Aluminum alloys, prized for their lightweight, high strength-to-weight ratio, and corrosion resistance, have become indispensable in industries such as aerospace, automotive manufacturing, and rail transportation. However, challenges like oxide film formation, porosity, and hot cracking often plague aluminum welding processes. The choice of welding wire directly determines joint performance and process feasibility. For instance, a new energy vehicle battery tray manufacturer reduced porosity rates from 15% to below 3% by switching to a compatible wire. This article systematically explores how to select aluminum welding wires based on material properties, matching principles, and process controls.
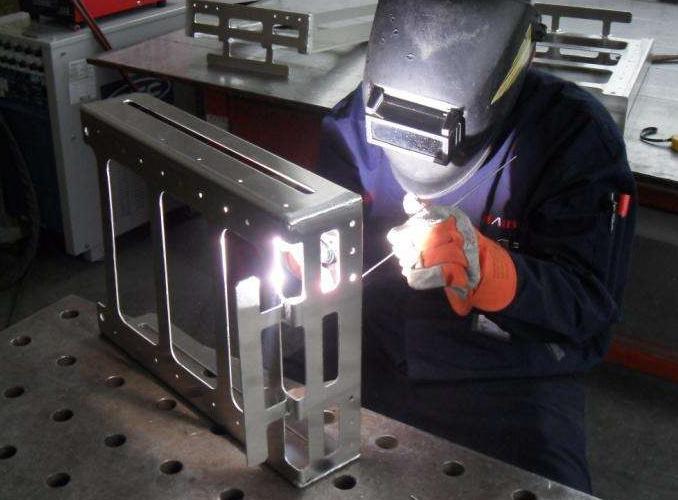
Why Choosing the Right Wire Matters
The welding wire acts not only as filler metal but also as a critical medium for regulating weld composition, mechanical properties, and corrosion resistance. Using the correct wire minimizes these risks and ensures compatibility with the base metal, leading to a seamless and reliable weld.
Consequences of Incorrect Wire Selection:
- Strength Loss: Insufficient strength to hold under stress. For example, using ER4043 wire to weld 7005 aluminum alloy can reduce weld tensile strength from 350 MPa (base metal) to 240 MPa.
- Corrosion Risks: Mismatched wire and base metal (e.g., 5XXX vs. 2XXX alloys) may accelerate electrochemical corrosion by over 500%.
- Process Failures: Incompatible wires can cause a lack of fusion or hot cracking, increasing rework rates by 30%.
Economic Impact: A rail transport company reduced welding costs by 18% and boosted productivity by 25% through optimized wire selection.
Wire selection is the first line of defense for weld quality, impacting product lifespan and production costs.
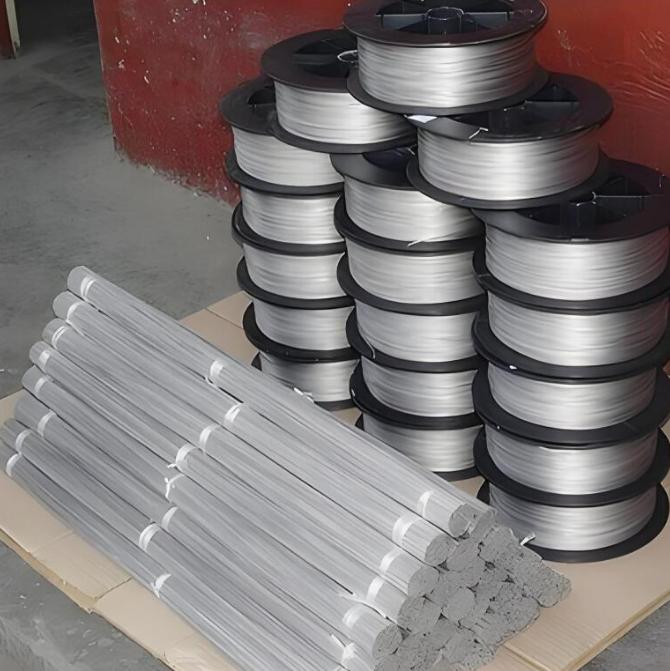
Key Factors in Selecting Aluminum Welding Wire
1. Material Composition Compatibility
Silicon (Si) vs. Magnesium (Mg) Balance:
- Silicon: ER4043 (5% Si) reduces molten pool fluidity, ideal for 6000-series alloys (e.g., 6061), but sacrifices ductility.
- Magnesium: ER5356 (5% Mg) enhances strength and corrosion resistance for 5000/7000-series alloys but requires precise heat input to avoid porosity.
