Additive Manufacturing (AM), often referred to as 3D printing, is a transformative approach to industrial production. This process allows for the creation of complex parts and structures layer by layer, directly from digital models. A key component of this technology is the use of metal powders, which have revolutionized industries by enabling the production of high-strength, durable, and intricate parts. Among the various metal powders used in AM, bronze metal powders stand out for their unique combination of properties and applications.
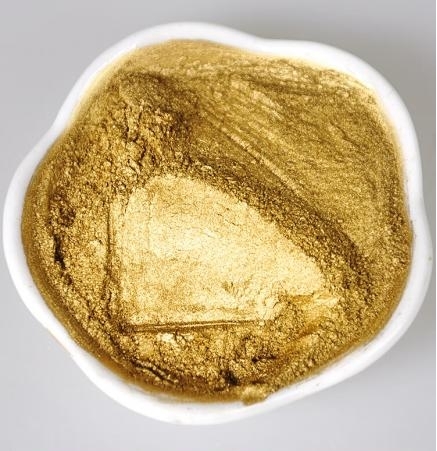
Why Use Metal Powders in Additive Manufacturing?
Additive manufacturing relies on the layer-by-layer deposition of materials to create objects directly from digital models. Metal powders are preferred in AM due to their ability to produce high-density, structurally sound components with fine details. They enable the fabrication of parts with complex geometries that would be difficult or impossible to achieve with traditional manufacturing methods.
Properties of Bronze Metal Powder
Bronze is an alloy primarily consisting of copper, with tin as the main additive, along with other elements like aluminum, manganese, or nickel. This combination gives bronze several advantageous properties:
- Particle Size and Shape: Bronze metal powders typically have a spherical shape, promoting good flowability and packing density. Particle sizes can range from a few micrometers to hundreds of micrometers, depending on the application.
- Mechanical Properties: Bronze exhibits high tensile strength, excellent hardness, and good ductility, making it suitable for robust applications.
- Physical Properties: Bronze is known for its excellent corrosion resistance, low friction, and thermal and electrical conductivity.
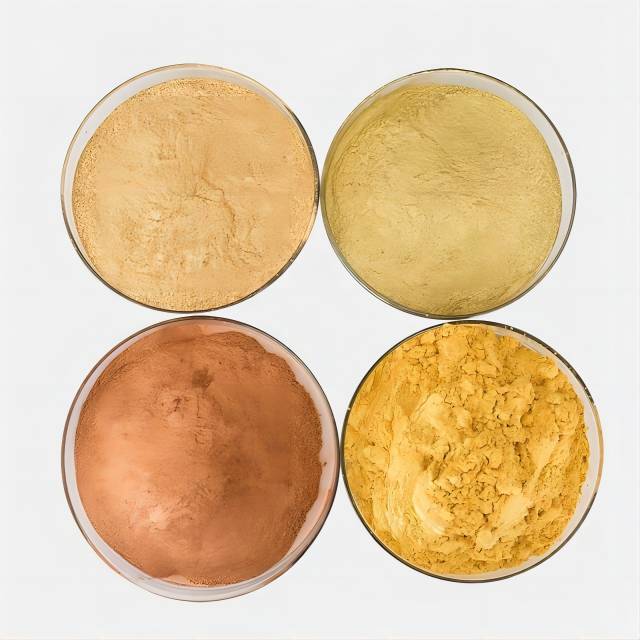
Advantages of Using Bronze in AM
Using bronze metal powder in additive manufacturing presents several advantages:
- Complex Geometries: Bronze powder allows for the creation of intricate and detailed designs that are difficult to achieve with traditional manufacturing. The flexibility of AM enables the production of customized components tailored to specific needs.
- Reduced Waste: Additive manufacturing with bronze powder minimizes material waste compared to subtractive methods.
- Rapid Prototyping: Bronze powder facilitates quick production of prototypes, speeding up the design and development process.
- Cost-Effectiveness: Bronze is relatively affordable compared to other metal powders, The efficiency and precision of AM with bronze powder can lead to cost savings in material usage and production time.
- Aesthetic Appeal: Bronze has a distinct, attractive appearance, which is highly valued in art, jewelry, and decorative items.
