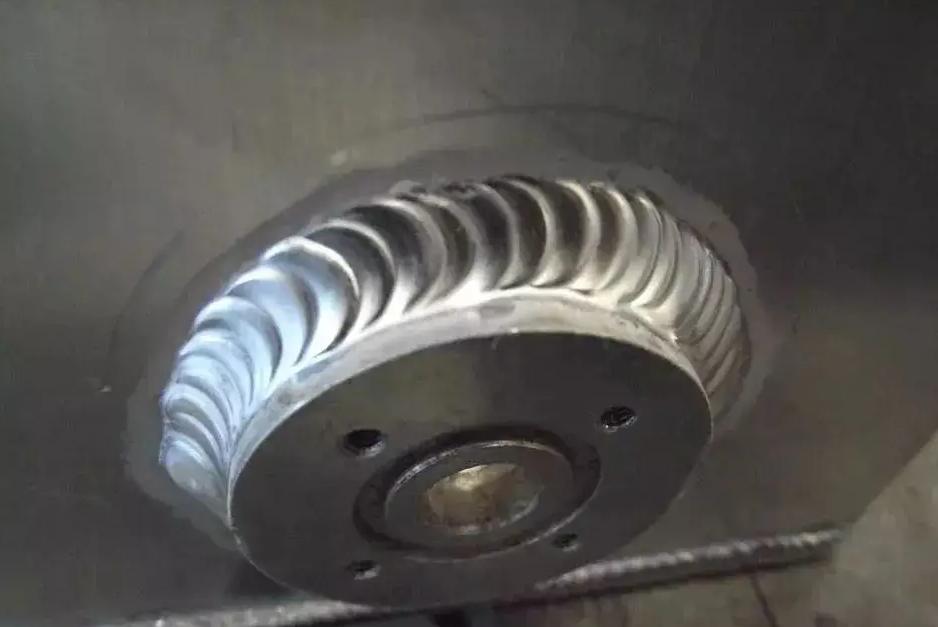
Mistake 3: Improper Storage and Handling of Filler Metals
Aluminum filler metals are sensitive to moisture and contamination. Storing them in a humid or unclean environment can lead to oxidation or dirt buildup, reducing weld quality. Store filler metals in sealed, dry containers, and avoid touching them with bare hands to minimize oil transfer.
Mistake 4: Incorrect Welding Technique
Common technique errors include using the wrong torch angle, travel speed, or excessive heat. These mistakes can cause issues like burn-through, poor penetration, and excessive spatter. Adjust your technique based on the filler metal type and the thickness of the aluminum, and consider pulse welding for improved control.
Mistake 5: Ignoring Heat Control
Aluminum conducts heat quickly, which can lead to warping, cracking, or burn-through. Managing heat input is essential; overheating not only affects the filler metal but also weakens the base metal. Using techniques such as pulse welding, intermittent cooling, or welding in short bursts can help manage heat effectively.
Avoiding these common mistakes with aluminum filler metals helps improve weld quality, durability, and aesthetics. Awareness and prevention of these issues will contribute to stronger, longer-lasting welds and reduce the need for costly rework.
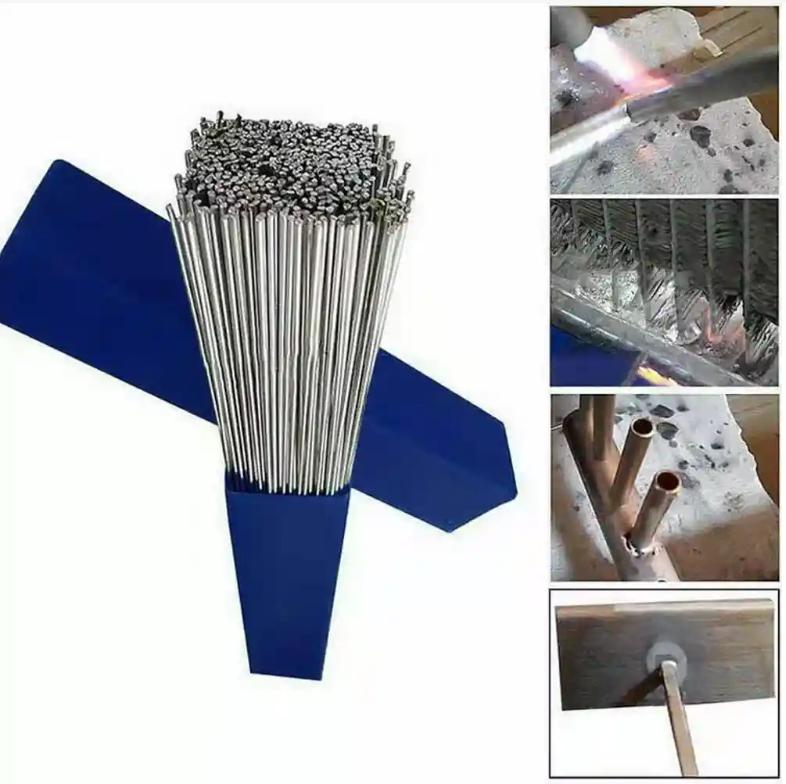
Tips for Successful Aluminum Welding
Achieving a high-quality aluminum weld requires not only the right filler metal but also attention to technique and preparation. Here are practical tips to help welders avoid common pitfalls and improve their aluminum welding results.
Tip 1: Choose the Right Filler Metal
Selecting the appropriate filler metal ensures a strong, compatible bond with the base metal. Consider the alloy composition, corrosion resistance, and desired strength. Consult filler metal compatibility charts or inquire about the experienced manufacturer who can assist in making an informed choice.
Tip 2: Prepare the Surface Thoroughly
Aluminum surfaces should be free of oxides, grease, and other contaminants. Use a stainless steel brush specifically for aluminum, and avoid cross-contamination by cleaning the work area and equipment. Even minor impurities can weaken the weld and lead to porosity.
Tip 3: Store Filler Metals Properly
Moisture exposure leads to oxidation, which compromises filler metals. Store filler metals in a dry, sealed container, and handle them with clean gloves to avoid introducing oils. Proper storage extends the filler metal’s lifespan and maintains its performance.
Tip 4: Use the Right Welding Equipment and Settings
Aluminum welding often requires specialized equipment settings. Use AC (alternating current) for TIG welding aluminum, and adjust the power settings to suit the metal’s thickness. Consider using pulsed settings to manage heat input, which is crucial for preventing warping and cracking.
Tip 5: Control Heat Input Carefully
Aluminum’s high thermal conductivity can lead to distortion or burn-through if overheated. Pulse welding, working in short passes, and cooling techniques such as using a heat sink or air cooling can prevent excessive heat buildup and maintain weld integrity.
Tip 6: Practice and Test
Welding aluminum takes practice. Set up test welds on scrap pieces to refine your technique, test different filler metals, and adjust equipment settings. Practicing on similar materials before the final project improves confidence and helps identify potential issues.
Avoiding common mistakes with aluminum filler metals in welding requires attention to detail, knowledge of materials, and proper technique. By understanding filler metal types, avoiding common errors, and following expert tips, welders can consistently achieve strong, reliable welds.