2. Base Metal Alloy Series: The most crucial factor is the specific aluminum alloy being welded. Different alloys have varying chemical compositions and mechanical properties, requiring compatible filler metals to achieve a strong and sound weld. Some recommendations are:
Base Alloy Series | Recommended Wire | Matching Principle |
1000 Series | ER1100 | Purity alignment (99% Al) |
5000 Series | ER5356 | Mg content synchronization (5-6%) |
6000 Series | ER4043 | Si compensates for Mg-Si compound loss |
3. Welding Process: The chosen welding process (MIG or TIG) can influence wire selection. MIG welding typically uses a continuously fed wire, while TIG welding uses a separate filler rod.
4. Weld Joint Design: The geometry of the weld joint, including its thickness and configuration, affects the amount of filler metal required and the appropriate wire diameter.
5. Service Conditions: Consider the intended service environment of the welded component. Factors like temperature, corrosive atmospheres, and stress levels can influence the choice of a wire with specific properties. In cryogenic conditions, prioritize ER5183 (4% Mg), which retains toughness at -196°C. In corrosive environments, ER5356 outperforms ER4043 in salt spray resistance (40% lower weight loss).
6. Desired Weld Properties: The desired characteristics of the weld, such as strength, ductility, corrosion resistance, and color match, will guide the selection of the appropriate filler metal.
Composition, process, and environmental factors need to be considered to ensure that the weld meets specific requirements.
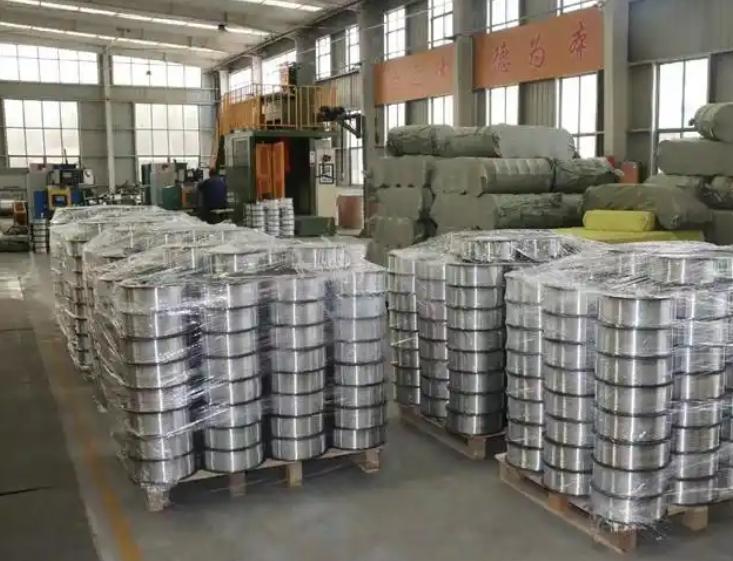
Common Aluminum Welding Wire Types
Aluminum welding wires are categorized by their alloy designation, similar to the base metals they are designed to weld. Understanding the common wire types and their characteristics is essential for proper selection. Some of the most frequently used aluminum welding wires include:
Type | Composition (%) | Key Properties | Typical Applications |
ER1100 | 99.0 Al | High purity, low strength | 1060 alloy containers |
ER4043 | 5 Si | Crack resistance, high fluidity | 6061 automotive parts |
ER5356 | 5 Mg | High strength, corrosion resistance | 5083 ship decks |
ER5183 | 4.5 Mg | Cryogenic toughness | LNG storage tanks |
Other Specialized Wires:
- 4045 aluminum welding wire: Used for brazing and cladding applications.
- 5554 aluminum welding wire: Designed for welding 5xxx series alloys with higher magnesium content.
- 2319 aluminum welding wire: Compatible with 2xxx series alloys, offering high strength for aerospace applications.
