Aluminum compressed air piping is commonly used in industrial settings due to its lightweight properties, corrosion resistance, and durability. However, proper maintenance is essential to ensure the system operates efficiently, prolongs its lifespan, and provides clean, high-quality compressed air for downstream equipment and processes. Here’s why maintaining aluminum compressed air pipes is critical, along with practical steps for upkeep and handling emergencies.
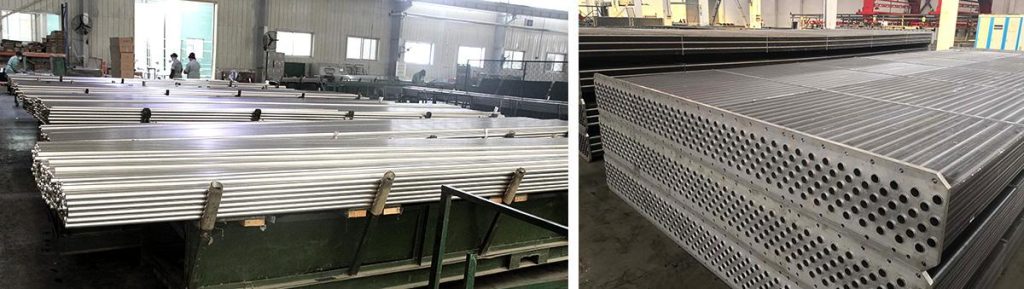
Why Should You Maintain Aluminum Compressed Air Piping?
Regular maintenance of aluminum pipes for air compressor lines is not just a matter of convenience but is essential for several reasons. Let’s examine the key reasons in detail.
1. Ensuring the Quality of Compressed Air
Compressed air quality is a vital aspect of any system because it directly impacts the performance of downstream equipment and the quality of products produced. Aluminum compressed air piping can accumulate impurities, oil residue, or water vapor over time, which can:
- Contaminate the air being transported
- Lower the efficiency of machinery that uses compressed air
- Compromise product quality in industries like food, pharmaceuticals, or electronics where clean, dry air is essential
By regularly cleaning the aluminum piping, you can prevent the buildup of such contaminants, ensuring the air quality remains high.
2. Increasing System Efficiency
Over time, dust, dirt, and other impurities can build up inside aluminum compressed air pipes. This buildup increases frictional resistance within the system, causing the compressor to work harder to maintain the same level of pressure. This results in:
- Increased energy consumption
- Reduced overall system efficiency
Regular cleaning and maintenance of the piping system reduce the frictional resistance, leading to smoother airflow and lower energy consumption. This results in both cost savings and a more energy-efficient system.
3. Extending the Lifespan of Piping
Corrosion, though less common in aluminum piping compared to other materials like steel, is still a potential issue, especially in harsh environments or where moisture accumulates. Corroded pipes can:
- Lead to leaks
- Reduce the system’s performance
- Eventually require costly replacements
Proper cleaning and maintenance can prevent or slow down corrosion, ensuring the longevity of the aluminum compressed air piping system.
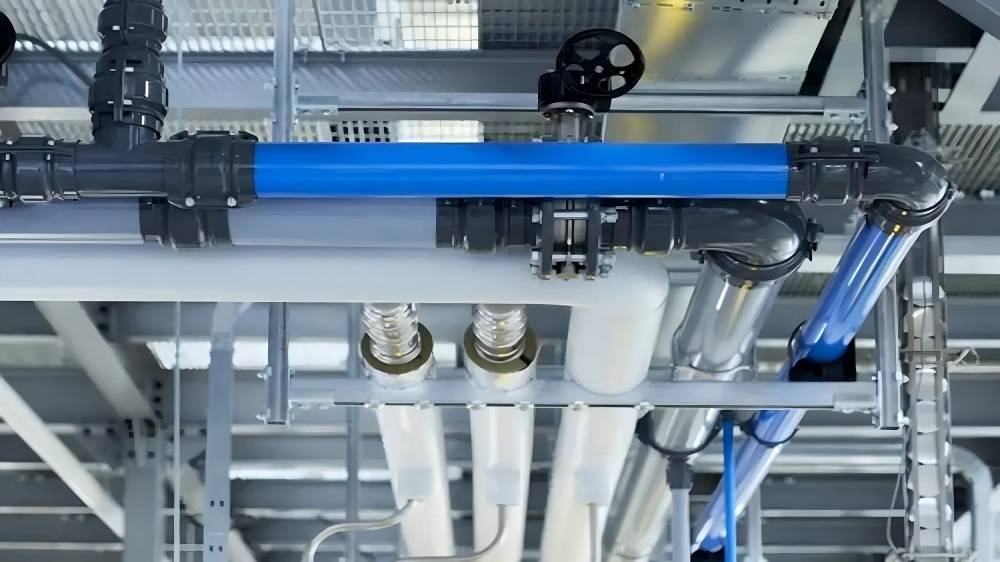
Methods for Maintaining Aluminum Compressed Air Piping
Proper maintenance involves regular inspections, cleaning, rust removal, and, when necessary, replacement. Let’s dive into each step of the maintenance process.
