Aluminum is a highly versatile material that has gained popularity in various industries due to its lightweight, durability, and corrosion-resistant properties. One of the key enhancements that improve its aesthetic appeal and durability is anodizing. Anodizing aluminum not only boosts its surface resilience but also allows for a wide variety of color finishes. Colored anodized aluminum sheets, including black, red, gold, white, and many others, have become essential in modern architecture, design, and manufacturing. This article delves into the principles behind anodized aluminum coloring, how a wide range of colors is achieved, the different types of colored anodized aluminum sheets, and their applications.
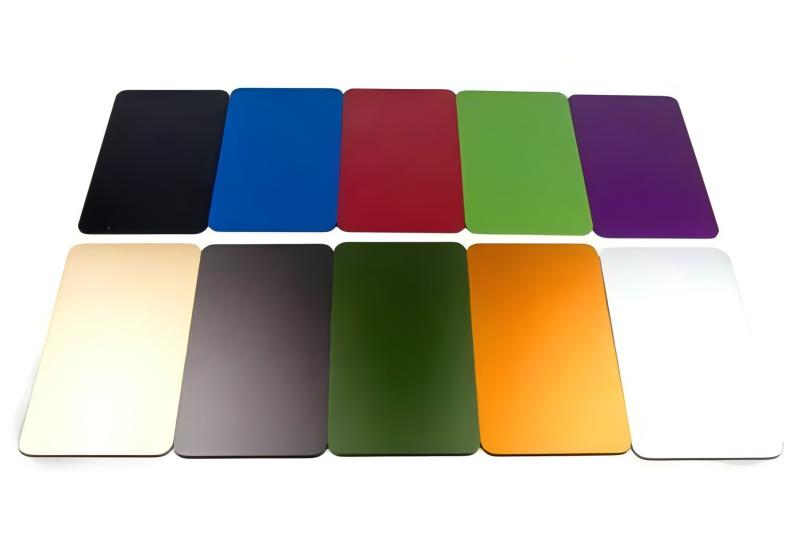
The Coloring Principles of Anodized Aluminum Sheets
The coloring of anodized aluminum sheets primarily hinges on the structural characteristics of the porous anodic oxide layer. During the anodization process, aluminum sheets serve as the anode in an electrolyte bath. Upon the application of an electric current, a dense layer of aluminum oxide forms on the aluminum surface. This oxide layer features a micro-porous structure with pore diameters in the nanometer range and porosity levels of 30-50%. These micro-pores facilitate subsequent coloring processes.
Coloring typically follows the anodization step, involving the immersion of aluminum sheets in solutions containing metal salts (such as copper, nickel, or cobalt salts). Metal ions permeate through the micro-pores into the aluminum oxide layer. Through heating or natural oxidation, these metal ions react chemically with aluminum oxide to form metal oxides or metal salts, thereby imparting various colors to the aluminum sheets. This method is known as seal coloring or chemical coloring.
How to Achieve a Wide Range of Colors in Anodized Aluminum Sheets?
There are several ways to achieve a variety of colors in anodized aluminum panels:
- Selection of Different Metal Salts: Different metal salts react with the aluminum oxide layer to produce different colored compounds. For example, copper salts create a reddish-brown hue, nickel salts result in green, and cobalt salts yield blue. By selecting different metal salts, a wide range of colors can be achieved.
- Mixing Metal Salts: Combining two or more types of metal salts can produce more complex and diverse colors. For instance, mixing copper and nickel salts can result in a unique color that lies between reddish-brown and green.
- Adjusting Coloring Conditions: Factors such as solution concentration, temperature, and time can all influence the final color outcome. For example, increasing the temperature accelerates the diffusion of metal ions, reducing the time needed for coloring. However, excessively high temperatures may lead to color instability.
- Using Dyes for Coloring: In addition to metal salts, organic dyes can be used to color anodized aluminum. Organic dyes offer more vibrant and varied colors. After dyeing, a sealing process is typically required to enhance the durability of the color.
- Multilayer Coloring: By applying multiple layers of color, each using different metal salts or dyes, a composite color with a layered appearance can be created, enhancing the visual effect of the aluminum panel.
Through these methods, a broad range of colors can be achieved on anodized aluminum panels, meeting diverse application needs. Colored anodized aluminum panels not only provide aesthetic appeal but also offer excellent weather resistance and corrosion protection, making them an essential material in modern industrial and architectural design.
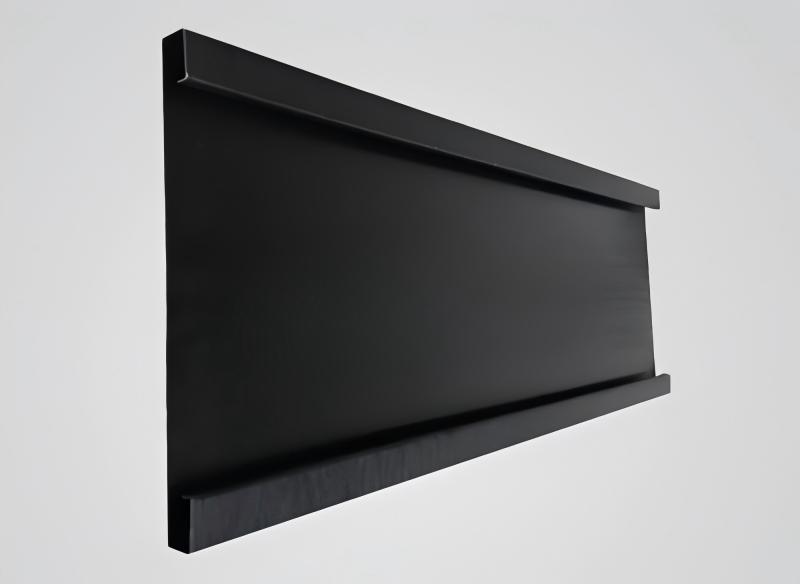
Types of Colored Anodized Aluminum Sheets
The color spectrum of anodized aluminum sheets is vast, each hue tailored to specific applications and aesthetic requirements.
