Aluminum foil plays a critical role in the manufacturing and performance of batteries. As an essential component, it contributes to the structural integrity, electrical conductivity, and overall efficiency of various battery types. From lithium-ion to lead-acid batteries, aluminum foil is utilized for its unique properties and versatility in meeting the specific demands of different battery chemistries. Understanding the manufacturing process and the different types of aluminum foil used in batteries can shed light on its significance and impact on battery performance.
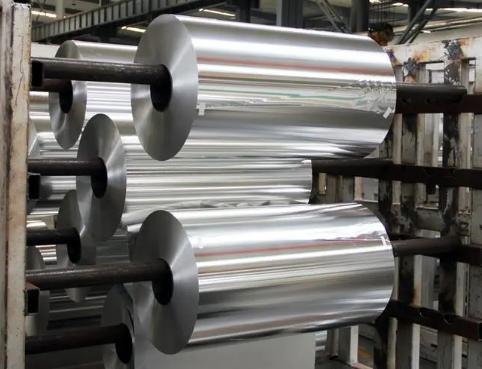
Manufactured Process of Battery Aluminum Foil
Aluminum foil used in battery applications is manufactured through a multi-step process that involves several stages of rolling, annealing, and finishing. Here is a general overview of the manufacturing process for aluminum foil used in batteries:
- Casting: The process begins with the casting of aluminum ingots or billets. Aluminum is melted in a furnace and cast into large rectangular blocks or cylindrical shapes. These blocks are called “slabs” or “logs.”
- Hot Rolling: The slabs or logs are heated and passed through a series of rolling mills. The rolling process gradually reduces the thickness of the aluminum while increasing its length and width. This initial hot rolling is done at high temperatures to make the aluminum more malleable.
- Cold Rolling: After hot rolling, the aluminum strip undergoes a process called cold rolling. It is passed through additional rolling mills at room temperature to further reduce the thickness and improve the surface finish. Cold rolling helps achieve the desired foil thickness and tight tolerances.
- Annealing: The cold-rolled aluminum strip is annealed to enhance its mechanical properties. Annealing involves heating the strip to a specific temperature and then slowly cooling it. This process helps relieve internal stresses and improves the foil’s flexibility and strength.
- Finishing: The annealed aluminum strip is trimmed to the desired width and length, and the edges are smoothed to ensure uniformity. The foil may undergo additional treatments, such as surface texturing, coating, or lamination, depending on the specific battery application requirements.
- Quality Control: Throughout the manufacturing process, strict quality control measures are implemented to ensure the foil meets the desired specifications. Various tests, such as thickness measurements, surface inspections, and conductivity checks, are performed to verify the quality of the foil.
- Slitting and Packaging: The finished aluminum foil is typically slit into narrower rolls of the desired width to meet customer requirements. The foil rolls are then packaged, often in protective packaging materials, to prevent damage during storage and transportation.
It’s important to note that the manufacturing process may vary depending on the specific requirements of battery aluminum foil.
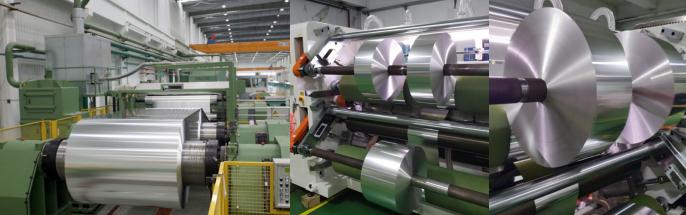
Common Types of Battery Aluminum Foil
Different types of aluminum foils can be used in batteries, depending on the specific battery chemistry, design, and application requirements. Here are some common types of aluminum foils used in batteries:
- Plain Aluminum Foil: This is the basic type of aluminum foil used in batteries. It is typically a high-purity aluminum foil without any additional coatings or treatments. Plain aluminum foil provides good electrical conductivity and mechanical support to the electrodes.
- Coated Aluminum Foil: In some cases, aluminum foil used in batteries may be coated with a thin layer of other materials. For example, a carbon coating may be applied to improve conductivity, enhance the adhesion of active materials, and increase the surface area for electrochemical reactions. Polymer coatings can also be used to enhance chemical stability, prevent oxidation, or provide barrier properties.
- Textured or Roughened Aluminum Foil: Texturing or roughening the surface of aluminum foil can increase the available surface area for electrochemical reactions. This type of aluminum foil is commonly used in batteries where maximizing the electrode/electrolyte interface is crucial, such as lithium-ion batteries. The increased surface area facilitates faster ion transport and enhances the battery’s capacity and power output.
- Ultra-Thin Aluminum Foil: In some battery applications, ultra-thin aluminum foil is used to reduce the overall weight and thickness of the battery. These foils can have thicknesses in the range of a few micrometers or less. Ultra-thin aluminum foil enables the production of lightweight and flexible batteries, making them suitable for portable devices and applications where space constraints are important.
- Laminated Aluminum Foil: Laminated aluminum foil consists of multiple layers of aluminum foil bonded together with adhesive or other materials. This type of foil is used in certain battery designs where improved mechanical strength and stability are required. Laminated aluminum foil can provide enhanced protection against punctures, tears, or deformation during battery assembly and operation.
It’s important to note that the choice of aluminum foil type depends on factors such as the specific battery chemistry, electrode materials, manufacturing process, and desired performance characteristics. Different battery technologies, such as lithium-ion, lead-acid, nickel-based, or other emerging battery systems, may have specific requirements for the type of aluminum foil used.
As battery technologies continue to advance, the demand for high-quality aluminum foil will persist. Ongoing research and development efforts aim to optimize the manufacturing process, explore innovative foil designs, and enhance the performance of batteries across various industries and applications. Additionally, sustainable practices, such as recycling aluminum foil from used batteries, contribute to reducing the environmental impact and promoting a circular economy.
Understanding the manufactured process and the common types of aluminum foil used in batteries provides valuable insights into the intricacies of battery technology. By focusing on the development and improvement of battery aluminum foil, researchers, manufacturers, and engineers can contribute to the advancement of battery performance, energy storage capabilities, and the overall sustainability of battery systems.