1. Regular Inspections
Routine inspections are the first line of defense in maintaining the health of aluminum compressed air tubing. These checks should include the following:
- Visual Inspection: Regularly check the surface of the pipes for cracks, deformation, or signs of corrosion.
- Connection Points: Inspect all fittings and connections to ensure they are tightly secured and free from leaks. Over time, joints may loosen or degrade, leading to air loss and system inefficiencies.
- Support Points: Examine the pipe supports and hangers to make sure they are firmly in place. Sagging pipes can lead to increased stress at the joints, increasing the likelihood of leaks or breakage.
2. Cleaning
Cleaning aluminum compressed air tubing is an essential part of regular maintenance, and it should be done thoroughly and carefully to avoid damage.
- Shut Down the System: Before starting the cleaning process, the entire compressed air system should be turned off to avoid any accidents.
- Choose the Right Cleaning Agent: When cleaning aluminum pipes, it is crucial to use a non-corrosive cleaning agent specifically designed for aluminum. Harsh chemicals can cause corrosion or weaken the material, so select cleaners that are safe for use on aluminum.
- Cleaning Methods: High-pressure water guns, compressed air, or specially designed brushes can be used to clean the interior of the pipes. These methods effectively remove dirt, oil residue, and other contaminants from the surface of the pipes.
- Drying: After cleaning, it is essential to dry the interior of the pipes thoroughly. Any remaining moisture can lead to corrosion over time.
3. Rust Removal and Corrosion Prevention
Though aluminum is resistant to rust, it can still corrode under certain conditions, such as prolonged exposure to moisture. If any signs of corrosion are found, the following steps should be taken:
- Rust Removal: If rust or corrosion is detected, it is vital to remove it promptly. This can be done through mechanical methods, such as using a wire brush or chemical treatments designed for aluminum.
- Corrosion Prevention: After removing the rust, apply a protective coating to prevent further corrosion. This can include anti-corrosion paint or other sealants specifically designed for aluminum surfaces.
4. Replacing Damaged Pipes
Despite regular maintenance, some aluminum compressed air pipes may become too damaged to repair. In such cases, replacement is the best option. Here’s what to keep in mind:
- Severe Damage: If a pipe shows signs of severe wear or has multiple cracks or leaks, it should be replaced immediately. Attempting to repair significantly damaged pipes can be both unsafe and inefficient.
- Scheduled Replacement: For older piping systems, even if there is no visible damage, it is a good practice to replace the pipes after a certain period of use to avoid unexpected failures and ensure optimal performance.
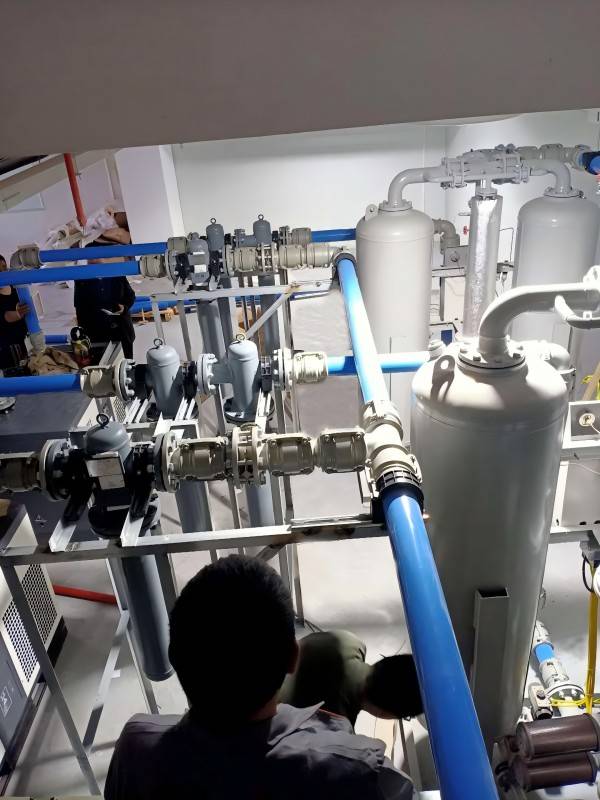
Emergency Actions When Aluminum Compressed Air Piping Fails
When a failure occurs in the aluminum compressed air piping system, immediate action is essential to mitigate risks and restore functionality.