- Black Anodized Aluminum Sheet: This variant is a popular choice in high-end electronic products, offering a sleek and modern aesthetic. Its application extends to architectural projects where a dark, sophisticated finish is desired.
- Red Anodized Aluminum Sheet: Red sheets are favored in artistic installations and interior designs for their bold and vibrant appeal. They add a striking visual element to spaces requiring a splash of color.
- Gold Anodized Aluminum Sheet: Exuding luxury and elegance, gold sheets are ideal for high-end packaging, luxury goods, and decorative architectural features. They bring a touch of opulence to any setting.
- White Anodized Aluminum Sheet: With a clean and minimalist appearance, white sheets are often used in medical equipment and clean rooms, where sterility and a pristine look are essential.
- Other Colored Anodized Aluminum Sheets: The palette expands to include blues, greens, and a host of other hues, each with unique applications in various sectors.
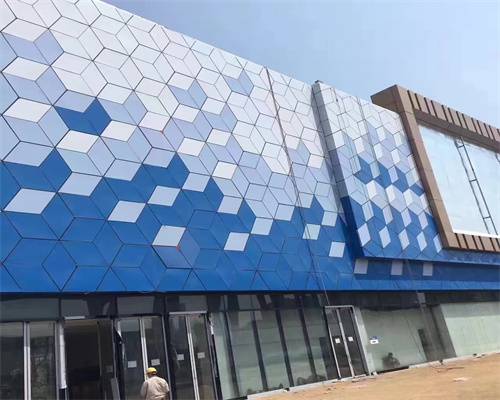
Applications of Colored Anodized Aluminum Sheets
The utilization of colored anodized aluminum sheets spans a multitude of industries, from the grandeur of architectural designs to the precision of automotive and electronic components.
- Architecture: These sheets find extensive use in building facades, interior decorations, and furniture designs. Their color stability and resistance to weathering make them a reliable choice for exterior applications.
- Automotive: In the automotive sector, colored anodized aluminum sheets are employed for decorative trims, dashboard components, and body panels. The combination of aluminum’s lightweight nature and the durability of the anodized finish makes them a sought-after material.
- Electronics: The technology industry benefits from the use of colored anodized aluminum in the manufacturing of consumer electronics like smartphones, laptops, and tablets. These sheets not only protect the devices but also enhance their aesthetic appeal.
- Art and Design: Artists and designers incorporate colored anodized aluminum into their works for its visual impact and the potential to create unique textures and finishes.
- Aerospace: The aerospace industry utilizes colored anodized aluminum for both decorative and functional elements in aircraft interiors. The material’s lightweight and corrosion-resistant properties make it an ideal choice.
- Medical: In the medical field, white anodized aluminum sheets are favored for their clean and sterile appearance, suitable for use in equipment and facilities where hygiene is paramount.
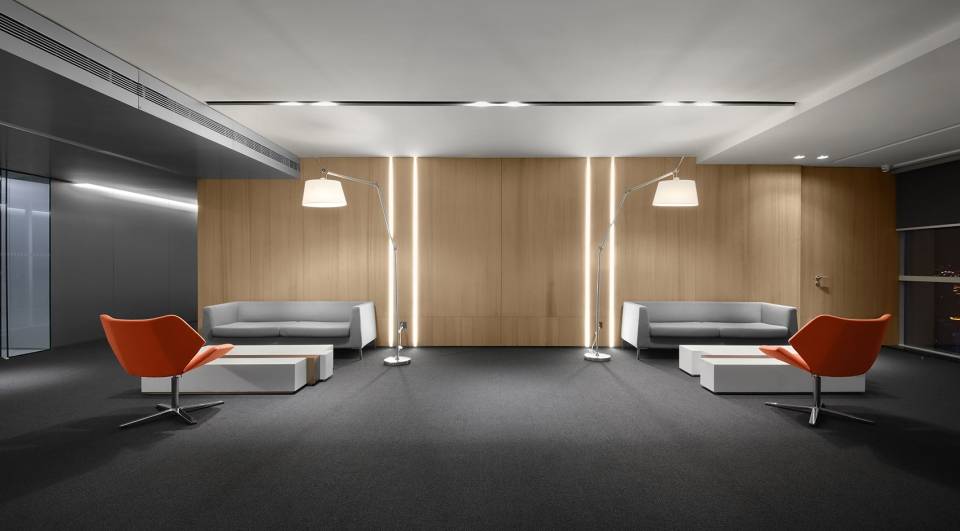
Therefore, when selecting colored anodized aluminum sheets, consideration should be given to their application environment and design requirements to ensure that the selected color meets specific performance and aesthetic standards.