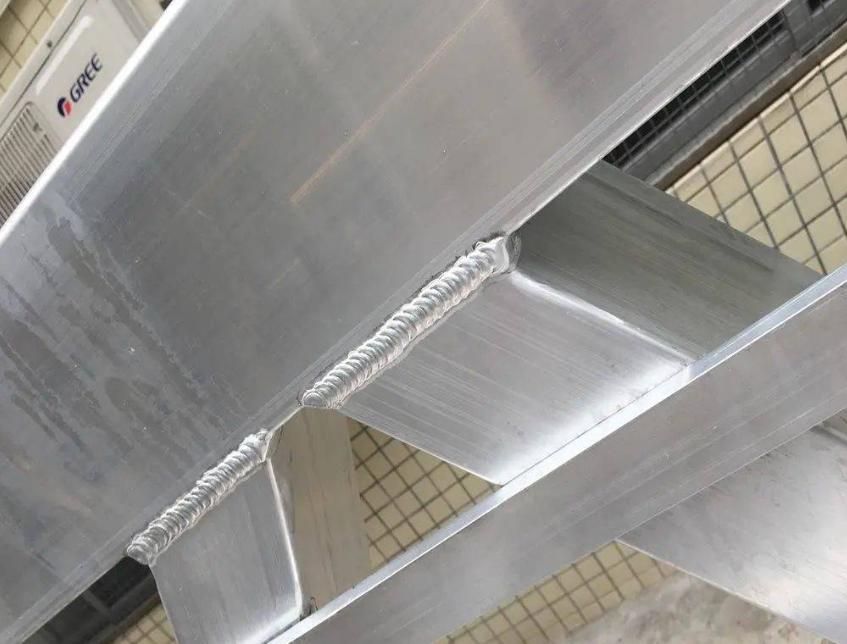
Matching Wire to Alloy: The Key to Success
Selecting the right wire for your aluminum alloy ensures a strong, defect-free weld. Here’s how to match them effectively:
Matching by Alloy Series
- 1XXX Series (Pure Al): ER1100 ensures purity alignment; impurities degrade conductivity.
- 5XXX Series (Al-Mg): ER5356/ER5183 with ≤0.5% Mg deviation from base metal.
- 6XXX Series (Al-Mg-Si): ER4043 or ER5356 compensates for Mg-Si compound loss.
Dissimilar Alloy Welding
- 5052 (Al-Mg) + 6061 (Al-Mg-Si): ER5356 balances dilution effects.
- Thickness Compensation: For 3003 (1.2 mm) + 6061 (6 mm), use ER4043 with ≥220A heat input.
Practical Example
For welding a 6061-T6 aluminum alloy, 4043 wire is preferred for general applications, while 5356 wire is better for higher strength and corrosion resistance.
By correctly matching the wire and alloy, you’ll achieve optimal weld quality and performance. The “composition-performance-process” triangle dictates welding success.
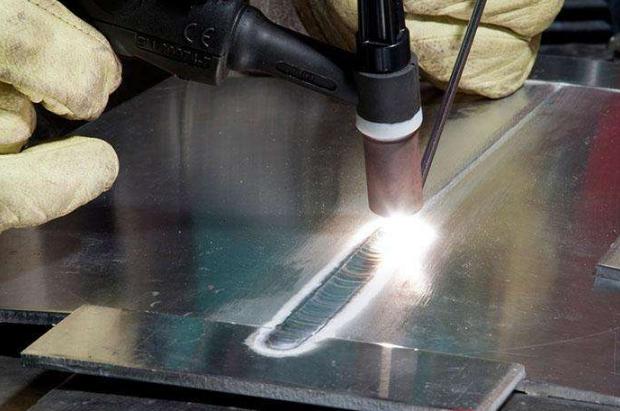
Tips for Successful Aluminum Welding
Preparing for Welding:
- Clean the Surface: Remove oxide layers and contaminants using a stainless steel brush. For mechanical cleaning, use 120-grit stainless steel brushes and weld within 4 hours.
- Use Proper Shielding Gas: 100% argon is ideal for aluminum welding.
- Control Heat Input: Aluminum conducts heat quickly, so adjust settings to prevent warping or burn-through.
Techniques for Success
- Pulsed MIG: Base current 80A, peak 250A, 50 Hz frequency reduces heat input by 30%.
- Preheating: For 6061 alloys >10 mm thick, preheat to 80-120°C to slow cooling.
- Wire Feed Speed: Use a faster wire feed to ensure consistent welds.
- Spool Gun or Push-Pull System: Prevents bird-nesting and ensures smooth wire delivery.
- Practice: Aluminum welding requires skill; practice to master speed, angle, and technique.
Troubleshooting
- Porosity: Check for contamination or improper gas coverage.
- Cracking: Use compatible filler wire and adjust cooling rates.
- Inconsistent Weld Bead: Ensure steady wire feed and clean materials.
By following these tips, you’ll reduce defects and enhance the overall quality of your welds.
Selecting aluminum welding wires demands a systematic approach integrating metallurgy, process mechanics, and service conditions. Precision in composition matching, parameter optimization, and rigorous pre-weld preparation significantly enhance weld quality and efficiency. Always consult manufacturer guidelines and consider the specific requirements of your project to make an informed decision.