- Safety First: Ensure the safety of personnel by shutting down valves to cut off the air supply in the event of a leak. This prevents backflow or over-pressurization of the system.
- Immediate Reporting: Operators should promptly report the issue to supervisors or relevant personnel, providing details about the failure and its impact.
- Initiate Emergency Procedures: Depending on the severity and scope of the failure, emergency protocols should be activated. Notify maintenance teams and prepare necessary responses.
- On-Site Assessment: The shift supervisor or relevant authority should quickly assess the situation on-site and communicate with higher management for swift decision-making.
- Temporary Solutions: While waiting for repairs, consider implementing temporary fixes to ensure safety, such as switching to backup equipment or adjusting system pressures.
- Prevent Secondary Accidents: During emergency repairs, follow safety protocols closely to avoid secondary accidents like electrical short circuits or further pipe ruptures.
- Troubleshooting and System Recovery: Once the issue is resolved, carefully restart the compressed air system following standard procedures. Inspect the affected production lines to ensure no safety risks remain before resuming normal operations.
- Root Cause Analysis: After handling the incident, conduct a thorough analysis of the failure to identify its root cause. Develop preventive measures and integrate them into routine maintenance practices to enhance future emergency response readiness.
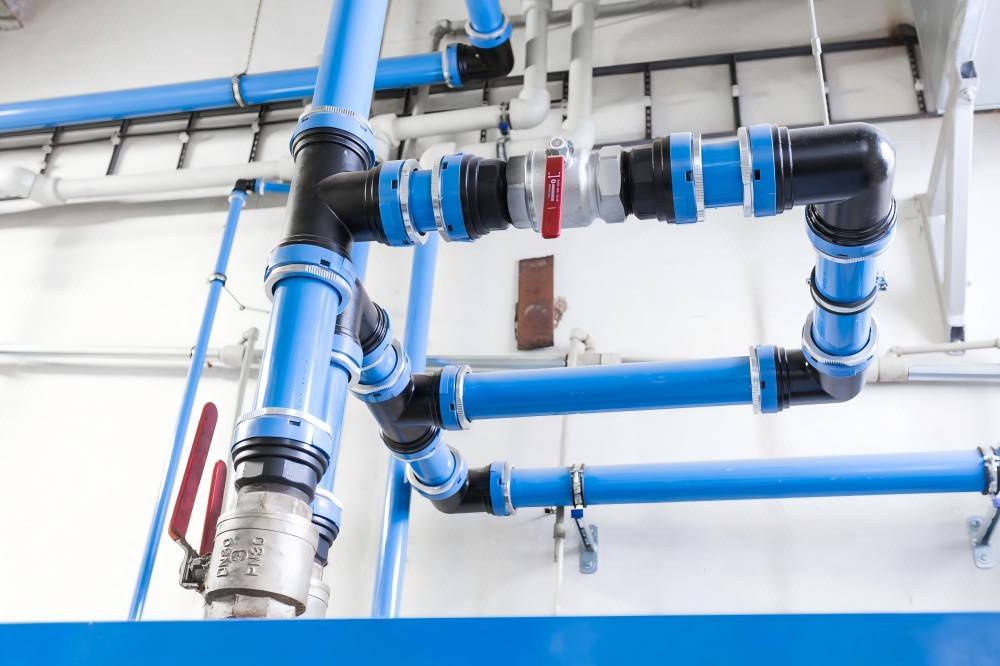
As mentioned above, aluminum compressed air piping systems offer excellent durability and performance when properly maintained. Regular inspections, cleaning, rust removal, and timely replacements can greatly enhance the efficiency and longevity of these systems. By following the outlined maintenance procedures and being prepared for emergencies, industries can ensure the optimal operation of their compressed air systems and avoid costly downtime or accidents.