- Durability and Corrosion Resistance: Bronze’s resistance to corrosion and wear makes it ideal for components exposed to harsh environments.
- Thermal and Electrical Conductivity: These properties make bronze suitable for applications requiring efficient heat dissipation or electrical conduction.
Metal powders are crucial in additive manufacturing for their versatility and precision, with bronze metal powder offering unique properties and advantages. Leveraging these properties, various techniques are employed to optimize the use of bronze in additive manufacturing.
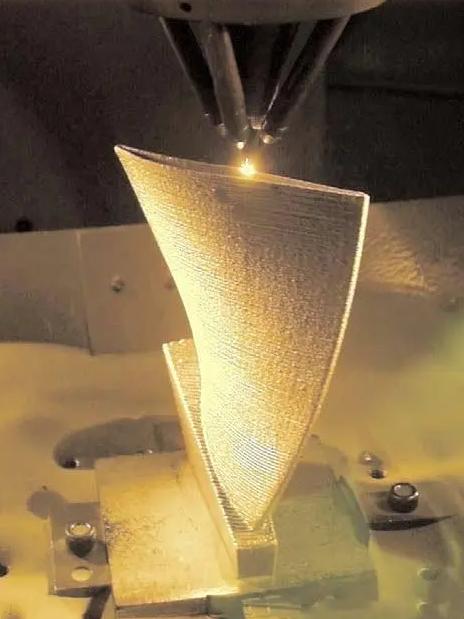
Techniques for Additive Manufacturing with Bronze Powder
Several AM techniques can be employed with bronze metal powder, each offering unique benefits and capabilities:
- Selective Laser Melting (SLM): This technique uses a high-power laser to selectively melt and fuse powder particles layer by layer. SLM is known for producing high-density parts with excellent mechanical properties.
- Direct Metal Laser Sintering (DMLS): Similar to SLM, DMLS involves using a laser to sinter metal powder. It allows for the production of complex geometries and is widely used in the aerospace and medical industries.
- Electron Beam Melting (EBM): EBM uses an electron beam to melt metal powder in a vacuum environment. It is particularly effective for high-temperature materials and produces parts with high density and excellent mechanical properties.
- Binder Jetting: This technique involves depositing a liquid binding agent onto a bed of metal powder, layer by layer. The bound part is then sintered in a furnace. Binder jetting is valued for its high production speed and ability to create large parts.
Applications of Bronze Metal Powder in AM
Bronze components produced through AM find applications in various industries:
Industry | Application | Representative Parts |
Aerospace | High-strength, durable components | Bushings, bearings, gears |
Automotive | Efficient, long-lasting components | Connectors, bushings |
Medical | Biocompatible implants and prosthetics | Medical implants, prosthetic devices |
Decorative and Artistic | Aesthetic and customized designs | Jewelry, sculptures, decorative items |
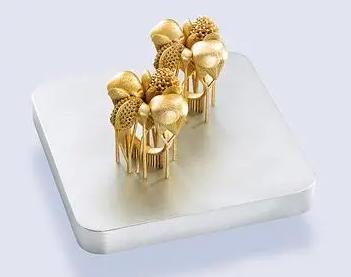
Get Bronze Metal Powder from CHAL
When sourcing bronze metal powder for additive manufacturing, quality and reliability are crucial. CHAL is a leading provider of high-quality metal powders, including bronze. CHAL’s bronze metal powders are produced using state-of-the-art techniques to ensure uniform particle size, shape, and composition, meeting the stringent requirements of various AM applications.
CHAL ensures the highest purity levels in their bronze powders, resulting in superior mechanical properties and performance. Advanced production processes guarantee consistent particle size and shape, crucial for reliable AM outcomes. By choosing CHAL for bronze metal powder, manufacturers can enhance their additive manufacturing processes, achieving high-quality, reliable, and cost-effective results across a range of applications.
In conclusion, bronze metal powder plays a significant role in additive manufacturing, offering unique properties and advantages that benefit various industries. With the support of suppliers like CHAL, the potential for innovation and efficiency in AM continues to expand, paving the way for new possibilities and advancements.